3D Printing vs. CNC Machining: Understanding the Differences Between These Technologies
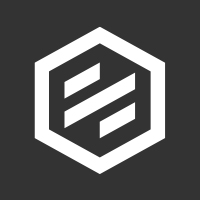
Manufacturing methods abound these days. Product designers and engineers have a stunning range of choices, and that’s usually beneficial for companies.
Sometimes, though, there’s such a thing as too much choice when trying to decide which process will work best for custom part designs and applications.
Case in point: two manufacturing techniques, which are especially well suited for prototyping and low- to mid-volume part production, are CNC machining and industrial-grade 3D printing—but how to decide between the two?
Key factors to consider when evaluating these methods are whether to use subtractive (machining) or additive (3D printing) manufacturing for your part. Also, think about which materials are available for your part within each process, the surface finish qualities of each method, part geometry capabilities of each, and, of course, pricing or costs.
What’s the Difference Between Subtractive and Additive Manufacturing?
CNC machining is a form of subtractive manufacturing, which produces parts by removing material from a larger block, that is, cutting away solid plastic or metal blocks into final parts. We offer CNC milling—3-axis milling and 5-axis indexed milling processes—and CNC turning with live tooling that combines both lathe and mill capabilities.
Machining in various primitive forms has actually been around since the 1700s, with computer numeric-controlled (CNC) machining emerging in the 1950s and 1960s as computers became smaller and more powerful.
By comparison, industrial-grade 3D printing or additive manufacturing builds plastic, metal, and elastomeric parts layer-by-layer using a variety of additive processes. We offer six in-house 3D printing technologies, plus other 3DP techniques through Hubs, our manufacturing network.
3D printing is a much more recent invention, with the additive manufacturing method of stereolithography first patented in 1984.
While machining has long been a reliable manufacturing process for both prototyping and end-use production, 3D printing has mostly been used as an essential prototyping method. However, that’s changing. More recently, 3D printing—and, to be clear, we mean industrial-grade 3D printing, not the at-home or in-office desktop variety—has emerged as a viable production method, especially for low- to mid-volume part production or when part complexity might prohibit processes such as machining. More about complexity and geometry a bit later.
Accordingly, here are the main advantages of each process:

CNC Machining
- High accuracy and precision
- Excellent repeatability
- Speed
- Wide array of production-grade materials, including plastic, available
- Broad range of post-processing options and surface finishes

3D Printing
- Nearly boundless capabilities in terms of freedom of shape or geometry
- Accuracy and repeatability
- Ability to reduce weight in parts, often through consolidating multi-part assemblies into a single part (lightweighting is especially key in automotive and aerospace sectors)
- Speed
- Can serve as a manufacturing option when parts require materials that can’t be easily machined, such as flexible thermoplastic polyurethane (TPU)
Comparing Materials Between 3D Printing and CNC Machining
You should also consider the types of plastics and metals available that each manufacturing method offers. Our website offers a huge list of options, along with data sheets for each material.
Considerations on the machining materials side include:
- CNC machining offers excellent mechanical and thermal properties with fully isotropic behavior—materials in which properties remain the same when tested in different directions
- CNC does have dimensional restrictions from material blank or block sizes (using a non-standard blank size increases the manufacturing cost)
- CNC offers a wide range of production-grade materials from which to choose
Considerations on the 3D printing materials side, include:
- Potentially lesser mechanical properties compared to CNC parts, as they are typically not fully isotropic
- Materials that would be difficult to machine (TPU and metal superalloys) can be 3D-printed
Materials at Protolabs by Manufacturing Process
Process | Metals | Plastics | Elastomers |
CNC Machining | Aluminum, Brass, Copper, Stainless steel, Steel alloy, Steel mild low carbon, Titanium | ABS, Acetal, CPVC, Delrin (POM), HDPE, LDPE, Nylon, PEEK, PEI, PET, PMMA, Polycarbonate (PC), Polypropylene (PP), PPSU, PS, PSU, PTFE, PVC | |
3D Printing | Aluminum, Cobalt chrome, Inconel, Stainless steel, Titanium | ABS-like, PA (nylon), PC-like, Polypropylene | Digital photopolymer, TPU, True silicone |
Surface Finish Quality of Machined and Printed Parts
Parts produced by both of these manufacturing processes can initially come out a bit rough. Those parts built by machining can come out, as some in the industry call it, “as-machined” or “as-milled,” that is, with some surface roughness and blemishes. Those parts produced by 3D printing can also have surface roughness or graininess and might have a stairstep appearance.
Fortunately, you can improve functionality and aesthetics of those produced parts with a variety of post-process finishing options.
Several post-process options for machining can help protect parts and improve overall finish. Common processes include plating (zinc, tin, gold, silver, chromate, etc.), anodizing, powder coating or painting, and more. Additional details can be found in our design tip that covers finishing considerations for machining and sheet metal.
For 3D printing, depending on the additive manufacturing technology, build direction, resolution, and materials chosen, you might see issues with part aesthetics. Here’s a quick look at the 3D printing finishing options we offer and what you can expect when your parts arrive from us:
- Unfinished: Dots, or standing “nibs,” remain evident on the bottom of the part from the support structure remnants.
- Natural: Supported surfaces are sanded down to eliminate the support nibs.
- Standard: Supported surfaces are sanded, and the entire part is finely blasted for a consistent look. Note that the layers are still present.
- Custom: Soft-touch paint, clear part finishing, painting, masking, color matching, decals/graphic, and texture finishes are available.
- Vapor smoothing: Eliminates rough surfaces and leaves a glossy, aesthetic finish on parts.
- Surface finish improvement: Finishing options include light sanding to remove layer lines all the way to cosmetic, polished surfaces.

3DP SLA ABS (unfinished)

3DP DMLS (standard finish)

3DP SLA Watershed (natural finish)
Here’s something to consider: Use post-processing machining on 3D-printed parts to get the complexity that machining alone can’t achieve and the precision on critical features that additive can’t achieve. This especially applies to metal 3D-printed parts, showing how this combination can be the ideal equation for metal manufacturing.
Part Geometry, Complexity, and Manufacturability
Remember we promised more about geometry and complexity? Here we go.
Generally speaking, CNC machining is better for fairly straightforward part designs while 3D printing can produce parts with few geometric limits.
Machining can be limited by elements such as tool access or path, tool type, minimum radii, and clearances, among other items. In fact, in some cases, manufacturability becomes an issue. We sometimes work with customers who initially have part designs with geometries that simply can’t be machined.
By contrast, as mentioned, 3D printing can create parts with few geometric limitations, and can produce parts with hollow features without the need for support structures. The vast design freedom and capacity for complexity that 3D printing provides, and the overall capability to produce highly complex geometries with relative ease, is one of additive manufacturing’s key strengths.
Scale and Pricing of Machined and Printed Parts
For the most part, these two items are inextricably linked. That is, costs will generally depend on how many parts are required and how quickly those parts are needed. Additionally, the cost of materials (for example, think ABS vs. PEEK) can be a factor, and the degree of complexity of a design’s geometry can also influence cost.
Accordingly, for parts with higher volumes (100 or more) and fairly straightforward geometries, CNC machining would likely be the choice. Machining provides more favorable economies of scale. Use 3D printing for lower quantities—and especially for rapid prototyping—and if the part’s design has complex geometries.
Finally, with quantities beyond say 500 or 1,000, consider other manufacturing processes such as injection molding, all of which we offer.
As always, if you have any questions, feel free to contact one of our applications engineers at [email protected] or 877-479-3680.

If you have any issues getting your guide, download here.