Protolabs Switches Additive Manufacturing for PA11 Black to MultiJet Fusion for Better Results
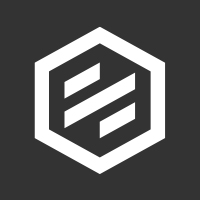

Protolabs has switched all of its 3D printing of PA11 Black Nylon from selective laser sintering (SLS) to multi jet fusion (MJF) because it produces better material characteristics using this process.
Offering six different additive manufacturing technologies, including both SLS and MJF, the company has made the decision to ensure that customers get the best results.
Says Andrea Landoni Product Manager for Protolabs, “We have a number of different technologies so that we can best match a process to the customer’s project for rapid prototyping or producing final parts. For PA11 Black, MJF produces better results than SLS so we have decided to switch all additive manufacturing production to this technology for the material.”
PA11 Black is a commonly used material for industrial applications because it has excellent ductility and temperature resistance with a good tensile strength. It also has one of the highest elongation to break thresholds of any nylon, which makes it a good choice for functional moving parts such as snap fits and living hinges.
Using MJF to produce parts instead of SLS further improves its elongation at break and also produces better isotropic mechanical properties. In addition, the process creates water and airtight parts without further treatment and Protolabs offers more secondary services for the process including vapour smoothing.
Protolabs provides six different additive manufacturing processes, CNC machining and injection moulding. After uploading your CAD onto our systems, we will produce a quote and a design for manufacturability analysis report within a few hours. Our application engineers are also available to advise on the best process and material for your next project.
For further material information, check our Multi Jet Fusion design guidelines page here.