Impression 3D et injection plastique : 2 procédés au service du médical
Ce nouvel article de blog traite de l’impression 3D et du moulage par injection dans le cadre du développement de pièces destinées à l’industrie médicale.
Plusieurs technologies d’impression 3D, de nombreuses matières, voici un rapide résumé des méthodes qui peuvent vous aider à prototyper ou développer vos pièces à usage médical :
- L’état du marché médical en Europe et en France
- L’impression 3D plastique, avec les processus de stéréolithographie et de frittage de poudre
- L’impression 3D métal, ses matières et les opérations secondaires permettant d’utiliser les pièces dans un milieu médical
- L’injection plastique pour réaliser des séries de pièces en utilisant des matières biocompatibles
- Des études de cas afin d’illustrer concrètement les avantages de la fabrication additive et de l’injection plastique dans le domaine médical.
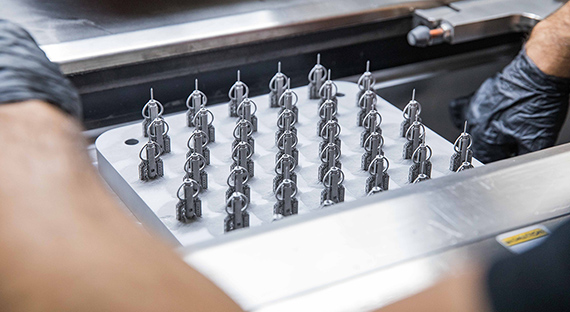
ÉTAT DU MARCHE MÉDICAL EN EUROPE
En 2021 le marché du médical en Europe représentait 150 milliards d’euros, soit 27% du marché mondial. Sans surprise, c'est le marché américain qui est le plus important dans le monde (41%)
Cela représente environs 800.000 employés et plus de 34.000 entreprises. À l’échelle de la France, cela représente 88 000 employés, pour 1440 entreprises (93% sont des PME) et la France se situe sur la deuxième marche du podium derrière l’Allemagne en termes de part de marché avec 31 Mds € en 2021.
L’IMPRESSION 3D PLASTIQUE
STÉRÉOLITHOGRAPHIE
Le procédé
La stéréolithographie est un process d’impression 3D à base de résine liquide et qui est souvent utilisé durant les phases de prototypage. La machine commence le tracé, les couches des supports, puis celui de la pièce elle-même, à l'aide d'un rayon laser ultraviolet dirigé sur la surface d'une matière thermodurcissable liquide. Lorsque la couche est numérisée sur la surface de la matière, la plateforme de fabrication est abaissée et une barre de ré-enduisage se déplace le long de la plateforme afin d'appliquer la couche de matière suivante. Ce processus est répété couche par couche, jusqu'à ce que la fabrication soit terminée.
Une fois la pièce produite, celle-ci est retirée de la machine et rincées avec des solvants dans le but d'enlever toute matière excédentaire. Lorsque les pièces sont complètement propres, les supports sont retirés à la main. À partir de ce stade, les pièces sont soumises à un cycle de durcissement aux rayons ultraviolets afin de solidifier entièrement leur surface externe.
La dernière étape du processus de stéréolithographie concerne l'application d’options secondaires souhaitées par le client. Les pièces réalisées par stéréolithographie doivent être utilisées dans un environnement où l'exposition aux rayons UV et à l'humidité est minime afin qu'elles ne se dégradent pas, car ce ne sont pas des vraies matières, mais des résines époxy ou acrylate.
LES MATIÈRES

MICROFINE
Développée par et pour Protolabs. Cette résine permet d’imprimer des pièces de tailles extrêmement petites
La microfine green permet la réalisation de pièce de très haute précision, avec une rigidité comparable à celle de l’ABS.
Cette matière est imprimée avec des épaisseurs de couches de 25 microns et permet d’obtenir une finition lisse et des détails très fins.
Les dimensions maximales des pièces réalisées avec cette matière sont de 25mm3.
L’utilisation de cette matière vert vif pour créer des structures microscopiques rend possible toute une série d’applications, qui n’étaient pas envisageables auparavant pour l’impression 3D médicale. Des pièces détachées des stimulateurs cardiaques, dont la taille ne dépasse pas une fraction de millimètre, sont tout aussi réalisables que des cathéters miniaturisés.
LE FRITTAGE DE POUDRE PLASTIQUE - SLS et MJF
SLS - Selective Laser Sistering
Le SLS est un process d’impression 3D plastique à base de poudre. La machine commence le tracé de la pièce à l’aide d’un laser dirigé sur la surface de la poudre. Une fois que la première couche a été fusionnée, un rouleau se déplace pour distribuer la prochaine couche de poudre. Ce processus est répété là aussi en couche par couche, jusqu'à ce que la fabrication soit terminée.
Lorsque la fabrication est finie, l’opérateur va extraire les pièces du lit de poudre. Un brossage initial est effectué à la main afin de retirer une grande partie des particules de poudre en excès. Les pièces sont ensuite soumises à une procédure de microbillage dans le but de retirer toute trace de poudre résiduelle avant d'arriver au service de finition.
Le SLS est idéal pour fabriquer des pièces fonctionnelles nécessitant une plus grande robustesse et une meilleure résistance aux chocs que les pièces produites par stéréolithographie. En effet, les matières utilisées en SLS sont de vrais thermoplastiques comme des Nylons et TPU. Cependant, le SLS n'offre pas la finition de surface et les détails fins disponibles avec la Stéréolithographie.
Le MJF - Multi Jet Fusion
Le MJF est également un procédé d’impression 3D plastique à base de poudre mais le process en lui-même diffère un peu de celui du SLS :
La Multi Jet Fusion utilise une tête d'impression pour appliquer de manière sélective des agents de fusion et de détails sur un lit de poudre, fondu ensuite par des éléments de chauffe pour former une couche solide. Après chaque couche, de la poudre est rajoutée sur le lit précédent et le processus se répète jusqu’à ce que la pièce soit terminée.
Lorsque la construction s’achève, l’ensemble du lit de poudre avec les pièces encapsulées est dirigé avec une station de traitement où la plus grande partie de la poudre restante est éliminée par aspiration. Ensuite, les pièces sont sablées pour éliminer les résidus de poudre.
Le MJF possède les mêmes avantages que le SLS, mais il permet de réaliser des pièces avec une rugosité de surface plus fine et des propriétés mécaniques plus isotropes.
LES MATIÈRES

En termes de matières spécifiques à l'industrie médicale, chez Protolabs nous pouvons proposer :
En frittage de poudre plastique (SLS)
- Nylon 12 blanc biocompatible, avec une bonne résistance chimique et un excellent comportement sur le long terme.
EN ISO 10993-1 / USP VI
Il peut être utilisé pour l’impression de prothèses et sa haute résistance à l’abrasion permet de l’utiliser pour réaliser des pièces de liaison.
En Multi Jet Fusion (MJF) :
- Nylon 11 gris (exemple ici avec plusieurs niveaux de finitions), c'est également une matière biocompatible qui offre une excellente résistance chimique et une bonne flexibilité. Ce qui en fait aussi une matière de choix pour la réalisation de prothèses.
EN ISO 10993-1 / USP VI - Nylon 12 gris, robuste et présentant lui aussi une excellente résistance chimique.
EN ISO 10993-1 / USP VI
En résumé, l’un des grands avantages de l’impression 3D, c’est de pouvoir réaliser des géométries non réalisables avec les process classiques tels que l’usinage ou le moulage par injection par exemple.
La personnalisation est aussi particulièrement rapide puisqu’une seule modification du fichier 3D permet d’adapter une pièce selon le besoin, sans avoir à retoucher un moule au passage.
IMPRESSION 3D DE METAL (DMLS) - ISO 13485
Le procédé
La fabrication additive à base de poudre de métal (DMLS) est souvent utilisée dans l’industrie médicale. A noter que notre usine est certifiée ISO 13485, pour la production d’implants et d’instruments en métal.
Le DMLS est un process d’impression 3D basé sur des poudres métalliques ; il a été lancé en 1995. Le process de frittage de poudre métallique et similaire à celui de frittage de poudre plastique, à l’exception qu’en DMLS il faut prévoir l’ajout de supports de construction pour maintenir la pièce dans le lit de poudre.
La machine de DMLS commence le frittage des couches, en commençant par les supports la pièce, à l'aide d'un laser dirigé sur un lit de poudre métallique. Lorsqu'une couche est terminée, la plateforme de construction s'abaisse et un rouleau se déplace le long de la plateforme pour déposer la prochaine couche de poudre dans une chambre de fabrication inerte. Ce processus est répété une couche après l'autre, jusqu'à ce que la fabrication soit terminée.
Lorsque la fabrication est finie, un brossage initial des pièces est effectué à la main afin de retirer une grande partie des particules de poudre superflues. Ensuite, le cycle de traitement thermique approprié leur sera appliqué pendant qu'elles sont encore maintenues en place sur la plateforme de construction avec les supports afin d'atténuer toute contrainte. Les pièces sont ensuite retirées de la plateforme, puis les supports sont enlevés des pièces. La finition des pièces est alors réalisée au moyen d’une procédure de microbillage. Les pièces finales produites par DMLS ont une densité de près de 100%.

LES MATIÈRES
Le titane est biocompatible et répond à un certain nombre de normes :
- ISO 5832-3
- ASTM F1472
- ASTM B348
Il est couramment utilisé pour réaliser plusieurs types d’implants, car c’est un métal robuste et résistant avec un poids peu élevé. Il possède en outre une résistance élevée à la corrosion.
Pour la petite histoire, la pièce présentée ici a bien été utilisée en tant qu’implant crânien suite à une opération de chirurgie vasculaire sur un patient.
Le but ayant été de développer un implant avec le dégagement de chaleur le plus faible possible dans le tissu cérébral, perméable aux fluides tissulaires du cerveau et bien sûr facilement toléré par le corps humain.
Seule une structure en titane poreuse disposait des propriétés requises ; l’implant a été imprimé puis implanté au patient pendant une opération qui a duré 1h30 ; le patient a quitté la clinique 2 jours après et aucune complication n’est apparue ultérieurement.
FICHE MATIERE TITANE
Le cobalt chrome
Le Cobalt/Chrome est également utilisé pour des applications médicales. C’est un superalliage reconnu pour son excellent rapport résistance/poids.
Il présente de hautes performances en matière de résistance mécanique et de résistance à la corrosion.
Le Cobalt/Chrome est bio compatible et est en général utilisé en tant que pièces d’appui en raison de sa grande dureté.
Biocompatible et norme ASTM F75
FICHE MATIERE COBALT CHROME
Structures lattices
L'un des avantages du frittage de poudre métallique est le fait que l'on peut réaliser des structures lattices
Les structures lattices sont une combinaison d'une matière et de zones vides, assemblés d'une manière à créer des caractéristiques physiques inatteignables par un matériau seul. Grâce à leurs caractéristiques géométriques, les structures lattices peuvent être utilisées pour obtenir des pièces de faible masse et de haute résistance.
➢ Nous pouvons concevoir toutes sortes de structures lattices (taille minimale 0,2 mm d'épaisseur)
➢ Nous pouvons les imprimer et les nettoyer
De façon générale, la structure lattice sert à alléger une pièce tout en conservant une bonne résistance mécanique.
Dans le domaine médical, les structures lattices servent en plus à permettre la croissance osseuse ; chez protolabs nous sommes en mesure de définir avec vous la structure lattice qui correspond le mieux à votre besoin, de l’imprimer et de la nettoyer.
OPÉRATIONS SECONDAIRES
Pour des pièces fabriquées en DMLS, nous pouvons en plus proposer des opérations secondaires, ainsi 1 seul interlocuteur tout au long du processus.
Traitements thermiques pour durcir les pièces ou relaxer les contraintes internes,
Reprises d’usinage pour atteindre des tolérances plus fines ou tarauder des trous par exemple,
Polissage comme on peut le voir sur les deux pièces à l’écran,
Nettoyage ultrasons ou haute pression,
Conditionnement particulier que l’on peut définir avec vous comme un conditionnement sous vide par exemple,
Assemblage, quand vous faites imprimer plusieurs pièces.



TESTS ET ANALYSES
Point essentiel dans la production des pièces, pouvoir les tester et les analyser ! C'est pourquoi nous proposons de nombreux tests et analyses :
- Certificat matière
- Certificat de conformité - CoC
- Essais de traction et de dureté
- Analyse de porosité
- Rapport d'inspection du 1er article
- Tomodensitométrie
- Instructions personnalisées
- Analyses chimiques
- Analyse de la micro-structure
- Gabarits personnalisées pour tests de forme et ajustement de pièces complexes
- Revêtement de Nitrure de Titane


GUIDE DES FINITIONS IMPRESSION 3D

Finitions de surfaces pour pièces imprimées en 3D
Vous souhaitez améliorer la résistance, la transparence ou l’aspect de vos pièces imprimées en 3D ? Choisissez des matières spéciales microfluidique/microrésolution, un réusinage ou bien une finition sur mesure (peinture).
LE MOULAGE PAR INJECTION
Le processus du moulage par injection n'est plus à expliquer, mais pour en savoir plus c'est par ICI ou encore par ICI
Dans le medical, notamment pour la création de devices, de produits ne nécéssitant pas autant de personnalisation, le moulage par injection est encore et toujours LE processus le plus courrament utilisé.
Nous vous présentons aujourd'hui 4 matières particulièrements adaptées pour l'industrie du médical

PC - Makrolon 2458
Il s'agit d'une matière biocompatible et qui a été aussi développé pour résister à la stérilisation vapeur à 121°C ou à la stérilisation gaz à l’oxyde d’éthylène.
Cette matière est couramment utilisée pour l’injection de pièces en contact avec le corps humain.
FICHE MATIERE
PBT - Celanex 2401/MT
C'est une matière un peu plus technique que le PC, mais tout aussi biocompatible et qui a un avantage non négligeable par rapport au PC, c’est qu’il présente une fluidité beaucoup plus importante, donc il est intéressant pour injecter par exemple des pièces assez fines, qu’on aurait du mal à remplir avec un PC qui est une matière plus visqueuse.
FICHE MATIERE
OCP - cyclic olefine copolymer
Cette matière est un polymère amorphe qui présente une barrière à l'humidité exceptionnelle, une très bonne résistance chimique, une grande pureté et une surface non réactive, ce qui en fait un excellent choix pour les produits de santé.
C'est un substrat non polaire qui ne favorise pas l'adsorption, la dénaturation, l'agrégation ou la précipitation comme le verre par exemple.
Il est peu réactif, résistant chimiquement à l'alcool et à l'acétone.
Il est transparent comme du verre, résiste à divers types de stérilisations et ne contient pas de BPA, des phtalates ou d’halogènes.
Du point de vue des applications, il peut être utilisé pour l’administration de médicaments, pour réaliser des seringues, flacons, cartouches, bouteilles, des instruments chirurgicaux, du matériel de laboratoire ou encore être utilisé dans le domaine de l’optique.
Guide des matières Protolabs
Le silicone
Le silicone, très largement utilisé dans le domaine médical en raison de sa faible toxicité et son excellente résistance à la chaleur
Guide des matières ProtolabsIl s’agit ici d’une liste non exhaustive de matières proposées par Protolabs pour des applications médicales. Si vous avez une matière spécifique que vous souhaitez utiliser, n’hésitez pas à nous contacter, car nous sommes en mesure d’injecter d’autres grades que ceux que nous avons de base en stock.
PROTHÈSES ORTHOPÉDIQUES - Impression 3D métal (DMLS)

La prothèse a été réalisée en TPU avec le process de frittage de poudre plastique Multi Jet Fusion (MJF)
La pièce sortie d’impression est à gauche, son aspect est assez hétérogène et rugueux.
Pour améliorer le visuel et la rugosité, nous avons teint la pièce en noir et nous l’avons lissé grâce à un procédé de lissage chimique qui consiste à vaporiser un solvant chimique porté à température sur la pièce. Le Vapour smoothing.
Le solvant va permettre de combler les aspérités de surface de la pièce pour améliorer sa rugosité.
L’Impression 3D a été une évidence dans ce cas, puisque l’idée était de réaliser une prothèse qui puisse être adaptée à toutes sortes de morphologies.
Sur dernière prothèse, l'on peut voir que la technique de la structure lattice (ou nid d'abeille) a été utilisée, ce qui a impliqué moins de matière engagée que la prothèse pleine, donc moins de matière et moins de temps d’impression.
ANCILAIRE CHIRURGIE GLAUCOME - Moulage par injection - Rheon Medical

L’eyeWatch est le premier implant au monde à permettre d’ajuster la pression intra-oculaire de manière non invasive. C’est une révolution dans le traitement du glaucome.
Rhéon medical a choisi PL pour réaliser 2 pièces qui seront utilisées en tant qu’outils médicaux lors de l’implantation du dispositif médical dans l’œil.
Les deux pièces ont été injectées en Makrolon 2458, le PC biocompatible
Il y a le Tweezer qui est utilisé comme pince afin de bien tenir l’implant sans l’endommager pendant son insertion dans l’œil, et le Marker qui est un outil d’aide pour le chirurgien, qui laisse une emprunte afin de l’aider à positionner l’implant avant de le suturer.
Les moules en aluminium utilisés par Protolabs sont plus rapides à produire que les moules classiques. Ils sont proposés avec une garantie limitée (jusqu’à 2000 pièces) ou illimitée, sachant que le client propriétaire des moules peut à tout moment passer d’un niveau de garantie à l’autre. Cette offre est particulièrement intéressante pour disposer rapidement d’une ou plusieurs séries de pièces tout en se laissant la possibilité d’améliorer encore la conception.
Rheon Médical a su en profiter pour accompagner le développement de la pose des implants eyeWatch.
REDUCTION ACOUPHENES IMPRESSION 3D - FORGTIN

15% de la population est affectée par des acouphènes au moins une fois dans sa vie, et pour de nombreuses personnes qui en souffrent, l'acouphène chronique devient un compagnon familier de la vie quotidienne ; il se traduit par des sifflements ou des bourdonnements permanents, 24 heures sur 24, 7 jours sur 7.
L’inventeur autrichien Klaus Grübl a récemment développé un dispositif médical qui aide les patients grâce à l'accompagnement de Protolabs : ForgTin, une abréviation de Forget Tinnitus (oublier l'acouphène).
Du concept original au produit fini, ForgTin a fait l'objet de nombreuses évolutions en termes d'ingénierie et de conception. Il est apparu très tôt au concepteur que l'impression 3D était incontournable. ForgTin comprend des géométries complexes et doit être personnalisable et adaptable pour que toutes les personnes affectées puissent utiliser l'appareil.
Le support supérieur, imprimé en acier, en DMLS, se place sur l'oreille externe, comme des écouteurs sur des lunettes, et maintient ForgTin en place tout en couvrant l'un des points de pression. Le support supérieur est relié au support inférieur par une goupille fendue qui suit le lobe de l'oreille jusqu'au tragus face au canal auditif externe. Ici, et derrière l'oreille, deux points de pression supplémentaires combattent l'acouphène en appliquant une pression constante. Enfin, ForgTin est enrobé d'éléments en silicone, injectés, qui sont essentiels pour le confort d'utilisation.
Voilà qui achève notre tour d’horizon de ce qui existe en fabrication additive et moulage par injection chez Protolabs et au service de l'industrie médicale.
Et embarquez avec nous pour la visite de nos sites de productions.
