PODCAST: Breathe99 Founder Max Bock-Aronson’s Next-gen Mask Protects Against COVID-19
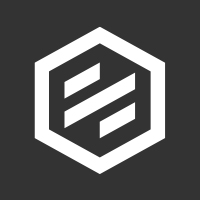
With the emergence of COVID-19, people are taking a close look at available personal protective equipment. A new company called Breathe99 recently developed a face mask with 99% filtration and a sustainable filtration system that can help people safely navigate this new reality. On our first episode of The Digital Thread, Breathe99 founder Max Bock-Aronson discusses the history of the B2 mask and the challenges of manufacturing it.
Additional Links
> Full Breathe99 Success Story
> Breathe99 Kickstarter Campaign
Podcast Transcription
Steve Konick: Hi and welcome to the Digital Thread. Our new podcast that's all about manufacturing. It's produced by Protolabs.
Steve Konick: Throughout the series, we'll give you some insight into latest and best practices in manufacturing. We're going to talk about some cool parts and explore how they were made. We'll also check out companies that are pushing boundaries with cool ideas.
Max Bock-Aronson: It's much more akin to industrial grade respirator, and that filters the cartridges are removable that are components that can be exchanged off of the mask, their sort of mask accessories or mask components, which is obviously something that's really important in the current context right now with the Coronavirus pandemic.
Steve Konick: I'm your host for this edition, Steve Konick. And today is our first podcast. So it's great to have you along. Covid-19 continues to affect lives all over the world. Engineers are finding themselves challenged to come up with new ideas to protect frontline medical teams and folks like you and me. One of the more interesting ideas is the B2 mask from Breathe99, our recent Protolabs Cool Idea Award winner.
Steve Konick: Today we're talking with Breathe99 founder Max Bock-Aronson. Max joins us from a safe social distance from me of roughly fourteen hundred miles in Minneapolis, Minnesota. Before we get into discussing the B2 Mask,and what makes it so different? Can you tell me a little bit about the evolution of Breathe99?
Max Bock-Aronson: Sure. So the genesis of Breathe99 came from the study abroad experience that I had in Singapore. So it was back in 2013. I was studying and living Southeast Asia and I was taking mostly mechanical engineering courses. But just out of curiosity, I also took an air pollution engineering course. And Singapore itself doesn't have poor air quality usually. But neighboring countries will clear their fields using polluting slash and burn techniques. And that pollution will drift across national borders and cause issues for people living in Singapore. And so it was through my lived experience, experiencing that acute air pollution for the first time. And what I was studying that sort of formed the basis of Breathe99.
Steve Konick: From what I read, you would run and the air pollution caused you to have difficulty breathing.
Max Bock-Aronson: That's right. I would go for nightly runs and it was later in the evening just because it can get quite hot during the spring season. And there was one night in particular when I got back to my apartment and noticed that my throat was scratchy and my lungs were hurting a little bit. And I looked up the air quality index for that night, the AQI, and saw that it was really high from the coursework that I was taking at the time. I was aware of how that was affecting me physiologically. And so I actually went to a market and tried to find the mask that would provide adequate protection for that small particulate matter, but also was comfortable and looked good. And I had a lot of difficulty finding something.
Steve Konick: The mask is like nothing I've seen before. It does have a cool quality about it. It's got a great look. Can you walk us through the B2 design and what makes it so special?
Max Bock-Aronson: Sure. In essence, the B2 mask consists of three main components. There is a flexible face piece and that's what's actually in contact with a person's face. It has a flexible seal that conforms to a wide range of face shapes and sizes. And it's what ultimately provides sort of that that high quality seal to ensure that you're only drawing air through the filters that face pieces loaded with two high efficiency filters that remove ninety nine percent of common contaminants from the air you breathe. And loading those filters is really easy to do. You sort of just press it down into a shallow dish like interface on the face piece and then there's a filter cap that with sort of a quarter turn type interface. You just press it down onto the filter and then you twist it sixty degrees technically. That's what provides the clamp and pressure for the filter, ensuring that the air is only passing through the filter and not around the filter. And then all of that is covered with a comfortable and breathable fabric overlay. And this was something that we garnered from early user feedback testing that we did in China and Korea. We had a design even before sort of the B1 mask that was much more similar to just an industrial sort of respirator. It was more stylish, but it didn't have a fabric overlay at all. It just had a harness. And the feedback that we received was that I like that this is comfortable. I like that this provides high protection, but it's a little bit too aggressive. I want something that feels a little bit more stylish or something that blends into my lifestyle more. And that was part of what brought about the fabric overlay.
Steve Konick: And where did you get the idea to create the filters as a separate piece entirely?
Max Bock-Aronson: Yeah, I think really what that decision was derived from my experience working in the woodshop at both my university and also where I worked at the time. So it's much more akin to industrial grade respirator and that filters the cartridges are removable that are components that can be exchanged off of the mask, their sort of mask accessories or mask components. And it was after exploring that, that I realized that one of the biggest value ads of doing that is that you're no longer throwing out large portions of the mask. You're reusing a vast majority of the mask, and you're only throwing out what you need to throw out. And there's a lot of efficiencies that are gained in that, primarily that we're reducing filter waste and cost by up to half. And also because of the simplicity of the filter, it's just a small circular disk. That filter is much, much easier and faster to produce and to scale, which is obviously something that's really important in the current context right now with the Coronavirus pandemic.
Steve Konick: Yeah, no question. I mean, the idea that this is sustainable is going to mean a lot to people, I think. Was that something you wanted as part of your design or is that something that came along for the ride?
Max Bock-Aronson: No, I mean, when we were first thinking of the mask, we were laying out what might be considered marketing requirements, things that maybe they weren't specifically measurable, but goals that we sort of qualitative attributes of the mass that we wanted to make sure were captured in the design. One of those was that it was a more sustainable option and more affordable in the long run as well.
Sponsorship Message: Our CNC machining facilities have infinite capacity to eliminate production delays. Plus, our in-house engineers will talk directly with you to help optimize your parts for manufacturing. Ready to start a machining project? Get an interactive quote with free design analysis in ours at protolabs.com.
Steve Konick: Was going with ninety nine percent filtration, a conscious decision?
Max Bock-Aronson: It was a conscious decision. Yeah, yeah. No, it was a conscious decision. I mean, our brand is Breathe99. And that speaks to the efficiencies that we're seeking to achieve and eventually the certifications that we planned to pursue as well. From a manufacturing perspective at least. No, no drawbacks really to going with N99 material. The one thing to consider is that it's the breathing pressure is a little bit higher, but then the material itself is more expensive. But because again, we're not throwing out vast majorities of the mask. We can produce that N99 grade filter, it can last the same amount or longer during use and it's cheaper because it's easier to produce.
Steve Konick: Yeah, it makes a lot of sense. You mentioned before that there was a predecessor to the B2. What were the essential differences between the two?
Max Bock-Aronson: Yeah. So the B1 mask was and you can imagine, Steve, that there were a lot of iterations before the B1 as well.
Steve Konick: Oh definitely that's always the way it goes.
Max Bock-Aronson: But the B1 started taking a more firm shape in 2019. And we ended up actually launching a Kickstarter campaign for the B1 in August of 2019. We learned a lot through that process. We didn't end up meeting our funding goal, but really learned a lot from that process. And a lot of the learnings that we had through that were then implemented into the B2, primarily the big one was just the overall form factor. Changed a little bit. So the B1 was featuring what I might consider more like pucks, like filter pucks that are magnetically coupled to the mask. We were going for sort of this cool, flashy consumer approach to the filters, but they were a little bit cost prohibitive. So that was one thing that we stripped away. Also, we completely rethought how the fabric overlay was constructed, how it's attached to the mask, how it harnesses to the head as well. And so it's designed to just be a lot more comfortable. Finally, the filters themselves, we increase the surface area of the filters. And what that does is that reduces the breathing pressure and makes the mask more comfortable to wear. So because we were creating the B1 with consideration to air pollution, primarily, we were aware of the fact through our user research that people wear masks in Asia, in particular to help prevent the spread of sickness. So we were aware of that before, but we really were thinking about the B1 has a product to help protect one from ambient air pollution. That was the idea. But in the context of Covid-19 and an infectious disease, we decided to take out the exhalation valve for the time being. And the reason for that is because if you are sick and you're wearing a mask, you're still potentially putting others at risk if you have this high flow air path moving through the mask. So we made various changes to ensure that the mask is still really breathable. But that was one decision that we made as well. In this specific context.
Steve Konick: So the B1 didn't work for you. Was that a setback or were you already working on the B2?
Max Bock-Aronson: Well, I was thinking about what the next generation mask would look like. Yeah, it's absolutely a setback, a humbling experience. But those sorts of experiences are really, you know, they inform a lot. And I learned a lot both about how to design a product, how to engage the public with that product, and also how to move through hardship as well. Just in general, I mean, it's never easy to put yourself out there and not meet the goal that you've sort of put forward for yourself. But you grow through that experience and I would take it back for anything.
Steve Konick: A lot of people forget that the rewards are not instantaneous, that there is a process in all their iterations to be made. And now you have to B2. You worked with Protolabs to manufacture parts for the mask. How did you connect up with us?
Max Bock-Aronson: I've had a long, ongoing relationship with Protolabs. Protolabs is one of the first manufacturers I ever interfaced with out of college. And my first job as a young design engineer, I was working in Madison, Wisconsin at the time and I uploaded several parts to Protolabs online quoting tool. And that was that was sort of my first exposure to you guys and to your business. And from there, it's just been pretty organic. I mean, working with Protolabs is really easy. It's one of the reasons why people who are looking for parts quickly come from all around the world, frankly, to interface with you guys. So I've been aware of Protolabs for a long time and a little bit of history about Breathe99 and Protolabs is relationship was, I spoke with somebody on the marketing team back in summer of 2019 about the B1 mask and we had an engaging conversation and she recommended to me that I apply for the Cool Idea Award.
Steve Konick: And for people who don't know about the Cool Idea Award, we provide grants that help build prototypes or maybe fund initial production runs. And we are looking for companies that are have kind of brilliants. Interesting ideas.
Max Bock-Aronson: Exactly. And so I applied and we made it through the first round, but it was in the second round that we started digging into the details. And what it turned out was that while Protolabs was able to manufacture certain components of the B1 mask, it was the overall over mold of the flexible face piece that didn't fit well into Protolabs capabilities at the time, at least. And so ultimately, we didn't get that first award. But when we came back around the second time for the B2, I had found a partner who would be able to do that second molding process and I thought that Protolabs might be a really good partner for getting those other components made quickly and then being able to build sort of a partnership between Protolabs and MME Group is the name of the other molder and Breath99. And so that relationship sort of came about really organically.
Steve Konick: And so how did our Cool Idea Award help you and the Breathe99 team gets where you wanted to be?
Max Bock-Aronson: In more ways than one. I mean, obviously we're an early stage startup. We don't have a lot of liquidity right now and we aren't able to just go and pay for large injection molding tools. Working with a group like Protolabs that's able to offer those grants through the Cool Idea Award and help accelerate our time to market is huge, especially in this context here, where it's important that we get product to people as quickly as possible to help advance our public health objectives, not only as Protolabs, as speed and sort of your digital manufacturing. That's really beneficial to Breathe99 and getting parts to people and assemblies to people quickly, but also the support on the front end for getting that injection molding tooling is really important. And then beyond that, just working with Protolabs and building this relationship, deepening this relationship has been incredible for us and led to a lot of credibility to what we're doing and also helped us as we communicate our story and our progress to consumers, the media and everybody else.
Sponsorship Message: At Protolabs, we accelerate your entire manufacturing experience from automated coding and connected production to digitized quality control and shipping, ready to start a project, get an interactive quote with free design analysis and hours and custom parts in days at protolabs.com.
Steve Konick: And ultimately, what we made for you for the B2 mask was the filter assembly?
Yeah, exactly. So again, the face piece is the flexible component that conforms to a user's face. But as part of that subassembly, there are several components that flexible TPE material is molded over. And then there are several components that are actually assembled to those rigid substrate materials. And so Protolabs is manufacturing all of those rigid components, which consists primarily of the filter interface. So the filter is being clamped against these parts. And then also the fabric overlay is hooking on to one of these rigid components as well. And that's what attaches the overlay to the face piece itself.
Steve Konick: What specific materials did you ultimately choose for the filter assembly?
Max Bock-Aronson: The face piece consists of of several rigid plastic components that are molded out of polypropylene. And the overmold is an FDA compliant TPE arterial. Both both families of resins are FDA compliant. When the conversation started with Protolabs and MME, we first were looking at using ABS for those rigid plastic components. And part of the reason for that was because ABS is just a really good overall sort of well rounded plastic for it's durable, it's good for medical applications, things like that. And it's also ideal for ultrasonic welding, which is one of the processes that we need to use for the assembly portion of the mask. But ultimately, we decided to go with polypropylene for those rigid components. And part of it had to do with some of the thinner wall sections that we have on those rigid components. Polypropylene has really good flow characteristics and there's less of a concern with those than portions. But also the overmolding group was they were confident in the chemical bonding that occurs between the TPE material and the polypropylene. And they were less familiar with how that bonding might occurred to a ABS. And so because speed is really critical for our product launch and getting this product to people quickly, we wanted to go with processes and with materials that were more familiar to both groups. And so that was what ultimately drove the decision to go with the polypropylene.
Steve Konick: So, Max, how does Protolabs range of materials and processes helped you with development of the B2 mask?
It's rare that you find one group that offers all sorts of 3D printing processes that you can work with. You can quickly iterate on your design and then you can transfer those designs to your manufacturable product and then work with the same groups to help drive that through the commercialisation process. So it's that range that's really unique. And for the B2 mask in particular, we ended up using an SLS or a selective laser sintering 3D printing process because of the flexibility that that process affords, not just in the actual part itself, which is a flexible resin, but also in how the part is supported during the printing process as well. It doesn't require port materials to be built like an SLA process does. And because of the complicated geometry of the B2 mask, it was that SLS process that really gave us the best flexibility in both process and in material.
Steve Konick: How is Protolabs helped with prototyping and also getting approvals for the B2 mask?
Max Bock-Aronson: Yeah, actually. So we are about to run a face fit study. We're working with a really well known group that has worked with NIOSH in the past. That's the National Institute of Occupational Safety and Health to parameterize face shapes and head sizes. And they've run a lot of face fit studies like this to ensure that respiratory protection products fit a wide range of people, cross demographics. And so Protolabs is actually supporting us in this testing by doing some 3D printing for us. So we are 3D printing the face piece and several other components to help accelerate that testing so that we can sort of confirm our geometry, but also potentially accelerate our application for the FDA as emergency use authorization or the EUA, which is something that we're considering and we've been looking at with some of our medical advisors as a potential pathway for this product. Protolabs has also in the past, 3D printed test fixtures for us so that we can run flow testing for our filters themselves, and it's through that flow testing that we've confirmed that our filter removes ninety nine percent of contaminants, you know, down to point one micron. It's that testing that really lends a lot of confidence to what we're doing and that we are building a product that provides the highest level of protection to people in their daily lives.
Steve Konick: So Max, what are some of the other ways in which business is growing for you?
Max Bock-Aronson: Yeah. So it's been really exciting over the last month and a half. We just closed our first round of financing with Venn Foundation, which is a 501C3 nonprofit foundation here in the Twin Cities area. And they help accelerate early stage companies and also nonprofit organizations that are trying to advance social missions. And they do it through donor advised funds and an investment tool called a program related investment. And basically, it is a way through which people can make tax deductible donations to help support businesses and nonprofits that are engaged in social impact work. So it's a really creative and unique way to advance social businesses. And so working with them has been really incredible. And it's one of the only reasons actually we're able to move as quickly as we have been, along with the Cool Idea Award as well. So that's been great. And through that process, we've also brought on several key team members as well who have backgrounds in nanotechnology. One person who is an ex Google and has her master's degree from the London School of Economics. And so we're starting to build a team of like minded individuals who really are dedicated to this purpose that we have at Breathe99, to advance public health objectives and to make high quality public health products more accessible to everyone.
Steve Konick: That's really cool. OK, your Kickstarter has gone way beyond your expectations. That really has to make you feel pretty good.
Max Bock-Aronson: It does. You know, I will say that as the founder and CEO of Breathe99, one thing that I'm trying to keep in mind is that, you know, we're making public health products and these products are for people who many of whom are going through difficult time right now. And so while there's a lot of excitement in the Breathe99 team and we're eager to help support people and the public, we're trying to do that in a way where we're very mindful of the fact that the people we're hoping to serve are struggling. So, yes, it is exciting, but at the same time, we're really invested in getting product to people quickly so that we can support better health outcomes.
Steve Konick: Well, when does the product officially come out? What do you think? What's it looking like?
Yes, right now we're targeting the second to last week in June is when the mask will start shipping to people. So we anticipate that our early backers on Kickstarter in the US will start getting their mask's second or third week of June. And then depending on where people are internationally, it might end up being early July for those backers. So that's sort of the timeframe that we're looking at right now.
Steve Konick: Well, let's talk about pricing. What is the B2 mask going to cost for the public?
Max Bock-Aronson: Yes, the retail price we are anticipating is fifty-nine dollars. There's still some details that we need to work out on our cost end of things, but we feel pretty confident in delivering at that fifty-nine dollar mark. And then obviously we'll be working with businesses as well for larger orders and there will be discounting for people who are making larger orders as well.
So Max, Breathe99 is out there. Where do we find you?
So our website breathe99.com is a good place to start. Have a lot of good information about B2 mask and also our social mission. We also have an FAQ you section on the Web site if you scroll down to the footer. And we're also live on Kickstarter right now until May 7th. And that is where we are currently doing our preorder campaign. You can still get deals on B2 mask. I think it's a it's like a ten percent discount on B2 mask if you order through the Kickstarter. But if you do miss that May 7th date, then we will be transferring over to our website in order to handle any additional preorders that people might like to make before the mass becomes available in June.
Steve Konick: And that's it for the first edition of the digital thread. I'd like to thank Max Bach Aaronson of Breathe99 for joining us. If you like what you heard, subscribe to future podcasts through one of our host sites like Apple, Google or Spotify or listen on our website. The digital thread is produced by Protolabs, a digital manufacturing company with locations across North America, Europe and Japan. For more information, go to protolabs.com.
The Digital Thread is a new podcast series from Protolabs that looks at all things manufacturing. We'll talk with today’s leading product innovators, hear from crafty veterans on trends affecting different industries, uncover issues disrupting supply chains, and much more. We'll publish new episodes periodically, so tune in when you have a few minutes—you might just discover a few design and manufacturing nuggets to help you along the way.