
Plastic Injection Moulding Services
Get custom moulded plastic parts within days. Request an instant online quote with free DFM analysis through our secure file upload system
Moulds from £995
shield_locked All Uploads are Secure and Confidential
Certifications ISO 9001:2015 | ISO ISO 14001:2015 | Critical to Quality Inspections
Jump to Section
→ Capabilities
→ Materials
→ Surface Finishes
→ Quality Inspections
→ Finishing Options
→ About Plastic Injection Moulding
Leverage one of our plastic injection moulding processes in order to produce custom prototypes and end-use production parts in as fast as 1 day. We produce and use aluminium moulds because they offer cost-efficient tooling and reduced lead times. What's more, with over 200 different thermoplastic resins in stock, you are not limited on choice.
Common applications for plastic injection moulding services:
- low-volume production
- bridge tooling
- pilot runs
- functional testing and prototyping
Design Guidelines: Plastic Injection Moulding
Our innovative operating model enables us to handle a wide range of variables, meaning we can quote in a number of ways. Plus, with our Digital Network, we’re equipped to take on more projects than ever. Simply upload your CAD file for a rapid assessment, and let us take care of the rest.
To discuss with an applications engineer, please book a meeting.
Protolabs can maintain a machining tolerance of +/- 0.08mm. Depending on the material selected the resin tolerance can be as accurate as 0.002mm/mm. The resin tolerances of all thermoplastic materials are now visible on your quotes.
If your part is outside of these listed tolerances, please contact us direct to discuss how we can help applicationengineers@protolabs.co.uk
Vertical Faces |
0.5° |
---|---|
Most Situations |
2° |
Minimum for Shut Off | 3° |
Minimum for Light Texture (PM-T1) | 3° |
Minimum for Medium Texture (PM-T2) | 5°+ |
Read our design tip on Draft
Maximum Side Core Dimensions
Width | Height |
Pull |
---|---|---|
450mm | < 150mm | < 200mm |
Read our design tip on Undercuts
Material |
Recommended Wall Thickness |
---|---|
ABS |
1.143mm - 3.556mm |
Acetal |
0.762mm - 3.048mm |
Acrylic | 0.635mm - 12.7mm |
Liquid Crystal Polymer | 0.762mm - 3.048mm |
Long-Fiber Reinforced Plastics | 1.905m - 25.4mm |
Nylon | 0.762mm - 2.921mm |
Polycarbonate | 1.016mm - 3.81mm |
Polyester | 0.635mm - 3.175mm |
Polyethylene | 0.762mm - 5.08mm |
Polyphenylene Sulfide | 0.508mm - 4.572mm |
Polypropylene | 0.635mm - 3.81mm |
Polystynene | 0.889mm - 3.81mm |
Polyurethane | 2.032mm - 19.05mm |
* The table is adapted from manufacturingcenter.com.
Some edges of parts have a radius instead of a sharp edge because we use an automated CNC milling process to create the mold for your parts. This usually does not require any changes to your design, but the resulting radii are identified before the shape is milled.
Grab a Design Cube
Want to learn more about injection moulding and design better parts? Request a free Design Cube today. This physical aid is exclusive to Protolabs and will help you understand the proper design and implementation of common features on moulded parts.

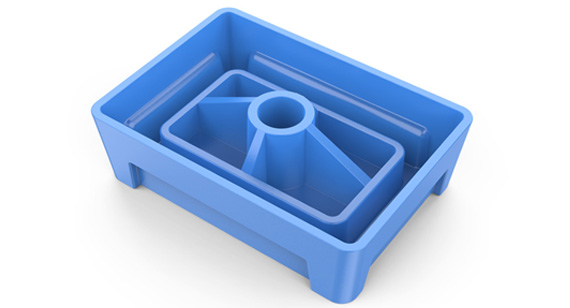
Thermoplastic Materials
We have a wide selection of more than 100 thermoplastic and thermoset materials. And if you're looking for alternative material options, check out our guide to resin substitutes for ABS, PC, PP, and other commonly moulded plastics.
- ABS
- ABS/PC
- Acetal
- Acetal Homopolymer/Delrin
- HDPE
- LDPE
- Nylon
- PBT
- PEEK
- PEI
- PMMA (Acrylic, Plexiglas)
- Polycarbonate
- Polypropylene
- PS
- PPS
- TPC-ET
- TPE
- TPU
- TPV

Are Recycled Injection Moulding Materials Right for you? Comparing recycled thermoplastics with traditional thermoplastics for injection Moulding.
In today’s world, where sustainability is a pressing global concern, the need for greener manufacturing practices has never been more crucial. In this blog we delve into the realm of recycled materials for injection moulding and explore their potential to replace their traditional counterparts.
We compare characteristics such as heat deflection, shrinkage, yield strength, and more.
Surface Finish Options
Draft angle requirements will vary by requested finish. Industry standard Mold-Tech finishes are also available.
Finish | Description |
---|---|
PM-F0 | non-cosmetic, default |
PM-F1 |
low-cosmetic, most toolmarks removed |
SPI-C1 | 600 grit stone, |
PM-T1 | SPI-C1 + light bead blast |
PM-T2 | SPI-C1 + medium bead blast |
SPI-B1 | 600 grit paper |
SPI-A2 | grade #2 diamond buff |
For more information read our design tip on surface finishes or contact your dedicated Account Manager.
Quality Inspections and Finishing Options for Custom Moulded Parts
Depending on your application's requirements, you can choose from the following when requesting an injection moulding quote.
Quality Inspections available for on-demand manufacturing orders
- Designing for Manufacturability Feedback (DFM)
- Scientific moulding process development report
- In-process CMM inspection and machine monitoring
- First article inspection (FAI) and process capability report with GD&T
|
|
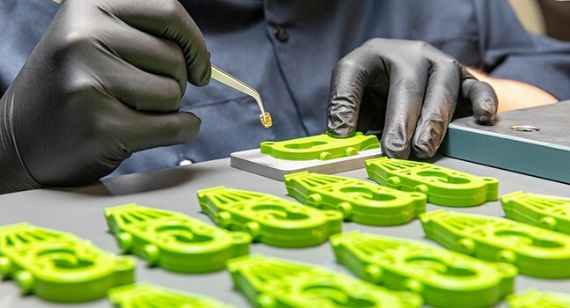

Prototyping or On-demand Manufacturing?
While the moulds themselves are similar, part quantities, lifetime maintenance, quality documentation, and pricing vary depending on which service option is chosen. The right one depends on your project needs.

Design for Mouldability Toolkit
No one ever said that designing and manufacturing moulded parts was easy. Our goal is to get you through it quickly and with quality parts. A good starting point is our Design for Mouldability Toolkit.
Check out Toolkit
About Plastic Injection Moulding Services
How does the plastic injection moulding process work?
expand_less expand_moreFrom left to right, the components of a rapid injection moulding press include: ram (1), screw (2), hopper (3), barrel (4), heaters (5), materials (6), nozzle (7), mould (8), and part (9).
The thermoplastic injection moulding process at Protolabs is a standard process involving an aluminium mould. Aluminium transfers heat much more efficiently than steel, so does not require cooling channels - which means the time we save on cooling can be applied to monitoring fill pressure, cosmetic concerns and producing a quality part.
Resin pellets are loaded into a barrel where they will eventually be melted, compressed, and injected into the mould’s runner system. Hot resin is shot into the mould cavity through the gates and the part is moulded. Ejector pins facilitate removal of the part from the mould where it falls into a loading bin. When the run is complete, parts (or the initial sample run) are boxed and shipped shortly thereafter. Request your Free Design Cube which shows surface finishes and thick and thin finishes.
What is plastic injection moulding?
expand_less expand_morePlastic injection moulding is the process of melting plastic pellets (thermosetting/ thermoplastic polymers) that once malleable enough, are injected at pressure into a mould cavity, which fills and solidifies to produce the final product.
Why choose plastic injection moulding for your project?
expand_less expand_moreProtolabs utilise a rapid injection moulding a technology-driven process that leverages manufacturing automation. CAD models are sent directly to the production floor where mould milling begins, but in most cases, moulds are fabricated from aluminium, not steel. This allows for faster and most cost-effective tooling when compared to traditional steel moulds. We offer a number of additional secondary services to support your project.
How can I reduce mould costs?
expand_less expand_more1. Eliminate undercuts |
2. Get rid of unnecessary features |
3. Use a core cavity approach |
4. Reduce cosmetic finishes and appearances |
5. Design self-mating parts |
6. Modify and reuse moulds |
7. Pay attention to DFM analysis |
8. Use a multi-cavity or family mould |
9. Consider part size |
What is injection moulding used for?
expand_less expand_moreInjection Moulding is used to make a variety of widely used products. If you look around your desk/ home you will find a multitude of injection moulded products, from bottle tops, remote control casing, console covers, syringes and most plastic made products.
To see an example of an injection moulded part worked on by Protolabs, please view our Hager case study.
To show off some of the features our injection moulding service can offer, please click to register for your free design cube
Where can I learn more about injection moulding?
expand_less expand_moreFor more information on injection moulding, please check out our White Papers and comprehensive library of design tips
Need support in choosing materials for your project? See our whitepaper on thermoplastics Materials Matter
For tips and advice on designing for injection moulding. See our whitepapers Designing for Mouldability: Fundamental Elements and Design for Mouldability: Complex Features
and for further support with cosmetic appearance of moulded parts. See our whitepaper on Cosmetics
We also have design compilations for injection moulding and the initial design process.
How can I get a quote for injection moulding?
expand_less expand_moreProduct designers and engineers can upload a 3D CAD model online at any time to receive an interactive ProtoQuote® with free design for manufacturability (DFM) analysis and real-time pricing information within hours. The DFM analysis helps eliminate potential problems like sink, challenging undercuts or walls that are too thin or thick. Once a part design is ready and a quote approved, production begins almost immediately. Upload a part today for a ProtoQuote with design analysis.

What are the advantages and disadvantages of Injection Moulding?
Injection moulding has a number of advantages. But like any manufacturing process it does have some disadvantages and if these prove important then you may be better exploring alternative technologies such as 3D printing or CNC machining.
Here we will take you through the main advantages and explore when it may be better for you to consider another option.
Watch: Injection Moulding
Rapid injection moulding works best for on-demand production, bridge tooling, pilot runs, and functional prototyping. Our affordable aluminium moulds and quick turnaround times help reduce design risks and limit overall production costs.
Three Types of Moulding
Manufacturing has experienced radical change over the years, but one of the few constants has been the prevalence of injection moulding as the most common process within the sector. But what makes injection moulding so compelling to design engineers around the world?
Resources
