Guía sobre el moldeo por inyección para principiantes
Conoce los conceptos básicos del proceso de moldeo por inyección, incluido: funcionamiento, principios de diseño, materiales y sistemas de calidad
¿Qué es el moldeo por inyección?
El moldeo por inyección es un proceso diseñado para fabricar grandes tiradas de piezas. En comparación con otras tecnologías de fabricación, como el mecanizado CNC y la impresión 3D, requiere una inversión inicial de capital en herramientas. Sin embargo, el precio de cada pieza será mucho inferior al de otros medios de fabricación de piezas de plástico. Esta estructura de costes la convierte en una solución asequible para tiradas de producción.
Se utiliza sobre todo para la fabricación de piezas de plástico a gran escala por su escaso desperdicio de material y su bajo coste por pieza. Es un proceso de fabricación ideal para sectores como el de dispositivos médicos, productos de consumo y piezas de automóvil.
¿Cómo funciona el moldeo por inyección?
Fabricación de has herramientas: una vez finalizado un diseño de moldeo por inyección, el primer paso del proceso de fabricación es fresar las herramientas, que suelen fabricarse en acero o aluminio. En la mayoría de los casos, el bloque metálico del material se coloca en una fresadora CNC que, a continuación, talla un negativo de la pieza de plástico final. A continuación pueden aplicarse tratamientos adicionales, como el pulido o el grabado láser, para conseguir acabados de superficie específicos.
Producción de la pieza: la producción real de las piezas de plástico comienza con la carga de granulados de resina en un barril. La temperatura del barril se aumenta hasta que los granulados de resina se funden y luego se comprimen. A continuación, el plástico fundido se inyecta en la herramienta metálica a través de un sistema de canal de colada, que luego se introduce en la cavidad del molde a través de unas boquillas. Después, la pieza se enfría, se solidifica y se expulsa de la herramienta mediante extractores.
Tipos de moldeo por inyección
El término moldeo por inyección engloba una serie de procesos que inyectan resina líquida en una herramienta para formar piezas de plástico. Estos son los cuatro tipos habituales:
Moldeo por inyección de termoplástico: el moldeo por inyección de termoplástico es el tipo de moldeo más habitual. Se inyecta resina termoplástica en el molde, donde el material se enfría para formar la pieza final.
Moldeo con silicona líquida (LSR): en el moldeo con silicona líquida (LSR) se utilizan materiales termoestables y la pieza de plástico se crea mediante una reacción química.
Sobremoldeo: el sobremoldeo es un proceso que se utiliza para fabricar piezas de plástico con dos o más materiales. Suele encontrarse en piezas para mejorar el agarre añadiendo silicona al asa.
Moldeo por inserción: el moldeo por inserción es un proceso que comienza colocando un componente de inserción en el molde antes de que entre la resina. A continuación, el material se inyecta y fluye alrededor del inserto, normalmente metálico, para formar la pieza final. Se suele utilizar para piezas que requieren roscados metálicos.
Principios básicos de diseño para el moldeo por inyección
Tolerancias
Con nuestro proceso de moldeo por inyección, podemos mantener una precisión de mecanizado de ±0,08 mm. La tolerancia de encogimiento depende principalmente del diseño de la pieza y de la elección de la resina. Dependiendo del material seleccionado, la tolerancia de la resina puede tener una precisión de 0,002 mm/mm. (Puedes ver las tolerancias de resina de todos los materiales termoplásticos en el presupuesto).
Espesor de pared
El espesor de pared es importante porque puede provocar defectos como rechupes y alabeos. La práctica recomendada consiste en mantener un espesor uniforme en toda la pieza moldeada por inyección. Recomendamos que el espesor de las paredes no sea inferior al 40-60% del espesor de la pared adyacente, y todas deben ajustarse a los márgenes de espesor recomendados para la resina seleccionada.
Geometría del núcleo
Vacía el interior de las piezas para eliminar paredes gruesas. Se obtiene la misma funcionalidad en una buena pieza moldeada. Un espesor innecesario puede alterar las dimensiones de la pieza, reducir su resistencia y hacer necesario un mecanizado posterior.
Ángulo de desmoldeo
Aplicar un ángulo de desmoldeo a las piezas moldeadas es fundamental para garantizar que no se deformen durante el proceso de enfriamiento y ayuda a que la pieza se pueda expulsar fácilmente del molde. La aplicación de 1 a 2 grados funciona bien en la mayoría de los casos. Si hay caras verticales, aconsejamos añadir 0,5 grados de ángulo de desmoldeo.
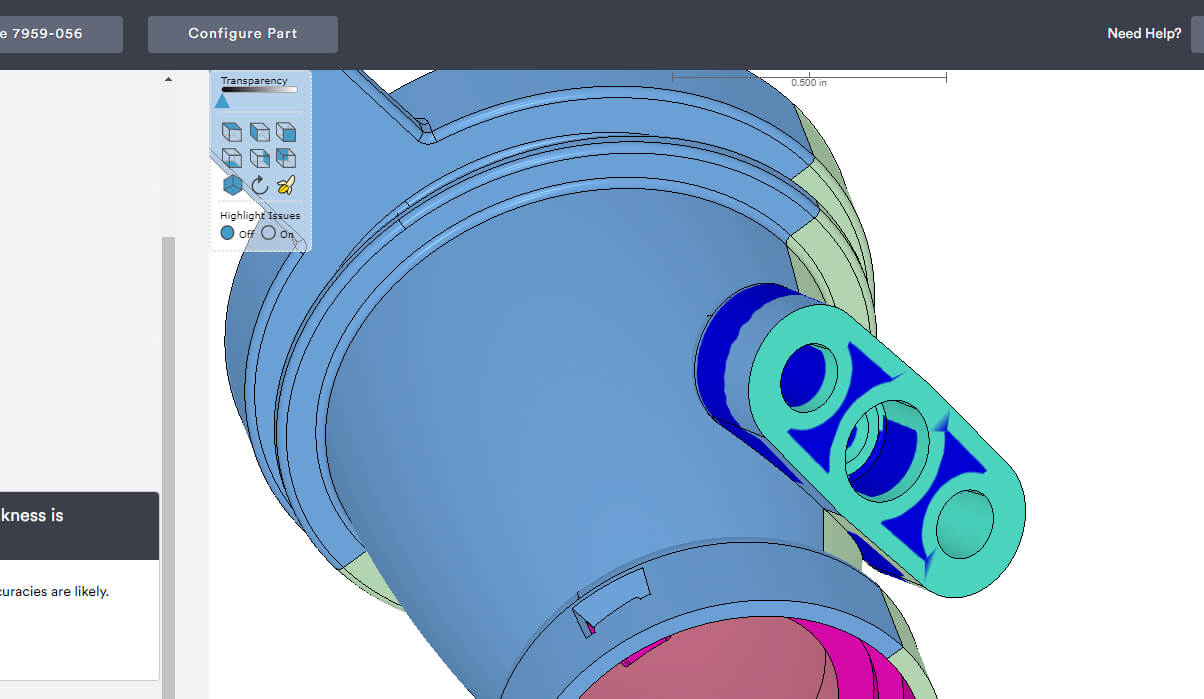

Acciones laterales
Parte del molde que encaja en su sitio cuando se cierra, mediante una corredera. Normalmente, las acciones laterales se utilizan para solucionar un negativo o, a veces, para permitir una pared exterior sin ángulo de desmoldeo. Al abrirse el molde, la acción lateral lo aleja de la pieza, lo que permite su expulsión. También se llama "corredera".
Negativos
Una parte de la pieza que proyecta sombra a otra parte de la pieza, creando un encajable entre la pieza y una o ambas mitades del molde. Un ejemplo es un orificio perpendicular a la dirección de apertura del molde perforado en el lateral de una pieza. Un negativo impide la expulsión de la pieza, la apertura del molde o ambas cosas.
Salientes
Elemento de espárrago elevado que se utiliza para enganchar elementos de fijación o de soporte de otras piezas que pasan a través de ellos. Puede haber una tendencia a diseñar salientes gruesos, lo que aumentará la probabilidad de rechupes y vacíos en una pieza. Piensa en reforzar los salientes con nervaduras o chapas de refuerzo para aumentar la resistencia.
Boquillas
Una boquilla es una abertura en la máquina de moldeo por inyección que permite que la resina entre y llene la cavidad. Existen tres tipos comunes de boquillas para el moldeo por inyección.
- Las boquillas de inyección son las más habituales, ya que funcionan bien con aditivos y es la opción más rentable.
- La boquilla de canal caliente es la mejor para piezas en las que el aspecto estético es una prioridad. Estas boquillas también pueden reducir el desgaste de las herramientas y las rebabas.
- Las boquillas capilares, guía o submarinas son ideales para piezas estéticas que no requieren un vestigio. A veces no es una opción, según el material y la geometría.
Nervaduras
Una nervadura es un elemento delgado en forma de pared paralelo a la dirección de apertura del molde, que se utiliza para añadir resistencia y apoyo a elementos como salientes y paredes. Para evitar rechupes, las nervaduras no deben superar el 60% del espesor de la pared.
Extractores
Los extractores se instalan en la cara B del molde y ayudan a liberar la pieza de plástico de la herramienta cuando se ha enfriado lo suficiente. Diseñar con suficiente ángulo de desmoldeo puede ayudar a reducir la necesidad de extractores en una pieza.
Logotipos y texto
Las fuentes Sans serif serán las más fáciles de fresar en un molde con texto. Recomendamos una fuente superior a 20 puntos y con una profundidad de entre 0,25 mm y 0,38 mm.


Kit de diseño para la moldeabilidad
Nadie dijo que diseñar y fabricar piezas moldeadas fuera fácil. Nuestro objetivo es que puedas hacerlo rápido y con piezas de calidad. Un buen punto de partida es nuestro kit de diseño para la moldeabilidad.
Leer el kitResinas para el moldeo por inyección
A la hora de elegir un material para tu pieza, algunas de las propiedades que debes tener en cuenta son la resistencia mecánica, física, química, térmica, eléctrica, inflamabilidad o a los rayos UV. Los fabricantes de resinas y de compuestos, y los buscadores independientes de resinas disponen de datos en línea. A continuación te ofrecemos una breve descripción de algunas resinas básicas y técnicas comunes.
Resinas técnicas comunes
ABS: el ABS es una gran elección para la mayoría de las piezas. Tiene un precio razonable, es fuerte, relativamente resistente, tiene un aspecto decente y es maleable incluso si no se siguen todas las reglas de diseño estándar para las piezas de plástico.
Acetal: un material resistente con buena lubricidad
LCP: un material muy resistente que fluye bien, especialmente para piezas finas. Produce líneas de punto finas.
Nailon: coste asequible, fuerte y resistente al desgaste. Pueden encogerse y deformarse, sobre todo el nailon relleno de vidrio.
Policarbonato (PC): puede tolerar temperaturas más altas y es más duradero que un ABS típico, pero menos tolerante en cuanto a moldeabilidad.
PMMA (acrílico): una opción asequible para piezas transparentes, aunque puede ser quebradizo.
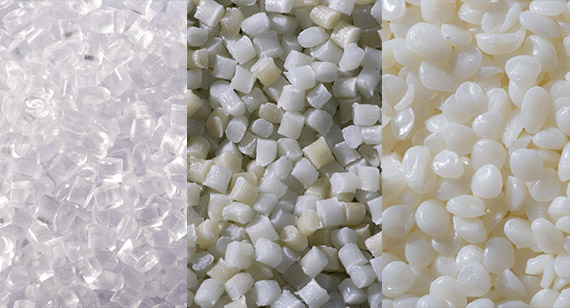
Commodity Resins
Polipropileno (PP): es un material barato y bueno cuando la estética y la rigidez no son una prioridad. Con resistencia química y buena opción para diseños de bisagras flexibles.
Polietileno: opciones de alta y baja densidad. Es duradero y con resistencia química.
Poliestireno: un termoplástico duro, barato y transparente.
Consulta nuestra guía de materiales para el moldeo por inyección si quieres obtener más información sobre la selección de plásticos.
Aditivos de colorantes y resinas para el moldeo por inyección
Los colores de resina que suelen tener los proveedores son el negro y el natural. El natural puede ser blanco, beige, ámbar u otro color. Se pueden crear colores semipersonalizados añadiendo granulados de colorante a las resinas naturales. Los colores de nuestro inventario no tienen coste adicional. Puede que no coincidan exactamente y que creen vetas o remolinos en las piezas.
Aditivos de resinas
Las fibras de vidrio cortas se utilizan para reforzar un compuesto y reducir la fluencia, especialmente a altas temperaturas. Hacen que la resina sea más resistente, más rígida y más quebradiza. Pueden provocar alabeo debido a la diferencia de encogimiento por enfriamiento entre la resina y las fibras.
La fibra de carbono se utiliza para reforzar y/o dar rigidez a un compuesto y también para contribuir a la disipación estática. Tiene las mismas limitaciones que las fibras de vidrio. La fibra de carbono puede hacer que el plástico sea muy rígido.
Algunos minerales como el talco y la arcilla se suelen utilizar como rellenos para reducir el coste o aumentar la dureza de las piezas acabadas. Como no se encogen tanto como las resinas al enfriarse, pueden reducir el alabeo.
El PTFE (teflón) y el disulfuro de molibdeno se utilizan para autolubricar piezas en aplicaciones de rodamientos.
Las fibras de vidrio largas se utilizan como las cortas para reforzar y reducir la fluencia, pero hacen que la resina sea mucho más resistente y rígida. El inconveniente es que pueden resultar especialmente difíciles de moldear en piezas con paredes finas y/o flujos de resina largos.
Las fibras de aramida (Kevlar) son como fibras de vidrio menos abrasivas, pero no tan resistentes.
Las perlas de vidrio y las escamas de mica se utilizan para dar rigidez a un compuesto y reducir el alabeo y el encogimiento. Con una carga elevada, pueden ser difíciles de inyectar.
Las fibras de acero inoxidable se utilizan para controlar las interferencias electromagnéticas y las interferencias por radiofrecuencia, normalmente en carcasas de componentes electrónicos. Son más conductoras que la fibra de carbono.
Inhibidor de rayos UV para aplicaciones de exteriores.
Los tratamientos e,státicos hacen que las resinas disipen la estática.
Acabados de superficie de las piezas moldeadas
El acabado de superficie es otro de los aspectos que se debe tener en cuenta en el moldeo por inyección, ya que las piezas suelen tener estética y normalmente están destinadas a la producción final. Ten en cuenta que una superficie texturizada requerirá más ángulo de desmoldeo que un acabado más pulido. Esto es así para que la pieza se pueda desprender del molde y para que el granallado pueda aplicarse correctamente a la herramienta.
Estas son nuestras opciones de acabado de superficie para el moldeo con termoplásticos y silicona líquida
Termoplástico | Silicona líquida (LSR) |
|
|
Además de nuestras opciones estándar de acabado de superficie, también ofrecemos acabados Mould-Tech estándares del sector para texturas más complejas. Se pueden utilizar para mejorar el agarre del asa de una pieza o para ocultar defectos estéticos como las líneas de partición. Las texturas Mould-Tech se pueden utilizar para conseguir los efectos siguientes::
- los acabados obtenidos mediante granallado o pulido de la superficie del molde;
- el veteado de tipo madera o cuero;
- las superficies esmeriladas;
- los acabados mates, brillantes o difusos; y muchos más.
Técnicas de postprocesamiento y avanzadas de moldeo
Soldadura ultrasónica: en aplicaciones de moldeo más complejas puede utilizarse la soldadura ultrasónica para fusionar las piezas.
Marcado de piezas: hay dos formas de añadir imágenes, a menudo logotipos, a las piezas: la tampografía y el grabado por láser.
La tampografía permite añadir gráficos en color a las piezas moldeadas a escala. Se puede utilizar para añadir logotipos, gráficos e instrucciones a las piezas. Ofrecemos tampografía para resinas ABS, PC y ABS/PC.
El grabado por láser utiliza un láser para grabar una imagen 2D en una pieza o cavidad de molde. Aunque el grabado por láser no dispone de la opción a color, es una forma más rentable y rápida de marcar piezas de plástico en comparación con la tampografía.
Insertos amovibles: los insertos amovibles se mecanizan por separado en la herramienta y se colocan en el molde antes de inyectar el material. Se utilizan para conseguir negativos en las superficies interiores. Los insertos amovibles se expulsan junto con la pieza de plástico y se vuelven a colocar en el molde. El uso de un inserto amovible permite adaptarse a muchas restricciones de forma y posicionamiento, pero es más costoso que los cierres deslizantes o el uso de una acción lateral.
Pines de núcleo de acero: un pin de acero es lo suficientemente resistente como para soportar la tensión de la expulsión y su superficie es lo suficientemente lisa como para desprenderse limpiamente de la pieza sin ángulo de desmoldeo. No debería haber ningún efecto estético en la pieza resultante; si lo hay, estará dentro del orificio, donde no se verá.
Sistemas de calidad del moldeo por inyección
Dado que las empresas confían en el moldeo por inyección para fabricar miles, a veces millones, de piezas, el control de calidad es fundamental.
Moldeo científico: El moldeo científico describe un proceso estándar que se utiliza para desarrollar, optimizar y documentar el proceso de configuración ideal para cada proyecto de moldeo por inyección, para que se sigan el mismo proceso y los mismos parámetros en cada tirada. De este modo se garantiza la coherencia de las piezas en cada serie.
Inspección del primer artículo (FAI): FAI es un método que se utiliza para comprobar que las piezas cumplen las especificaciones. En el método FAI adoptamos un enfoque de crítico para la calidad. Mediante el uso de GD&T, los clientes pueden señalar las dimensiones más críticas de su pieza.
Proceso de aprobación de piezas de producción (PPAP): PPAP es un proceso de inspección de calidad usado habitualmente en el sector de la automoción. Este método se usa para comprobar que el proceso de producción pueda producir con fiabilidad una pieza de calidad de manera repetida. Hay 18 componentes en una inspección PPAP, que van desde la aprobación del cliente a la producción de piezas de muestra.
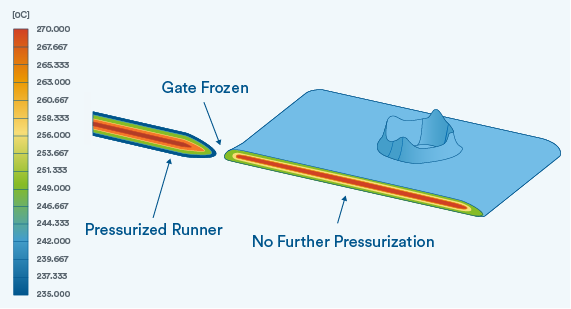