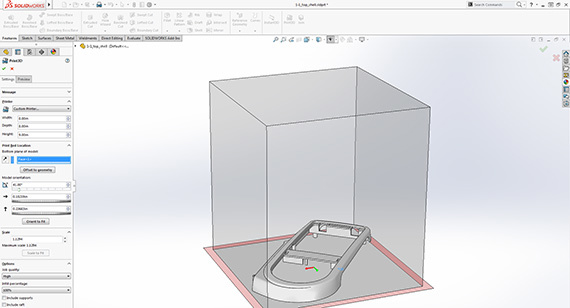
Our blog series on designing for manufacturability in SOLIDWORKS has already looked at tips for injection molding and CNC machining, and concludes now with a look at additive manufacturing, or 3D printing as it’s more commonly known.
This technology is really the new kid on the block when it comes to making things. Originally only used for prototyping, the design “rules” were not really considered as parts that were 3D printed were designed for a completely different process and often just a quick way to get a physical representation. As the patents for 3D printing expired starting in 2013, the flood of new market entrants and huge acquisitions has spiked interest in using it for production.
However, there are significant variations in processes, materials, manufacturers and, therefore, capabilities. The design rules for 3D printing are really still being developed, but there are some key design considerations that you could—and should—be checking before sending them to be 3D printed.
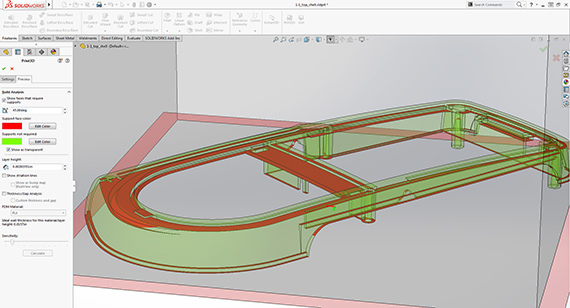
Wall and Feature Thickness
Regardless of which additive process you use, if your part’s walls are too thin or its gaps so small that they fall below the resolution of the printer, they will not be printed as desired. The values of each depend on what material, process, and even in some case, the settings used on the machine for that build.
Support Structures
Another consideration when designing for 3D printing are the support structures. Not all additive processes require supports, but for the ones that do, it is something you should be thinking about whilst designing your components. Supports are often times the same material as the part. This may be fine when it is a low-cost polymer, but if you want a Ti 6-4 Titanium component, you don’t want loads of support structures being built only to be cut off and thrown away. More supports also usually mean more build time (and potential cost) and who wants that?
SOLIDWORKS can check your designs for all of these things so you know any features likely to have undesirable results. To run these checks, go to File > Print3D. You’ll find it beneath the 2D print option.
In order to run the checks, you need to enter the build envelope size of your printer, or the printer you are going to use so you know it fits. You also need to choose the build orientation. Then to check the manufacturability, go to the Preview Tab. On the Preview tab, you can highlight any faces requiring support material. Using the Show as Transparent option makes it easier to see those faces without rotating to a bottom-up view.
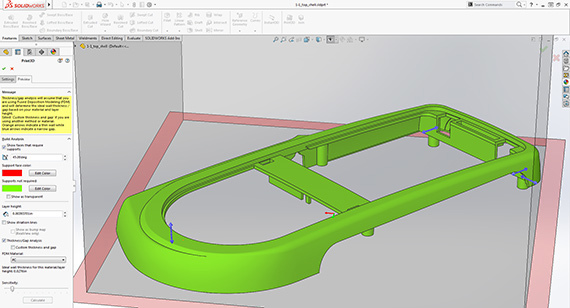
Thickness/Gap Analysis
The most important check for additive manufacturing is the Thickness/Gap analysis. Built into SOLIDWORKS are some recommended values for the FDM process based on the layer thickness the printer is set to. For all other processes, check the Custom thickness and gap box and enter the minimum thickness/gap that is achievable by the process you are going to use.
Thin walls are highlighted with orange arrows and thin gaps with blue ones. These checks are particularly useful when you have scaled down the part as it is easy to overlook the fact that walls thickness reduces by the scale amount.
Even if you know the design for manufacture rules for all of these processes, there are still times when running a quick check can save a lot of time and cost. As designs become more complex, it is not always obvious were rules may have been broken in order to achieve the functionality or aesthetics required. A couple of clicks upfront in SOLIDWORKS can definitely make a difference.
Want to know more about 3D printing? Check out solidworks.com/am for a range of resources to help understand the pros and cons of the current available technologies.
About the Author
Mark Rushton is a product portfolio manager for SOLIDWORKS, in the Desktop products team, focused on additive manufacturing. He has been involved with 3D CAD and 3D printing for over 15 years in several capacities from research to consulting for the likes of Rolls Royce, GE, JCB, and Dyson.