Manufacturing Robotics Report
An engineer's guide to understanding the state of the art in hardware, materials, and the future of robotics manufacturing.
This short report aims to provide a survey of the most recent developments and status of core robotics technologies. It acts as a guide for engineers to understand the state of the art in the future of robotics with an emphasis on manufacturing.
To understand which areas of robotics and robotics manufacturing to concentrate on, we asked key players in the robotics industry to respond to a short survey. Wevolver's robotics community responded enthusiastically, and we gained valuable insights into what the robotics industry themselves see as the most pressing issues and trends. This feedback helped steer the direction of the report, including a larger focus on soft robotics and additive manufacturing, as well as an extended fifth chapter that gives a snapshot of the most exciting robotics projects and their applications.
Survey quick stats
47%
of respondents want to know more about robotics applications.
32%
suggested soft robotics or new materials will have the biggest impact on robotics in the next five years.
27%
indicated the material supply chain is the most serious barrier to innovation.
Introduction

The discussion and focus of the field of robotics have often been closely tied to its manufacturing application origins. However, over the past decade, robotics has exploded to include devices that augment surgery, assist with elderly care, lead search and rescue missions and monitor waterways. The importance of robotics is not lost on the engineering community — robotics-related content is continually the most read on the Wevolver platform. With that focus in mind, this report’s purpose is to enable you to be up to date and understand the complexity and depth of robotics, and to help you gain specific insights into the current status of robotics manufacturing.
Over the next five chapters, we will examine the core technologies that make up a robotics project, and we will shed light on the trends and challenges in getting them created.
One of the most exciting areas of technology advancement is in materials. As the survey linked to this report found, many consider soft robotics an area with great potential. One early example of soft robotics are soft grippers, they are more flexible and can grip a wider variety of items. This makes robots able to perform even more logistical tasks. They are also able to handle delicate and perishable items. This opens up interesting opportunities in agriculture, where the interest in automation is growing fast.
Soft robotics presents new problems that need to be addressed.
Materials and design need to be carefully evaluated. When developing grippers for a particular application it’s important to consider that these materials are different from other commonly used materials. This makes it especially important to know the manufacturing process used, and to be aware of their opportunities and challenges. It’s also important to approach this in an iterative way as this explores new context where robotics have not been used before. Here the ability to make small numbers of parts in many different soft materials is key. This makes iterations faster and shortens the development time. As this is new and materials are sometimes challenging, special care has to be taken when working with suppliers.
Developing and manufacturing robots for these emerging markets presents new challenges and requires creative thinking. As with the soft robots mentioned previously, an iterative approach with a close eye on manufacturability is necessary here. A key factor for consideration is that the users will be much more diverse as will the situations the robots will be used in. The low-cost factor drives the need for more focus on keeping up with the latest manufacturing methods and to design with them in mind. Here, good support from suppliers and partners are essential as they know their methods best.
In other parts of robotics, we also see tremendous growth in advanced systems. Images, video and other data streams that can be considered complex can now be processed reliably.
New legged platforms can bring the technology out in complex production settings that are not constructed with robotics in mind. IoT devices can monitor systems in new ways, and because they are small and cheap, they can be used in large numbers.

More advanced robotics systems also allow for more remote working in roles that traditionally have been onsite. This reduces staff cost and provides existing staff with a better work environment. Improvements in resource utilisation is also an opportunity as problems can be addressed by accessing the robot remotely, reducing response time and increasing up time. It can also enable cooperation between humans and robots. The robot can do the 80% that is relatively easy to automate. When necessary, it calls on the human to do the remaining 20% that is hard or impossible to automate, or to fix any problems.
The introduction of ecosystems of products that work together around common standards will be incredibly significant in the long term, as it was when the same thing was introduced to computer peripherals. Nowadays everyone expects that whatever they buy and plug in to their computer will just work. Plug and play has indeed fulfilled its destiny. The same thing is about to happen in robotics, automation, and IoT. The trend is moving towards a time when a task can be automated with a solution that "just plugs into" your operation. Even if this is achievable, automating complex production will always be much more complicated.
Product ecosystems will be quite practical in many production and logistics settings. This growing ecosystem of software and hardware that all work together is also a key factor in bringing new technologies to
market much quicker.
They make it surprisingly easy to assemble solutions. These trends together make robotics available, practical, and affordable.
On the financial side of things, we are not only seeing prices coming down, but also much more flexible ways of paying. With today's more intelligent systems, you can pay per task that the robot performs for you. This and other new robotics as a service (RaaS) implementations drastically lower the barriers to entry. This makes it possible to try robotics in more contexts and see where a good fit can be found.
To sum up, this report will give you key knowledge about the current state of robotics, covering opportunities in new materials, and innovative ways of designing and manufacturing robots. Trends that are expected to be significant are also discussed in this report. Examples of the wide variety of new systems that are currently being developed are also included.
Materials
New frontiers in robotics materials
The field of robotics has been progressing remarkably fast in recent years, challenging conventional ideas of robot architecture and function. In an article published in 2018 by the journal Science Robotics, an expert panel of scientists identified a set of challenges for the future of robot design and manufacturing. It is significant that, among these challenges, the first is the development of new manufacturing materials for robotics.[1]
Additional challenges that are connected to materials science include the design of bio-hybrid and bioinspired robots, taking inspiration from living organisms to create multifunctional and autonomous systems. In addition, the adaptability of robots to extreme and complex environments is related to the mechanical and self-healing properties of innovative robotics materials.
To understand the rapidly advancing field of robotics materials, it is necessary to introduce a distinction between traditional robotics and soft robotics.
Traditional robotics relies on mechatronic systems for the design of robots. These robots are typically powered by electromechanical motors and are assembled from independent components and materials, each performing a separate function (actuation, sensing, structural). Traditional robotics is based on rigid materials, such as steel, aluminium, hard plastic, alloys, and composite materials.
On the other hand, soft robotics aims to integrate different functions into one single material, including actuation, sensing, adaptivity, and locomotion. In this context, soft robots take advantage of smart and multi-functional materials, such as elastomers, gels, fabrics, and biological materials, which allow the body of the robot to comply with the surrounding environment.[3]

Traditional robotics materials
Today, steel, aluminium, cast iron, and hard plastic are among the most frequently used materials for industrial robots. By creating materials that make these robots stronger, lighter, stiffer, and more precise, material science has considerably supported their success in the industry. Robots, however, have rarely been employed outside of factories, since doing so calls for a level of agility and adaptability that standard robots made of hard materials struggle to provide.
Among the emerging materials for traditional robotics, carbon fibre-reinforced composites can greatly improve energy consumption,
performance, and the safety of robots. Since carbon fibre-based composites are much lighter and more durable than metal, these materials are promising for the future of robotics. However, their manufacturing cost is still high and mass production remains challenging.[4]
Shape-memory alloys (SMAs), such as the nickel-tin alloy Nitinol, can be programmed to recover a specific shape when heated. Although their applications are still limited, SMAs may gradually replace heavy hydraulic actuators in robots while increasing durability. Nitinol components are already being used in robotics for space applications. The tyres on the NASA Mars Curiosity rover were entirely composed of shape-memory Nitinol.
A new generation of robotics materials
Compared to traditional robotics, soft robotics is based on a new generation of deformable, flexible, and smart materials. One of the main classes of soft robotics materials is elastomeric materials, such as natural and synthetic ubbers, silicones, like polydimethylsiloxane (PDMS), and soft composites.
Elastomers are mechanically compliant and have high elastic modulus so that they can recover their shape even after very significant deformations.[5]
The first fully autonomous soft robot was designed in 2016 and featured an elastomer-based body.[7]

This robot, called “Octobot” from its octopus-inspired shape, is controlled by microfluidic logic and actuated by a gas-producing chemical reaction. It is actuated by an Embedded Pneumatic Network (EPN) that exploits the ability of elastomers to expand without breaking when gas is released.
The main advantage of using elastomers compared to rigid materials for robotics is the possibility of movement in limited space and the ability to distribute impact loads more effectively across the entire robot body.
Another class of evolving robotics materials is smart materials. These materials are intrinsically multifunctional, combining sensing, actuation, and structural purposes in a single component. Smart materials can change their shape in response to several stimuli including electric fields, temperature, light, and pH.[3]
Among smart materials, electromechanically active polymers (EAPs), also known as artificial muscles, are deformed in response to applied voltages. In soft robotics, they are used to produce actuators by sandwiching the polymer between two compliant electrodes.[8] Shape-memory polymers, on the other hand, are programmed to recover a specific shape upon heating. These have interesting applications in the aerospace and biomedical fields.[3]
Fabricating soft-bodied robots
Compared to traditional robots, the large-scale fabrication of soft robots is still in its infancy. In recent years, however, new manufacturing possibilities have emerged. Since soft robots are mostly polymer-based, there are two main approaches to their manufacture, namely, cast-moulding, and additive manufacturing.
Cast moulding is commonly used for soft robots that do not require elaborate structures. In the case of silicone rubbers and other catalysed polymers, crosslinking takes place from the mixing of two components; therefore, degassing the polymer mixture before hardening is crucial to prevent defects in the final component. If traditional moulding is not sufficient, approaches such as dip-coating and rotational moulding are effective to shape complex internal volumes.[9]
Additive manufacturing (AM), also known as 3D printing, is the easiest way to shape highly elaborate components. It is based on the deposition of small volumes of materials to create the desired shape. Although it was originally designed only for hard, thermoplastic polymers, in recent years AM has been extended to soft materials such as elastomers and hydrogels, becoming one of the most promising manufacturing approaches for soft robots. In this context, AM techniques have been applied to smart materials, with an approach known as 4D printing.[10] When exposed to specific environmental conditions, 4D-printed components morph into a pre-programmed shape.
Read more about the impact of AM in the manufacturing chapter.
Sustainability of robotics materials
Electronic waste, or e-waste, management is one of the most pressing issues of the 21st century.
It is estimated that more than 100,000 tons of electronic devices are discarded each day, with only a very small percentage of this waste being recycled. Due to their complex compositions, consumer electronics – which often include rare and toxic materials - are typically landfilled.[6]
Because of this, innovative robotics materials need to take the circularity mindset into account, promoting new and more sustainable technologies. Compared to traditional robotics, soft robotics is an opportunity for the industry to greatly reduce its environmental impact. Because they often rely on multifunctional materials, soft robots have less complex architectures, with the same material often serving multiple purposes
(e.g., actuation and structural). Because of this, they are intrinsically easier to recycle.
In addition, biocompatible and biodegradable materials can be used for soft robotics applications. These materials include both natural polymers, such as collagen, cellulose, and chitosan, and synthetic polymers, such as polycaprolactone (PCL) and polylactic acid (PLA).[11]
Finally, self-healing materials can be used in soft robotics to significantly extend the lifetime of robots. Self-healing materials incorporate the ability to autonomously repair damage.[12]
Designing For the Future: Understanding Life Cycle Analysis
Life cycle analysis (LCA) is a tool used to evaluate the environmental impact of a product or service throughout its entire life cycle, from raw material extraction to disposal. LCA is essential for designers to understand the impact of their robotics products, provide transparency to potential customers and endeavour to lower environmental impact. Some of the challenges associated with LCA include:
Data availability:
LCA requires a large amount of data, including information on the materials and energy used in production, transportation, use, and disposal. This data can be difficult to obtain, particularly for small or niche products such as robotics.
Complexity:
LCA can be a complex process, involving many different stages and multiple impacts. This can make it difficult to compare the environmental impact of different products or services. Particularly when working with completely new products and markets.
Uncertainty:
There is often a degree of uncertainty in the data used in LCA, which can make it difficult to make definitive conclusions about the environmental impact of a product or service. As robotics is an emerging industry, reliable long term data is harder to acquire.
Relevance:
LCA is often used to evaluate the environmental impact of a product or service within a specific context, such as a particular geographic region. This can make it difficult to generalise the results to other regions or contexts.
To overcome these challenges, Protolabs worked with leading designers and engineers at Design Council's Design for Planet festival to develop five tips for including LCA in your next product development.

1. Make sure that you include the planet in the scope of the design brief
To be effective you need to ensure that you think about the effects of the product on the planet and its people within the brief. Think about what is important and how you will measure these impacts.
2. Consider materials carefully and optimise material use, for product and packaging
For production, you need to consider how to optimise rather than maximise material use. Leveraging design methodologies such as generative design can lead to lean products that are also stronger, lighter and more aesthetic.
3. Analyse where there are highest levels of waste and energy
The more you understand your own processes and what to measure the better you will be able to pinpoint high levels of waste – whether of raw materials or energy – and then take action to eliminate, reduce or recycle and reuse. Look for manufacturing partners that also have transparent energy and material information at hand.
4. Design for end of life and disassembly
Abide by Design for Planet principles of circularity and regeneration. The disposal of old products will have an impact on the environment, so the challenge is to minimise this by designing it for end of life and disassembly rather than consigning it to landfill. Also consider how the product may be reused beyond its original life, so consider modularity of replacement parts, reuse and upcycling. And even better, can what you’re designing actually regenerate natural resources?
5. Share what works and what doesn’t so we can learn collectively
We can all learn from our experience so we need an open-source model that demonstrates what works well, supports how things can be done correctly, and helps us to learn from mistakes. Designers need to experiment, try different things and learn from their collective experience. Consider how you will share your experiences with other designers so that we can all move towards more sustainable products.

Applications for soft robotics
The expected Compound Annual Growth Rate (CAGR) for the soft robotics industry between 2022 and 2027 amounts to 35.1%, with North America as the largest market.
This testifies to the growing interest in soft robotics solutions in various fields, with medical and surgical applications predicted to register the highest growth. [13]
In the biomedical field, soft robotics offer unprecedented opportunities to design smart prosthetic limbs at a fraction of the cost required for traditional devices. For example, a soft robotic elastomeric hand (see image to the right) actuated via a pneumatic system, was recently designed to provide real-time tactile feedback to patients.[14]
Soft robotics may also enable growth in Minimally Invasive Surgery (MIS), providing quicker and safer surgical procedures without damaging surrounding tissues.
Another promising field for soft robotics is the production of soft grippers for handling fragile objects.
With more and more industries, including the food industry, progressing towards automation, a new generation of versatile robotic grippers is being developed. Due to their light weight, dexterity, and robustness, soft-bodied robots are also a promising technology for space applications.[15]
Overall, the intersection between robotics and materials science offers great opportunities for diverse fields of technology. Thanks to the development of smarter materials and advanced manufacturing techniques, a new generation of soft-bodied,
bio-inspired, and sustainable robots are on the rise.
-
Yang G-Z, Bellingham J, Dupont PE, Fischer P, Floridi L, Full R, et al. The grand challenges of Science Robotics [Internet]. Vol. 3, Sci. Robot. 2018. Available from: http://robotics.sciencemag.org/
-
Fu C, Xia Z, Hurren C, Nilghaz A, Wang X. Textiles in soft robots: Current progress and future trends. Vol. 196, Biosensors and Bioelectronics. Elsevier Ltd; 2022.
-
Mazzolai B, Mondini A, Del Dottore E, Margheri L, Carpi F, Suzumori K, et al. Roadmap on soft robotics: multifunctionality, adaptability and growth without borders. Multifunct Mater. 2022 Sep 1;5(3).
-
Lan X, Zhao X. Application of carbon fiber composite materials in the field of industrial robots. In: ACM International Conference Proceeding Series. Association for Computing Machinery; 2019. p. 310–5.
-
Gariya N, Kumar P. A review on soft materials utilized for the manufacturing of soft robots. In: Materials Today: Proceedings. Elsevier Ltd; 2021. p. 11177–81.
-
Hartmann F, Baumgartner M, Kaltenbrunner M. Becoming Sustainable, The New Frontier in Soft Robotics. Vol. 33, Advanced Materials. John Wiley and Sons Inc; 2021.
-
Wehner M, Truby RL, Fitzgerald DJ, Mosadegh B, Whitesides GM, Lewis JA, et al. An integrated design and fabrication strategy for entirely soft, autonomous robots. Nature. 2016;536(7617):451–5.
-
Bar-Cohen Y, Anderson IA. Electroactive polymer (EAP) actuators—background review. Mech Soft Mater. 2019 Dec;1(1).
-
Schmitt F, Piccin O, Barbé L, Bayle B. Soft robots manufacturing: A review. Vol. 5, Frontiers Robotics AI. Frontiers Media S.A.; 2018.
-
Sydney Gladman A, Matsumoto EA, Nuzzo RG, Mahadevan L, Lewis JA. Biomimetic 4D printing. Nat Mater. 2016;15(4):413–8.
-
Rossiter J, Winfield J, Ieropoulos I. Here today, gone tomorrow: biodegradable soft robots. In: Electroactive Polymer Actuators and Devices (EAPAD) 2016. SPIE; 2016. p. 97981S.
-
Terryn S, Langenbach J, Roels E, Brancart J, Bakkali-Hassani C, Poutrel QA, et al. A review on self-healing polymers for soft robotics. Vol. 47, Materials Today. Elsevier B.V.; 2021. p. 187–205.
-
Soft Robotics Market - Growth, Trends, Covid-19 Impact, and Forecasts (2022-2027) [Internet]. Available from: https://www.mordorintelligence. com/industry-reports/soft-robotics -market
-
Gu G, Zhang N, Xu H, Lin S, Yu Y, Chai G, et al. A soft neuroprosthetic hand providing simultaneous myoelectric control and tactile feedback. Nat Biomed Eng [Internet]. 2021; Available from: http://dx.doi.org/1 0.1038/s41551-021-00767-0
-
Zhang Y, Li P, Quan J, Li L, Zhang G, Zhou D. Progress, Challenges, and Prospects of Soft Robotics for Space Applications. Adv Intell Syst. 2022 June 30; 2200071.
Hardware
Robots extend human capabilities with more precision, less fatigue, and a higher tolerance for hazardous conditions.
Robotics today are expanding from the limited movements of the factory to uncontrolled environments shared closely with humans. This progress is made possible with advances in robotics hardware, which includes the motors, joints, and sensors used to create and control the movement required to solve a given task.
This move also demands an increase in computation to solve the accompanying perceptual, planning, and control tasks ‘robots in the wild’ require. Advances in software, particularly artificial intelligence (AI) and machine learning, go some way to deliver the smart robots of the future, but computing platforms will also take a significant role in the future of solving complex perceptual and control tasks.
In the first half of this chapter, we give an overview of the core hardware requirements for most robotics projects. In the second half we look at the rise of embedded systems that enable cutting-edge robotics.

Robotics hardware overview

Sensors
Sensors are the method by which the robot receives input from the world around it, similar to the human senses of sight, hearing, balance, touch, and smell.
Common types of robot sensors are:
- Cameras for a visual of the environment
- Microphones to pick up sound Force sensors to detect weight and resistance
- Proximity sensors that pick out objects in an environment Gyroscopes that identify robot orientation
- Environmental sensors to measure humidity, temperature, gases, pollutants, and other factors
Sensors are passive, meaning that they do not give the robot any type of direction.
Instead, the information from the robot’s sensors is typically sent to a central processing unit (CPU), where the input is transformed into action.
One of the biggest trends in robotics sensors is the increasing use of ultrasonic sensors. An ultrasonic sensor measures the distance of a target object by emitting ultrasonic sound waves, and converts the reflected sound into an electrical signal.
Ultrasonic sensors have two main components: the transmitter (which emits the sound using piezoelectric crystals) and the receiver (which encounters the sound after it has travelled to and from the target).

Central processing unit
The CPU is the hardware and software interface between the robot sensors and the control system. The CPU parses commands for the robot to execute and routes them to specific components of the robot. In automated robots, it processes the information received from the input sensors, interprets the information, performs calculations, and may apply machine learning algorithms. In that sense, the CPU functions as the major component of the robot’s brain.
The CPU provides additional processing for error handling. When the robot fails to execute a command, or when something unexpected occurs in the robot’s environment, the CPU determines how the robot handles the situation.
Some examples of error-handling are:
- Retrying the command
- Requesting manual control from the robot operator
- Recording the error as a data point for machine learning
- Disabling the robot
For a semi-autonomous robot or a manual robot, the sensor input may be relayed to an external human operator. The operator’s commands are sent back through the CPU and to the robot.
In some robots, a lighter weight single board computer (SBC) might be installed as middleware to process input and send commands. An SBC gathers sensor input and may relay it to an external CPU for further processing. The CPU then sends commands back to the robot, which are parsed by the SBC and sent to specific parts of the robot.
With the advent of artificial intelligence and edge computing, newer SBCs have AI-friendly designs to boost efficiency and drive greater applications. Edge computing allows data processing and analytics to take place at the network’s edge, providing rapid real-time insights and allowing SBCs to be used in IoT-based systems with greater ease and adaptability. One of the most significant benefits SBCs offer is flexibility in platform configuration. The system can be designed with minimum requirements and can then be scaled according to the application. Purpose-built PC systems do not provide such agility.

Control system
The robot control system sends the commands that govern the robot’s actions, similar to the human nervous system, which sends the signals that direct the human body to move. The robot control system depends on the robot’s level of autonomy.
- With fully autonomous robots, the control system may be a closed feedback loop in which the robot is programmed to perform a specific task. The CPU uses input from the sensors to inform the action to take and may detect whether the action was performed correctly.
- With manual robots, the control system is manipulated by the human operator using an external console. The CPU routes commands from the operator to the robot.
- With semi-autonomous robots, the control system is a hybrid of both types of control systems. The level of autonomy determines whether the human operator makes all high-level decisions using the control system or whether the robot requests human input as needed.
Hardware for the robot control system can take many forms, depending on the environment, tasks to perform, and manufacturing capabilities.
For example:
- A manual or semi-autonomous robot may be controlled using various types of hardware, such as a personal computer, a purpose-built hand controller, headset, foot pedals, a microphone for voice commands, or even a textile-based controller, such as a VR-like bodysuit.
- An autonomous robot may be controlled entirely by the onboard CPU, or it may be controlled by software on an external server.

Motors and actuators
Motors and actuators are the mechanisms for robot mobility, similar to the human muscular and cardiovascular systems, which provide the means for human movement. Without motors and actuators, the robot cannot perform tasks in the physical world.
Advances in motor technology enables smaller casings, which are often injection moulded, so that motors are more agile and have an increased range of applications. Recent advances in motor design include newer permanent magnets that distribute more power with smaller motors. Higher-resolution encoders improve accuracy, and motor tuning can also be improved to help with accuracy and cycle time. This creates opportunity for higher-precision robotics applications, and it improves repeatability and the throughput of the robot and automation. Smaller motors with better torque-to-weight ratios achieve higher peak speeds for a short time, as well as faster acceleration and deceleration times. Smaller motors also reduce robot mass, which in turn permits more rigidity and reduces vibration.
Motors and actuators are similar to each other, but serve distinct purposes.
- A motor has rotational movement and is usually intended for continuous power. For example, a motor may drive a robot across terrain, operate an internal fan, or rotate a drill.
- An actuator has linear movement and is usually intended for more precise operation. For example, an actuator may be used to provide the flexible bending motion of a robotic elbow, or to rotate a robot torso. Most actuators are electrical, hydraulic, or pneumatic.
Degrees of freedom (DOF) is an important concept in robotic movement that refers to the axes that a mechanical joint can move along. The DOF of a robotic joint is limited by hardware, including the actuators that power the movement.

End effectors
End effectors (sometimes called end-of-arm tools or EOAT) are mechanical assemblies positioned at the end of a robot arm that allow the robot to manipulate objects in the physical environment.
End effectors essentially act as the robot’s hands, although their function varies from that of human hands.
- Tool-specific end effectors can be highly specialised for robots that perform specific tasks. There are limitless possibilities for these end effectors, from power tools like a drill or electric sander, a water pressure washer, a powered vacuum suction cup, or tools for scientific research.
- Gripper-type end effectors may be used to grasp and hold objects, and are more generalised than tool attachments. Grippers may take on a variety of forms, such as clamps controlled by actuators, electromagnetic systems, or static features, like hooks or specially-designed fasteners.
Some robots have a combination of gripper and tool-specific end effectors. For example, a robot built to weld pipes may have a welding torch at one arm and a gripper to hold the pipe in place at another.
With interchangeable end effector attachment systems, the operator can choose the best tool for a task, whether it is a specialised power tool, or a more generalised gripper-type attachment. Some grippers can hold and operate tools, though they may offer less precise control for a human operator than tool-specific end effectors.
The field of soft robotics extends the versatility of end effectors by replacing rigid components with softer and more flexible end effectors. Soft robotics mimics biological qualities, which may improve a robot’s ability to manipulate fragile or pliable objects. Minimising rigid surfaces on the robot may also reduce safety hazards for robot operators.

Connectors
Connectors are used in robotics to relay commands and power throughout the robot. Motors, actuators, sensors, and end effectors require both data bus and electrical circuits to operate.
Types of connectors used in robotics include:
- Robust connectors for data and power, such as circular connectors, push-pull connectors, and micro-D connectors. These are connected and disconnected by hand, while preventing accidental disconnection. Circular connectors can be very compact, making them effective for smaller moving parts at end effectors and robotic joints.
- Data networking connectors. These connectors are specific to data signals and can provide a faster connection than multi-purpose connectors. RJ45 connectors are ethernet connectors that are commercially available in a variety of flexible shells that suit industrial robotics.
- Wireless data connectors. Wireless connectors are critical for mobile robots that send sensor data and receive commands via Wi-Fi and radio signals. They are also used in stationary industrial robots connected to a central server.
Today, many types of connectors serve the purposes of robotics. Commercial connectors are available in housings that can withstand harsh environments and are flexible enough to handle the robot’s movement. Connectors can inform robot design and assembly at end effectors and robotic joints, and can affect the speed of data transfer.
Powering the robot
The power supply is a major manufacturing challenge, particularly for mobile robots. Stationary robots may connect directly to an industrial power source, while mobile robots are usually powered with rechargeable lithium-ion batteries. Batteries may require custom design and manufacturing based on robot Wattage requirements, mobility, weight restrictions, charging source, and environmental factors.
One consideration for battery-operated robots is the power source used to charge the battery. It may be necessary to design a specialised battery charger that accounts for the battery’s power r equirements, power source limitations, and environmental factors. The charger may be installed directly on the robot itself or the charger may be designed as standalone equipment.
Some power sources include:
- Standard industrial power from a municipal power station. For mobile robotics, a standard power source usually powers a standalone battery charger rather than the robot itself.
- Solar panels, either installed on the robot or at a separate charging station. Solar panels can also be installed on the robot to provide backup power during remote operation.
- A portable power generator, often fueled by petrol, propane, or bio-diesel. Advances in generator technology increase the portability and fuel-efficiency of generators, and expand the possibilities for fuel sources.
Another design consideration for battery-operated robots is battery hot-swapping during robot operation. A robot with hot-swapping capabilities is powered with multiple batteries. When one battery is discharged, it can be replaced while the robot is in operation.
The discharged battery is then recharged for future use.
Robotics Hardware Challenges
Resource shortages
Global shortages of computer chips and commercial off-the-shelf hardware have a major impact on robotics manufacturing.[11] Hardware shortages are outside of the control of robotics manufacturers, and may result in design compromises, increased costs, missed deadlines, and inaccurate projections.
Environmental conditions
The robot operating environment is a consideration for every piece of robot hardware. Robots work in hazardous environments, are exposed to weather, dust, pressure, or may be submerged in water. This means that IP rating and chemical tolerance limit the hardware that can be incorporated into the robot design. Custom housing for hardware and the robot chassis can mitigate some of these limitations, but may also result in additional manufacturing challenges. Software can also be leveraged to minimise contact with hazards. For example, an autonomous system might be programmed so that the robot can recognize and intelligently navigate hazardous environments.
Increasing computational power
As robotic applications expand from controlled environments to uncontrolled there is a natural increase in the computational load. In combination with software advances, computing platforms that enable efficient and fast computation to solve complex perceptual and control tasks will be essential.
Key advances in this area include:
Open research and development platforms
Open platforms for research and development that encompass robot hardware, software, computing platforms, and simulation are supported by many academics. These open platforms facilitate comparison and benchmarking of various methodologies while allowing researchers to concentrate on the necessary algorithmic progress.
Standardisation is necessary to hasten the development of the sector by enabling efficient exchange and integration of algorithmic, hardware, and software components.
Neuromorphic computing hardware
Neuromorphic computing is a method of computer engineering in which elements of a computer are modelled after systems in the human brain and nervous system. It uses specialised computing architectures that reflect the morphology of neural networks from the bottom up: dedicated processing units emulate the behaviour of neurons directly in hardware, and a web of physical interconnections (bus systems) facilitates the rapid exchange of information.
Neuromorphic computing hardware is expected to take its place among other platforms—central processing unit
(CPU), graphics processing unit (GPU), and field programmable gate array (FPGA). Neuromorphic hardware systems are promising in robotics thanks to their modularity and flexibility. These systems have a high degree of parallelism and asynchronous event-driven implementation, meaning that multiple computations can be performed quickly, simultaneously, and automatically. Neuromorphic systems incorporate in-hardware learning by combining processing and memory, unlike traditional systems that have separate components for these functions. This type of machine learning is supported by software algorithms that are based on synaptic plasticity and neural adaptation.[13]
Computational solutions inspired by insect brains
Uncrewed aerial vehicles (UAV) require a robotic system that is particularly resource-constrained because UAVs must be fast, light, and energy efficient. Some computational solutions for UAVs are inspired by insect brains, such as obstacle avoidance, object targeting, altitude control, and landing. Elegant robotic solutions are based on insect biology, including insect embodiment, tight sensorimotor coordination, swarming, and parsimony. In UAVs, these solutions take the form of algorithms and multi-purpose circuits.
An important insight from these solutions is that close integration of algorithms and hardware leads to extremely compact, powerful, and efficient systems. Hardware platforms from microcontrollers to neuromorphic chips can support these bio-inspired algorithms. Particular attention should be devoted to the interface between computing and movement-generating hardware. [12]
Artificial skin: combining sensors with materials
An emerging area of robotics is artificial skin, or smart skin, which integrates robot sensor hardware with the actual robot form. While this area of research has multiple applications, one of the initial areas of interest is smart skin that enables closer robot-human interaction. The smart skin is used to sense unexpected physical interactions. There is an opportunity for computing fabric integrated directly into the sensor. [13]
Summary
Robots have many applications that extend human capabilities, and robot hardware requirements vary depending on the tasks that a robot is built to perform. Common parts of a robot are sensors, the CPU, motors, actuators, end effectors, and connectors. All of these components pose hardware considerations individually and as part of a system.
Outside of the robot’s working parts, there are other factors that raise hardware challenges for robot manufacturers. Resource shortages can result in design changes and manufacturing delays, while environmental conditions limit the materials and components used on the robot, and may require software-based solutions.
Recent innovations in robotics technology include increased computational power, advanced software solutions, as well as the development of biomimicry, such as software based on insect brains, smart skin, neuromorphic computing and other emerging technology. These innovations extend the capabilities of robots and advance the field of robotics hardware.
-
Gabriel Aguiar Nour, State of the Art Robotics, Ubuntu Blog, May and June 2022 edition
-
Sven Parusel, Sami Haddadin, Alin Albu-Schaffer, Modular state-based behaviour control for safe human-robot interaction: A lightweight control architecture for a lightweight robot, IEEE International Conference on Robotics and Automation, 2011.
-
Mathanraj Sharma, Introduction to Robotic Control Systems, Medium Newsletter, Sept 2020.
-
Ravi Teja, Blog on Raspberry Pi vs Arduino, www.electronicshub.org, April 2021.
-
Mats Tage Axelsson, Top 5 Advanced Robotics Kits, www.linuxhint.com, September 2022.
-
Techopedia contributor, Actuator, www.techopedia.com, Jan 2022.
-
Tiffany Yeung, What Is Edge AI and How Does It Work?, https://blogs.nvidia.com/blog/ 2022/02/17/what-is-edge-ai/, Feb 2022.
-
NT Desk, The state has the potential to grow as an electronic manufacturing centre, www.navhindtimes.in, Oct 2019.
-
Dr Matthew Dyson, Printed Electronics: Emerging Applications Accelerate Towards Adoption, IDTechEx, Nov 2021.
-
Advanced network professionals blog, www.getanp.com/blog/35/hardwa re-your-business-needs-to-succee d.php, Dec 2019.
-
Advanced Mobile Group, The Latest Technology and Supply Chain Trends in Robotics for 2022 and Beyond. https://www.advancedmobilegrou p.com/blog/the-latest-technology -and-supply-chain-trends-in-robot ics-for-2022-and-beyond, Oct 2022.
-
Moncourtois, Alyce. Can Insects Provide the "Know-How" for Advanced Artificial Intelligence? AeroVironment https://www.avinc.com/resources/av-in-the-news/view/microbrain-case-study 2019.
-
Yirka, Bob. Biomimetic elastomeric robot skin has tactile sensing abilities. Tech Xplore. https://techxplore.com/news/2022-06-biomimetic-elastomeric-robot-skin-tactile.html June 2022.
Manufacturing

Industry 4.0 and robotics manufacturing
For over a decade, the manufacturing sector has been undergoing a rapid digital transformation as sensors, internet-connected devices and cyber-physical production systems (CPPS) are increasingly deployed on the shopfloor.
CPPS systems are considered as the main driver of the fourth industrial revolution (Industry 4.0) in manufacturing.
They digitise physical processes and enable their optimisation by means of cutting-edge technologies like Big Data, Artificial Intelligence, and the development of powerful digital twins.
This rapid shift has had a significant impact on how products are manufactured, and in some cases lowering the barrier to entry for smaller original equipment manufacturers (OEMs) and reducing investment costs. This is a benefit for the development of robotics where smaller teams can now more competitively compete against traditional larger players.
In this chapter, we examine the cutting-edge systems and technologies that enable the acceleration of the robotics industry. We look at how digital manufacturing is accelerating the industry through its ability to offer increased accessibility to the manufacturing processes necessary to advance robotics including 3D printing, CNC machining, and injection moulding.
Industrial Robotics as an Innovation Driver
Industrial robots are one of the most prominent types of CPPS systems. They comprise physical parts that carry out field automation processes, yet they are controlled by digitally enabled data-driven applications. Industrial robots are usually deployed to automate the following two types of manufacturing tasks:
- Repetitive tasks, such as painting, palletizing, and product assembly. Industrial robots are faster and more efficient than humans in performing such processes. This is because the corresponding manual tasks are usually tiring, cumbersome and error prone.
- Hazardous tasks, such as materials handling, arc welding, and CNC monitoring. Such tasks require human workers to work in harsh environments, to perform dangerous tasks, or even to deal with hazardous substances.
Industrial robots are contributing to more flexible, scalable, and efficient production processes. Contrary to human workers, they work 24×7 in fast, safe and cost-effective ways. Nowadays, they are commonly deployed to support many different automation processes on the factory floor.
Industrial robots are also perceived as one of the most powerful ways to automate and build flexible production lines that enable customised production models like made-to-order and engineering-to-order. The latter model leads to mass customization i.e., the ability to produce highly customised products with only marginal increase in production cost.Industrial robots can automatically reconfigure production lines to produce alternative product variants with limited, or even zero, human intervention. Nevertheless, this flexible manufacturing approach is gradually reaching its limits, as radically differentiated products require changes, not only in the configuration of the production line, but also on the machinery used, especially when there is a need to manufacture a new product. Designing the production system of a new product requires efforts that are orders of magnitude higher than producing a variant of an existing product.
The need to overcome this barrier drives a novel use of industrial robots: using manufacturing robots to produce a new machine in order to achieve unprecedented scalability and efficiency in production. During the last couple of years, industrial robots are increasingly used to build parts of machines or even entire industrial machines from scratch. To this end, industrial robots leverage digital models of the machines and emerging technologies like additive manufacturing.
Manufacturing as a Service: When the Machine Makes the Machine
A key enabler of the advancement of robotics innovation is the leveraging of digital models to enable the manufacturing as a service (MaaS) paradigm. MaaS or digital manufacturing platforms offer access to various manufacturing processes, such as 3D printing, CNC machining, and injection moulding, and provide an easy transactional experience by allowing customers to upload their part designs to quickly get quotes for manufacturing costs and lead times.
Digital manufacturing opens access to cutting edge manufacturing processes for design teams of any size, with low investment costs, transparent lead times and design and iteration support.
Robotics-based manufacturing models deliver:
- Flexibility, as it can enable the development of diversified machines with minimal human involvement.
- Resilience, through easing production repurposing and facilitating the development of effective manufacturing responses to fluctuations in demand, as well as to supply chain disruptions.
- Scalability, as it helps alleviate the bottleneck of developing new machinery.
- Supply chain efficiency, through enabling supply chain stakeholders to instantly access data models of machines or of their parts.
Advantages of Digital Manufacturing for Robotics
Rapid, accessible prototyping
Digital manufacturing can allow for the remote design and development of robotic prototypes, as well as remote testing and evaluation of those prototypes. This can allow for faster development cycles, as well as the ability to test prototypes in a variety of different environments. Having parts shipped and ordered enables development teams across the globe to access quality manufacturing.
Access to advanced manufacturing technologies
Digital manufacturing provides access to advanced manufacturing technologies, such as metal 3D printing and CNC machining.
Data-driven design
Digital manufacturing can enable the collection and analysis of large amounts of data on the performance of robotic systems. This can be used to inform the design process and improve the performance of the final product.
Collaborative design
Digital manufacturing can allow for collaboration between designers, engineers, and other stakeholders, regardless of their location. This can enable real-time communication and collaboration on the design of a robot, which can lead to more efficient and effective development. Some digital manufacturing platforms offer a design portal that all stakeholders can access and contribute to, further accelerating the design and development phase.
Cost reduction
Digital manufacturing can reduce the cost of robotic design and development by offering low-volume prototyping and fixed material costs pricing models.

Design for manufacture (DFM)
Advanced digital manufacturing platforms will provide manufacturing analysis with each quote. After uploading a 3D CAD model, a quote is generated that contains pricing information as well as valuable feedback from the quote to understand how your design impacts the manufacturability and cost of your part. Protolabs offer this service.
At the core of this feature is Protolabs' manufacturability analysis of part designs that are provided to ensure every robotics project gets well-designed parts ready for manufacture. Within the quote analysis, customers are able to access an interactive three-dimensional image of their part design, which allows review of part geometry and assess any potential design issues that are highlighted.
Some issues will be identified in the required changes tab, and those changes will need to be modified before the parts can be made. Issues that are not critical to part production will be listed as advisories. Those advisories do not require change, but do indicate design considerations for optimal performance in the manufacturing process you choose. Within the platform, you can move the transparency slider in the 3D viewer to full transparency so that you can hide all of the areas of your part that do not need to be addressed, leaving only the important design considerations. It brings into focus any areas that need further review. Those may include undercuts, draft, surface finishes, wall thickness, and material flow.
Undercuts
The process supports simple undercuts in part geometry. A side-action can be built into part design to create a through-hole undercut feature, if needed. The maximum side-core dimensions are: 8.419 in. (width), 2.377 in. (height) and 2.900 in. (pull).
Draft
If the part has very little to zero draft, a required change or advisory may appear in your quote. Draft is recommended on all parts, and Protolabs recommends adding 0.5 degree of draft on all vertical faces, if possible. In most cases, applying 2 degrees of draft where possible is best for moulding, but is not required. If you choose to ignore a draft advisory, Protolabs will make your part as-is, without draft in the noted area, but issues can arise such as drag marks, distortion from ejection stresses, or other effects that can cause delays.
Surface finishes
Depending on the surface finish selected, additional draft may be suggested. With textured finish on parts, PM-T1 (light bead-blast) generally requires at least 3 degrees of draft, and PM-T2 (medium bead-blast) generally requires at least 5 degrees of draft.
Wall thickness
Uniform wall thickness is recommended on all parts to help minimise sink and warp, but if there are any features that are too thin or thick, Protolabs’ manufacturability analysis will pinpoint those issues in the interactive CAD model and provide a precise thickness measurement that those features can be adjusted to. If a feature is too thin, fill problems can occur; if it’s too thick, sink is possible. Note that recommended wall thicknesses vary by resin type.
Material flow
On certain parts, Protolabs will run a ProtoFlow fill analysis that shows an animated display of resin flow through the quoted part. Various colours represent the pressure field on an indicated scale. If the virtual resin flow is poor, adjustments may need to be made in either part geometry or material type.
Customers are also able to make adjustments to the surface finish, material, and delivery of your parts within your quote as well as modify sample and production quantities as needed. Because it is an interactive quote, total cost will update in real time to reflect any changes you make, and a quote remains active for 30 days.
Key manufacturing processes delivered through Digital Manufacturing: 3D printing, CNC machining and injection moulding

3D printing enables manufacturers to build parts by joining materials layer by layer based on a computer aided design (CAD). Within robotics manufacturing, 3D printing has created new ways of designing that allows for rapid, affordable prototyping and design iterations using end-product materiality for accurate testing.
3D printing also edges closer to a method of deploying robotics at scale and on-demand.
3D printing offers endless possibilities regarding geometries and materials that other services potentially can't provide, making it an excellent match with the development of robotics projects.
Why 3D printing for the Robotics industry?
- Ability to deliver unique design features
- Quick prototyping
- Design versatility
- Complex geometries, including lattice structures
- Significant weight reduction over other manufacturing processes with the same material
- Waste reductive process (additive rather than reductive)
3D printing can be particularly useful in the the design and manufacture of cameras, motors, sensors, microcontrollers, manipulators, and robotic arms. Further discussed in the materials section, the materials available for 3D printing are expanding. Once limited to a narrow range of plastics, 3D printing is now available in metals, ceramics, and flexible materials.

CNC machining, which includes both milling and turning, is a valuable manufacturing process for robotics development and end manufacturing. Ideal for prototyping and low volume production, automated CNC machines enable robotics developers to order and receive parts, sometimes within just days. CNC also offers tighter tolerances than other services, and its 5-axis process provides high complexity and variation, important for applications that demand precise, repeatable movements. Finally, the service allows for controlled surface finishes, which are needed for low-friction components in interactive parts. These aspects make CNC machining perfect for the highly customised parts at low volumes that robotics often requires.
Why CNC machining for the Robotics industry?
- Precision parts (important as parts need to fit together perfectly - critical for the proper function of a robot)
- Strong, durable materials
- Can be used to create complex shapes - allows for greater design flexibility
- Fast and efficient
- Surface finishes - good for low friction parts required for interacting
- CNC machining is a good fit for the manufacture of gears, end effectors, custom fixtures, motor and components among others.

Injection moulding can be used for plastics, liquid silicone rubber, as well as overmoulding and insert moulding. It offers a repeatable option when larger-scale production is required. It can be a more cost-effective option for larger quantities as the same mould is used for each part, and the parts are consistent and precise. But new methods of injection moulding are also enabling prototyping and testing. While it is not the key process used for producing robotic components, it is commonly used for production of housings, frames, casings, gears and camera mounting frames. Further, the liquid silicone rubber (LSR) process is increasingly used with the introduction of soft robotics.
Why injection moulding for the Robotics industry?
- Precision components
- Repeatability
- Light-weight (plastic parts) Scalability
- Rapid prototyping
Digital manufacturing eases the deployment of 100s of robots in the manufacturing shop floor, while facilitating their collaboration towards end-to-end automation.
Furthermore, digital manufacturing enables scalable on-demand automation in-line with the pay-as-you-go paradigm. At the same time, 3D printing and CNC machining lays a foundation for robotic machines to manufacture other robotic machines automatically and quickly. This is a starting point towards hyper-automated and scalable manufacturing systems that can build their own components based on the concept of “machines that build machines”.
Iterative Design
Iterative design is a process in which a product or system develops through a series of repeated cycles, each of which builds upon the previous cycle's results.
This process allows for the continuous improvement and refinement of the product or system based on feedback and testing. It is commonly used in complex design projects that may require multiple rounds of testing and refinement. Iterative design practices can be hugely beneficial for robotics projects where there are multiple overlapping outcomes required such as task-specific performance, material robustness, aesthetics, and controller costs. Iterative design can be used in robotics in a number of ways, such as developing control algorithms, human-robot interactions and task-specific performance patterns. However, it is also a key design methodology for developing the robot’s physical design.
In general, the iterative design allows for rapid prototyping, testing, and refinement of robotic systems, allowing for faster development and better performance. The steps of iterative design can vary depending on the specific context and application but for a robotics development project there are some common themes.
1. Define the problem or opportunity: understand the project's goals, constraints, and requirements.
2. Research and ideation: gather information, explore potential solutions, and generate ideas. A reputable MaaS platform can offer extreme value at this stage by offering support on the various material and manufacturing processes available. Cost, minimum order numbers, and speed are all factors when selecting a manufacturing method and can also influence material choice. In some cases using a material close to the estimated final product will be essential, in other situations a lower-cost material is adequate for initial iterations.
3. Design and prototype: create a design or prototype of the solution, considering the research and ideation from the previous step.
By using a digital manufacturer with automated design analysis feedback and onsite experts, you can often go through multiple iterations before manufacturing a single part. When transitioning from design to prototype, parts can be ordered and shipped within days.
4. Test and evaluate: gather feedback on the prototype, test it with users or other stakeholders, and evaluate its performance.
5. Iterate and improve: use the feedback and evaluation results to make changes and improve the design or prototype.
Repeat the above steps as needed until the design or prototype meets the goals and requirements of the project. It's worth noting that the iterative design process can be cyclic, and the steps may not always be linear; it's common to revisit previous steps to refine the design and improve the quality of the final product.
Technology and Project Survey
In the following chapter we provide a survey of cutting-edge robotics projects from across the globe. We’ve attempted to gather a rich variety of projects from the length of the robotics definition that demonstrates the depth of the industry. The projects range widely in their use cases and application, materials, and manufacturing methods and come from both the research labs of universities to established engineering firms.
Manufacturing robotics: Franka Emika Robotics
Franka Emikas Panda is a sensitive, interconnected, and adaptive robotic arm. The robotic arm is inspired by human agility and sense of touch. With torque sensors in all seven axes, the arm can delicately manipulates objects, and accomplish programmed tasks. The collaborative lightweight robot system is specifically designed to assist humans.
What sets the Franka Emika Panda apart from other single-arm, collaborative robots is its unique training and programming methods. The robot learns movement through physical demonstrations by imitating an expert on the task it is being prepared for. This can be physically demonstrated by a person or another robot. To train the Robot to perform specific actions, the user can manually direct the robotic arm through a sequence of motions while pressing buttons on the arm, for the robot to commit each step to memory. The arm learns the task in only a few minutes and can start repeating the action without the need for complicated software updates or programming. The user can also choose from several pre-designed apps to use the arm for other tasks.
The robot can also learn from the stimulation of 3D artificial environments. This allows a robot to swiftly construct a 3D map of its immediate environment, which includes objects and their semantic labels (for example, a chair vs a table), as well as walls, rooms, people, and other structures. The robot can also use the model to extract necessary information from the 3D map, such as the placement of objects and rooms, as well as the movement of humans along its route. The Franka Emika Robot’s ability to “think” or reason through machine learning makes it aware of its immediate environment. As a result, the cobot is safe around human counterparts.
Industrial automation is frequently used in places where precision is as essential as safety. Examples include packaging and material handling, carrying a heavy load, quality control and inspection, metal fabrication, and repetitive production. Robotics, on the other hand, are frequently found working alongside people on factory production lines.
To avoid the potential to harm from the robotic arm in motion, the Franka Emika Robot has a highly advanced robot manipulator that can sense its environment. The Franka Emika is equipped with a force-sensing control scheme and is designed to work safely alongside people.
The cobot is designed to perform tasks that require direct physical contact in a carefully controlled manner. It achieves its dexterity through a torque-control.
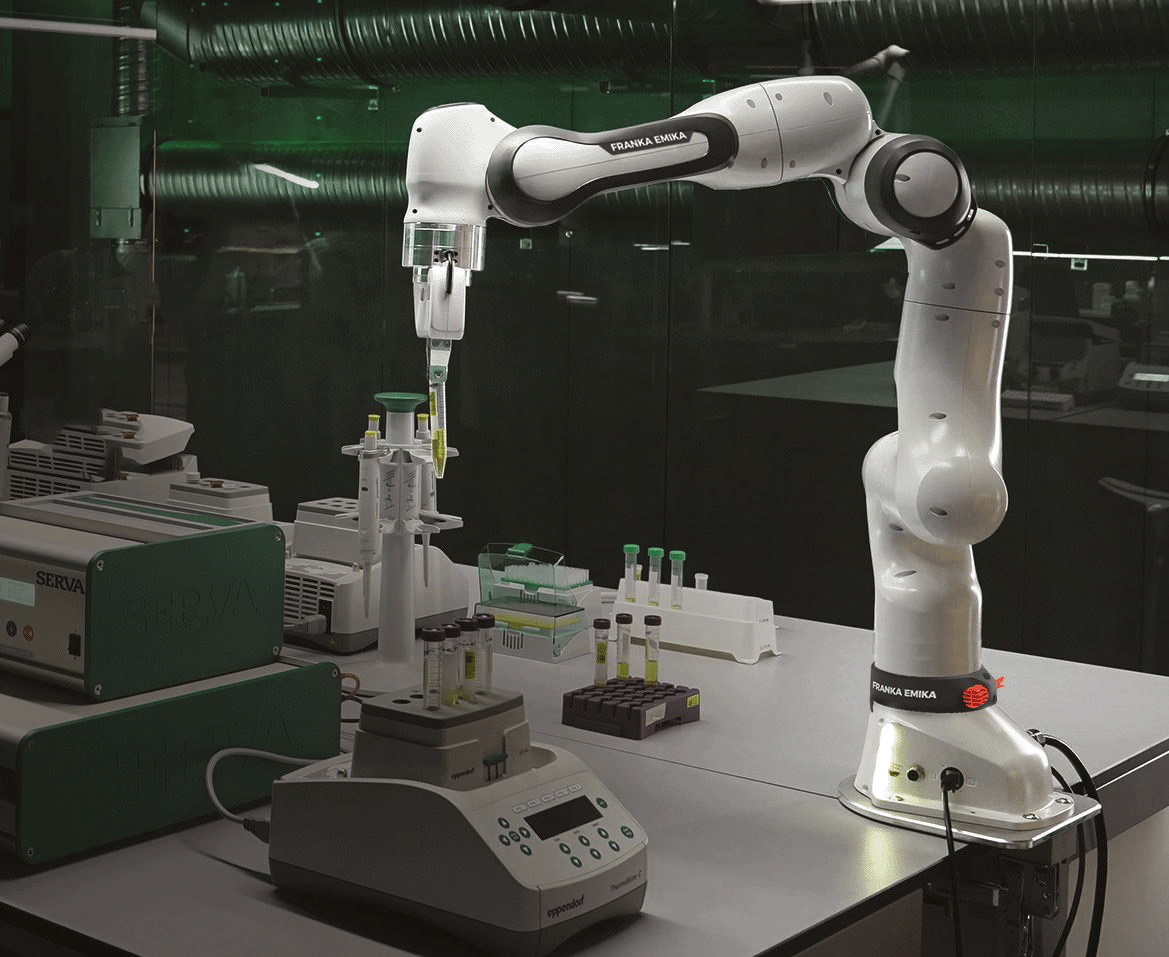
Specifications:
- Degrees of freedom (DOF): 7
- Payload: 3 kg
- Sensitivity: torque sensors in all 7 axes
- Maximum reach: 855 mm
- Repeatability: +/- 0.1 mm
- Interfaces: ethernet (TCP/IP) for visual intuitive programming, input for external enabling device, input for external activation device or a safeguard control connector and hand connector
- Interaction: enabling and guiding button, selection of guiding
- Protection rating: IP30
- Weight: 18 kg
- Hand
- Parallel gripper with exchangeable fingers
- Grasping force: continuous force maximum force
- Weight: ~ 0.7
Bionic Robots: Jueying X20
The Jueying X20 is a quadruped robot, designed and built based on user feedback from real-world application scenarios. Its robust “dog” design enables it to be applied in search and rescue operations. Further, the company is developing coordinated multi-robot exploration that sees multiple robots deployed to work autonomously together on a single task.
The robot has a strong durable build to operate and perform tasks in challenging conditions. The X20 can carry a load of 85 kilograms in addition to its self-weight of 50 kilograms. They can overcome any obstacle within the height range of 18-20 cm very easily and operate on a slope of 30 degrees. The Jueying X20 also includes depth sensor cameras to perceive changes in the environment and a laser radar system for navigation purposes. It also has thermal imaging to help identify humans and other living species in general and cataclysmic environments. This can help the rescue teams in their operations by locating the heat signatures of the people under the rouble.
Jueying X20 can travel across ruins, heaps of rubble, stairwells, and other unorganized passageways in high-risk outdoors and indoor post-disaster environments. The robot dog can lessen the likelihood of subsequent mishaps thanks to its flexibility in movement in all directions and its ability to maneouver within a constrained contact area. The four-legged robot can carry out detection tasks in adverse weather conditions such as torrential downpours, dust and sand storms, cold temperatures, and hail thanks to the IP66 industrial-grade protection.
Robots from the Jueying series have found use in a variety of situations, including hazard identification, surveying hazardous terrain, inspecting high-voltage power facilities, and taking part in rescue operations. The average run time of the robot is around 4hrs, but with the autonomous charging enabled with several external power interfaces, they can be easily charged using several different types of power outlets and sent back into action right away. By integrating a wide range of application modules including a long-distance communication system, a bi-spectrum PTZ camera, gas sensing equipment, an omnidirectional camera, and a pickup, the robotic solution includes long-distance control and images transmission, heat source tracking, real-time detection of harmful gases and rescue calls, among other functions. Additionally, the X20 can also be equipped with a robot arm to do much more.

Specifications:
- Gross Weight: 50kg
- Maximum Working Load: 85kg
- Safe Working Load: 20kg (Duration of operation >2h)
- Standing Dimension: (L* W * H) 95mm*470mm*700mm
- Maximum Speed: 4.95m/s
- Average Mileage: 15km (3.6km/h, with a load of 0 kg)
- Average Runtime: 4h (with a load of 0 kg)/ 2hwith a loadof 20 kg)
- External Power Interface: 5V;12V;24V;72V(BAT)
- External Communication Interface: Ethernet;WIFI;USB;RS485;RS232
- Optional Equipment Support: dual-light pan,robotic arm, debug shelf
- 4G/5G communication
BionicANTs
Robotics company Festo, is combining Selective Laser Sintering (SLS) with 3D MID technology to create experimental swarm robotics known as BionicANTs. The bodies of the BionicANTs are made of polyamide powder, which is melted layer by layer with a laser. 3D Moulded Interconnect Devices feature spatial conductive tracks, which are visibly attached to the surface of shaped parts and act as circuit boards for electronic and mechatronic subassemblies. They make do without any cables and only require a small amount of effort to be assembled. Well-known areas of application for MID technology are automotive construction, medical and telecommunication engineering, and the aerospace industry. For the first time, Festo is now producing miniature robots with the technology, the BionicANTs serve as a method for testing the cooperative behaviour of creatures transferred to the world of technology using complex control algorithms. Like their natural role models, the BionicANTs work together under clear rules. They communicate with each other and coordinate both their actions and movements. Each ant makes its decisions autonomously, but in doing so is always subordinate to the common objective and thereby plays its part towards solving the task in hand.
In an abstract manner, this cooperative behaviour provides interesting approaches for the factory of tomorrow. Future production systems will be founded on intelligent components, which adjust themselves flexibly to different production scenarios and thus take on tasks from a higher control level. The BionicANTs demonstrate how individual units can react independently to different situations, coordinate with each other and act as an overall networked system.
By pushing and pulling together, the artificial ants move an object across a defined area. Thanks to this intelligent division of work, they are able to efficiently transport loads that a single ant could not move.


Technical data:
- Length: 135mm
- Height: 43mm
- Width: 150mm
- Weight: 105g
- Step size: 10mm
- Material, body and legs: polyamide, laser-sintered
- Material, feelers: spring steel
- 3D MID: laser structuring and gold plating by Lasermicronics
- Actuator technology, gripper: 2 trimorphic piezo-ceramic bending transducers (32.5 × 1.9 × 0.7 mm)
- Actuator technology, legs: 18 trimorphic piezo-ceramic bending transducers (47 × 6 × 0.8 mm)
- Stereo camera: Micro Air Vehicle (MAV) lab of the Delft University of Technology
- Radio module: JNtec
- Opto-electrical sensor: ADNS-2080 by Avago Technologies
- Processor: Cortex M4
- Rechargeable batteries: 380 mAh & Li-Po batteries in series, 8.4 V
Androids: Clone Robotics
Previously humanoid-type robots have been limited to applications related to entertainment, education, and research. However, Polish startup Clone is looking to explore how super strong humanoid robots could be applied in environments unsafe for humans, which include nuclear waste facilities, wet labs, meat processors, space stations, and chemical plants. The basic materials that are to be considered while designing a robotic arm are steel, rubber, silicone, aluminum, Kevlar, and biodegradable material. The hard materials (i.e. steel and aluminum, etc.) can be utilized in building the core or the skeletal structure of the clone arms, and the softer materials (i.e. silicone and biodegradable smart materials, etc.) make up the muscle mass and the outer covering or the skin of the functional limb. As for the muscle contractions and other functioning of the limbs different pneumatic principles are incorporated.
The Polish Startup Clone has currently developed the robot arm and hand and is working on building out the torso. Their model incorporates steel and plastic as the base material and silicone for the outer coverings. Additionally, they replaced the pneumatic air muscles with the hydro version for better maneuverability and easier maintenance of the prosthetics. What makes Clone special is the use of hydraulics to mimic the
multi-articulation of human hands. Most macro-scale robots today, including those with anthropomorphic hands use DC motors for actuation. While this may work for joints with three degrees of freedom, human-level hands require actuators that are far more robust to chaos in the environment. A general-purpose robot performing many tasks in a “chaotic” environment such as a human household will need to actuate its hands with a mechanism that can adapt to strong, random forces from the environment.
A human hand offers a total of 27 degrees of freedom to perform all sorts of tasks. In order to inculcate that level of degree of freedom in the prosthetic arms, a total of 36 different muscles have been designed and included in the latest versions of clone arms. The beta Clone Hand includes 16 magnetic encoders, which measure the joint angles and velocities, and a total of 35 pressure sensors, for almost every muscle/valve. These sensors help monitor and regulate the proper functioning of the bionic arm.

Agricultural Robotics: Carbon Robotics’ Autonomous LaserWeeders
Carbon Robotics’ Autonomous LaserWeeders take the technology of machine vision from manufacturing and apply it to agriculture to create an autonomous bot-like robot capable of independently identifying and destroying weeds in crop conditions. The robot is designed for 24-hour use, contributing to increased crop yields and lower production costs. The robot has a traditional design of tractors and other agricultural equipment to meet the demands of the industrial agriculture environment.
The Autonomous LaserWeeder from Carbon Robotics works all day long with its 75 gallons of fuel capacity. It utilizes 4 hydraulic drive motors along with its GPS and visual guiding system to stay inside the lines of the field, travel through furrows, and turn around to start scanning the following row. Real-time scanning of the field, harvests, and weeds is done via 12 high-resolution camera lenses. While moving, a tough, inbuilt supercomputer utilizes machine learning to quickly identify unwanted weeds amongst the prized crops. The meristem of each weed is then subjected to a beam of high-powered laser thermal energy, which burns away the weed. The laser beam operates at 150W and has an accuracy of about 3mm. The Autonomous LaserWeeder uses 8 simultaneously running laser units to provide fast zaps on budding weeds and can eliminate over 100,000 weeds every hour.

Specifications:
- Weight: 9,500lb
- Track width: 80in
- Wheelbase: 110 in (9.2 ft)
- Vehicle speed: 5 mph
- Coverage: 15-20 acres/day
- 12 high-resolution cameras targeting weeds
- 8 independent weeding modules
- 150W CO2 lasers with 3mm accuracy
- Ready to fire every 50 milliseconds
- 74-hp Cummins diesel QSF2.8
- 4 hydraulic drive motors
- 75-gallon fuel capacity
Care Robotics: Hello Robot - Stretch Robot
Hello Robotics is a robot for researchers by researchers working on robotics projects addressing care needs.
Historically, versatile mobile manipulators have been large, heavy, and expensive. Stretch changes that.
Thanks to its pared-back design, it performs a wide range of tasks in a simple, intuitive manner. The Stretch robot is designed for autonomous operation. It comes with a calibrated robot model (URDF) that is well-aligned to 3D camera images, and open source calibration code in Python that is customizable. ROS integration simplifies the use of existing ROS
packages for autonomy, including the ROS navigation stack.

Image credit: Hello Robot
Specifications
- Interact with people using a low mass, contact-sensitive body
- Work in clutter with a compact footprint and a slender manipulator
- Go outside the lab, it only weighs 51 lb.
- Everything included: a gripper, a computer, sensors, and software
- Ready for autonomy: calibrated, Python interfaces and ROS integration, autonomy demos in Python, open source code
Voxels Assembler Robot
MIT researchers have made substantial progress towards developing robots that are practically and economically capable of assembling essentially anything, including objects that are much larger than themselves, such as larger robots, structures, and cars. In contrast to past iterations of assembler bots, which were linked by bundles of wires to their power supply and operating systems, the Center for Bits and Atoms (CBA) at MIT has developed a new system of voxel bots that can each transmit both power and information from one unit onto the next one. The construction of structures that can lift, move, and manipulate materials, including the voxels themselves, as well as support loads, could be made possible by this.
The new method uses voxels, which are vast, useful structures made up of a variety of tiny, identical subunits. The actual robots are made up of a series of numerous voxels linked end to end. These can migrate like inchworms to the appropriate spot, where they can grasp other voxel employing attachment sites on one end, connect it to the growing structure, and release it there. Every step of the way, these robotic machines have to make decisions as they assemble something. To assist with the following activities, it might construct a building, build a bigger or identical robot or both.
For instance, before the production of a novel car, the manufacturer may invest a year in tooling alone. The new system, however, would skip that entire procedure. Gershenfeld and his pupils have been collaborating closely with automakers, aviation firms, and NASA because of these potential efficiencies. But even the comparatively low-tech building construction sector might stand to gain. Although there is growing interest in 3-D printed homes, the printing equipment needed today is at least as large as the home being created. Alternatively, it could be more advantageous if such buildings are instead constructed by swarms of tiny robots.

Image credit: MIT
RoboBee
Inspired by the biology of a bee, researchers developed a tiny mechanical insect that achieved flight in 2012 for the first time by flapping its wafer-thin wings at the speed of approximately 120 flaps per second. Prof. Robert Wood of the Harvard Micro Robotics Lab played around with the design and the material of the tiny robot and conducted the first controlled flight test of the RoboBee. A RoboBee uses “artificial muscles” made of polymers that contract whenever a voltage is introduced to take flight. It is roughly the size of a paper clip and weighs less than one-tenth of a gram. Some RoboBee models have additional modifications that enable them to fly and “perch” on different surfaces utilizing static electricity in addition to swimming underwater. RoboBee could be used for a variety of tasks, including agricultural pollination, high-resolution meteorology, climate, and environmental monitoring, espionage, rescue operations, and surgical procedures.
RoboBee is made of different materials including ceramics, composites, polymers, and metals. Researchers at the Wyss Institute have created novel manufacturing techniques for building RoboBees, including so-called Pop-Up microelectromechanical (MEMs) techniques that have already significantly pushed the limits of current robotics engineering and design techniques. In contrast to conventional MEMS approaches or manual “nuts-and-bolts” assembling, the Pop-Up MEMS method efficiently builds many micro machines at once while also producing sophisticated, articulated mechanisms. Additionally, “Pop-Up” MEMS devices can combine piezoelectric actuators, integrated circuits, mechanical features at the micrometer scale, a range of materials, and real 3D geometries. Pop-up MEMS may make it possible to mass produce sophisticated micro-robots with sizes ranging from a few nanometers to a few centimeters, like the Wyss Institute's RoboBees, as well as unique implantable medical devices and specialized optical systems.

Image credit: Wyss Institute
Specifications:
- Wing span: 3 cm (1.2 inches)
- Weight: 80 milligrams
- Flapping speed: 120/sec
- Speed: 3.6 km/h (2.2 mph)
- Sensors: Gyroscopes, optical flow sensors, ocelli sensor (insect-inspired horizon detection sensors)
- Actuators: Piezoelectric bending bimorph cantilevers
- Degree of Freedom: 3 to 5 (Depending on the model)
Email [email protected] with your name, title of activity, and completion date to receive your certificate