How to select the best manufacturing process for your Part
Injection Moulding vs. CNC Machining vs. 3D Printing
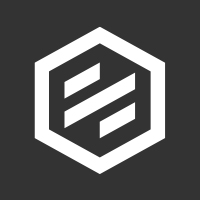
There are various manufacturing processes available for plastic, elastomer, and metal materials. In this blog, we will focus on injection moulding, CNC machining, and 3D printing.
What does the manufacturing landscape look like?
While sharing similarities, injection moulding, CNC machining, and 3D printing are different approaches that can support different needs. Certain parts and products are better suited to one service than another, whether because of the material used, quantity, surface finish, or functionality.
Injection moulding and CNC machining are subtractive processes, which means the material is removed from a block to create a part. While injection moulding injects molten plastic into a hollowed-out mould, CNC cuts away at a block using a mill or lathe.
3D printing is slightly more sustainable because it is an additive process. This means that material is added layer-upon-layer to create a part, meaning less waste.
Achieve precision with CNC machining.
Why is CNC machining a great option?
Where high precision is crucial, CNC machining is the perfect choice. It can produce parts with incredible accuracy, often within a tolerance of just a few microns. In addition to being highly precise and accurate, parts produced using CNC machining are consistent, repeatable, versatile, and efficient.
What are the main applications of CNC machining?
CNC machining has applications in most industries. It tends to be favoured by the aerospace and automotive industries for use in parts such as engine components, transmission parts, turbine blades, airframe components and more. That’s not to say other industries don’t use it; CNC machining is highly adopted by the medical industry, electronics industry and more.
Define intricacy with 3D Printing.
How does additive manufacturing work?
Additive manufacturing, also known as 3D printing, is a term used to describe several different technologies that build parts layer-by-layer. Some examples of additive manufacturing technologies include Stereolithography, Selective Laser Sintering, Direct Metal Laser Sintering, Multi-Jet Fusion, Fusion Deposition Modelling, and more.
Some 3D printing machines will use an extruded filament to produce parts, whilst others use layers to sinter or cure materials such as metal or plastic powders and liquid resins.
What is the best application for 3D printing in manufacturing?
3D printing has many applications, but perhaps one of its best is its prototyping applications. It’s fast, cost-effective and allows design flexibility, making it perfect for testing part functionality at the start of your product lifecycle. But 3D printing isn’t limited to prototypes; it is good for a wide range of applications; some notable uses include tooling and fixtures, customised and personalised parts, complex and lightweight structures, replacement parts and small batches of end-use parts such as aerospace components, medical implants, and custom automotive parts.
Be versatile with injection moulding.
How does the injection moulding process work, and where does it sit in a product's lifecycle?
Injection moulding will play a crucial role in the lifecycle of a product created using this process.
- Product Design – While the process is not being used here, the part is designed with injection moulding in mind. During this stage, the designer will consider the part's manufacturability and work to ensure it can be produced using injection moulding. Design for Manufacturability, or DFM, can help; the software will highlight any areas of the product that are not manufacturable and why. It will also highlight any potentially problematic areas, such as areas with too thin walls or a feature too small. DFM also supports iterative design, enabling the designer to keep designing and sending for feedback until the part comes back as manufacturable and without defects.
- Prototyping and Testing – While 3D printing is the go-to for prototyping, injection moulding can and is also used for producing prototypes for functional testing. From these functional tests, it can be determined whether further modification is required before proceeding with production.
- Low-Volume Production – small batch production for pilot runs, part validation and customer feedback.
- Growth / High-Volume Production – on-demand production runs. When your product is fully tested and launched.
- Maturity – perhaps lower production runs/supply chain emergencies to fill the gap.
- Decline – Declining production runs, end-of-life planning. Perhaps circling back around to produce version 2.0 of a product.
What industries typically benefit from injection moulding?
Injection moulding is a versatile and efficient manufacturing process that is used across a wide range of industries. Its ability to produce high volumes of complex and precise parts with consistency and quality makes it particularly attractive to most industries.
Some examples of how injection moulding has benefited key industries include,
- Automotive industry – dashboards, bumpers, door panels, small engine parts
- Consumer industry – household items, toys, kitchen utensils, storage containers
- Electronics industry – housings for electronic devices, connectors, switches, various smartphone components
- Medical industry – surgical instruments, housings for medical equipment, disposable items such as syringes and containers
- Packaging industry – caps and closures, bottles, containers, packaging for food, beverages, cosmetics, and pharmaceuticals
- Construction industry - fixtures, fittings, pipes, panels
- Aerospace industry – components for aircraft interiors, lightweight structural parts
- Agricultural industry – components for machinery, components for irrigation systems, plastic parts used in farming.
- Lighting Industry – lenses, fixtures, covers for LEDs and fluorescent lights, reflectors.
Manufacturing processes compared.
In this section, we compare the main manufacturing processes and provide insight into how to decide on the best process for your needs.
Injection moulding is ideal for high-volume production and complex geometries with detailed features and material variety. Usually, the service is split between prototyping and on-demand production runs. On-demand services mean that injection moulding can be more cost-effective in the long run.
CNC machining is ideal for scenarios where high precision, tight tolerances, and complex shapes and features are required. It is more comfortable with low levels of production and offers a wide range of materials, including metals.
3D printing is perfect for rapid prototyping; its quick turnaround times and lower costs in relation to other processes make it perfect for quick iteration. Its near-limitless design also makes it perfect for complex structures that are too complicated to be moulded or machined. Due to the complexity it offers it is also great for lightweighting structures. Its quickness also enables better opportunities for customisation and personalisation of parts.
So, how do the services compare? See the handy table we created below, which highlights ideal quantities, turnaround times, materials, and much more for each service.
Injection Moulding | CNC Machining | 3D Printing | |
---|---|---|---|
Quantity | 25 to 10,000+ parts | 1 to 200+ parts | 1 to 50+ parts |
Speed | 1-15 days | same day - 3 days | 1-7 days |
Material Options | 70+ grades of thermoplastic/ thermoset resins | 40+ grades of plastic and metal | 25+ grades of plastic and metal |
Surface Finishes | PM-F0, PM-F1, PM-T1, PM-T2, SPI-C1, SPI-B1, SPI-A2 | As-machined, deburred, or deburred with a light bead blast | Painting/dying, vapour smoothing, polishing, bead blasting |
More offered by our network | More offered by our network | More offered by our network | |
Design Limitations | Limitations highlighted in Design for Manufacturability Feedback | Limitations highlighted in Design for Manufacturability Feedback | Almost limitless design (any limitations highlighted in design for manufacturability feedback) |
Support Available | Dedicated Account Mgr and Applications Engineer/ Consultative Design Service | Dedicated Account Mgr and Applications Engineer | Dedicated Account Mgr and Applications Engineer / Project Management Service |
What are the advantages and limitations of manufacturing processes?
Each manufacturing process has benefits and limitations, so let’s compare. Perhaps it will give you further insight and help you decide which process is best for you.
Injection Moulding | CNC Machining | 3D Printing | |
---|---|---|---|
Benefits | Lower cost at higher volumes Functional Parts Repeatable Complexity Wide range of materials Prototyping, bridge-tooling and low-volume production |
High Accuracy and Precision Low-volume parts Repeatability Functional Parts Complexity |
Prototyping and concept testing Low-volume parts Bespoke customised parts Speed and complexity Functional/ aesthetic components Reduced waste compared to other processes Design flexibility Lightweighting |
Limitations | Longest lead times Higher costs Higher material waste More design constraints than other services Initial costs |
Higher costs Higher material waste |
Reduced material choices Size constraints Additional post-processing time and cost for better surface finishes |
How to determine the best manufacturing process?
When determining the best manufacturing process, the main considerations are regarding your part. What will your part be used for? What material does it need to be made from? How quickly do you need it? What budget are you restricted to?
All of these questions can help you narrow down your search for the perfect fit for you.
As highlighted previously and in the tables above
Injection moulding – best for higher production volumes, is consistent, repeatable and offers a massive number of materials to choose from.
CNC machining – ideal for high-precision parts in lower quantities, has a wide range of materials available, including metals.
3D printing - perfect for rapid prototyping, customisation, complex geometries and lightweighting.
Where has each manufacturing process been successful?
Let’s have a look at some real-life examples of each process and how they have supported customers.

PepsiCo achieves highly complex parts in low volumes to support a Marvel promotional campaign with 3D printing services.
PepsiCo came to Protolabs looking for a solution for low volumes of highly complex parts to support a promotional campaign in advance of Marvel’s “Black Panther” movie premier.
After evaluating several 3D printing processes, the team selected Multi Jet Fusion. It offered precise parts at the lowest cost and the components had the durability to last for several years.
The result was a 3D-printed Black Panther mask that served as the centrepiece for an online promotional campaign that generated over 10 million social media impressions.

On-demand injection moulding for Polarcool to gain agility
Polarcool had developed a device to rapidly lower the temperature of the brain in a controlled manner following sporting head trauma. Protolabs had already previously supported the production of 3D-printed prototypes. Polarcool then required support moving to production.
Working together with guidance from Protolabs’ expert support team, casing and internal parts were manufactured using Protolabs’ rapid injection moulding service, ultimately accelerating the development of a product that can prevent long-term injury and save lives.

CNC machining creates Moverio prototypes for Epson
Japan-based Seiko Epson Corporation utilised Protolabs’ rapid CNC machining services to provide quick-turn prototypes that helped Epson enhance the comfort of its lightweight, high-resolution Moverio glasses.
Epson later went on to use Protolabs’ injection moulding services in newer devices of the Moverio professional models.
What are the future trends in the manufacturing industry?
The manufacturing industry is undergoing a transformation, with AI, automation, and robotics at the forefront and an increasing focus on sustainability.
Here are some of the key and Future trends,
- Industry 4.0 and Smart Manufacturing – enhanced automation, real-time monitoring, predictive maintenance, and optimised/ integrated/ automated production processes. Digital twins for simulation, improved design, real-time monitoring, and proactive maintenance strategies.
- Additive Manufacturing – constantly evolving and changing the manufacturing landscape. Reduced lead times, customisation, and larger build volumes.
- Advanced Materials – research into nanomaterials, bioplastics and smart materials.
- Robotics and Automation – Increased use of cobots (collaborative robots), AGVs (autonomous guided vehicles), and RPA (robotic process automation). Leading to higher productivity, improved safety and the ability to operate 24/7.
- Sustainable manufacturing – energy efficiency, waste reduction, recycling, renewable energy sources.
- Customisation and Personalisation – increased desire for differentiation from customers, enabled by flexible manufacturing systems, advanced software and additive manufacturing.
These are just some of the trends shaping the manufacturing landscape at the moment and will continue going forward, with a huge focus growing on sustainability, customisation and automation. Staying ahead of these trends requires continuous investment in technologies, workforces and strategic planning.