Was ist Lean Manufacturing (Schlanke Produktion)? Und was sind die 5 Grundsätze?
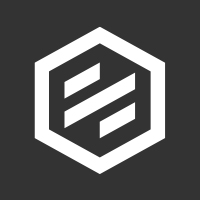
Woran denken Sie, wenn Sie den Begriff "Lean Manufacturing" hören? Kaizen? Kontinuierliche Verbesserung? Abfallreduzierung? Lean Manufacturing ist ein Herstellungsprozess, das seinen Ursprung bei Toyota in Japan hat, als Mitte des 20. Jahrhunderts das Toyota-Produktionssystem entwickelt wurde.
Die Ideologie der schlanken Produktion dreht sich um die Grundsätze der kontinuierlichen Verbesserung, der Beseitigung von Verschwendung und eines kundenorientierten Ansatzes - kurz gesagt, um den Wert zu maximieren und die Verschwendung zu minimieren.

Lean Manufacturing hat "5 Grundsätze": Wert (Kundenmehrwert), Wertstrom identifizieren, Fluss-Prinzip umsetzen, Pull-Prinzip einführen und Perfektion (kontinuierliche Verbesserung). Schauen wir uns jedes Prinzip genauer an, um zu verstehen, wie jeder Schritt das Streben nach einem schlanken Fertigungsprozess unterstützt.
Wert – Der erste Schritt besteht darin, Wert zu definieren. Wert ist jede Handlung oder jeder Prozess, für den ein Kunde zu zahlen bereit ist und den er als wertvoll erachtet. Der "Wert" des Kunden ist der Ausgangspunkt, und Sie sollten dann alle Aktivitäten ermitteln, die diese Werte unterstützen. Überlegen Sie: Wie sieht der Zeitplan für die Bereitstellung Ihres Produkts/Ihrer Dienstleistung aus? Wie hoch ist der Preis? Welche Erwartungen müssen erfüllt werden?
Wertstrom – Als nächstes wird der gesamte Prozess der Bereitstellung Ihres Produkts/Ihrer Dienstleistung analysiert und abgebildet. Vom ersten Konzept bis zu den Händen des Kunden. Während der "Wert" des Kunden der Ausgangspunkt ist, sollten Sie von dort aus alle Aktivitäten identifizieren, die diese Werte unterstützen. Bei der Darstellung Ihrer Werte werden Sie auf "Verschwendung" in Ihrem Prozess/Ablauf stoßen. Diese Verschwendung kann in zwei Kategorien eingeteilt werden: 1) Nicht wertschöpfend, aber notwendig. 2) Nicht wertschöpfend und nicht notwendig.
Kategorie 1, die Sie sofort aus Ihrem Prozess entfernen sollten!
Kategorie 2 sollten Sie mit der Zeit reduzieren.
Fluss-Prinzip – Sicherstellung eines reibungslosen und kontinuierlichen Arbeitsflusses durch den gesamten Wertstrom. Sobald die Verschwendung beseitigt ist, besteht der nächste Schritt darin, die Schritte Ihres Prozesses aufzuschlüsseln. Was kann getan werden, um diese Schritte zu verbessern und einen reibungsloseren Fluss zu gewährleisten? Dies könnte die Schulung von Mitarbeitern, die Anpassung von Produktionsprozessen und -schritten, die Einbeziehung von Robotik und KI usw. umfassen.
Pull-Prinzip – Im Idealfall werden die Komponenten so produziert, wie und wann der Kunde sie braucht. Dieser Just-in-Time-Ansatz für die Produktion bedeutet weniger Lagerbestände und unfertige Erzeugnisse, während gleichzeitig sichergestellt wird, dass alle erforderlichen Materialien, Prozesse und Informationen für einen reibungslosen Arbeitsablauf verfügbar sind. Das bedeutet weniger Abfall und höhere Effizienz.
Perfektion – Das letzte Prinzip der schlanken Produktion. Dies ist die Phase, in der alle anderen Phasen abgeschlossen sind, was zu weniger Abfall und einem reibungsloseren, effizienteren Prozess führt.
Wenn Sie diesen Zyklus abgeschlossen haben, ist das noch nicht das Ende der Kette. Im Sinne einer echten kontinuierlichen Verbesserung gehen wir zurück und beginnen den Prozess erneut, was das Wesen der schlanken Produktion ausmacht.