Building supply chain resilience: five solutions for strengthening your supply chain
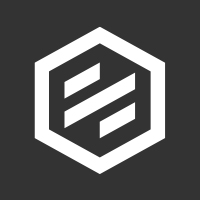
As the complexity of supply chains continues to grow and the number of unforeseeable disruptions increases, it is essential for businesses to develop a risk management strategy to address future disruptions. These strategies can help organisations identify potential risks and vulnerabilities in their supply chain and develop plans to mitigate those risks before they become major problems.
Unfortunately, despite facing significant supply chain disruptions in recent years, many organisations remain unprepared for future risks. A recent survey conducted by Hubs* found that approximately 30% of respondents had not taken any steps to improve the resilience of their supply chain. Which is surprising given that 76.6% of surveyed companies experienced disruptions caused by external factors in 2022. It is clear that more needs to be done to ensure that businesses are able to withstand future supply chain disruptions.
For organisations looking to build a resilient supply chain, this blog focuses on five key elements necessary for preparing for future disruptions.
Automation
Automation can improve supply chains by increasing productivity and efficiency. These processes can mitigate the effects of certain supply chain risks, particularly those related to labour shortages and lockdowns. With Robotic Process Automation, (RPA), many repetitive manual tasks can be digitised and streamlined, reducing supply chain complexity and reducing reliance on manual labour. In 2021, 78% of organizations were already using RPA technologies, while only 6% had no plans to implement it.[1]
Automation is particularly advantageous for its ability to speed up processes that can slow down supply chains if done manually. Request for Quote, (RFQ) and Design for Manufacturability, (DFM) processes can be automated, providing clients with accurate quotes within seconds, rather than days or even weeks. Protolabs’ automated design analysis takes your CAD and within a couple of hours provides feedback on whether your design is manufacturable. It also helps identify any particularly challenging features and provides suggestions on how to improve manufacturability. You can submit your part for analysis and quote as many times as you want, at no cost. Learn more about Protolabs’ DFM feedback here.
Automation across the supply chain also enables businesses to break down silos and streamline the sharing and access of data between supply chain links. Digital Process Automation
(DPA) creates greater efficiency by integrating various platforms used in the supply chain, effectively bridging processes and creating greater transparency and visibility. This in turn empowers suppliers to monitor processes and identify inventory needs as well as supply chain bottlenecks and weaknesses.
Reserve inventory
Though it goes against lean manufacturing strategies, building a reserve inventory can improve supply chain resilience substantially. It effectively creates a buffer so that if or when a link in the supply chain fails, there is enough inventory to keep things up and running while the link is re-established. It is particularly valuable to have reserve inventory for critical parts and parts that could not easily be sourced from alternative suppliers.
The challenge to the broad adoption of reserve inventory strategies has been cost. However, as AI-driven cost analyses and predictions become more popular, supply chain partners will be able to more accurately predict the probability and cost of supply chain disruptions and weigh those against the costs of reinforcing inventories. In other words, intelligent technologies can make supply chains less reactive and more proactive. Predictive models can also help indicate other changes, such as demand drops or surges, which can help keep production and inventory levels in line with changing consumer trends.
As well as reserve inventory, working with on-demand production partners can also add flexibility to the supply chain by effectively managing demand volatility and reducing inventory costs. Dependent on your product, reserve inventory or on-demand production could play an important part in your long-term supply chain resilience strategies.
Geographical diversification
Diversifying supply chains is essential to building resilience. Many recent events have demonstrated this: pandemic lockdowns in China brought manufacturing to a standstill at various times between 2020 and 2022; while Europe's over-reliance on Russia for gas is leading to significant energy shortages.[2] In Hubs’ latest survey, they found that 41% of companies believe diversifying their supply chain is the best way to avoid disruptions in the future.
With a strong, distributed network of suppliers or potential suppliers, supply chains can adapt in the face of regional disruptions and changing geopolitics. If one geographic region goes down, suppliers in another can step up and fill the gap.
Enabling the greatest number of qualified manufacturers possible is a critical step to diversifying supply chains. The more complex a product is to make, the more specialized a manufacturer will have to be, which narrows the pool of possible production partners. By simplifying product designs, whether through consolidation or the elimination of complex features, companies will have access to a greater number of potential suppliers.
Protolabs have in-house digital manufacturing factories across the US and Europe as well as an extended global digital network of premium manufacturing partners powered by Hubs, you can learn more about our modern manufacturing model.

Agile internal processes
Supply chain resilience is not only about adding flexibility externally – internal processes are also paramount. Start-ups are typically associated with agile processes, with team members working quickly and dynamically to grow business, but larger organisations can also benefit from agility. By encouraging cross-functionality and greater autonomy across teams, internal processes like product development become faster and more flexible. An agile strategy prioritises collaboration with clients or stakeholders throughout every stage of development as well as continual improvements based on feedback. This ultimately leads to superior product quality, process transparency, and efficiency, as well as lower risk, since the project is being monitored and evaluated at every step. With an agile methodology, your internal processes will be more flexible and can seamlessly adapt to market changes. For example, 93% of businesses reported that their agile business units fared better than non-agile business units during the pandemic.[3]
Protolabs’ digital quoting platform allows you to easily forward a quote to share with colleagues, managers and procurement teams and allows all collaborators to adjust turn time, materials, finishing, and other options whilst seeing a real-time price impact. This feature enables engineers and purchasers to share and review order details in a single place, making it easier and faster to order parts. This can help improve the efficiency of your team's workflow and reduce the time it takes to order parts.
Supply chain monitoring
In the manufacturing industry, tier-one suppliers are companies that supply parts or materials directly to the original equipment manufacturer (OEM). Tier-two suppliers are vendors that provide parts or materials to tier-one vendors, and tier-three suppliers are companies that provide parts or materials to tier-two. Generally, most businesses only monitor tier one and tier two suppliers as they are considered the most important. However, that's not ideal because even tier-three suppliers can still play a significant role in the overall supply chain. Delays caused by deeper-tier suppliers can cause disruption throughout your entire supply chain. By closely monitoring suppliers across all tiers, you'll be able to spot any warning signs well before the consequences of disruption take effect.
However, monitoring your supply chain from the raw materials to the finished product can be a complex and lengthy process. This may explain why this approach was the least popular according to the survey, with only 11.6% of respondents selecting thorough monitoring of supply chain as an effective measure to reduce the effects of supply disruptions.
Thankfully, specialised software tools have simplified the supply chain monitoring process. Additionally, companies are exploring emerging technologies such as AI and machine learning for supply chain optimisation. While only 13.1% of surveyed companies revealed using AI and ML, a resounding 90.9% of the users found it to be useful.
- Supply chain mapping to monitor not only tier one and tier two suppliers, but the entire supply chain
- 24/7 supplier monitoring which alerts you to disruptions that may affect your suppliers
- Risk calculation of disruptive events with the potential revenue lost
Conclusion
As the past few years have shown us, disruption in the supply chain can happen at any time and is therefore critical for organisations to transform and upgrade their supply chain processes to minimise vulnerabilities and achieve greater resilience.
Fortunately, there are many tools and strategies for building a resilient supply chain that organizations can use. Automation technologies, diverse supply networks, agile internal processes will help establish a robust, future-proof supply chain that can withstand a wide array of disruptions. Resilience is a must for organisations looking to succeed over the long term and adapt to whatever the future brings.
--
-
Automation with intelligence: Pursuing organisation-wide reimagination. Deloitte, 2021.
-
Share of gas supply from Russia in Europe in 2021. Statista, October 7, 2022.
-
Agile resilience in the UK: Lessons from COVID-19 for the ‘next normal’. McKinsey, October 13, 2020.