A Deep Dive Into Manufacturing Analysis: Accessing and Interpreting Feedback to Optimize Your CAD Model
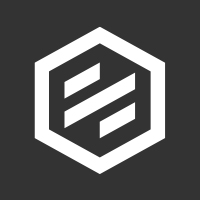
Have you heard the news? We’ve launched an all-new digital quoting platform designed to accelerate the design and manufacturing process every step of the way. And one of the first interactions you’ll have with us, when you’re ready to manufacture parts, is within our newly optimized ecommerce quoting and ordering application. It sits firmly at the core of our software-driven, front-end digital manufacturing process—before any production begins.
In our last blog post, we covered basic navigation, organization, and collaboration within the platform. In this, our final post in the series, we take a closer look at what is arguably the most important benefit of the platform, sandwiched between your request for analysis and actual placement of your order. It’s our automated, interactive manufacturing analysis. And with the relaunch of our new platform, you’ll see that we’ve given it a modern interface along with some new features you’ll find valuable.
Finding Your Manufacturing Analysis
Before we go too far, how do you actually get your free manufacturing analysis? Just sign in and upload a part at protolabs.com, make your appropriate selections in key areas like materials, quantity, surface finish, turn time, and submit a request for quote. Within a few hours, you’ll have an email in your inbox letting you know your quote is ready with a 3D analysis of your design. The overall process is fast and painless, and honestly, something you don’t often get with traditional manufacturers.
Simply stated, our manufacturing analysis provides feedback on the geometry of your CAD file to improve manufacturability. And in our new platform, manufacturing analysis has been enhanced to provide even more clarity on any design decisions. We’ve improved the revision and reanalysis process to drastically accelerate the design feedback loop. As a result, the analysis and any resulting design adjustments can reduce manufacturing time and production costs. And who doesn’t want that?

But hey, in some cases, your design may have no critical manufacturability issues. No required changes. Not even any suggested changes. You nailed it. Nice work. In other instances, you may need to make some tweaks. Your parts will have many color-coded statuses as they progress through the configuration, analysis, review, and approval stages. Ultimately, the goal is to get your parts to green Ready to Manufacture status. Here’s how the colors translate:
- White = Needs Configuration. All newly uploaded parts begin with a white status. These parts need to be configured and, if necessary, sent for analysis.
- Gray = Manufacturing Analysis in Progress. Parts with a gray status are currently being analyzed by our team to identify manufacturing limitations, lead times, and pricing. You'll get an email from us when all the parts on your quote are ready for review.
- Green = Ready for Manufacturing. Parts have completed analysis and quoting, and do not require additional review or approval. You may checkout once all parts on a quote have reached this status.
- Yellow = Review and Approve. Parts with a yellow status are almost ready for manufacturing. We just need you to review the manufacturing analysis to approve advisories, accept gate and ejector layouts, and/or choose your threading options. Once approved, your parts will change to green status.
- Red = Revisions Required/Unable to Manufacture. Unfortunately, we are unable to manufacture parts with a red status. Please review the manufacturing analysis to learn how you may modify your part design to match our manufacturing capabilities. You can also contact us to review with one of our application engineers.
- Black = Expired Quote. Parts with a black status have expired pricing. Please resend for quoting. Thanks!
We look at many variables and, depending on the manufacturing service you’re using, highlight features that are potentially troublesome. On any recommended changes, you’ll need to adjust your design to improve manufacturability, or accept any limitations to the part that may occur if changes aren’t addressed. Any required changes means you’ll need to update your part geometry based on the feedback and upload a new CAD file to proceed with your order.
The first thing you’ll probably notice when you jump into your manufacturing analysis is a beautiful, three-dimensional model of your part on the right side of the screen. You can manipulate the part in any direction, so go ahead, spin it around, zoom in and out, get familiar with the controls. You can also:
- Change orthogonal views
- Reduce or increase part transparency and single out the manufacturability issues
- Bounce between metric and imperial measurements
- Access shortcut keys
- View as a PDF

Common Advisories Within Your Manufacturing Analysis
Now that you’ve poked around a bit, let’s walk through some of the suggested and recommended advisories you may see.
Part Exceeds Limitations. For each of our manufacturing processes, we have minimum and maximum part sizes and some other design guidelines to adhere to for manufacturing that can be found on our website for each process.
Thin and Thick Areas and Walls. While excessive wall thickness is less of a concern with machining and 3D printing, walls and features that are too thin or too thick can be troublesome on injection-molded parts. Well-designed parts will have uniform wall thickness when possible, and walls in any plastic-molded part should be no less than 40 to 60 percent that of adjacent walls. And all should fit within recommended thickness ranges for the selected material. If not attended to, defects like flash, sink, and knit lines can wedge their way into the cosmetic appearance your parts.
Zero Draft. Draft—a taper applied to the faces of parts that prevents them from being damaged due to the scraping as they are ejected from the mold—is another important design consideration with molding. Without draft, drag marks, distortion from ejection stresses, and other issues can arise. A general rule of thumb is 1 degree of draft per 1 inch of cavity depth. The manufacturing analysis will highlight areas with zero draft so they can be modified.
Texture. Speaking of draft, with textured features, we recommend higher degrees of draft angles to assist with part ejection during molding and avoiding cosmetic defects.
Radius. Adding radii—an edge or vertex that has been rounded—is typically a natural element of the milling process, whether a mold is being milled or an actual part is being machined. In your manufacturing analysis, we’ll highlight on your 3D model where these radii will occur. In some cases with injection molding, we’ll add radii to assist with the flow of thermoplastic resin through the mold. Radii are less of a concern with additive manufacturing, however, if you plan on producing larger quantities of molded parts from that same 3D-printed design, it’s something to keep in mind.

Mold Flow Analysis. Another part design element we analyze and provide valuable early feedback around is how resin will flow through the mold. You’ll see fill pressure mapped out across your part that resembles a color-coded rainbow. We’ll recommend design changes like changes to wall thickness or other features to reduce fill pressure and ease the flow of resin through the mold. We avoid flash or short shots—geometry that wasn't completely filled with resin, causing short or missing features. Again, up-front analysis, before production begins, to make modifications if needed and accelerate the manufacturing process.
Material Left Behind. If you’re part is destined for machining, you may come across this advisory. We’ll identify what percentage will be milled and what will remain un-milled, thus deviating from your original design. You’ll see highlighted in red, areas where material will be left behind. At this point, you can modify your design or roll with the existing design.
OK to Machine on Lathe. Your part design may be best suited for turning on a CNC lathe. We’ll let you know in your manufacturing analysis is that’s the case, but you’ll still have the option to have it milled instead. Cylindrical parts are typically good candidate for turning, which can improve overall surface finish. Also, our CNC lathes—including an advanced Mazak lathe—have live tooling for features like on-axis, axial, and radial holes.
Threadable Features for CNC Machining
Applying threads to machined parts now simpler than it has ever been and of our more popular features with machining customers. Within your manufacturing analysis, you can easily highlight and assign which holes need threads by clicking on your 3D model (vs. choosing from a list of holes) and you’ll immediately see the cost implications.
We offer a limited selection of UNF, UNC, and metric threads along with coil and key inserts (but do not supply or install the inserts). On both milled and turned parts, threaded holes must be modeled at the proper diameter, however, threading options differ for milled and turned parts. For detailed information on machined threading options, check out our comprehensive threading guide.
Gate & Ejector Pin Layout for Injection Molding
We’ve now built your gate and ejector pin layout design review on molded parts directly within your manufacturing analysis before you place your order! In our prior platform, this could be a time-intensive back-and-forth conversation whereas now it’s streamlined directly within your quote. Again, the goal is to make this as painless as possible for you to order parts.
Within your manufacturing analysis, you’ll be prompted to VIEW GATE & EJECTOR LAYOUT. In doing so, we’ll highlight on your 3D model in yellow and red where it will be gated along with specific notes on the left side of the screen detailing the type of gate used—sprue or tab gate, for example—and that a small vestige typically may occur on the surface. You can comment on the layout by clicking on a section of your 3D model or advance to the next step, which is your ejector pin placement.
Here, we highlight in yellow circles all of the areas on you 3D model where pins will be used to eject your parts from the mold. Note that ejector pins typically leave small indentations on the surface your parts of approximately. Again, you can leave a comment on our recommended pin placement, or continue toward approval. Finally, you can download a PDF design review to look over, check the approval box, and you’re all set. If you’ve left any comments, those will be sent back to our team for review and to prepare a revised layout based on the feedback.

On-Demand Manufacturing for Low-Volume Injection Molding
We provide two injection molding service options. One is best suited for those who need smaller part quantities often associated with prototyping and the other a good fit for those who require larger part quantities common in low-volume production called On-Demand Manufacturing (ODM). While the molds themselves are similar, part quantities, lifetime maintenance, quality documentation, and pricing vary depending on which service option is chosen. The right one depends on your project needs. Let’s quickly look at the benefits of ODM and how to select that option it in your quote.
When requesting a quote, you’ll have the opportunity to choose the Mold Life of your tooling—limited or unlimited. You can even choose I’ll Decide Later and we’ll work with you to identify the best tooling option. By selecting unlimited, you’ll move into our ODM option. From there you can also select Sample Quantity and can identify whether you’ll need a single-cavity mold or multi-cavity (up to 8 cavities).
To help you decide, we created an all-new Price Curve tool that compares prototyping against ODM options so you have full visibility and total cost of ownership on molded parts throughout the product life cycle. As you adjust the total quantity you’ll see in real-time the impact on cost. And because of the cost saving at higher volumes, ODM is suitable for ramping up before shifting to full production volumes (outside of Protolabs). Additionally, a range of secondary services help provide a more comprehensive on-demand manufacturing service.

Protolabs Proposed Revisions for Injection Molding
The final area that we want to touch on is what we call our Protolabs Proposed Revisions (PPR), which are intended to help improve part design and material selection on injection molded parts, and again, accelerate the overall manufacturing process. PPRs are a suggested modification to your part geometry to ensure your design complies with the capabilities of our digital manufacturing process. If you part has some required changes and qualifies for PPR, we’ll send you an already-revised model that you can review within your manufacturing analysis.
Generally, we'll provide STEP, IGES, and SolidWorks files depending on your original CAD model. If you like the change and there are no unresolved required changes, you can go ahead and accept the revisions and order your parts. If you like the proposed changes but want to order from your own source file, you can download the CAD model from your quote, update your own source file to match the PPR, and resubmit it. Quoting again is required to ensure a match between the quote and part, but the updated quote should be returned with no required changes and thus, your part should be orderable.
If you don’t like (or can’t accept) the PPR, you can resolve design advisories by modifying your part geometry to meet the intent of the advisories and PPR, and resubmitting your part, or you can discuss alternative solutions by contacting one of our applications engineers at 877-479-3680 or [email protected]. PPRs are free (!) and revised geometries are priced as any part would be. Some changes will influence price up or down. In practice, most price changes from minor geometry revisions are negligible.
Ok, that’s it. We know this was a lot to cover but hopefully it helped serve as a primer for our manufacturing analysis, interpreting the feedback, leveraging all of the capabilities that are possible inside your quote.
Got a project? Upload a part now. If you’re not quite ready, head over to our sample quotes for injection molding, CNC machining, and 3D printing, which will give you a chance to test drive the platform and the interactive manufacturing analysis.