
As the world-leading source of digital manufacturing services we are proud to officially open our new 3D printing centre of excellence in Putzbrunn near Munich. The centre is a world class facility that contains future-oriented technologies, highly skilled employees and a host of sustainable benefits.
The expansion means our customers will now be able to access even faster lead times and more than 60 industrial 3D printers offering metal and plastic parts through a range of additive manufacturing technologies.
It is perfect timing, with clients in the automotive, aerospace, electrical, industrial, medical and energy sectors looking to invest following the easing of lockdown.
"We are very pleased about the opening of our new European 3D printing center in Putzbrunn and the strategic importance it will have for customers in the UK," explained Bjoern Klaas, Vice President and Managing Director of Protolabs Europe.
"The new production facility expands our capacity and enables further growth for pioneering 3D printing technologies in the future. Our customers will enjoy an even greater range of services and this latest investment will undoubtedly help us meet our promise of delivering prototypes and low-volume production parts in just a few days."
We’ve also enhanced our commitment to the environment with several sustainable features included in the design of the Putzbrunn plant as part of our ISO 14001 certification and our desire to save resources and reduce our CO2 footprint.
This is already evident in energy consumption alone, which has been reduced by leveraging the capabilities of heat recovery and waste heat utilisation, as well as the intelligent linking of engineering processes.
The new location, which keeps noise emissions below 26 decibels, also includes charging facilities for electric and hybrid vehicles in its own parking garage and draws on a mix of green electricity.
"The opening of the 3D printing centre illustrates our long-term corporate strategy, which is geared towards fast evolving technologies, rapidly shifting markets, environmental considerations and world-class employees,” added Bjoern.
"In doing so, we want to fulfil our social responsibility, as well as deliver an unparalleled service through digital manufacturing. This approach enables our customers to more rapidly develop their products, go to market faster, reduce manufacturing costs and achieve a flexible supply chain throughout the entire product lifecycle.”
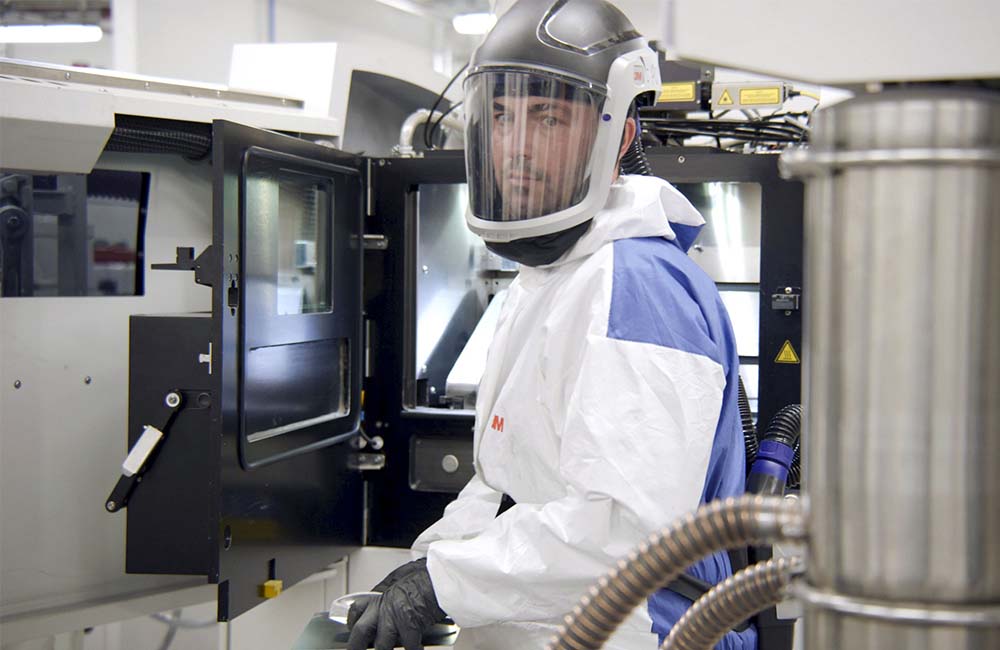
