3D Printing Part Orientation: How it Affects Strength, Accuracy, and Surface Finish
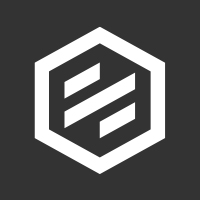
It may seem like a no-brainer to opt for the orientation that offers the minimum z-height, and thus the quickest build time. But, orienting solely for z-height may not always make the most sense in terms of your part requirements. There are a few other technical factors that come into play when thinking about part orientation for 3D printing. When you think about part orientation for 3D printing—specifically stereolithography (SLA)—think of a pencil. What would it take to 3D-print this pencil layer-by-layer either horizontally or vertically? Doing it horizontally would take less time, because it’s flatter when lying on its side, and printing it vertically would take substantially longer, because it’s standing tall and requires more drawn layers stacked sequentially one on top of another. Printing it horizontally would also require more support structures compared to printing the pencil vertically, and those would require additional time to remove to achieve a finished part. So, your orientation selection could come down to strength requirements or surface finish requirements for your pencil, and you may even want to orient your part at an angle. There are a handful of considerations when selecting stereolithography build orientation. Let’s get into it!
3D-printed Part Orientation for Strength
Let’s first look at a quick illustration that explains the general implications of 3d printing layer buildup and external part forces on parts. When tension forces are normal, or perpendicular, to the layers, part weakness tends to occur. When tension forces are parallel, or in line with the layers, the part is stronger. When forces are normal to the layers, the part is generally able to accommodate more compression than if forces are in line with the layers. Two takeaways apply:
- Print in an orientation so that layers align with the axis where tension forces are highest and
- Print in an orientation so that layers intersect the axis where compression forces are highest
In the theoretical case of the pencil, a horizontal build orientation will likely work to account for the tension and bending forces the pencil will encounter when in use. Note that these guidelines always apply to Fused Deposition Modelling, (FDM) parts. SLA parts exhibit much less anisotropy than FDM parts because layers are chemically bonded, and the resolution achieved with SLA is much higher than with FDM. However, thermoset materials may require some additional thought around part orientation to maximise the strength of critical part features.


Orienting to Avoid Differential Shrink
In general, the more unequal distribution of material there is in a part, the more prone it is to fall victim to a phenomenon known as differential shrink. Certain part geometries and sizes are inherently more likely to shrink because they don’t include adequate support from the preceding layers of material. To illustrate this, think of a capital letter “H.” When the crossbar section appears layer-by-layer in the middle, it tends to pull the supporting legs inward, causing the part to bow near the bottom. To prevent differential shrink, there are a couple of options. Often, we build SLA parts on an angle to reduce the surface area, and thus the overall stress encountered for each layer. This also helps increase part dimensionality and tolerancing accuracy. In addition, we build parts lying down so that each layer formed is the same surface area as the layer beneath it, and there are no large cross-sectional swings. When dimension critical or high-resolution part features are required, we advise that parts are oriented to position those features on the up facing surface of the part. Keep in mind that building parts on an angle can result in parts with non-ideal surface finish if cosmetics are key.

Differential shrink can be avoided by orienting to eliminate small to large cross-sectional changes on the part (shown above) or by orienting the part at an angle (shown right).

If smooth, cosmetic features are the goal, build parts vertically. Building at an angle will cause visible layer lines as shown on the angled cylinder.
Orienting to Achieve Desired Surface Finish
If it’s important for your part to have a cosmetic finish for use in a tradeshow or on display, we will tend to build the part flat and not at an angle. Any critical features should face up, as the top surfaces will be smooth and more prone to dimensional accuracy. On the other hand, if your part is built facing down, support structures that need to be removed and blasted would eliminate any glossy effect.

The glossy effect is shown on the “H” that was built lying flat. The “H” built at an angle highlights layer lines and the visual effects they can have on text.
As a rule of thumb, our team may choose a different orientation to provide you with the best quality part. One important thing to keep in mind is that if you don’t specify a desired part orientation (horizontal vs. vertical), we will choose the orientation we think is the best trade-off between fastest possible build time and good optics. Letting us know what aspects are most vital to your 3D-printed parts helps us determine how best to orient your part during the build process. Overall, the biggest takeaway is that if you have a particular need for a 3D-printed part, whether it's critical features, cost consideration, or a specific desired surface finish, be sure to let our team of engineers know in advance so we can ensure your part meets your specific goals.
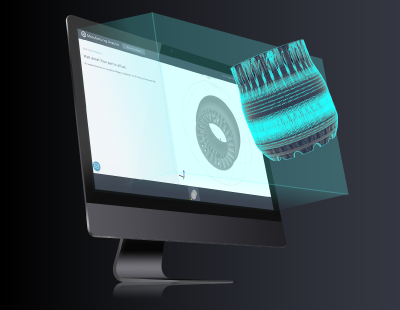
Need custom 3D-printed parts? Upload your CAD file for an instant online quote.
Get Printed Parts