Aluminum Mold Tooling for Injection Molding

A part's journey through injection molding hits an early form in the road when the customer must decide between aluminum and steel tooling. Choosing a path is based primarily on quantity demands. If you are producing quantities north of a million parts, steel tooling and a capital investment of more than $50,000 is necessary.
If your part volumes don't stretch into the millions, aluminum tolling at a fraction of the cost is likely the path for you. In bypassing the high-volume paradigm—large investment, long wait times, and above all, inflexibility—aluminum tooling allows product developers to be nimble.
The aforementioned benefits of aluminum are in part due to the materials machinability. Compared to steel, aluminum is softer, meaning it can be CNC machined for molding much faster than steel. Less machine time equals less cost. Aluminum is capable of molding production quantities of about 10,000 parts as a rule of thumb, but quantities are often much higher. Mold life is dependent on the material type and geometry. Still, it will likely need to be replaced for before a steel mold would.
In general, aluminum tooling is the ideal choice if part volumes don't stretch into the millions, if you need on-demand production parts within days, and if you're looking to avoid risky tooling investments before your part design is truly validated.
Key Benefits of Aluminum Molds
Aluminum tolling has several advantages. Molds begin around $1,500 and can be delivered in seven days or less. Steel tooling, comparatively, works on a larger lead time.
Aluminum tooling produces production quantities of at least 10,000 parts, but often much more. At Protolabs, customers can choose either prototyping or on-demand production for quantities and corresponding price point to fit their needs (more on that later).
Aluminum molds are also capable of many of the features customers expect with production tooling, including:
- Single and multi-cavity tooling: 1-, 2-, 4-, and 8-cavity molds are possible depending on part size and complexity.
- Expansive materials library: thermoplastic and thermoset materials identical to that of high-volume production materials are available. More than 100 different materials can be used including ABS, polycarbonate (PC), polypropylene (PP), liquid crystal polymer (LCP), polyoxymethylene (POM)
- Beneficial material properties: The thermal conductivity of aluminum allows for improved heat dissipation, reducing the need for messy cooling lines.
An additional cost savings, aluminum molds also remove the need for maintenance feeds with damage to the mold covered over its lifetime.

Design Considerations for Aluminum Molds
Part Finish
Choosing the correct surface finish for your part's application will prevent unnecessary expense. If part cosmetics are critical, a smooth SPI-A2 finish requires mold cavity surfaces to be hand-polished with diamond buff to 1-2 Ra. This drives up the cost of mold manufacturing and increases in lead time. If aesthetics is not a concern, PM-F0 is an as-machined surface that will probably show some tool marks but is the least expensive. Below you will find the full range of surface finishes offered at Protolabs:
Surface Finish Specification | Description |
---|---|
PM-F0 | Non-cosmetic, finish to Protolabs' discretion |
PM-F2 | Non-cosmetic, EDM permissible |
PM-F1 | Low-cosmetic, most toolmarks removed |
SPI-C1 | 600 grit stone |
SPI-B1 | 600 grit paper |
SPI-A2 | Grade #2 Diamond Buff |
PM-T1 | Light bead blast |
PM-T2 | Medium bead blast |
Draft for Part Ejection
Whether aluminum or steel tooling, adding draft to your mold is required to improve the moldability of your part. Without it, parts may have a poor surface finish, and may bend, break, or warp due to the molding stresses caused by the plastic cooling. By adding a taper to the faces of the part, draft prevents scraping as the part is ejected out of the mold.
Wall Thickness
Each thermoplastic family has a recommended minimum wall thickness. Following those guidelines will help prevent warp and sink during cooling. A general rule for wall thickness is somewhere between 0.040 in. to 0.140 in. (1 to 3.5mm), applied consistently across the entire part.
Add Radii to Corners
Aluminum molds are CNC machined at Protolabs, which is quick and effective; however, the end mills used make machining sharp internal corners difficult. Furthermore, sharp corners on any mold create stress and weaken structural integrity. With that, generous use of radii (rounded edges or vertexes) in part design is recommended.
Aluminum Tooling at Protolabs
Protolabs offers two service-level tooling options capable of meeting unique needs during the product development process.
Prototyping offers a lower price point for limited qualities, while part price is higher. On-demand manufacturing offers a longer mold life and is best when production will be needed for multiple years at higher volumes for end-use parts. View this page to compare our tooling options for injection molding.
If you have any questions, don’t hesitate to contact our applications engineers for help at 877-479-3680 or customerservice@protolabs.com.
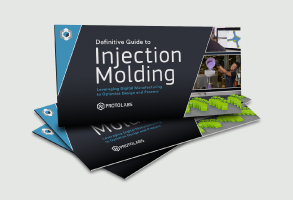
If you have any issues getting your guide, click here to download.