Game Changing Innovations
Digital Manufacturing in the Sporting Industry
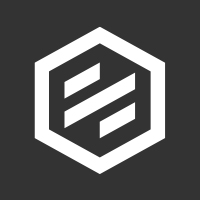
When someone says “digital manufacturing”, you probably think of parts being produced for cars, planes, and possibly even medical devices; it’s unlikely you think of the sporting industry. But digital manufacturing is increasingly shaping the industry through innovations that enhance performance, customisation, sustainability and overall user experience.
In this blog, we will look at ways digital manufacturing supports the sports industry.

Lightweighting - Not just important for increasing fuel efficiency in rockets and aircraft by making lighter frames and panelling, lightweighting is proving just as important in the sporting industry and it’s not just for bicycle bodies. The process of lightweighting is innovating many different areas of sport, from tennis rackets and golf clubs, designed lighter for enhanced manoeuvrability, to running shoes and protective gear to improve performance and protection without compromising mobility. 3D printing (also known as additive manufacturing) builds parts layer by layer and can create hollow and lattice structures, using less material and, as a result, creating lighter overall parts.
Besides offering enhanced performance, lightweighting is beneficial for several other reasons, including sustainability, customisation, innovation and cost efficiency.
Intricate Geometries – Aside from lightweighting, the intricate geometries that 3D printing achieves deliver fascinating benefits. By creating a part layer by layer, there are no traditional tooling constraints, and complex structures can be achieved. CNC machining also comes to the fore here, as CNC machines often feature multi-axis capabilities (e.g., 3-axis, 4-axis, 5-axis, and beyond). These additional axes allow the machine to simultaneously move the cutting tool and workpiece in multiple directions, creating highly intricate and complex shapes.
Some examples of intricate geometries in sport include:
- Footwear with customised cushioning and support for enhancement of comfort and performance.
- Helmets with honeycomb and other lattice structures that enhance impact absorption and offer safer pressure distribution from physical impacts.
- Golf Clubs with advanced internal geometries that optimise weight distribution allowing for an improved swing and offering better control.
Intricate geometries can enhance performance, reduce weight, provide better customisation, improve material efficiency, and facilitate product innovation.
Material Innovation – Material versatility in injection moulding, CNC machining, and 3D printing significantly enhances the sports industry by enabling the creation of high-performance, durable, and customised equipment. Injection moulding utilises high-performance plastics like polycarbonate, nylon, and TPU, as well as reinforced polymers, to produce impact-resistant and flexible protective gear and rigid parts for athletic footwear. CNC machining works with high-strength metals such as aluminium, steel, and titanium and precisely machines advanced composites and alloys, resulting in durable, lightweight components for bike frames, golf clubs, and motorsports. 3D printing leverages high-performance polymers and metal printing with materials like titanium and aluminium to create strong, lightweight parts for custom bicycle frames, protective gear, and prosthetics, promoting innovation and performance in various sports.
Enhanced Customisation – 3D printing, in particular, enables highly customisable parts such as custom-fit helmets (designed using 3D scans of an athlete’s head), midsoles with custom lattice structures tailored to an individual’s weight and running style, bikes designed to fit individual body type and riding style, and compression wear custom-fit to improve circulation and muscle fatigue.
Enhanced customisation can offer improved performance, increased comfort, a personalised experience, innovative designs and reduced weight. CNC machining allows for precise customisation of sports equipment tailored to individual athletes’ needs. For instance, custom bike frames, golf clubs, or prosthetics can be produced to fit the athlete's exact specifications.
At Protolabs, when it comes to the sports industry, we’re in the game! We’re certainly no strangers; here are a few examples of companies we have worked with and the parts they successfully created after partnering with us.
We have more sporting case studies available on our website.
The sporting industry may not be the first industry you think of when it comes to digital manufacturing, but uptake by the industry is undoubtedly increasing, especially because of the intricate geometries, lightweighting, and customisation options that digital manufacturing offers.