Finishing options for sheet metal vary depending on your needs. For instance, are you looking for an aesthetically pleasing part, a part that needs to withstand environmental challenges and wear, or are you testing overall functionality? The answers to these questions can send you down different paths when it comes to your finishing requirements. Let’s dig into some of those.
Standard Surface Finish Options
If you are purchasing a sheet metal part to test form, fit, or function, you probably don’t care a lot about the overall appearance of your part—but you also don’t want it to have sharp edges or the raw finish from metal straight off the mill. To remove the dross and burrs that are a product of laser cutting, we put parts through a process called deburring. It’s worth noting that all parts that we make are deburred for free as part of our standard offering. Deburring sheet metal parts not only smooths edges, but it also reduces risk of injury. Here are some other finishing options available to take your part a step further than deburring.

Orbital Sanding
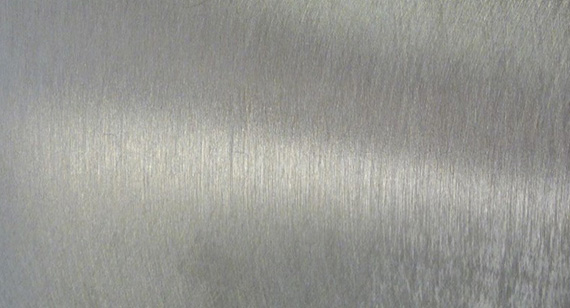
Swing Arm

Straight Grain/Stroke Sand

Standard Mill

Long-life Finishes
The most common application used to help strengthen and or prevent corrosion on sheet metal parts is plating. Passivation is another, but in a different way that we’ll talk about in a second.
Plating is used to harden sheet metal parts and prevents corrosion by adding a thin layer of another metal, like chromate or zinc. Plating is most used with aluminum and may be particularly useful during field testing.
It’s worth mentioning that we do offer pre-plated steels such as galvanized and galvanneal that arrive from the mill pre-coated. We won’t apply additional coatings to parts made with those two materials, but we will deburr pre-plated parts after lasering. This removes the coating on the edges around the perimeter, cutouts, and holes. The remaining part profile will keep the coating. This could be a low-cost alternative.
Protolabs offers the following five plating options for sheet metal parts:
- Anodizing, to prevent scratches and dents and improve aesthetics
- Block oxide, to prevent corrosion and reduce light reflection
- Chromate, to minimize wear and friction and improve aesthetics
- Tin, to protect against water damage
- Zinc, to protect against water damage
Passivation is a cleaning process that limits corrosion and rust on stainless steel parts by removing or limiting traces of contamination caused by the presence of susceptible elements. Citric acid is used to remove these and basically wash them away. While it’s not a 100% perfect solution, it is recommended for all stainless steel sheet metal parts that must withstand extreme conditions.
Cosmetic Finishing Options
For production-grade parts most used for end-use products, customer facing components, tradeshow demo units, or production requirements validation, we recommend the following aesthetic finishing options: powder coating, silk screening.
The application of powder coat creates a hard finish on metal that is tougher than traditional wet paint. It’s unique dry-finishing process is created by an electric charge that causes applied powder to fuse to a metal surface. The part then cures in an oven to achieve a smooth, hard finish. The advantage of powder coating is that it allows for a textured or non-textured color finish in more than 50 colors, including popular RAL colors to meet customer specifications. It also can provide a layer of protection against scratches/chipping and some corrosion.
Silk screening is often used to apply design elements such as company logos, safety warnings, labels, and other graphics directly onto the part. Protolabs silk screening service allows for custom coloring mixed closely to match Pantone numbers. That’s helpful for any internal art department trying to match its company brand guidelines.
Part applications best suited for powder coat and silk screening include:
- Faceplates
- Signs
- Panels
- Customer-facing enclosures

A Note About Silk Screening at Protolabs
Protolabs strives for industry-leading quality and on-time delivery targets. Our silk screening process has been designed to yield a high-quality result and make your logo/branding stand out while showcasing your new product to a stakeholder or potential investor.
The key is to use vector graphics tools when creating your logo instead of raster graphics. Raster graphics are not made to be resized, so they typically generate a more pixelated image. This lessens the accuracy of the logo when applied to the surface of your sheet metal part. Vector graphics are highly compatible with the Protolabs screen creation process and deliver the high-quality branded finish you need.
If the file has been designed using rasterizing tools, it could delay shipment timing.
That about sums up the many options for finishing your sheet metal parts, but if you have any more questions our engineering team is standing by to help you with your next project!