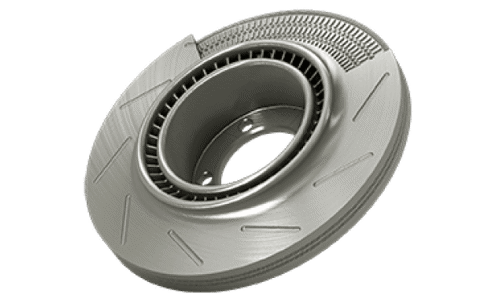
Direct Metal Laser Sintering (DMLS) for Metal 3D Printing
Get quality metal 3D-printed prototypes and production parts. Request an online quote today.
shield_locked All Uploads are Secure and Confidential
Certifications ISO 9001:2015 | ISO 13485 (Protolabs Network) | DNV Qualification of Manufacture Certification for Inconel 718
Direct metal laser sintering (DMLS) is an industrial metal 3D printing process that builds fully functional metal prototypes and production parts in 7 days or less. A range of metals produce final parts that can be used for end-use applications.
Metal 3D printing technology is commonly used for:
- Prototyping in production-grade materials
- Complex geometries
- Functional, end-use parts
- Reducing metal components in an assembly
Metal 3D Printing Material Options
Stainless Steel (316L)
expand_less expand_moreStainless steel 316L is a workhorse material used for manufacturing acid and corrosion resistant parts. Select 316L when stainless steel flexibility is needed; 316L is a more malleable material compared to 17-4 PH. Final parts built in 316L receive stress relief application.
Primary Benefits
- Acid and corrosion resistance
- High ductility
Aluminium (AlSi10Mg)
expand_less expand_moreAluminium (AlSi10Mg) is comparable to a 3000 series alloy that is used in casting and die casting processes. It has good strength -to-weight ratio, high temperature and corrosion resistance, and good fatigue, creep and rupture strength. AlSi10Mg also exhibits thermal and electrical conductivity properties. Final parts built in AlSi10Mg receive stress relief application.
Primary Benefits
- High stiffness and strength relative to weight
- Thermal and electrical conductivity
Inconel 718
expand_less expand_moreInconel is a high strength, corrosion resistant nickel chromium superalloy ideal for parts that will experience extreme temperatures and mechanical loading. Final parts built in Inconel 718 receive stress relief application.
Primary Benefits
- Oxidation and corrosion resistance
- High performance tensile, fatigue, creep and rupture strength
Titanium (Ti6Al4V)
expand_less expand_moreTitanium (Ti6Al4V) is a workhorse alloy. Versus Ti grade 23 annealed, the mechanical properties of Ti6Al4V are comparable to wrought titanium for tensile strength, elongation, and hardness.
Primary Benefits
- High stiffness and strength to relative weight
- High temperature and corrosion resistance
Maraging Steel
expand_less expand_moreMaraging Steel 1.2709 is a pre-alloyed ultra high strength steel in fine powder form. Its composition corresponds to US classification 18% Ni Maraging 300, European 1.2709 and German X3NiCoMoTi 18-9-5. This kind of steel is characterized by having very good mechanical properties, and being easily heat-treatable using a simple thermal age-hardening process to obtain.
Primary Benefits
• High strength
• High hardness
• Good High-temperature resistance
Compare Material Properties
Materials | Resolution | Condition | Ultimate Tensile Strength (MPa) |
Yield Stress (MPa) |
Elongation (%) |
Hardness |
---|---|---|---|---|---|---|
Stainless Steel |
20/50 μm | As Built | 570 MPa +/- 30 MPa | 470 MPa +/- 30 MPa | 40 +/- 5% | 85m+/- 5 HRB |
20/50 μm | Heat Treated | 570 MPa +/- 30 MPa | 33 +/- 5 MPa | 35 +/- 5% | 85 +/- 5 HRB | |
Aluminium (AlSi10Mg) | 30/60 μm | As Built | 360 MPa +/- 30 MPa | 240 MPa +/- 30 MPa | 6 +/- 5% | 120 +/- 5 HBW |
30/60 μm | Heat Treated | >267 MPa | >200 MPa | 10 +/- 2% | - | |
Inconel 718 | 50/60 μm | As Built | 960 MPa +/- 50 MPa | 600 MPa +/- 50 MPa | 30 +/- 5% | Ca. 30 HRC |
50/60 μm | Annealed | 980 MPa +/- 50 MPa | 630 MPa +/- 50 MPa | 30 +/- 5% | Ca. 30 HRC | |
50/60 μm | Annealed & Age Hardened | >1240 MPa | > 940 MPa | 12% | Ca. 47 HRC | |
Titanium (Ti6Al4V) |
20/30/60 μm | As Built | 1200 MPa +/- 50 MPa | 1050 MPa +/- 50 MPa | 8 +/- 2% | 33 +/2 HBW |
20/30/60 μm | Heat Treated | > 930 MPa | > 860 Mpa | >10% | 33 +/-2 HBW |
These figures are approximate and dependent on a number of factors, including but not limited to, machine and process parameters. The information provided is therefore not binding and not deemed to be certified. When performance is critical, also consider independent lab testing of additive materials or final parts.

Surface Finishes
Read our guide to 3D printing surface finishes. This guide will give you a quick look at the finishing options available at Protolabs.
Learn MoreLooking for an additive manufacturing solution for production projects? With our metal 3D printing technology, you’re able to choose from several secondary processes like post-process machining, tapping, reaming, and heat treatments that produce end-use production parts. To ensure high-quality parts, we also offer powder analysis, material traceability, process validation, and inspection reporting, and our direct metal laser sintering (DMLS) 3D printing process is ISO 9001 and ISO 13485 (through Protolabs Network). It’s industrial 3D printing designed around your project needs—whether prototyping or production.
1. Expertise
Consultative quoting and design feedback from our experienced engineering team and reliability from a manufacturer that has 3D printed millions of unique geometries over the last two decades.
2. Project Management
Dedicated project management support for all of your production needs from part design to finishing processes.
3. Scale
More than 100 industrial-grade metal and polymer 3D printers across five additive manufacturing technologies supporting production projects in various engineering-grade materials.
4. Quality
Rigorous process controls and engineering staff focused on achieving parts with tight tolerances, dimensional accuracy, and robust mechanical properties.
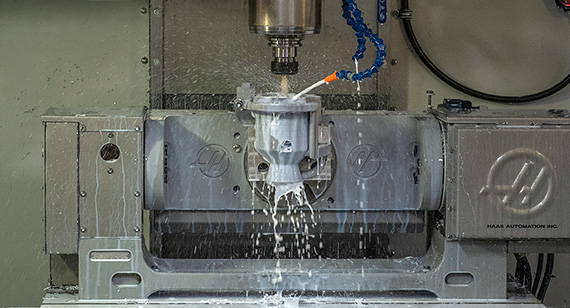
Achieve tight tolerances while having the design freedom of additive manufacturing.
- 3- and 5-axis milling
- Turning
- Wire EDM
- Tapping
Powder Analysis & Material Traceability
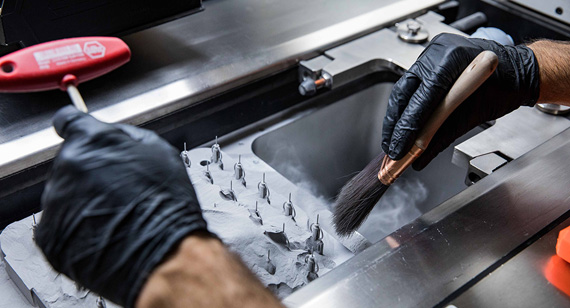
Analysis of powder and traceability of the supplier to meet your production requirements.
- Traceability
- Chemistry
- Particle size and distribution analysis
Mechanical Testing

Certified testing to confirm mechanical requirements on production parts.
- Tensile
- Hardness Testing
- Fatigue
- Vibration
Heat treatments
Specialised heat treatment processes improve the mechanical properties of parts by relieving internal stresses that develop during the sintering process.
• Stress relief
• Hot isostatic pressing (HIP)
• Solution annealing
• Aging
Quality Inspections & Reports
Validate part geometry and evaluate material structure for quality reporting.
• Dimensional inspections with report
• First article inspection (FAI)
• CMM, optical, and CT scanning
• X-ray
• Surface roughness and porosity analysis
• Certificate of compliance with parts tracking
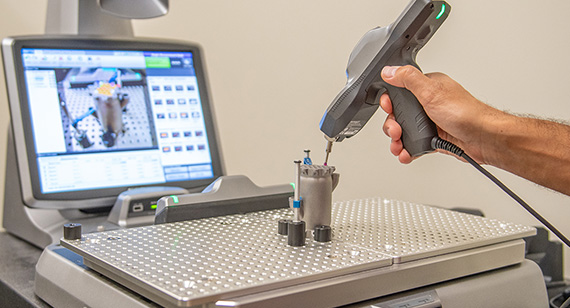
Why use Direct Metal Laser Sintering?
DMLS materials are generally accepted to be equal or better than those of wrought materials. DMLS is also ideal when the geometry or structure of the part is not possible in any other process (for weight saving designs using honeycomb or latice structures for example). Protolabs can also produce parts for implant medical applications. We also offer a number of secondary services such as painting, post machining and measurement and inspection, to further enhance the finish of your 3D-printed project design.
Get a QuoteResources
