Kombination von Baugruppen mit additiver Fertigung
Wie man die richtigen Möglichkeiten findet, um mehrteilige Baugruppen mit industriellem 3D-Druck zu einzelnen Komponenten zusammenzuführen.
- Wann sollten Baugruppen für die additive Fertigung kombiniert werden?
- Wie man Baugruppen für die additive Fertigung kombiniert
- Berücksichtigung von Toleranzen für additiv gefertigte Teile
- Nachbearbeitungsoptionen für additiv gefertigte Teile: Spanende Bearbeitung, Gewindeschneiden, Polieren
- Skalierbarkeit berücksichtigen
- Wann man bei der traditionellen Fertigung bleiben sollte
Die additive Fertigung, oder auch der industrielle 3D-Druck, bewegt sich von ihrer ursprünglichen Funktion zur Prototypenherstellung in den Bereich der endgültigen Serienteile. Es eröffnen sich neue Möglichkeiten für die Gestaltung von Teilen, die noch vor 10 Jahren undenkbar gewesen wären.
Einer der am häufigsten genannten Vorteile der additiven Fertigung ist die Möglichkeit, bestehende, aus vielen Teilen zusammengesetzte Baugruppen zu einem einzigen Teil zusammenzuführen. Wenn Sie mit einem neueren Flugzeug geflogen sind, haben Sie dies vielleicht schon erlebt, ohne es zu wissen. Das bekannteste Beispiel aus der Luft- und Raumfahrtindustrie ist die additiv gefertigte Treibstoffdüse von GE für das LEAP-Flugzeugtriebwerk von CFM International. Die Düse war ein aus 20 Teilen bestehendes Triebwerkselement, das in ein einziges umgewandelt wurde, wodurch das Gewicht um 25 % reduziert wurde.
Die Durchführung eines solchen Entwicklungsprojekts ist jedoch entmutigend, und allzu oft müssen Ingenieure feststellen, dass das Ergebnis entweder nicht so viel Geld spart, wie gedacht, oder dass sie die Anforderungen, die sie von der traditionellen Fertigung gewohnt sind, nicht erfüllen können.
Das Problem ist nicht der Ingenieur oder die Technologie, sondern oft die Auswahl der zu kombinierenden Baugruppen und ein falsches Verständnis davon, wie man es effektiv macht. In diesem Leitfaden wird untersucht, wie man Möglichkeiten findet, mehrteilige Baugruppen in Richtung zusammengeführter additiver Fertigung in Direktes Metall-Laser-Sintern (DMLS), Selektives Lasersintern (SLS), und Multi Jet Fusion (MJF), zu bewegen, aber auch, wie man ein Ergebnis erzielt, das kostengünstiger und leistungsfähiger ist als andere Fertigungsmethoden. Neben den additiven Technologien, die in diesem Leitfaden vorgestellt werden, bieten wir bei Protolabs noch zwei weitere 3D-Druckverfahren an: Stereolithographie (SLA) und PolyJet.

Wann sollten Baugruppen für die additive Fertigung kombiniert werden?
In der Regel reicht es nicht aus, zwei Teile miteinander zu kombinieren – idealerweise sollten Sie an mehr als 20 Teile denken. Je mehr Teile kombiniert werden, desto größer sind aller Voraussicht nach die Einsparungen. Wenn die Teile nach der Montage fest verbaut sind, kann dies eine Gelegenheit zur Konsolidierung sein. Je schwieriger die Montage in ihrer jetzigen Form ist, desto besser. In der additiven Fertigung ist Komplexität oft kostenlos –
die erfolgreichsten Teile machen sich dieses Axiom so weit wie möglich zunutze.
Im besten Fall, und das sollte jeder Ingenieur anstreben, lassen sich mit der additiven
Fertigung nicht nur Kosten einsparen, sondern auch die Leistungsmerkmale der Teile verbessern. Eine kombinierte Baugruppe weist in der Regel weniger Fehlerstellen auf und verfügt über eine höhere Stärke durch ein einheitliches Teil. Suchen Sie nach Anwendungen,
bei denen einer dieser beiden Punkte zu großen Vorteilen führt. Auch interne Kühlkanäle lassen sich leicht integrieren, was zu Vorteilen wie geringerer Ermüdung der Teile führen kann. Erfüllen Sie sich sämtliche Design-Wünsche – das Unmögliche wird plötzlich möglich:Entwerfen Sie also das bestmögliche Teil.
– die Einsparungen sollten viel umfassender sein. Was darüber hinaus zu beachten ist:
- Wegfall der Montage: Das bedeutet weniger Arbeitsaufwand, weniger Inventar,
weniger Vorrichtungen und weniger Produktionsfläche für Ihr Endprodukt. Auch
der Inspektionsaufwand bei der Montage verringert sich; die Möglichkeit von
Montagefehlern entfällt. - Weniger Fehlerquellen: Die Wartungskosten werden langfristig gesenkt, und Sie
müssen weniger Ersatzteile bevorraten. Bei Bedarf können auch kleine Mengen
schnell und kostengünstig ausgetauscht werden. - Niedrigere Betriebskosten: Die Optimierung von Teilen aufgrund der Designfreiheit
verbessert dank der additiven Fertigung die Leistungsfähigkeit des Produkts und
ermöglicht Verbesserungen wie Leichtbau und bessere thermische Eigenschaften
der Teile.
Die besten Gelegenheiten für eine Umstellung von anderen Fertigungsverfahren auf den 3D-Druck bieten sich häufig bei hochwertigen oder
leistungsfähigen Produkten, bei denen die bestehenden Lösungen ständig Gefahr laufen zu scheitern, nicht die Erwartungen erfüllen oder
erhebliche Produktionskosten verursachen, die über die Herstellung der Grundkomponenten hinausgehen. Teile und Baugruppen, die derzeit ohne
größere Schwierigkeiten hergestellt werden, sind eher keine guten Gelegenheiten für die Umstellung auf die additive Fertigung – zum Beispiel die
Bearbeitung einiger Metallkomponenten für eine relativ einfache Baugruppe. Wenn ein Teil nicht defekt ist, versuchen Sie nicht, es zu reparieren!
Wie man Baugruppen für die additive Fertigung kombiniert
Da die Reduzierung von Baugruppen auf eher unklare Weise mit Kosteneinsparungen gleichzusetzen ist, ist dies oft leichter gesagt als getan. Grundsätzlich können Sie mehrere traditionell gefertigte Teile in Ihrer 3D-CAD-Baugruppendatei als ein Stück exportieren, um ein verdichtetes „Frankenstein“-Teil zu schaffen, das theoretisch mit additiver Fertigung hergestellt werden könnte. Wir sehen häufig solche Teile und werden gefragt: „Können Sie das machen?“, worauf die Antwort oft „Ja!“ lautet. Das bedeutet jedoch nicht, dass das Ergebnis kosteneffizient, von hoher Qualität oder höherer Leistungsfähigkeit ist. Nur weil die additive Fertigung nahezu unbegrenzte Designfreiheit bietet, heißt das noch nicht, dass jedes Teil kosteneffizient oder für diese Technologie geeignet ist.
Es kann sich lohnen, Ihre Anwendung auf ihrer grundlegendsten Ebene zu betrachten
und sich zu fragen, welche – abgesehen von der Herstellbarkeit – die grundlegenden
Designanforderungen sind, und von dort aus rückwärts zu arbeiten. Zur Schaffung eines
effektiven Designs für die additive Fertigung muss man oft die Einschränkungen der
Fertigung ausblenden, die sich durch jahrelanges Arbeiten in den Köpfen festgesetzt
haben. Wenn bei Ihrem additiv gefertigten Teil ein Aspekt nur vorhanden ist, weil er
in einer früheren Version typisch für die Herstellungsmethode war, lohnt es sich, ihn
in Frage zu stellen.
Ganz allgemein gilt bei der additiven Fertigung, dass das Materialvolumen mit Kosten
verbunden ist. Lassen Sie alles beiseite, was für die Funktionalität nicht notwendig
ist. Aber denken Sie an eine der grundlegendsten Regeln der additiven Fertigung:
Komplexität ist kostenlos. Der Schlüssel zu einem kosteneffizienten Bauteil liegt oft
darin, einen Mehrwert zu schaffen, indem man das Design so leistungsfähig wie
möglich gestaltet, ohne die Einschränkungen des traditionellen Designs zu haben.
Die additive Fertigung bietet zwar eine von anderen Fertigungsverfahren unerreichte
Designfreiheit, hat aber auch ihre eigenen Regeln und Richtlinien. Die additive Fertigung
ermöglicht die Herstellung von Teilen, die bisher nicht möglich war, einschließlich
optimierter Teile, die durch generatives Design hergestellt werden. Es ist zu bedenken,
dass ein mit einer 3D-Topologie-Optimierungssoftware erzeugtes organisch geformtes Teil
zwar theoretisch die bestmögliche Lösung für eine bestimmte Belastungsbedingung sein
kann, dies aber nicht bedeutet, dass das Teil für die additive Fertigung gut konzipiert ist.
Dies gilt insbesondere für Technologien, die für die Formgebung ein Trägermaterial
erfordern, wie z. B. DMLS. Diese Teile können erhebliche Überhänge aufweisen, die
zusätzliches Stützmaterial bei der Herstellung erfordern, was die Druckzeit und den
Arbeitsaufwand bei der Endbearbeitung erhöht. Bei hohlen Bauteilen kann eine sorgfältige
Prüfung der inneren Überhänge oder „Brücken“ erforderlich sein, um zu verhindern, dass
zusätzliche, unzugängliche innere Stützen erforderlich werden. Wir empfehlen, unsere
DMLS-Designrichtlinien zu lesen, um mehr über die Designanforderungen bei Protolabs
zu erfahren.

die für Überhänge erforderlich sind, die auch zusätzliches Stützmaterial bei der Herstellung erfordern.
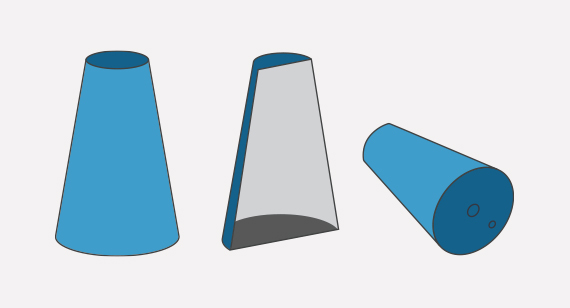
Wenn Sie jedoch ein Design für eine Technologie wie SLS oder MJF entwerfen, bei der der Pulverkuchen selbst zur Unterstützung des Teils verwendet wird, brauchen Sie sich keine Sorgen zu machen. In diesem Fall geht es nur um die Fluchtlöcher für die Pulverentfernung (falls zutreffend). Klemmen, Verschlussteile und Schnappverschlüsse werden bei diesen Technologien in der Regel aus haltbaren Materialien hergestellt. DMLS-Materialien benötigen zum Formen Stützmaterialien. Im Allgemeinen sind Clips, Verschlussteile und Schnappverschlüsse für den Zusammenbau verschiedener traditionell hergestellter Komponenten konzipiert. Mit SLS und MJF, technischen Nylons (gefüllt und ungefüllt) und Polyurethanen können derartige Teile in einer einzigen Baugruppe hergestellt werden. Stereolithographie-Materialien (SLA) sind aufgrund ihrer Sprödigkeit für derartige Teile weniger gut geeignet. Wenn es Ihnen jedoch um Passform und Form geht und Sie weniger an langfristiger Haltbarkeit und Funktion interessiert sind, kann SLA dennoch eine Option für Sie sein.
Bei Clips, Verschlussteilen und Schnappverbindungen, die aus einem Teil bestehen, sollten einige Konstruktionsregeln beachtet werden. Sie sollten wissen, dass diese Teile beim Verbinden am stärksten beansprucht werden. Stellen Sie daher sicher, dass Sie Kehlen in Ihre Konstruktion einbringen, die einen Teil der auftretenden Spannungen abschwächen können. Auch die Integration von Filmscharnieren in Clips und Verschlussteilen kann sich positiv auswirken. Hier ist ein Leitfaden für Filmscharniere, der Ihnen den Einstieg erleichtert. Schließlich ist zu bedenken, dass die Ausrichtung der Teile während der Herstellung ihre Leistungsmerkmale positiv oder negativ beeinflussen kann. Die Teile sollten so ausgerichtet werden, dass die Reibungspunkte weniger belastet werden. Wir können Ihnen dabei helfen, die richtige Teileausrichtung für jede unserer Technologien zu bestimmen, damit Ihre Designziele erreicht werden.
Wir stellen Ihnen Ressourcen zur Verfügung, die Sie bei der Erarbeitung solider Konstruktionsprinzipien für alle von Ihnen erwogenen additiven Technologien unterstützen.
Sie können sich auch mit einem unserer Anwendungsingenieure in Verbindung setzen, um Ihr Design zu besprechen.
Berücksichtigung von Toleranzen für additiv gefertigte Teile
Die Bestimmung der möglichen Toleranzen für jedes einzelne additiv gefertigte Teil kann schwierig sein, da jedes Teil anders auf die thermische Belastung während der Herstellung reagiert. Beim DMLS werden Toleranzen von +/- 0,1 mm bis +/- 0,2 mm + 0,005 mm/mm erwartet und erreicht. Für SLS liegen die erwarteten Toleranzen bei gut konzipierten Teilen typischerweise bei +/-0,2 mm, plus +0,002 mm/mm. Für MJF können in der Regel Toleranzen von ±0,25 mm plus ±0,002 mm/mm erreicht werden. Für TPU-88A Black kann eine Toleranz von ± 0,3 mm plus ± 0,002 mm/mm erwartet werden (bei Teilen, die größer als 100 mm sind, beträgt die Toleranz ± 0,3 % des Nennmaßes). Für PA 12 Flex Black kann eine Toleranz von ± 0,35 mm plus ± 0,002 mm/mm erwartet werden (bei größeren Teilen ansonsten ± 0,2 % des Nennmaßes). Teile, die zum Verformen oder Schrumpfen neigen, können diese Bereiche überschreiten. Jede Geometrie ist einzigartig und verhält sich unter der Belastung während der Herstellung anders. Wenn für ein additiv gefertigtes Teil enge Toleranzen erforderlich sind, müssen diese im Allgemeinen durch wiederholte Vorfertigung oder Nachbearbeitung eingestellt werden.

Ein gut konzipiertes additives Teil kann jedoch die Genauigkeit einer ansonsten komplexen Baugruppe verbessern, indem
Toleranzüberlagerungen beseitigt werden. Ein Teil der Umstellung auf die additive Fertigung eines Produkts kann darin bestehen, die engen Toleranzen auf Einzelteilebene aufzugeben, an die Sie gewöhnt sind. In diesem Fall ist es wichtig, nicht Äpfel mit Birnen zu vergleichen – fragen Sie nicht, ob das neue Teil so genau sein kann wie die Teile, die es ersetzt, sondern ob es so genau sein kann wie die Teile in ihrer Gesamtheit.
Eine weitere schwierige Frage, die es zu stellen gilt: Wie prüft man ein so kompliziertes Teil? Je nach Komplexität kann dies innovative Prüfverfahren erfordern. Auch hier ist zu bedenken, dass die Prüfung des Teils zwar schwieriger sein kann als die bisherigen Kontrollen, doch sie konzentriert sich auf ein einziges Teil anstelle von vielen. Eine Zeichnung mit eingeschränkten Abmessungen für die Inspektion sollte nur die für die Funktionalität wirklich kritischen Abmessungen enthalten. Theoretisch sollte es insgesamt weniger davon geben, da die neu konsolidierte Baugruppe weniger Schnittstellen haben wird. Die alten Schnittstellenpunkte befinden sich innerhalb des neuen Teils.
Nachbearbeitungsoptionen für additiv gefertigte Teile: Spanende Bearbeitung, Gewindeschneiden, Polieren
Denken Sie bei additiv gefertigten Teilen an die Nachbearbeitung, da diese Teile manchmal engere Toleranzen oder bessere Oberflächengüten erfordern, als dies bei
additiv gedruckten Teilen möglich ist. Es ist nicht ungewöhnlich, dass additiv gefertigte Teile bei kritischen Merkmalen wie Dichtungsschnittstellen und anderen
präzisen Passungen nachbearbeitet werden müssen. Eine effektive und kosteneffiziente Abwicklung nach dem Bau erfordert jedoch sorgfältige Überlegungen, um zu vermeiden, dass die Vorteile der Zusammenlegung Ihrer Baugruppe verloren gehen. Versuchen Sie, die Nachbearbeitung so weit wie möglich in Grenzen zu halten – im Grunde bezahlen Sie an dieser Stelle sowohl für die traditionelle als auch für die additive Fertigung. Die Anwendungen, bei denen dies wirtschaftlich sinnvoll ist, betreffen
oft komplexe, hochwertige Geometrien, die wirklich nicht anders hergestellt werden können.

Additiv gefertigte Teile stellen im Vergleich zu herkömmlichen Teilen aus Lagermaterial besondere Anforderungen an die Bearbeitung. Eine dieser Herausforderungen ist die Oberflächenrauheit. Eine unbedruckte Oberfläche ist rauer als ein gewöhnliches Material, was die Messabweichungen bei der Erstellung eines Referenzrahmens erhöhen kann. Dies kann zu einer geringeren Präzision bei bearbeiteten Features führen, die sich auf eine gedruckte Oberfläche beziehen. Sie können auch zuerst den Bezugspunkt bearbeiten. Natürlich muss der erste Schnitt irgendwann an einem unbedruckten Teil erfolgen. Große ebene Flächen auf dem Teil, die sich leicht befestigen lassen, eignen sich in der Regel am besten als erste Bezugsebenen.
Features, die in der gleichen Ebene gedruckt werden, neigen im Verhältnis zueinander zu einem sehr präzisen Druck. So können
die externen Ebenen als Referenz dienen, wenn versucht wird, Features in Bezug auf die interne Geometrie zu bearbeiten.
Wenn Sie für die Nachbearbeitung nur funktionale Gewinde benötigen, ist es eine sehr kostensparende Option, die Gewinde
in das gedruckte Modell einzubauen und sie dann nach dem Bau mit einem Gewindebohrer oder Schneideisen zu schneiden. Die Gewinde sind grob und wahrscheinlich nicht voll funktionsfähig wie gedruckt, aber sie sind präzise genug, um das Werkzeug zum Schneiden brauchbarer Gewinde zu führen. Dies erfordert in der Regel nur minimalen Werkzeugeinsatz und ist eine gute Option, wenn eine lose Gewindeklasse oder Positionstoleranz akzeptabel ist.
Schließlich bleibt noch die Frage der Verbesserung der Oberflächenqualität. DMLS-Teile sind in Bezug auf die Oberflächengüte ungefähr gleichwertig mit Gussteilen, in der Größenordnung von Ra 4-23 μm (je nach Material, Ausrichtung und Auflösung). Die beste Option zur Verbesserung dieser Situation hängt wahrscheinlich von der Anwendung und der
Menge der benötigten Teile ab. DMLS-Teile lassen sich sehr gut von Hand polieren, allerdings ist das ein vollständig manueller Prozess, der eher der Schmuckherstellung als der industriellen Fertigung ähnelt. Mit polierten Oberflächen lassen sich nahezu spiegelglatte Oberflächen erzielen, doch wegen der damit verbundenen Handarbeit ist es schwierig, enge Maßtoleranzen einzuhalten oder größere Stückzahlen zu produzieren. Für funktionale Schaustücke kann dies jedoch eine gute Option sein. Bei SLS- und MJF-Teilen verhält es sich ähnlich, wobei die Verbesserung der Oberflächenqualität in der Regel eine arbeitsintensive Reihe von Schleif-, Grundierungs-, weiteren Schleif- und Lackiervorgängen erfordert, um eine glatte Oberfläche zu erhalten.
Es gibt Optionen für die globale Verbesserung der Oberflächengüte von Teilen, die jedoch oft eine Vorab-Einrichtung und F&E-Kosten erfordern, um den Prozess für eine individuelle Geometrie zu optimieren. Diese Dienstleistungen sind in der Regel nur für Serienteile verfügbar und für Prototypen mit geringen
Stückzahlen nicht umsetzbar.
Skalierbarkeit bei der additiven Fertigung
Der gesamte Aufwand bei der Umwandlung oder Erstellung eines neuen Teils für die additive Fertigung ist möglicherweise nicht sinnvoll, es sei denn, es handelt sich um ein hochwertiges Bauteil oder es besteht Bedarf an einer Kleinserienfertigung. Die additive Fertigung ermöglicht niedrige Einstiegskosten und beschleunigte Fertigungsvorlaufzeiten, die Stückpreise erreichen jedoch viel früher als bei anderen Fertigungsverfahren eine Untergrenze. In der Vergangenheit lag der Break-even-Punkt für traditionell und additiv gefertigte Teile bei Stückzahlen von 10 bis 100, doch neue Fortschritte und Technologien verschieben diesen Bereich in Richtung 100 bis 1.000 oder in manchen Fällen sogar darüber.

Letztendlich hängen die Break-even-Kosten stark von der Größe und Komplexität eines
bestimmten Teils ab. Wenn Ihr additiv gefertigtes Teil viele traditionell hergestellte Teile aus einer ansonsten komplexen Baugruppe kombiniert, kann die additive Fertigung in fast jedem Maßstab wirtschaftlich sinnvoll sein.
Im Allgemeinen beginnen die niedrigsten Preise für additiv gefertigte Teile bei der Menge, die auf einer Plattform für die Einzelfertigung zusammenpassen kann. Zusammengebaute Teile teilen sich die Wiederbeschichtungszeit und reduzieren den Maschinenumsatz, was zu einer effizienten Produktion führt. Kleine Teile können im Extremfall in Losen von 1.000 Teilen oder mehr gefertigt werden; bei größeren Teilen, die annähernd die gesamte Größe einer Baukammer ausmachen, kann die Untergrenze des Stückpreises im Wesentlichen bei der Menge 1 liegen.
Bei kleinen Teilen, die in hohen Stückzahlen gedruckt werden, kann der größte Kostentreiber die Nachbearbeitungsarbeit sein. Die Teile lassen sich zwar in kürzester Zeit in der Maschine formen, aber jedes einzelne erfordert zusätzliches Trägermaterial, damit die Merkmale mittels DMLS geformt werden können. Wenn die Teile nicht ohne zusätzliche Stützen gebaut werden können und einfach per Drahterosion von der Bauplatte abgetrennt werden, ist für jedes Teil ein gewisser Arbeitsaufwand erforderlich, um die zusätzlichen Stützen zu entfernen. Die Konstruktion von Merkmalen zur Bildung selbsttragender Teile ist eine große Chance zur Kostensenkung bei der additiven Fertigung von Großserien. Bei Teilen, die im SLS- oder MJFVerfahren hergestellt werden, umfasst die Endbearbeitung das Entfernen von anhaftendem Pulver aus engen Ecken, Schlitzen oder Löchern. Die Vereinfachung von Oberflächen für eine einfache Reinigung nach der Fertigstellung kann den Arbeitsaufwand und die Kosten reduzieren.
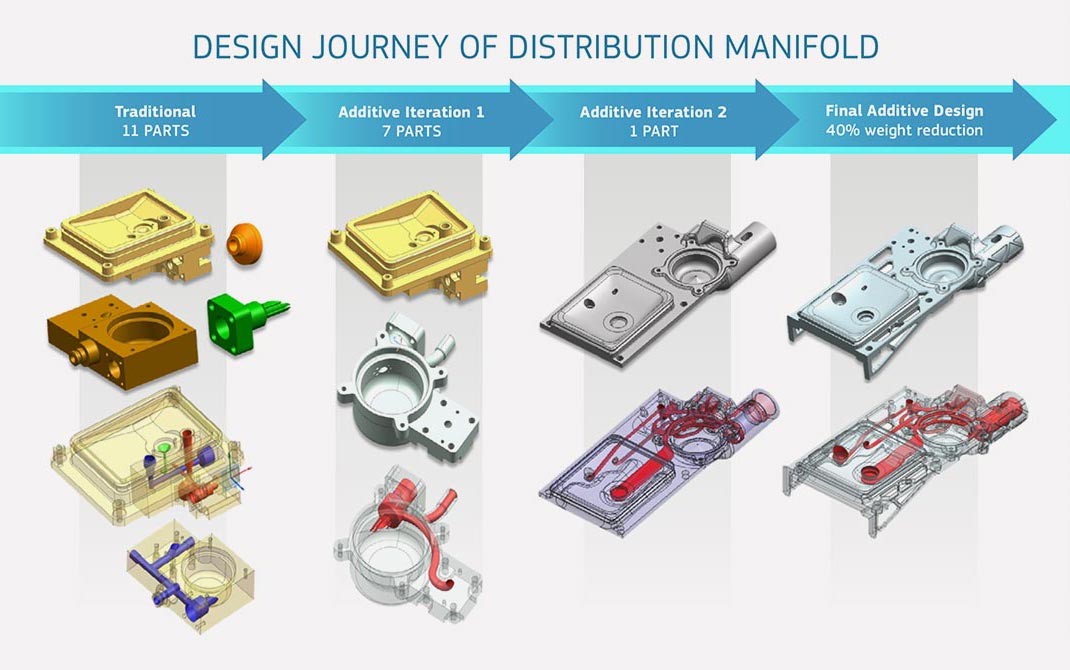
Bei größeren Teilen, die z. B. aus einer kombinierten Baugruppe stammen, kann der Preis hauptsächlich durch das Gesamtmaterialvolumen des Teils bestimmt werden. Dicke, einfache Querschnitte mögen in der traditionellen Fertigung keine zusätzlichen Kosten verursachen, doch in der additiven Fertigung verursachen sie erhebliche Kosten, da sie die Bauzeit verlängern. Außerdem können sie zu einem qualitativ minderwertigen Teil führen, da sie das Risiko des Verformens bei der Herstellung erhöhen. Der Leichtbau von Teilen für die additive Fertigung kann nicht nur die Leistungsfähigkeit verbessern, sondern ist in den meisten Fällen auch kostensparend.
Bei Protolabs fertigen wir großformatige Metallteile mit dieser GE Additive Concept Laser X Line 2000R Maschine. Es handelt sich um das weltweit größte additive Metallpulversystem, das Metallteile in Produktionsqualität in der Größe von EOS M300 herstellen kann, das nur Aluminium mit 300 x 300 x 400 mm (normale Auflösung) entspricht.
Wann man bei der traditionellen Fertigung bleiben sollte
Nicht jede Anwendung eignet sich für die additive Fertigung. Teile mit geringem Wert und hoher Stückzahl eignen sich immer besser für andere Fertigungsverfahren. Es ist sehr selten, dass ein Teil, das bereits erfolgreich mit anderen Fertigungsverfahren hergestellt wird, ohne Änderungen und zu geringeren Kosten in die additive Fertigung überführt werden kann.
Damit ein maschinell bearbeitetes Teil direkt in die additive Fertigung überführt werden kann, muss die Bearbeitung im Ist-Zustand extrem schwierig oder teuer sein. Um Additive für ein bestehendes Teil sinnvoll zu machen, müsste es sich um ein Teil handeln, bei dem derzeit mehr Material weggefräst wird als im Endergebnis übrig bleibt. Wenn zwei (oder mehr) maschinell gefertigte Teile zu einem einzigen additiv gefertigten Teil kombiniert werden, müssen sie wahrscheinlich beide einzeln schwer zu fertigen sein. Im Idealfall sollten sie so kombiniert werden, dass Ihr Produkt auf eine Art und Weise verbessert wird, die auf keine andere Weise erreicht werden kann. In den meisten Fällen sollte ein Produkt, das maschinell bearbeitet werden kann, auch auf diese Weise bearbeitet werden..

Größe und Material sind jedoch wichtige Faktoren für Teile, die möglicherweise kostengünstiger sind, als man denkt. Sehr kleine Teile, die normalerweise mikrobearbeitet werden müssten, können mit DMLS erstaunlich günstig hergestellt werden, da die Kosten an das Materialvolumen gebunden sind. Ein Teil, das nur ein paar Gramm wiegt, wird wahrscheinlich zu den billigeren DMLS-Teilen gehören, selbst wenn es vom Design her extrem komplex ist. DMLS ist auch für schwierige Werkstoffe wie Inconel oder Titan geeignet, die maschinell bearbeitet werden müssen. Der Preis für ein bestimmtes maschinell gefertigtes Teil aus Titan kann im Vergleich zu Aluminium erheblich abweichen; bei additiver Fertigung wird der Preis eher vergleichbar sein.
DMLS kann auch eine großartige Überbrückung für die Prototypenherstellung von Gussteilen sein – aber auch hier ist es selten, dass DMLS aus preislicher Sicht langfristig mit Gussteilen konkurrenzfähig bleiben wird. Der beste Anwendungsfall sind Spezialvarianten in kleinen Stückzahlen für kundenspezifische Aufträge, bei denen sich das Gießen nicht wirklich lohnt oder bei denen lange Vorlaufzeiten für die Herstellung der ersten Teile nicht ausreichen.
Bei Kunststoffen sind der Umfang und wiederum die Komplexität entscheidend. Wenn Sie für Ihr Produkt voraussichtlich mehr als 1.000 Teile benötigen, ist es wahrscheinlich am besten, wenn Sie einen Weg finden, Ihr Teil spritzgussfähig zu machen. Typische Anwendungsfälle für additive Kunststoffe bei höheren Produktionsmengen sind Szenarien, in denen die Anzahl der Teile und der Arbeitsaufwand für die Montage erheblich reduziert und gleichzeitig die Leistung verbessert wird. Drohnen sind ein großartiges Beispiel dafür – ein komplettes Chassis für eine Drohne kann als ein einziges Stück gedruckt werden, das für eine optimale Leistung ein geringes Gewicht aufweist und keine Montage erfordert. Auch die Schuhindustrie investiert derzeit stark in die additive Fertigung, z.B. für maßgeschneiderte Zwischensohlen.
Die Umstellung einer bestehenden Baugruppe auf eine konsolidierte additive Fertigung kann schwierig sein. Additive sind eine wirksame Lösung, wenn sie einsetzbar sind, doch nicht jede Situation erfordert sie zwingend. Daher ist es hilfreich, einen Anbieter zu wählen, der beides anbietet. Bei Protolabs scheuen wir uns nicht, Ihnen zu sagen, ob sich Ihre Anwendung besser für eine andere digitale Fertigungsoption wie die maschinelle Bearbeitung oder das Spritzgießen eignet. Wenn Sie neu im Bereich der additiven Fertigung sind und herausfinden möchten, wie sie funktioniert, sprechen unsere Anwendungsingenieure gerne mit Ihnen über Ihr Design und Ihr Produkt. Kontaktieren Sie einen unserer Ingenieure unter +49 (0) 89 90 5002 0 oder unter [email protected]