Progettazione per la Realizzabilità:
Volume 1: Guida di riferimento rapido sullo Stampaggio a Iniezione rapida per tecnici e progettisti
La progettazione di pezzi in plastica che tenga conto della stampabilità è sempre stata una considerazione importante per i tradizionali processi di stampaggio a iniezione, ma è particolarmente utile durante lo stampaggio rapido a iniezione per garantire velocità e qualità costanti durante la produzione. Questo White paper esamina molti aspetti importanti della progettazione da tenere in considerazione durante la progettazione e la produzione dei pezzi stampati a iniezione.
- Descrizione dello stampaggio a iniezione
- Applicazioni per lo stampaggio a iniezione rapida
- Spessore delle pareti
- Geometria a nucleo
- Spessore consigliato delle pareti
- Deformazioni
- Angoli vivi
- Nervature
- Borchie
- Angola di spoglia
- Nucleo-impronta
- Impatto profondo (Fresatura)
- Struttura
- Stampo scorrevole
- Azionamenti laterali
- Estratore
- Pick-out
- Perni in acciao
- Testo
- Accesso a linguetta
- Pezzi autocombacianti
- Tolleranza
- Scelta del materiale
- Scelta dei colori
- Additivi per resina
Che cos'è lo stampaggio rapido a iniezione?
Lo stampaggio rapido a iniezione è un processo guidato dalla tecnologia che fa leva sull'automazione della produzione. I modelli CAD vengono inviati direttamente al reparto di produzione dove inizia la fresatura degli stampi. In molti casi, questi sono fabbricati in alluminio e non in acciaio. Ciò permette di ottenere utensili in modo più veloce e più efficace dal punto di vista economico rispetto ai tradizionali stampi in acciaio.
Sono disponibili diverse opzioni di finitura di superficie e le capacità di produzione includono inserti ad azionamento laterale e a caricamento manuale così come il semplice sovra stampaggio e il costampaggio. L'uso selettivo dell'elettroerosione, o EDM, viene applicato per migliorare caratteristiche dello stampo quali angoli e spigoli. Il risultato è la produzione di pezzi in poche settimane rispetto ai diversi mesi necessari per i metodi tradizionali di stampaggio a iniezione.
Ecco alcune applicazioni adatte allo stampaggio rapido a iniezione e alcuni settori che si avvalgono a loro vantaggio della tecnologia:
Applicazioni
- Prototipi. Perfezionamento del progetto con veri pezzi stampati a iniezione
- Test funzionali nel ciclo di sviluppo del prodotto
- Possibilità di testare su più materiali per lo stesso particolare
- Possibilità di testare molteplici versioni dello stesso pezzo potendo iterare velocemente il progetto
- Utensileria di raccordo
- Produzioni in volumi medio-bassi
- Da 25 a 10,000 pezzi stampati
- Arresto della linea di produzione
- Progetti di sviluppo intensivi
Settori
- Medico
- Automobilistico
- Elettronico
- Aerospaziale
- Prodotti di consumo
- Elettrodomestici
- Illuminazione
- Marino
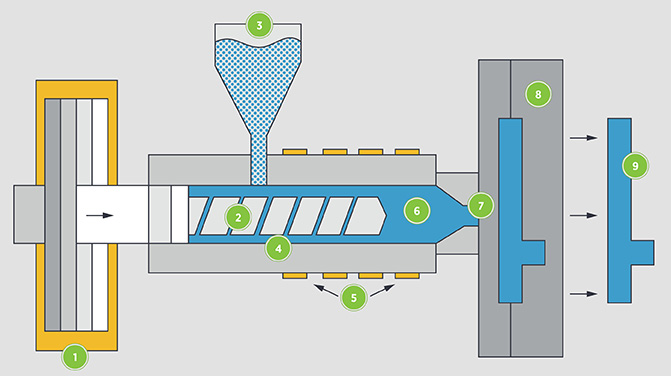
Da sinistra a destra: Pistone (1), Vite (2), Tramoggia (3), Cilindro (4), Riscaldatori (5), Materiale (6), Ugello (7), Stampo (8), Pezzo (9).

Un problema di spessore (delle pareti)
Il requisito progettuale più importante per ottenere pezzi stampati di buona qualità consiste nel mantenere pareti di spessore costante.
Suggerimento: un buon progetto per pezzi stampati a iniezione prevede pareti di spessore uniforme per ridurre al minimo il rischio di deformazione o distorsione dei pezzi.
Il nucleo della questione
Eliminando le pareti spesse si ottiene il nucleo del pezzo. La funzionalità rimane invariata in un pezzo correttamente stampato.
Suggerimento: pareti inutilmente spesse possono alterare le dimensioni del pezzo, indebolirne la struttura e richiedere una lavorazione a macchina post-produzione.

Verso l'assoluto
Spessore assoluto delle pareti consigliato a seconda del tipo di resina.
Resina | Spessore delle pareti consigliato (in mm) |
---|---|
ABS | 1.14 - 3.50 |
Acetale | 0.64 - 3.05 |
Acrilico | 0.64 - 3.81 |
Polimero liquido cristallizzato | 0.76 -3.05 |
Plastici rinforzati a fibra lunga | 1.90- 2.54 |
PA (Nylon) | 0.76 - 2.92 |
Policarbonato | 0.11 - 3.810 |
Poliestere | 0.64 - 3.17 |
Polietilene | 0.76 - 5.08 |
Solfuro di polifenile | 0.51- 4.57 |
Polipropilene | 0.64 - 3.81 |
Polistirene | 0.89 - 3.81 |
Nota: le indicazioni qui fornite sono linee guida generali e sono subordinate alla geometria del pezzo e alla struttura stampata. Si sconsiglia di prevedere pareti di spessore minimo nella progettazione di pezzi di grandi dimensioni.
Suggerimento: La regola generale di Protolabs per lo spessore delle pareti è 1mm – 3.5mm.
Una personalità deformata
Eliminare transizioni a spigoli vivi che per natura comportano sollecitazioni.
Progettare strutture 3D autosupportanti.
L’eliminazione delle sollecitazioni
Gli angoli vivi sono sinonimo di pezzi deboli.
- Sono per natura fonte di sollecitazioni derivanti dal flusso di resina.
- Creano concentrazioni di carico nell’applicazione.

Le borchie sottili vanno di moda
- Evitare la creazione di sezioni spesse con le borchie per viti.
- Le sezioni spesse possono causare vuoti e depressioni nel pezzo.

Nucleo-impronta
A livello di progettazione, se possibile è preferibile utilizzare la combinazione nucleoimpronta al posto delle nervature, poiché consente di ottenere pareti di spessore costante piuttosto che pareti con una base spessa. Facilita inoltre la creazione di stampi con una finitura di superficie migliore e la consegna di pezzi di maggiore qualità a velocità più elevata.
Suggerimento: questa opzione risulta più rapida e più economica da produrre.



Nervature adeguate
Per impedire la formazione di depressioni, le nervature non dovrebbero superare il 60% dello spessore della parete.
Suggerimento: se Protolabs richiede di aumentare lo spessore di una nervatura che è già il 40-60% della parete, è opportuno prevedere un aumento proporzionale dello spessore della parete per ridurre il rischio di depressioni.

Spogliatevi
L’uso dell’angolo di spoglia (l’inclinazione delle pareti verticali) ovunque sia possibile è vivamente consigliato, poiché facilita l’espulsione dei pezzi senza impronte di tiratura o fori prodotti dalle punte degli espulsori. I pezzi risultano migliori e vengono prodotti più velocemente.

Impatto profondo (fresatura)
Dotate il pezzo di angoli di spoglia ovunque sia possibile. In questo modo potremo creare particolari più profondi. La spoglia ci consente di ridurre le vibrazioni e i difetti estetici durante la fresatura di pareti profonde. Se possibile, utilizzate una spoglia di 1° o più. In progetti nucleo-impronta, cercate di utilizzare 2° o più. Una regola pratica abbastanza approssimativa suggerisce 1° grado di spoglia ogni 50 mm di profondità. A partire da profondità comprese tra i 50 e 101 mm potrebbero essere richiesti 3° gradi di spoglia o uno spessore minimo di 3 mm.
Struttura
Protolabs può effettuare la perlatura dello stampo usato per i pezzi. Una perlatura leggera richiede una spoglia minima di 3° su pareti verticali, mentre per una perlatura sono richiesti 5°.



Estrazione diretta
Gli elementi scorrevoli sono una scelta ideale e possono essere creati in uno stampo a estrazione diretta. Richiedono un angolo di spoglia di 3°, ma consentono di ottenere un notevole risparmio di tempo e denaro sugli azionamenti laterali.
Azionamenti laterali
Gli azionamenti laterali possono formare sottoquadri sull’esterno del pezzo. I sottoquadri devono trovarsi in corrispondenza della linea di giunzione o collegati ad essa ed essere sullo stesso piano della linea di giunzione. Protolabs è in grado di produrre multipli azionamenti laterali per pezzo.
Estrazione a Strappo
Nella progettazione di un pezzo, un “estrattore a strappo”consiste in un piccolo sottoquadro che non pregiudica l'estrazione, che può avvenire in tutta sicurezza da uno stampo a estrazione diretta senza ricorrere ad azionamenti laterali. Gli estrattori sono utili per risolvere lievi sottosquadri di semplice natura, ma dipendono dalla geometria, dal tipo materiale e dall’orientamento nello stampo.
Suggerimento: è possibile creare stampi del tipo nucleo-impronta con spazio sufficiente per consentire al pezzo di “estrarsi” quando lo stampo si apre.
Pick-out
Un pick-out è un elemento separato in metallo, inserito nello stampo per creare un sottoquadro. Viene espulso con il pezzo, quindi rimosso dall’operatore e reinserito nello stampo.
Suggerimento: l’utilizzo di un pick-out consente di superare numerose restrizioni di forma e posizionamento, ma è più costoso rispetto agli elementi di esclusioni scorrevoli o agli azionamenti laterali.
Fori di diametro ridotto con elevato rapporto altezza-larghezza
È possibile praticare questi fori collocando perni in acciaio nello stampo. I perni in acciaio sono sufficientemente robusti da sopportare le sollecitazioni collegate all’espulsione e hanno una superficie sufficientemente liscia da staccarsi dal pezzo senza angolo di spoglia. Non dovrebbero esserci effetti estetici negativi sul pezzo risultante. Se ve ne fossero, sarebbero comunque all’interno del foro dove risulteranno invisibili.

Attenzione alla calligrafia
Scegliete caratteri sans serif dove anche le parti più piccole presentano uno spessore minimo di 0,508 mm. I caratteri serif presentano code che sono spesso troppo piccole. È consigliabile utilizzare testo in rilievo. Il testo incassato non consente l’effettuazione della lucidatura.
- In SolidWorks, Century Gothic 26 point regular font and 16 point bold create millable text.
- Comic Sans MS 24 point also creates millable text.
- Con testi di dimensioni inferiori, una profondità pari a 0,3 mm spesso consente di ridurre i costi di fresatura e migliorare l’espulsione.
Largo ai punti di iniezione
I bordi sottili ostacolano il flusso e possono rompersi durante il taglio dei punti di iniezione. Il punto di iniezione deve trovarsi in corrispondenza di una parete spessa. Può darsi che vi siano soluzioni alternative. Contattate uno dei nostri tecnici del servizio di assistenza clienti al numero +39 0321 381 224 o all’indirizzo [email protected].
Pezzi autocombacianti
È possibile creare pezzi identici che, ruotando su se stessi, risultano combacianti e consentono di risparmiare sul costo di un secondo stampo.
Elementi di questo tipo includono:
- Pioli e fori
- Cerchi interdipendenti
- Ganci e serrature a scatto



Questione di materiale
Nel scegliere il materiale per il pezzo da produrre, le proprietà applicabili potrebbero includere la resistenza meccanica, fisica e chimica o la resistenza al calore, all’elettricità, alle fiamme o ai raggi UV. Le informazioni sono reperibili presso i produttori di resine e i produttori di miscele ed eseguendo ricerche nei motori indipendenti online per le resine. Per collegamenti relativi alle resine, visitare www.protolabs.com/it-it/materiali/guida-comparativa.
Resine comuni
Polipropilene
- Soffice
- Dura
- Economica
- Resistente agli agenti chimici
- Alta densità
- Bassa densità
Polietilene
- Soffice
- Dura
- Economica
- Resistente agli agenti chimici
- Alta densità
- Bassa densità
Polistirene
- Dura
- Trasparente
- Economica
- Fragile ma induribile
Resine industriali
ABS
- Economica
- Resistente agli urti
- Apparecchiature e custodie trasportate a mano
- Suscettibili alle depressioni
Acetale
- Più costosa
- Robusta
- Buone proprietà lubrificanti e di lavorabilità
- Molto sensibile all’eccessivo spessore delle pareti
LCP
- Molto costosa
- Molto robusta
- Riempie pezzi molto sottili
- Linee di giunzione deboli
PA (Nylon)
- Costo ragionevole
- Molto robusta
- Suscettibile ai restringimenti e alle deformazioni, in particolare se riempita con fibre di vetro
- Assorbe l’acqua, con alterazione di dimensioni e proprietà
Policarbonato
- Costo moderato
- Molto robusta
- Buona precisione dimensionale
- Suscettibile a crepe se sottoposta a sollecitazioni chimiche, vuoti
Poliesteri: PBT, PET PPS, PSU, PES, PEI... E molte, molte altre
Colori
Possiamo utilizzare sia i coloranti forniti dal cliente, sia i coloranti disponibili presso Protolabs, ed anche mescolare i coloranti tra loro, nel caso non vi sia corrispondenza tra il colore desiderato e le tabelle colore disponibili.
Scelta dei colori
Colori standard: i colori disponibili presso i venditori di resina sono solitamente il nero e il colore naturale. Il colore naturale può essere bianco, beige, ambra o altro. I colori semipersonalizzati vengono creati mediante l’aggiunta di pastiglie coloranti alle resine naturali. Per conoscere i colori disponibili, visitare www.protolabs.com/it-it/servizi/stampaggio-a-iniezione/stampaggio-a-iniezione-di-materiali-plastici/linee-guida-per-il-progetto/. La scelta di un colore da noi offerto non comporta sovrapprezzi. Non si tratta di corrispondenze esatte e in alcuni punti potrebbero presentare strisce o spirali. I colori personalizzati corrispondono esattamente a un Pantone o a un campione. Il cliente lavora con un produttore di miscele e ci fornisce la resina. Questo processo è più lento, ma genera una corrispondenza cromatica più accurata.
Additivi per resina
Fibre di vetro (corte): vengono utilizzate per rafforzare un composto e ridurre lo scorrimento, specialmente a temperature elevate. Possono rendere la resina più dura, più rigida e più fragile. Possono causare deformazioni a causa del diverso grado di restringimento tra la resina e le fibre.
Fibra di carbonio: viene utilizzata per rafforzare e/o irrigidire un composto, nonché per favorire la dissipazione statica. Presenta gli stessi limiti delle fibre di vetro. Le fibre di carbonio possono rendere la plastica molto rigida.
Minerali: ad esempio talco e argilla, che vengono spesso utilizzati come riempimento per ridurre il costo o aumentare la durezza dei pezzi finiti. Poiché durante il raffreddamento si restringono di meno rispetto alle resine, possono ridurre la deformazione.
PTFE (Teflon) e bisolfuro di molibdeno: vengono utilizzati per rendere i pezzi autolubrificanti nelle applicazioni a cuscinetti.
Fibre di vetro lunghe: avengono utilizzate come le fibre di vetro corte per rafforzare un composto e ridurre lo scorrimento, ma rendono la resina molto più forte e rigida. Lo svantaggio è rappresentato dal fatto che possono risultare disagevoli per pezzi con pareti sottili e/o flussi di resina lunghi.
Fibre aramidiche (kevlar): sono come le fibre di vetro, ma meno robuste e meno abrasive.
Perle di vetro e foglie di mica: vengono utilizzate per irrigidire un composto e ridurre deformazioni e restringimenti. In presenza di un carico elevato possono rendere difficoltosa l’iniezione.
Fibre in acciaio inossidabile: vengono utilizzate per controllare le interferenze elettromagnetiche (EMI) e le interferenze radio (RFI), normalmente in alloggiamenti per componenti elettronici. Hanno una conducibilità superiore alle fibre di carbonio.
Inibitore UV: per applicazioni outdoor.
Trattamenti antistatici eliminano l’elettricità statica dalle resine.
Domande?
Chiamate il vostro referente o un tecnico del servizio di assistenza clienti al numero +39 0321 381 211