CNC-Fräsen
Das CNC-Fräsen gibt es zwar schon seit über 50 Jahren, doch die Technologie entwickelt sich ständig weiter. Die jüngsten Fortschritte ermöglichen die Automatisierung des gesamten Prozesses, vom Entwurf bis zum fertigen Teil. Diese Fortschritte machen die Technologie für alle Szenarien verfügbar: für große oder kleine Serien, für die Prototypenherstellung bis hin zu fertigen Teilen – mit Vorlaufzeiten von nur einem Tag.
Was ist also passiert, um die CNC-Bearbeitung derart verfügbar zu machen und sie für alle zu demokratisieren?
Um diese Frage zu beantworten, schauen wir uns zunächst genauer an, was CNC-Fräsen eigentlich ist und untersuchen anschließend wie es sich weiterentwickelt.
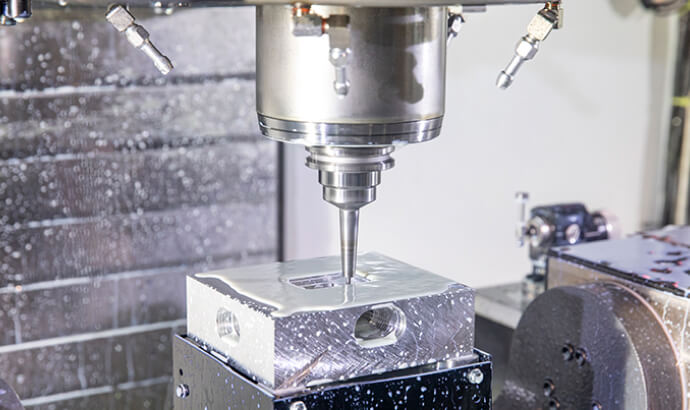
Was ist CNC-Fräsen?
Trotz der unterschiedlichen Methoden zum Abtragen von Material, wird zunächst einmal wird sowohl bei CNC-Bohr- und Fräsmaschinen als auch bei CNC-Drehbänken jeweils Material entfernt, um ein Teil herzustellen. Ein Bearbeitungszentrum kombiniert oft beide Methoden und mehrere Werkzeuge in einer Maschine. Alle besitzen mehrachsige Bewegungsfunktionen, die die Schneidwerkzeuge um das Werkstück herum und durch das Werkstück führen, um genau die gewünschten Formen zu realisieren.
Der grundlegende Unterschied zwischen den beiden Methoden besteht darin, dass eine Fräsmaschine mithilfe eines sich drehenden Werkzeugs Schnitte an einem Werkstück vornimmt, während eine Drehmaschine das Werkstück dreht und der Eingriff durch ein Werkzeug erfolgt.
Wie funktioniert das CNC-Fräsen?
Vor der Einführung von Computer Numerical Control, kurz CNC, wurden sowohl Fräsmaschinen als auch Drehmaschinen manuell bedient. Wie der Name schon sagt, hat CNC diesen Prozess automatisiert, um ihn genauer, zuverlässiger und schneller zu machen.
Ein geschulter Bediener programmiert nun G-Codes (was für Geometrical Code steht) in die Maschine, oft über eine Software. Diese steuern die Fräsmaschine und geben jeweils die Fahrwege und Geschwindigkeit vor, damit sie das Material bohren, schneiden und formen kann, sodass es den vorgegebenen Abmessungen entspricht.
Es gibt eine Reihe verschiedener Arten von CNC-Fräsmaschinen. Die gängigsten sind 3-Achsen-Maschinen, die sich auf der X-, Y- und Z-Achse bewegen, um die Werkzeugbereitstellung für die Fertigung in 3 Dimensionen zu ermöglichen. 3-Achsen-Maschinen sind in der Lage, komplexere Merkmale zu produzieren, indem sie das Werkstück drehen und neu einrichten, um den Zugang aus mehreren Winkeln zu ermöglichen.
Bei Maschinen mit fünf Achsen wird diese Fähigkeit durch zwei weitere Richtungsbewegungen optimiert, nämlich durch die Rotation um die X- und Y-Achse. Sie ist ideal für die Herstellung komplexer und präziser Teile. Der Nachteil ist jedoch, dass der Einsatz einer solchen Technologie Ihr Budget sprengen kann, da die Komplexität zusätzliche Kosten verursacht. Ob Sie es glauben oder nicht, mit 5 Bewegungsachsen können Sie jede beliebige 3D-Geometrie definieren. Es ist jedoch nicht zweckmäßig, das Werkstück zu halten und es frei in alle Richtungen zu drehen. Das wären dann Maschinen mit 6, 7 oder sogar 12 Achsen. Es ist allerdings äußerst unwahrscheinlich, dass Sie solche Maschinen brauchen, es sei denn, Sie benötigen extrem komplexe Teile – denn die Investitionen sind riesig, ebenso wie die Größe der Maschine!
Wie geht es weiter mit der CNC-Bearbeitung?
Wie Sie sehen können, hat die Entwicklung von immer komplexeren CNC-Fräsmaschinen, die immer größer und teurer in der Anschaffung sind und deren Bedienung immer mehr Fachwissen erfordert, viel Zeit in Anspruch genommen. Selbst wenn Sie die CNC-Bearbeitung auslagern, werden die Kosten für diese Komplexität höher sein, da die spezialisierten Hersteller ihre Investitionen wieder einspielen müssen. Wenn Sie ein extrem komplexes Teil haben, das unglaubliche Präzision erfordert und in großen Stückzahlen benötigt wird, können Sie die Investition vielleicht rechtfertigen. Für die überwiegende Mehrzahl der Aufträge ist eine 3-Achsen- oder bestenfalls eine 5-Achsen-Bearbeitung mehr als ausreichend.
Schließlich gibt es immer mehr als einen Weg für die Lösung eines Problems – zum Beispiel ist es in der Regel besser und günstiger, zwei oder mehr weniger komplexe Teile zu konstruieren und sie dann im Rahmen eines sekundären Montageprozesses miteinander zu verschrauben, zu verschweißen oder zu verbinden, als zu versuchen, ein extrem komplexes Einzelteil zu bearbeiten.
Warum also konzentriert man sich so sehr auf die Entwicklung neuer teurer und riesiger Maschinen, die immer weniger Gewinn abwerfen? Es ist ein bisschen wie bei Microsoft Office. Die meisten von uns verwenden Word, doch in Wahrheit nutzen wir wahrscheinlich nur 20 Prozent der Möglichkeiten, die es bietet. Dennoch fügt Microsoft ständig neue Funktionen hinzu, von denen wir die meisten wahrscheinlich nie brauchen, verwenden oder auch nur kennen werden.
Anstatt immer kleinere, schrittweise Verbesserungen am Prozess vorzunehmen, halten wir es für besser, den Prozess selbst zu verbessern. Hier können wir wahre Gewinne erzielen.
Den Prozess automatisieren
Gehen wir zum Anfang zurück und untersuchen den Prozess der Herstellung eines Teils.
Alles beginnt damit, dass der Konstrukteur an seinem CAD-System arbeitet, um das benötigte Teil oder die benötigte Komponente zu entwerfen. Üblicherweise programmiert ein erfahrener Mitarbeiter den G-Code für die computergestützte Fertigung (CAM).
Doch wenn der Entwurf einmal steht, warum sollte dann noch ein weiterer Schritt folgen? Die gute Nachricht ist, dass Sie Ihr CAD bei vielen CAD-Paketen in G-Code umwandeln können – aber wir müssen noch einen Schritt zurückgehen.
Nachdem Sie Ihr Teil entworfen haben, woher wissen Sie, dass es mittels CNC-Bearbeitung und in den von Ihnen gewünschten Toleranzen hergestellt werden kann? Ihr CAD sollte der digitale Faden sein, der alles mit wenig oder gar keinem menschlichen Eingriff verbindet.
Schließlich sollten wir mit Industrie 4.0 alle in einer vernetzten Welt leben. Ein Großteil der CNC-Bearbeitung hängt immer noch von einem erfahrenen Maschinenbauer ab. Wenn Sie Ihren Entwurf einsenden, muss in der Regel ein Mensch prüfen, ob er mit dem bekannten Verfahren hergestellt werden kann. Wenn das nicht der Fall ist, muss es Ihnen mitgeteilt werden, damit Sie den Entwurf neu gestalten oder optimieren können.
Bei Protolabs haben wir diesen Prozess automatisiert. Sobald Sie Ihre CAD-Daten eingesandt haben, werden diese von unserer Software auf ihre Machbarkeit geprüft und ein Angebot wird erstellt. Wenn Änderungen vorgeschlagen werden, die erforderlich sind, werden sie Ihnen im Machbarkeitsbericht, den die Software automatisch erstellt, auf Ihrem CAD angezeigt. Sobald Sie mit dem Entwurf und der Fertigung einverstanden sind, erstellt unsere Software den für die Bearbeitung erforderlichen Code wie im Angebot angegeben.
Schneller und kostengünstiger
Dadurch wird der Prozess viel schneller und kostengünstiger, was bei kleinen und mittelgroßen Aufträgen oder bei der Prototypenherstellung und dem Testen neuer Teile einen echten Unterschied ausmachen kann.
Dank der Automatisierung ist dieser Service für alle gleich, unabhängig von der Größe des Projekts. Traditionelle Maschinenbaubetriebe werden verständlicherweise den Projekten den Vorrang geben, die ihnen mehr Geld einbringen – sei es aufgrund der Größe des Auftrags oder der Komplexität des benötigten Teils – natürlich je nach ihren Möglichkeiten.
Die Automatisierung des Prozesses sorgt für gleiche Wettbewerbsbedingungen. So profitieren Sie bei der Prototypenherstellung oder einer kleinen oder mittleren Anzahl von benötigten Teilen dennoch von der gleichen Geschwindigkeit und der gleichen Servicequalität.
Da all diese Informationen von Anfang an generiert und gesammelt werden, können wir maßgefertigte CNC-gefräste Kunststoff- und Metallteile innerhalb von nur 24 Stunden zuschneiden und versenden. Wenn Sie es nicht ganz so eilig haben, können Sie sich für ein späteres Lieferdatum entscheiden und ihre Kosten reduzieren – auf diese Weise können Sie sogar die Bedingungen selber festlegen.
Dieser Prozess beginnt mit Ihrem CAD, d. h. nachdem Sie Ihr Teil entworfen haben, haben wir einen digitalen Faden, den wir während der gesamten CNC-Bearbeitung verwenden können – von Ihrem Computer bis zur Auslieferung.
Bei der Automatisierung geht es um mehr als nur CNC-Fräsen und -Drehen: Es umfasst alles ab dem Entwurf. Darin liegt die Zukunft des CNC-Fräsens. Das ist wirklich Industrie 4.0 in Aktion.
Wenn Sie Fragen haben, schreiben Sie uns eine Nachricht. Unsere Anwendungsingenieure stehen Ihnen jederzeit unter +49 (0) 89 90 5002 0 oder [email protected] zur Verfügung.