Material Hardness Testing
How to test the hardness of your material, using Brinell, Rockwell, Vickers or Leeb testing methods.
The 'hardness of a material' refers to the materials ability to resist deformation, indentation or scratches. There are several different tests used to display the hardness of materials including, Brinell (HB), Rockwell (HRC), Vickers (HV)and Leeb. In the guide we'll walk you through the ins and outs of each. Read on to learn more.
Rockwell tends to be the most commonly used way of testing hardness, due to its speed and simplicity. It is also suitable for a wide range of materials including metals, plastics and ceramics. The Rockwell test offers several different scales (A,B,C etc.) based on different combinations of indenter types and applied loads.
Which material hardness test should I use?
- If you need a quick, non-destructive measurement for a variety of materials in a manufacturing setting – the Rockwell hardness test is suitable.
- For softer materials or materials with coarse microstructures – the Brinell hardness test is suitable.
- When you require precise measurements for materials with high hardness or thin coatings – the Vickers hardness test is suitable.
- When needing to perform hardness testing on-site or non-destructively – the Leeb hardness test provides portability and convenience.
At Protolabs the majority of our datasheets include figures utilising the Brinell and Rockwell hardness tests, please see below for a selection metals we offer at Protolabs for CNC machining and their hardness values. For other materials, please check the numbers provided on our material datasheets. Alternatively, you can speak with one of our application engineers by phone +(0) 1952 683047 or email customerservice@protolabs.co.uk
Type | Material | Hardness HB Brinell Hardness kg/mm2 | HRB Rockwell B MPa | HRC Rockwell C MPa |
---|---|---|---|---|
Aluminium | Aluminium 2024 T351 | 3.1355 AlCu4Mg1 | 120 | [~65] | - |
Aluminium | Aluminium 5083 H111 | 3.3547 | AlMg4.5Mn0.7 | 75 | [~37] | - |
Aluminium | Aluminium 6082 T651 | 3.2315 | AlSi1MgMn | 90 | [~52] | - |
Aluminium | Aluminium 7075 T651 | 3.4365 | AlZn5.5MgCu | 150 | [~80] | - |
Aluminium | Aluminium 7075 T7351 | 3.4365 | AlZn5.5MgCu | 140 | [~75] | - |
Brass | Brass (bar) Cz121 | C360 | 2.0401 CuZn36Pb3 | 90 to 160 | - | - |
Brass | Brass (billet) Cz112 | C464 | 2.0321 | CuZn36Sn1 | 80 to 135 | - | - |
Carbon Steel |
Carbon Steel | EN8 | 1.0503 | Fe As machined Heat Treated |
150 to 200 (as machined) 200 to 255 (hardened) |
[~80 to 93] [~93 to 100] |
[~1 to 16] [~16 to 27] |
Copper | Copper C101 | <65 to 105 | - | - |
Mild Steel | Mild Steel S275JR | 1.0044 | Fe | [~135] | 75 | - |
Stainless Steel |
Stainless Steel 17-4PH | 1.4542 | X5CrNiCuNb16-4 As machined Heat treated |
<365 (solution annealed) 400 to 500 (heat treatment H900) |
[~100] [~114 to 117] |
[~40] [~43-47] |
Stainless Steel | Stainless Steel 304L | 1.4304 | X5CrNi18-10 | [~150] | 82 | [~15] |
Stainless Steel | Stainless Steel 316 L | 1.4404 | X2CrNiMo17-12-2 | [~150] | 81 | [~15] |
Titanium | Titanium Grade 5 | 3.7164 | Ti6Al4V | [~320] | 109 | [~36] |
What should I consider when selecting a material with hardness in mind?
What are the advantages of hard materials?
Hard materials resist deformation, indentation or scratches making them harder wearing, longer lasting and often easier to clean and maintain.
What are the disadvantages of hard materials?
Hardness and toughness are normally inversely proportional to each other e.g. glass is hard, but it’s low toughness makes it very fragile. Plastics are often tough, but not as resistant to surface and impact damage as metals.
What options are there for making my low-hardness metal harder?
Plating, coating or surface heat treatment often aim to provide the hard and/or hard-wearing surfaces required, whilst maintaining the materials’ inherent toughness.
Hard anodising is available at Protolabs, our digital network, also offer heat treatment and painting, learn more here.
What heat treatments can be used to harden CNC metal materials?
There are many methods of heat treating a part to potentially make it harder. These include quenching, precipitation hardening (ageing), case hardening and carburising, which are offered through our digital network.
What is case hardening?
Also known as surface hardening. This heat treatment is used to improve the hardness and wear resistance of the metal’s surface, whilst retaining the toughness of its inner core. This method is particularly useful for components that need to withstand abrasive wear, impact, and other forms of mechanical stress. The metal’s surface layer composition is altered through diffusion.
What are the different types of case hardening?
There are several different methods of case hardening, they include, carburising, nitriding, carbonitriding, induction hardening and flame hardening. Out digital network offers carburising.
Carburising – the most common of the methods. The metal part is heated in an environment that is rich in carbon, which causes the carbon atoms to diffuse into the surface layer. The result is a surface layer high in carbon, which can be hardened through subsequent quenching (rapid cooling).
Heat Treatment | Purpose | Compatible Materials |
---|---|---|
Case Hardening & Carburising | To increase the surface hardness of the metal part, while keeping the core soft. | Mild Steels (1018, A36) |
Nitriding – Like carburising the metal part is heated in an environment, but this time rich in not just carbon, but also nitrogen. Nitrogen atoms diffuse into the surface, forming nitrides, which increases the hardness and wear resistance. Particularly effective for use on stainless steel and other alloyed steels.
Carbonitriding – A combination of carburising and nitriding. The part is exposed to an atmosphere containing both carbon and nitrogen. This creates a surface layer rich in both carbon and nitrogen compounds.
Induction Hardening – the surface layer of the metal part is heated using high-frequency induction heating, and then the part is quenched. The localised heating and quenching result in a hardened surface, whilst retaining core properties.
Flame Hardening – a high-temperature flame is directed onto the surface of the metal part, followed by quenching. Similar to induction hardening this method only hardens the surface layer.

What is Quenching?
Quenching is a process used to rapidly cool a heated metal or alloy to enhance its mechanical characteristics. During the process the metal or alloy is heated to a high temperature to allow for changes in its atomic structure. It is then quickly cooled down, often by immersing the part into water, oil or exposing it to cool air/steam. This “quenching” locks in the changes to the structure that occurred during the heating process. The result, parts with very high hardness. To control the resulting hardness a tempering process may be used. Tempering prolongs the service life of the part, reducing brittleness.
Heat Treatment | Purpose | Compatible Materials |
---|---|---|
Quenching | To increase the hardness of the steel alloy. | Mild steels (1045, A36) Alloy steels (4140, 4240) Tool steels (D2, A2, O1) |
What is Precipitation Hardening?
Precipitation hardening is also known as age hardening and is used to strengthen certain types of alloys, in particular those based on aluminium, magnesium, and some steels. The treatment itself is a three-step process, a combination of solution treatment (solutionising) and ageing. During the first step the alloy is heated to a high temperature (also known as the solution treatment stage) it is generally heated to just below its melting point. This high heat allows metal atoms and alloying elements to dissolve into a solid solution. This treatment basically homogenises the alloy’s composition. Reducing any segregation of elements.
The second step is quenching (rapidly cooling) to hold the alloy’s new microstructure.
Before finally being heated at a lower temperature for a long-time (ageing). During the ageing process the alloying elements begin to separate from the solid solution. They form microscopic precipitates (particles) within the material structure. These precipitates hinder the movement of structural defects (dislocations) within the crystal lattice of the material. Consequently, impeding plastic deformation and improving strength and hardness.
There are two stages within the ageing process, nucleation and growth. At the beginning, during nucleation, small clusters of precipitate atoms begin to form with the alloy’s matrix (nucleation). Nucleation sites can include crystal defects, grain boundaries, and other imperfections.
During the “growth” stage and once nucleation has occurred, the precipitates grown in size and number. Then continue to hinder the movement of dislocations, effectively strengthening the material.
Heat Treatment | Purpose | Compatible Materials |
---|---|---|
Precipitation Hardening (Aging) | To increase the hardness & strength of the metal alloy. | Aluminium alloys 6061 T6, 6068 T6, 7075 T6, Stainless Steel (17-4) |
Here is an example of how precipitation hardening would affect Aluminium 7075
Aluminium 7075-0 (tempered) | Aluminium 7075-T6 (precipitation hardened) | |
---|---|---|
Ultimate Tensile Strength | 280 MPa | 510-540 MPa |
_Yield Strength_ | 140 MPa | 430-480 MPa |
_Elongation at Break_ | 9-10% | 5-11% |
Hardness (HV) | 68 | 175 |
What is anodising?
A thin, protective coating is applied to the aluminium part, forming a protective oxide layer. This layer creates a barrier against corrosion. There is the choice of decorative anodising and hard anodising. Hard anodising is the most durable anodising finish available on machined aluminium parts.
So now that we know about what hardness means for your part and how you can obtain hardness whilst simultaneously retaining a part’s toughness, let’s talk about testing a part’s hardness. How you test a part’s hardness and the methods that are available.
Hard anodised parts are tested for hardness using the Vickers test. On average, hard anodised aluminium 6082 can achieve values in the range of 300 to 500 HV, to put that into perspective, in its untreated state it has a hardness range of 80-95 HV. Exact hardness is entirely dependent on process parameters, such as anodising time, temperature, voltage and electrolyte composition. It’s also important to note that hardness may not be uniform across the entire material.
How do you test your part’s hardness?
Brinell Hardness Test
The Brinell hardness test is named after its inventor, Johan August Brinell. It involves applying a constant load or force to a spherical indenter made of hardened steel or carbide onto the surface of the material being tested. The indentation diameter is then measured optically. The Brinell hardness number (BHN) is calculated as the load applied divided by the surface area of the indentation.
The Brinell test is typically used for materials with a coarse or granular microstructure, such as cast iron, aluminium, and soft metals. It provides a reliable measurement of hardness but may not be suitable for very hard or thin materials due to the large indentation size.
Where:
- HB is the Brinell hardness number.
- P is the applied force in kilograms-force (kgf).
- D is the diameter of the indenter ball in millimetres (mm).
- d is the diameter of the indentation left in the material's surface after the test, in millimetres (mm).
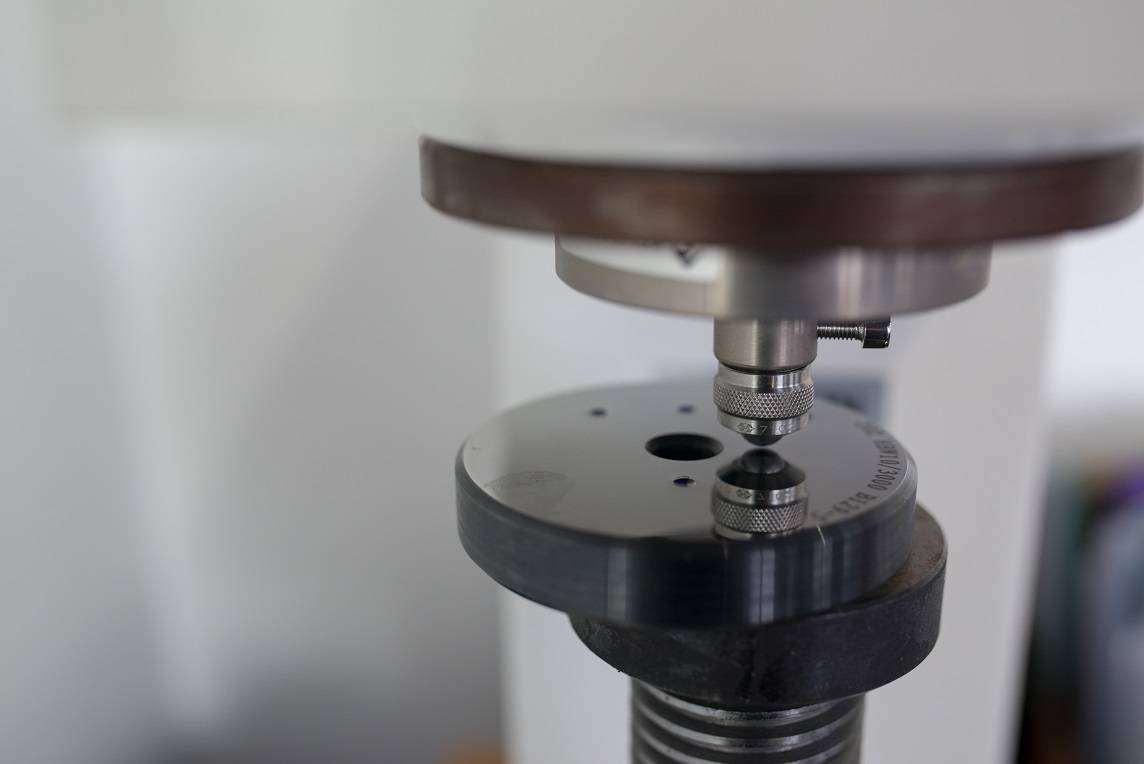
The Brinell hardness number is typically reported in units of kgf/mm² or N/mm² (Newton per square millimeter).
The difference between HBS and HBW is the indenter.
For HBS a hardened steel ball was/is used to determine the value. This is used for materials with a value below 450 such as mild steel and grey cast iron, however, the HBS method isn’t really used any longer, although it is sometimes still referred to.
HBW indicates a cemented carbide ball is used. This is used for materials with a value below 650.
As HBW is the only method still used it is often expressed as simply HB on datasheets.

Rockwell Hardness Test
The Rockwell hardness test is based on the indentation depth caused by a diamond or a ball indenter under different loads. There are two main scales used in the Rockwell test: the Rockwell HRC scale (uses a diamond cone indenter) for harder materials and the Rockwell HRB scale (uses a ball indenter) for softer materials.
The equations for calculating Rockwell B (HRB) and Rockwell C (HRC) hardness values are as follows:
- Rockwell B (HRB) Hardness: = 130 – (P/A)
- Rockwell C (HRC) Hardness: = N – d
Where:
- HRB is the Rockwell B hardness value.
- P is the depth of the indenter penetration under minor load
- A is a constant factor specific to the scale
- HRC is the Rockwell C hardness value.
- N is the depth of the indenter penetration under major load
- d is the depth the indenter has penetrated into the material's surface, which is determined by the Rockwell hardness testing machine.
It's important to note that the Rockwell hardness scales are dimensionless numbers and are used to represent the hardness of a material based on the depth the indenter penetrates the material. The higher the Rockwell hardness number, the harder the material. Additionally, different Rockwell scales are used for different types of materials, so it's essential to specify the scale being used when reporting Rockwell hardness values.
Hardness Symbol | Indenter Type | Total Test Force F/N (kgf) | Hardness Range | Application Examples |
---|---|---|---|---|
HRA | 120° Diamond Cone | 588.4 (6) | 40-100+ |
Thin steel, case-hardened steel, shallow case-hardened steel, cemented carbide, other materials with relatively low hardness |
HRB | Ø1.588mm Hardened Steel Ball | 980.7 (100) | 20-100 |
Soft metals, non-ferrous metals, annealed steel, aluminium alloys, brass, and other soft hardness materials. |
HRC | 120° Diamond Cone | 1471 (150) | 20-70+ |
Hardened steels, carbon steels, alloy steels, cast iron and other materials with high hardness. |
HRD | 120° Diamond Cone | 980.7 (100) | 70-100+ |
Hardened and tempered steel and other materials with high hardness. |
The Rockwell hardness test has multiple scales, each designated by a specific letter. The most common scales are Rockwell A (HRA), Rockwell B (HRB), Rockwell C (HRC), and Rockwell D (HRD). Each scale uses a different combination of the indenter and the applied load.
Vickers Hardness Test
The Vickers hardness test utilises a diamond pyramid-shaped indenter to create a small impression on the material's surface. Taking into consideration the weight of the load, the size of the indentation is measured using a microscope. The Vickers hardness number (HV) is calculated based on the indentation diagonal lengths.
This method is suitable for a wide range of materials, including metals, ceramics, and plastics. Due to its small indentation size the Vickers hardness test allows for testing on very thin materials and provides accurate results.
Where:
- HV is the Vickers hardness number.
- P is the applied force in kilograms-force (kgf).
- d is the average diagonal length of the indentation that is left on the material's surface after the test (in millimeters (mm).

The Vickers hardness is typically reported in units of kgf/mm² or N/mm² (Newton per square millimetre).

Leeb Hardness Test
The Leeb hardness test is a non-destructive and portable method used primarily for metals. It involves a spring-loaded end with a spherical or conical indenter. The end that makes contact with the material is released, and the rebound velocity is measured after striking the material's surface. The Leeb hardness value is then determined based on the ratio of the rebound velocity to the impact velocity.
This method is commonly used for on-site testing and is useful for large and heavy components. It is less accurate than the Brinell, Rockwell, or Vickers tests but offers the advantage of quick measurements without the need for sample preparation.
The Leeb hardness value is calculated using the following equation:
where:
- HL is the Leeb hardness value.
- v is the rebound velocity of the end that makes impact with the material after striking the surface.
- V0 is the calibrated rebound velocity of the end that makes impact with the material on a reference test block of known hardness.
The Leeb hardness value is a dimensionless number, and it is usually converted to different scales to represent the hardness of the material in specific units, such as HRC (Rockwell C hardness) or HB (Brinell hardness).
The Leeb hardness test is commonly used for on-site hardness measurements, especially in large and heavy components, where other conventional hardness tests might be impractical or not feasible. However, it's important to note that the Leeb hardness test might not be as accurate as other laboratory-based hardness tests (e.g., Brinell, Rockwell, or Vickers) and might be affected by factors such as surface roughness and material homogeneity. Calibration and standardisation are critical to obtaining reliable and accurate hardness values using the Leeb hardness test method.