Accelerating Production of Industrial Equipment and Components
Meet the growing need for connected hardware while still supporting legacy equipment and machinery with custom parts
Certifications ISO 9001:2015 | ITAR
Industrial equipment and machinery manufacturers are living in two worlds these days. They are dramatically embracing digital connectivity with features like sensors and actuators that exchange critical data with other machines and computer networks. At the same time, many of these companies must also service and support a large inventory of existing equipment and machinery with elongated life cycles—products that may have been put into use decades ago. From farm machinery OEMs and industrial truck and tractor makers to manufacturers of oil field machinery and other industrial equipment, companies can advance into the digital era while not abandoning their existing equipment with the help of digital manufacturing.
Why Protolabs for Industrial Equipment and Machinery Components?
Supply Chain Diversification
Build a manufacturing safety net into your supply chain that you can turn to during line-down situations or unplanned disruptions.
On-Demand Production
Create agility in your supply chain by ordering quick-turn industrial components when needed.
Jigs and Fixtures
Streamline part assembly and help reduce production costs with durable jigs and fixtures.
Maintenance, Repair, and Operations (MRO)
Order custom production parts on demand for MRO applications to keep equipment running without delay.
Durable Materials
Choose from more than 40 different metal alloys and hundreds of industrial-grade plastic and elastomeric materials, like silicone rubber and TPU for highly durable seals, gaskets, and other internal components.

Speeding Up Braking for Jacobs Vehicle Systems
Without engine braking, trucking as we know it would be impossible. When not using the accelerator, engine brakes use the power of an engine to slow down trucks - a mission-critical element of modern trucking. They do that in tandem with physical brakes. But not all brakes are the same, mostly due to space considerations in different trucks - it's never one-size-fits-all proposition. Because of this, Connecticut-based Jacobs Vehicle Systems turned to Protolabs to develop multiple prototypes with different form factors, then carry those through to the production phase.
What Materials Work Best for Industrial Applications

Steel and Stainless Steel. It’s strong, machinable, and relatively low in cost. Oil and gas fields, for example, often favor stainless steel for its corrosion resistance. Superalloys such as 3D-printed Inconel are an alternative for demanding applications.
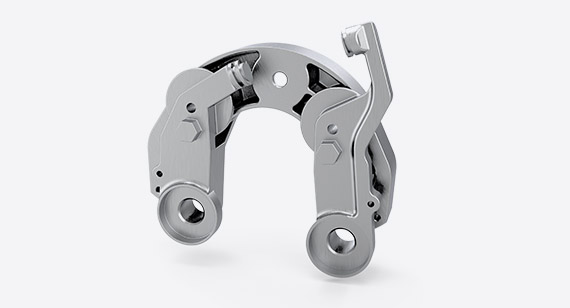
Aluminum. Though there is less concern with the component weight of industrial equipment and machinery, aluminum is often a metal of choice because of its excellent machinability and lower overall manufacturing cost.

Thermosets and Thermoplastics. Liquid silicone rubber and other elastomers are widely used for applications requiring fuel-resistant parts while high-performance thermoplastics such as PEEK and PEI (Ultem) can serve as stand-ins for metal in some situations.

Commodity Plastics. As companies retrofit existing equipment with computer electronics to meet connectivity demands, a large range of versatile and affordable thermoplastics can be leveraged.

Common Applications
We have several capabilities within our services and processes ideal for industrial. A few common applications include:
- Machine and tool parts
- Jigs and fixtures
- Electronic housings
- Pumps and accessories
- Oil and gas extraction equipment
- General industrial machinery
- Conveyors and conveying equipment
- Parts for tractors, bulldozers, forklifts, and other heavy construction and individual vehicles and equipment
Related Resources