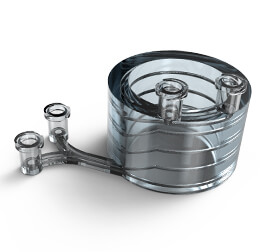
Die Wahl des richtigen Werkstoffs für den 3D-Druck
Werkstoffe müssen für die jeweilige Anwendung geeignet sein, um erfolgreiche Ergebnisse zu liefern. Die Eigenschaften eines Werkstoffs erlangen auf dem Weg vom Konzept über den funktionsfähigen Prototypen bis hin zum fertigen Produkt zunehmend an Bedeutung.
Die Werkstoffeigenschaften können aber nur unter Berücksichtigung des Fertigungsprozesses beurteilt werden. Die Merkmale ergeben sich nämlich aus der Kombination aus Werkstoff und Verfahren. So unterscheiden sich zum Beispiel die Eigenschaften einer Metalllegierung je nachdem, ob sie im Druckgießverfahren verarbeitet oder spritzgegossen wird. Ebenso hat ein Thermoplast unterschiedliche Eigenschaften je nachdem, ob er spritzgegossen oder CNCgefräst wird.
Der 3D-Druck, auch additive Fertigung genannt, ist einzigartig. Er unterscheidet sich von allen anderen Fertigungsverfahren, sodass die Eigenschaften des Werkstoffs und der damit hergestellten Teile sich selbst dann unterscheiden, wenn die verwendete Legierung bzw. der verwendete Thermoplast nahezu identisch ist. Hinsichtlich der Werkstoffeigenschaften geht es dabei nicht um besser oder schlechter; vielmehr ist es ganz einfach wichtig zu erkennen, dass die Resultate unterschiedlich ausfallen.
Die folgenden Informationen sollen Ihnen unter Berücksichtigung dieser Unterschiede bei der Charakterisierung und schließlich der Auswahl von Werkstoffen für drei weit verbreitete industrielle 3D-Druckverfahren helfen: das direkte Metall-Lasersintern (DMLS), das selektive Lasersintern (SLS) und die Stereolithographie (SL oder auch SLA).
Entwicklungen bei den Werkstoffen
Wie zu erwarten, wurden die für den 3D-Druck verwendeten Werkstoffe weiter verbessert. Dank dieser Fortschritte eignet sich die Technologie nicht mehr nur für Modelle und Prototypen, sondern auch für funktionsfähige Teile für Testdurchläufe, den Werkstatteinsatz und die Produktion.
Und obwohl sich sein Output von dem anderer Fertigungsverfahren unterscheidet, bietet der 3D-Druck eine brauchbare Alternative, wenn Sie einen direkten Ersatz suchen. Noch größere Vorteile ergeben sich jedoch, wenn Anwender mit seinen Möglichkeiten experimentieren.
Es ist allerdings nicht ganz einfach, mit dem 3D-Druck zu experimentieren, da die Unterschiede des Verfahrens über die Werkstoffeigenschaften hinausgehen, wenn sie auch damit
zusammenhängen. So fehlen bei additiven Werkstoffen zum Beispiel umfangreiche Leistungsdaten, die ein Material über verschiedene Bedingungen hinweg charakterisieren. Stattdessen wird 3D-DruckAnwendern ein einzelnes Datenblatt zur Verfügung gestellt, das eine begrenzte Anzahl an Werten enthält. Außerdem stellen diese Werte wahrscheinlich ein Best-Case-Szenario dar, dasauf der Prüfung von Neumaterial (z. B. nicht recycelten Pulvern) basiert.
Eine weitere Schwierigkeit besteht darin, dass der 3D-Druck anisotrope Eigenschaften erzielt, deren Werte für die x- und y-Achse (Zeichnungsebene) überwiegend von denen der
z-Ausrichtung abweichen. Der Grad der Anisotropie variiert je nach 3D-Drucktechnologie – das direkte Metall-Lasersintern z. B. kommt der Isotropie am nächsten – und sollte immer
berücksichtigt werden.
Materialzulieferer veröffentlichen jedoch manchmal keine Werkstoffspezifikationen, welche die Abweichung der Eigenschaften zwischen verschiedenen Achsen dokumentieren, da die zugrunde liegenden Daten je nach Werkstoff, Verfahren oder sogar Maschinentyp stark voneinander abweichen können.
Durch ein speziell auf das 3D-Druckverfahren ausgerichtetes
Design und die Anpassung der Bauausrichtung lassen sichAnisotropien oder unzureichende Werkstoffeigenschaften überwinden. Hierbei können Designer die Erfahrungen aus
früheren Projekten (oder die Erfahrung eines qualifizierten Serviceanbieters) nutzen, um Datenlücken aufgrund von begrenzt vorliegenden Werkstoffeigenschaftsdaten zu
schließen. Wenn die Leistungsfähigkeit des Teils eine entscheidende Rolle spielt, sollte eine unabhängige Laborprüfung von additiven Werkstoffen in Erwägung gezogen werden. Die Werkstoffeigenschaften sind zwar erfolgsentscheidend, jedoch nicht die einzigen Kriterien.
Jeder additive Werkstoff und jedes additive Verfahren bestimmt darüber hinaus über Eigenschaften, wie maximale Teilegröße, Maßhaltigkeit, Merkmalauflösung, Oberflächenqualität, Produktionszeit und Teilekosten. Es ist daher ratsam, ein geeignetes Material auszuwählen und dann zu prüfen, inwieweit es den Erwartungen und Anforderungen in Bezug auf Zeit, Kosten und Qualität entspricht.
Werkstoffauswahl
Im Allgemeinen unterscheidet sich ein additiver Werkstoff in ein oder zwei Werkstoffeigenschaften von allen anderen Werkstoffen.
Wird beispielsweise die durchschnittliche Zugfestigkeit von Polyamid (PA) 11 angestrebt, ist ein Stereolithographie Photopolymer möglicherweise eine bessere Option als ein für
das selektive Lasersintern verwendetes PA. Wird hingegen die Wärmeformbeständigkeit (HDT) eines ABS benötigt, dann ist gesintertes Nylon die beste Option.
Angesichts der Tatsache, dass sich ein Werkstoff aufgrund weniger Eigenschaften von anderen abhebt, empfiehlt es sich, bei der Auswahl eines Werkstoffs für den 3D-Druck zunächst zu
definieren, welche mechanischen oder thermischen Eigenschaften wichtig sind. Wählen Sie danach aus den vorhandenen Optionen den passenden Werkstoff aus. Nachdem Sie die Auswahl
eingegrenzt haben, sollten Sie die übrigen Eigenschaften prüfen, um herauszufinden, ob der Werkstoff für Ihr Projekt in Frage kommt.
Da der 3D-Druck einzigartig ist, ist es unklug, nach einem Material zu suchen, das perfekt zu einem Druckguss-, Spritzguss- oder CNC-Werkstoff passt. Stattdessen sollten Sie die Werkstoffoptionen prüfen, um den Werkstoff zu finden, der die kritischen Anforderungen erfüllt.
Direktes Metall Lasersintern (DMLS)
Beim DMLS werden für die Teileherstellung reine Metallpulver eingesetzt, deren Eigenschaften allgemein als Schmiedewerkstoffen gleichwertig oder überlegen
anerkannt sind. Da das Material unter dem kleinen, sich ständig bewegenden Laserpunkt schnell schmilzt und dann erstarrt, kann es zu Unterschieden bei der Korngröße und den Korngrenzen kommen, die sich auf die mechanische Leistungsfähigkeit auswirken. Derzeit werden die Kornstrukturen noch erforscht, die sich aufgrund von Laserparametern, Wärmenachbehandlung und
heißisostatischem Pressen ändern können. Die Ergebnisse sind jedoch nicht allgemein verfügbar. Dieser Unterschied wird schließlich zu einem Vorteil, wenn die Kornstruktur so
beeinflusstwerden kann, dass sie verschiedene mechanischeEigenschaften in einem Teil ermöglicht.
Von den drei hier besprochenen 3D-Druckverfahren ist DMLS das Verfahren, mit dem Teile hergestellt werden können, deren Werkstoffeigenschaften dem isotropen Zustand am nächsten
kommen. Die Eigenschaften können jedoch leicht variieren, wenn sie entlang unterschiedlicher Achsen gemessen werden.
Ein visueller Vergleich der Werkstoffeigenschaften von DMLS ist in Grafik 1 (Zugfestigkeit), Grafik 2 (Bruchdehnung) und Grafik 3 (Härte) aufgeführt.
Edelstahl ist ein häufig verwendeter DMLS-Werkstoff und ist bei Protolabs in der Qualität 316L erhältlich, die eine ausgezeichnete Bruchdehnung von 40 % aufweist und dadurch sehr gut formbar ist. 316L ist säure- und korrosionsbeständig und im spannungsfreien Zustand temperaturbeständiger als die meisten anderen Materialien.
DMLS-Aluminium (Al) ist vergleichbar mit einer 3000erLegierung, die in Guss- und Druckgussverfahren zum Einsatz kommen. Seine Zusammensetzung ist AlSi10Mg. Al besitzt
ein ausgezeichnetes Festigkeits-Gewichts-Verhältnis, eine gute Temperatur- und Korrosionsbeständigkeit sowie eine gute Dauer-, Kriech- und Bruchfestigkeit.
Im Vergleich zu 3000er-Druckgussaluminium liegen die Werte von Al für Zugfestigkeit (360 MPa +/- 30 MPa)
und Streckgrenze (240 MPa +/- 30 MPa) weit über den Durchschnittswerten. Die Bruchdehnung ist dagegen deutlich niedriger (3 % gegenüber 11 %) im Vergleich zum Durchschnittswert bei 3000er-Aluminiumlegierungen.
DMLS-Titan (Ti6Al4V) wird aufgrund seines FestigkeitsGewichts-Verhältnisses, seiner Temperaturbeständigkeit und seiner Säure-/Korrosionsbeständigkeit hauptsächlich für medizinische Anwendungen eingesetzt. Mit einer Zugfestigkeit von 930 MPA, einer Bruchdehnung von 10 % und einer Härte von 36 HRC besitzt er nahezu dieselben mechanischen Eigenschaften wie gehärteter Titan Grade 23.
Maraging-Stahl ist bekannt für seine hohe Festigkeit und Robustheit, ohne an Formbarkeit einzubüßen. Die Festigkeit dieser speziellen Klasse von ultrahochfesten Stählen mit niedrigem Kohlenstoffgehalt beruht nicht auf Kohlenstoff, sondern auf der Ausscheidung intermetallischer Verbindungen. Maragin-Stahl ist bis zu 37 HRC aushärtbar und besitzt eine hohe Temperaturbeständigkeit. Dank seiner gleichmäßigen Ausdehnung und einfachen Zerspanbarkeit vor seiner Alterung eignet er sich für Verschleißteile von Montagelinien und Formen.
Inconel 718 (IN718) ist eine Nickel-Chrom-Superlegierung, die in Anwendungen mit hohen Einsatztemperatur, wie z. B. Bauteilen für Flugzeugtriebwerke oder Gasturbinenteilen, zum Einsatz kommen. DMLS IN718 hat einen beeindruckenden Betriebstemperaturbereich von -252 °C bis 704 °C, gepaart mit einer hervorragenden Korrosionsbeständigkeit und guten Dauer-, Kriech- und Bruchfestigkeit.
Kupfer (CuNi2SiCr) ist ein niedriglegiertes Kupfermaterial, das gute mechanische Eigenschaften und eine hohe thermische und elektrische Leitfähigkeit vereint. Der Werkstoff kommt in der Regel in raueren Umgebungen zum Einsatz, in denen Reinkupfer nicht in Frage kommt.



Selektives Lasersintern (SLS)
Selektives Lasersintern (SLS) verwendet Thermoplastpulver, überwiegend Polyamid (PA), zur Herstellung von funktionsfähigen Teilen mit einer höheren Robustheit und Schlagzähigkeit gegenüber mittels Stereolithographie (SL) gefertigten Teilen, sowie hohen HDT-Werten (157 °C bis 188 °C). Nachteilig ist, dass SLS die Oberflächenqualität und Detailgenauigkeit von SL nicht erreicht.
Im Allgemeinen haben SLS-Polyamide im Vergleich zu entsprechenden Durchschnittswerten beim Spritzgussverfahren ähnliche HDT-Werte, jedoch niedrigere Werte bei den mechanischen Eigenschaften. In wenigen Fällen werden bei SLS-Polyamiden Eigenschaften ausgewiesen,
die den Grad der Anisotropie dokumentieren. Ein visueller Vergleich der Werkstoffeigenschaften von SLS ist in Grafik 4 (Wärmeformbeständigkeit), Grafik 5 (Bruchdehnung) und Grafik 6 (Zugfestigkeit) aufgeführt.
PA 11 Schwarz besitzt eine Duktilität und Flexibilität mit einem Elastizitätsmodul von 49 MPa und einer Bruchdehnung von 18 % +/- 7 % in XY-Richtung, ohne dabei an Zugfestigkeit (48 MPa) und Temperaturbeständigkeit (Wärmeformbeständigkeit:
188 °C) einzubüßen. Diese Eigenschaften machen PA 11 Schwarz zu einem beliebten Allzweckmaterial und zur besten Option bei aktiven Scharniergelenken mit begrenzten Testkapazitäten.
Im Vergleich zu den Durchschnittswerten bei spritzgegossenem PA 11 besitzt PA 11 Schwarz eine höhere Wärmeformbeständigkeit (188 °C gegenüber 140 °C) bei ähnlicher Zugfestigkeit und Steifigkeit. Seine Bruchdehnung ist zwar die höchste unter allen 3D-Druck-Kunststoffen, sie
liegt aber immer noch 60 % unter der eines spritzgegossenen PA 11.
Ein weiteres Unterscheidungsmerkmal von PA 11 Schwarz ist seine gleichmäßige, tiefschwarze Farbe. Schwarz bildet einen hohen Kontrast, von dem sich Merkmale hervorragend abheben, und verbirgt Schmutz und Fett. Schwarz ist aufgrund des niedrigen Reflexionsgrads eine begehrte Farbe für optische Anwendungen.
PA 12 Weiß ist ein ausgewogener und wirtschaftlicher Werkstoff und oft die erste Wahl für allgemeine Anwendungen. PA 12 Weiß besitzt eine ähnliche Zugfestigkeit wie PA 11 Schwarz (52 MPa gegenüber 48 MPa) Obwohl seine Bruchdehnung viel niedriger ist als die von PA 11 Schwarz, gehört es bei der Duktilität mit 20 % immer noch zu den Spitzenreitern. PA 12 Weiß ist grob vergleichbar mit den durchschnittlichen Eigenschaften eines spritzgegossenen PA 12. Es besitzt eine ähnliche Steifigkeit, aber etwa nur eine halb so große Zugfestigkeit und Bruchdehnung. Seine Wärmeformbeständigkeit ist mit 177 °C gegenüber 138 °C jedoch deutlich höher.
PA 12 mit 40 % Glasfaser ist ein Polyamidpulver, das mit Glaskugeln durchsetzt ist, die es steif und formstabil machen. Der Glasfaserfüllstoff macht es jedoch brüchig, wodurch die Schlagzähigkeit und die Zugfestigkeit erheblich verringert werden. Außerdem sind Teile aus PA 12 mit 40 % Glasfaser wegen der Glaskugeln viel schwerer als solche, die aus einem anderen 3D-Druckmaterial bestehen. PA 12 mit 40 % Glasfaser ist eine gute Wahl, wo Steifigkeit und Temperaturbeständigkeit wichtig sind.



Stereolithographie (SL)
SL verwendet Photopolymere, also thermoplastische Kunststoffe, die mit UV-Licht ausgehärtet werden. Das Verfahren bietet die umfassendste Materialauswahl mit einer breiten Palette an Zugfestigkeits-, Elastizitätsund Biegemodul- sowie Bruchdehnungswerten. Es ist
zu beachten, dass die Schlagzähigkeits und HDT-Werte in der Regel deutlich niedriger sind als bei gängigen Spritzgusskunststoffen. Die Werkstoffpalette bietet außerdem verschiedene Farb- und Opazitätsoptionen. Neben einer guten Oberflächenqualität und einer hohen Auflösung
von Details ermöglicht SL die Herstellung von Teilen, die Spritzgussteilen in Leistungsfähigkeit und Erscheinungsbild in nichts nachstehen.
Die Photopolymere sind hygroskopisch und UV-empfindlich, wodurch sich die Abmessungen und die Leistungsfähigkeit des Teils mit der Zeit ändern können. Durch die Exposition gegenüber Feuchtigkeit und UV-Licht verändern sich das Erscheinungsbild, die Größe und mechanische Eigenschaften. Ein visueller Vergleich der Werkstoffeigenschaften von SL ist in Grafik 7 (Wärmeformbeständigkeit), Grafik 8 (Bruchdehnung) und Grafik 9 (Zugfestigkeit) aufgeführt.
ABS-ähnlich, weiß (Accura Xtreme White 200) ist ein weit verbreiteter SL-Werkstoff. In Bezug auf seine Flexibilität und Festigkeit liegt er irgendwo zwischen Polypropylen und ABS, wodurch er sich gut für Schnappverbindungen, Urmodelle und anspruchsvolle Anwendungen eignet. Xtreme ist ein langlebiger SL-Werkstoff. Er besitzt eine sehr hohe Schlagzähigkeit (64 J/M) und mit 9 +- 5 % eine hohe mittlere Festigkeit und Steifigkeit. Seine Wärmeformbeständigkeit (47 °C) ist allerdings die niedrigste unter den SL-Werkstoffen.
Im Vergleich zum Durchschnittswert für spritzgegossenes ABS besitzt Xtreme eine etwas höhere Zugfestigkeit (45 MPa - 50 MPa), jedoch eine geringere Bruchdehnung (20 % gegenüber 30 %). Unter Biegebelastung ist Xtreme zu 26 % weniger steif und seine Schlagzähigkeit ist um 70% geringer.
ABS-ähnlich, grau (Accura Xtreme) ist vergleichbar mit Polypropylen (PP)/ABS und ein zäher, langlebiger Werkstoff. Er ist sehr gut geeignet für Schnappverschlüsse, Baugruppen und anspruchsvolle Anwendungen und zeichnet sich durch seine graue Farbe aus.
ABS-ähnlich lichtdurchlässig/durchsichtig (WaterShed) bietet eine einmalige Kombination aus niedriger Feuchtigkeitsaufnahme (0,35 %) und nahezu farbloser Transparenz – seine absolute Klarheit erhält der Werkstoff durch Nachbearbeitungsschritte. Danach behält er einen
ganz leichten Hellblauton. WaterShed eignet sich gut für Allzweckanwendungen und den Modellbau und ist die beste Wahl bei Modellen zur Flussvisualisierung, Lichtröhren und Linsen.
Unter den 3D-gedruckten thermoplastähnlichen Materialien besitzt WaterShed mit die höchste Zugfestigkeit und Bruchdehnung, was es zu einem robusten und langlebigen Werkstoff macht. Im Vergleich zu den Durchschnittswert für spritzgegossenes ABS bietet WaterShed eine etwas höhere Zugfestigkeit (55 MPa gegenüber 42 MPa), jedoch eine geringere Bruchdehnung (6 % gegenüber 30 %) und Wärmeformbeständigkeit (50 °C gegenüber 54 °C).
ABS-ähnlich, schwarz (Accura Black SL 7820) ist eine weitere Alternative bei der Prototypenherstellung von spritzgegossenen ABS-Teilen. Der Werkstoff imitiert nicht nur die mechanischen Eigenschaften von ABS, sondern seine tiefschwarze Farbe und seine hochglänzenden nach
oben weisenden Oberflächen in einem Top-Profil bieten das Aussehen eines Spritzgussteils, während Schichtlinien in einem Seitenprofil sichtbar sein können. Er bietet einen großen Arbeitsbereich von physikalischen Eigenschaften, eine hohe Bruchdehnung (5 +- 3 %) und eine Schlagzähigkeit, die sich zum Bau von Konzeptmodellen und funktionsfähigen Prototypenteilen eignet.
MicroFine™ Green / Grey (Grün & Grau) wird bei Protolabs speziell formuliert, um die höchste Detailgenauigkeit – 0,07 mm kleine Merkmale sind möglich – und die engsten Toleranzen unter allen SL-Werkstoffen zu erzielen. Das Material wird zur Herstellung von Kleinst- und Kleinteilen mit Abmessungen von in der Regel unter 25 x 25 25 mm³.
In Bezug auf die mechanischen Eigenschaften liegt MicroFine™ Green & Grey unter den SL-Werkstoffen bei der Zugfestigkeit (60 MPa) und dem Elastizitätsmodul (2200 MPa) im mittleren Bereich und bei der Schlagzähigkeit (0,23 J/m) und der Bruchdehnung (6 %) am unteren Ende
der Skala. MicroFine™ Green / Grey hat eine ähnliche Steifigkeit und Zugfestigkeit wie spritzgegossenes ABS, jedoch eine geringere Wärmeformbeständigkeit als ABS (59 °C gegenüber 102 °C).
Der Werkstoff PC-ähnlich, lichtdurchlässig (hochentwickelt, hochtemperaturbeständig) – (Accura 5530) sorgt für ein festes, steifes Teil mit einer hohen Temperaturbeständigkeit. Darüber hinaus kann eine thermische Nachhärtungsoption die Wärmeformbeständigkeit von
85 °C auf 250 °C erhöhen (bei 0,45 MPa). 5530 besitzt mit die höchsten Elastizitäts- und Biegemodulwerte unter allen unverstärkten SL-Werkstoffen sowie eine hohe Zugfestigkeit (50 MPa +/- 10 MPa). Die Nachhärtung macht 5530 jedoch weniger langlebig und führt
zu einer Schlagzähigkeit von nur 21 J/m sowie einer Bruchdehnung von 2,9 %. Ohne die thermische Nachhärtung behält 5530 seine Zugfestigkeit und wird flexibler. Außerdem erhöht sich die Bruchdehnung um rund 50 %.
Beim Vergleich mit spritzgegossenen Thermoplasten kommt das Material einem mit 10 % Glasfaser verstärkten Polycarbonat am nächsten. Mit der thermischen Nachhärtung hat 5530 eine ähnliche Zugfestigkeit und ein ähnliches Biegemodul (verglichen mit den
Durchschnittswerten) und eine um 66 % höhere Wärmeformbeständigkeit. Die Schlagzähigkeit und die Bruchdehnung fallen bei 5530 jedoch deutlich niedriger aus (um 81 % bzw. 72 % niedriger).
Keramik-ähnlich, hochentwickelt, hochtemperaturbeständig (PerFORM) ist der ideale Werkstoff zur Herstellung von festen, steifen Teilen mit einer hervorragenden, hohen Hitzebeständigkeit.
Mithilfe einer weiteren thermischen Nachhärtungsoption kann die Wärmeformbeständigkeit von 132 °C auf 268 °C (bei 0,45 MPa), d. h. auf den höchsten Wert unter allen SLA Werkstoffen, erhöht werden. Typische Einsatzbereiche sind die Herstellung von Werkzeugen
und Windkanaltestanwendungen.
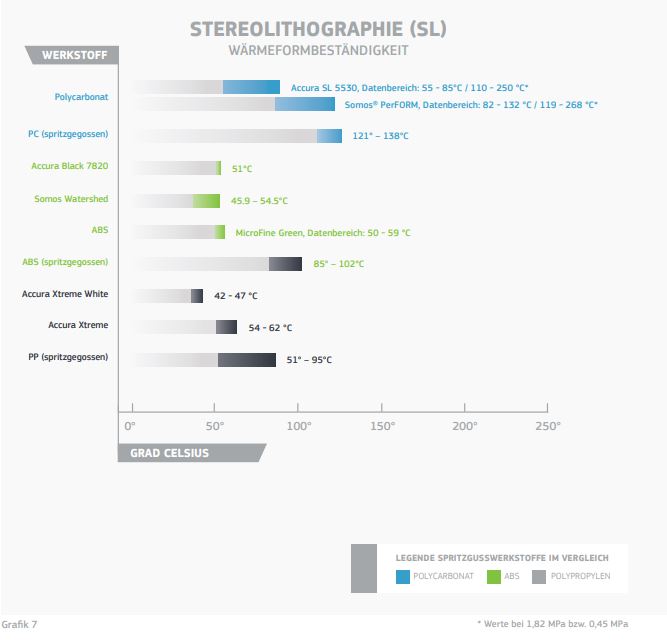


Fazit
Egal, ob Metall, Thermoplast und Duroplast – der 3D-Druck bietet viele verschiedene Materialien, die mit herkömmlichen Methoden verarbeitete Werkstoffe nachahmen, wenn nicht sogar ersetzen können. Eine exakte Übereinstimmung ist aufgrund der Unterschiede bei den
zugrunde liegenden Verfahren zwar nicht möglich, doch dank der breiten Materialauswahl ist es sehr wahrscheinlich, dass die Hauptanforderungen an das Material erfüllt werden.
Der Schlüssel zum Erfolg ist Offenheit und Bewusstsein für die Unterschiede. Mit der Unterstützung eines sachkundigen und qualifizierten 3D-Druckanbieters, der Datenlücken füllen kann, lassen sich die einzigartigen Vorteile der 3D-Drucktechnologie mit dieser
Einstellung optimal nutzen.
Quellen: matweb.com, ulprospector.com, Lieferantendatenblätter and protolabs.de.

