Manufacturers have plenty of materials to choose from when designing parts, but among the most popular and widely used, especially in the medical industry, is liquid silicone rubber (LSR), more commonly and somewhat inaccurately referred to as silicone. That’s because this versatile material is durable yet flexible, soft to the touch, and above all, biocompatible (assuming it’s a medical-grade LSR). For many, it’s the first choice for a wide variety of components.
We’ll dive more deeply into the specifics of LSR shortly, but top of mind for many designers is whether they should plan on plastic injection molding their silicone parts or possibly 3D printing them.
As with so many other manufacturing-related questions, the answer depends on numerous factors, among them production quantity, part geometry, desired accuracy and surface finish requirements, and more. As you’ll see, True Silicone printing has only recently become a reality, with practically all parts (until now) made of elastomers, such as molded TPE, TPU, and LSR materials or 3D-printed TPUs and digital photopolymers.
In this article, we’ll explore the pros and cons of each manufacturing approach, compare the materials available, and attempt to provide some guidance as to which process and materials make the most sense for a given application. We’ll also introduce a relative newcomer to the 3D printing world known as silicone additive manufacturing, or SAM, and offer some information on its use. Read on.

Liquid silicone rubber parts can be translucent, replacing glass in applications where safety is a concern.
Why is LSR a Go-to Material for Medical Applications?
In the medical sector, LSR is especially ubiquitous. Thanks to its flexibility, resistance to heat and chemicals, and biocompatibility, medical-grade silicone has long been used for prosthetic devices such as breast and ear implants, as well as orthotics like braces and arch supports. LSR is usually the first choice for intravenous tubing, catheters and shunts, syringes, breathing tubes, and insulin pumps. Wound dressings frequently contain silicone, as do the valve seals and gaskets in medical equipment. Silicone rubber is also quite suitable for wearables and other consumer products—watch bands, for instance, or the soft, squishy covers seen on earbuds and hearing aids. It’s everywhere.
What separates medical-grade LSR from other types of silicone? Not much. The primary difference comes down to how the material is cured during or immediately after the manufacturing process. For instance, commercial LSR uses hydrogen peroxide and high temperatures to permanently cross-link silicone’s polymer chains, which leaves behind acid residues and other by-products that may cause it to fail biocompatibility testing.
Medical LSR, on the other hand, relies on a platinum-based catalyst to cure the LSR, followed by a secondary “baking” or UV-light treatment (depending on the application). This procedure eliminates harmful by-products and makes the product safe for use on, in, or around the human body, although sterilization is still required for most applications.
That last statement is critical. Medical device manufacturers must specify the type of human contact and how long their products will be used if they’re to gain FDA approval. Direct contact is exactly what its name describes but is further defined as limited, prolonged, or permanent. There are also indirect, transient, and non-contact usage levels, all of which are outlined under ISO 10993-1: 2018 and other international standards.
Comparing Silicone and Thermoplastic Options
There’s much more to the science of LSR and the qualification steps necessary for any medical part development project, whatever the materials. For now, though, let’s discuss the manufacturing process. As indicated earlier, plastic injection molding is the most common method for making LSR parts, and for good reason. It’s fast, accurate, capable of producing the fine finishes common to medical parts, and very cost-effective in higher production quantities. And there’s the rub.
Still, some medical device firms would prefer to 3D print their prototype and low-volume production parts. Who can blame them? Additive manufacturing (AM) delivers high-quality, end-use components in days and sometimes hours, allowing designers to make multiple design iterations quickly. It also provides greater design freedom than traditional processes, with none of the concerns over flash, voids, and part ejection that can occur with injection molding.
There’s just one thing: LSR is a problem child for most 3D printing technologies. Between its relatively high viscosity and somewhat finicky curing requirements, accurate layer-by-layer deposition has proven difficult to achieve.
LSR vs. TPE vs. TPU
Property |
LSR |
TPE |
TPU |
Biocompatibility |
Excellent |
Good |
Good |
Chemical Resistance |
Excellent |
Good |
Excellent |
Durability |
Excellent |
Good |
Excellent |
Flexibility |
Excellent |
Good |
Good |
Temperature Resistance |
Excellent |
Good |
Excellent |
Toxicity |
Very low |
Low |
Low |
It's for this reason that manufacturers have turned to silicone-like polymers such as thermoplastic polyurethane (TPU) and thermoplastic elastomer (TPE) as alternatives to LSR. There are also several proprietary stereolithography resins available that mimic silicone’s properties and, like TPE and TPU, are much less expensive than LSR. All these materials come close in terms of flexibility, tear strength, biocompatibility, and other medically desirable properties, but they are not LSR.
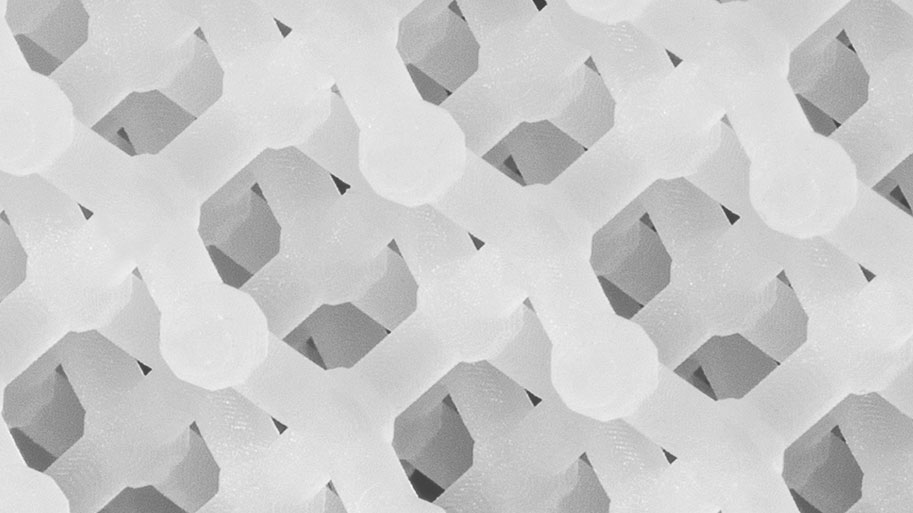
The molecular structure of 3D-printed silicone parts, like the one in the image above, share the same mechanical properties as LSR molded parts.
3D-Printed Silicone and its Benefits
Before discussing the one viable option for true 3D-printed LSR, it’s important to point out an alternative, which is to 3D-print tools for LSR molding. Doing so eliminates the need for “hard” molds and, since they can often be produced more quickly than molds machined out of aluminum, are an attractive option. Buyers should be aware, however, that these soft tools are just that—softer than metal—and therefore offer limited accuracy and production life.
Which brings us to SAM, short for silicone additive manufacturing. Developed by Spectroplast AG of Switzerland, SAM is the only 3D printing technology able to build parts from medical-grade silicone, which the company has dubbed TrueSil. It provides excellent feature detail and surface finish, with resolution and geometric freedom comparable to that of conventional stereolithography.
According to the manufacturer, SAM is a light-based system that cures a full layer of silicone parts in a single exposure. This means the number of parts does not affect print time as with competing systems, and by packing parts more densely on the build plate, production costs are often lower than other 3D printing processes. Part sizes are currently limited to "about the size of a smartphone," although the company will soon introduce a machine with a significantly larger footprint.
We offer SAM’s game-changing capabilities as part of our 3D printing offerings. We can produce silicone components in translucent white and black with durometers ranging from 20-60A, comparable to injection-molded LSR parts.
3D-Printed Silicone vs. LSR
|
Shore A Hardness |
Tensile Strength |
Elongation in % |
Tear Strength |
3D-Printed Silicone |
20A |
623.7 psi (4.3 MPa) |
815 |
33.1 lbf/in (5.8 N/mm) |
35A |
1,508.1 psi (10.4 MPa) |
1,000 |
58.2 lbf/in (10.2 N/mm) |
|
50A |
1,290.8 psi (8.9 MPa) |
650 |
57.1 lbf/in (10 N/mm) |
|
60A |
1,363.4 psi (9.4 MPa) |
360 |
85.7 lbf/in (15 N/mm) |
|
LSR |
51A |
1,200 psi (8.3 MPa) |
500 |
271 lbf/in (47.5 N/mm) |
Table source for 3D-printed silicone data: Spectroplast.com
SAM is also said to generate smoother finishes than competing AM technologies. For example, parts made from TPU using selective laser sintering (SLS) have a somewhat rough texture like a sugar cube, and are limited to white, although they do boast excellent biocompatibility.
Polyjet, on the other hand, generates smooth finishes, albeit not as fine and layer-free as seen with SAM parts. It also offers color choices and durometer levels not unlike those available with SAM, but the digital photopolymers are only suitable for prototyping and form/fit/function testing, as they are not deemed biocompatible. It should be noted that these alternative materials are less expensive than LSR, which might be a significant concern at higher production volumes or with large, bulky parts.
Designing Silicone Parts for Manufacturability
So, which is the best choice for your medical application—injection-molded LSR parts, or ones that are 3D-printed with SAM? As stated at the outset, the answer depends on numerous factors, but the good news is that product designers looking for the quickest turnaround possible no longer need to rely on alternative polymers that might not offer the same level of performance or part quality.
But even the most robust material will fail if the designer doesn’t follow the recommended guidelines for the intended manufacturing process. In SAM’s case, these are like most 3D printing technologies, with the chief concern being the need for temporary support structures to prevent curling and deformation on horizontal or near-horizontal surfaces. Tall, skinny walls can also be problematic, as are holes under 0.040 in. (1mm) or so in diameter, particularly those with long aspect ratios.
Injection-molding LSR is fairly straightforward, although it is distinctly different than “regular” thermoplastic molding. The material flows freely, so thin walls are typically not a concern as with plastics like polyamide (nylon) and PEEK. Nor is “sink” (caused by overly thick sections) a problem, although flash at parting lines occurs more readily with LSR. Also be aware that LSR does not like sharp edges, which means that delicate parts especially can tear during removal from the mold, so internal corners should be rounded. Thanks to its flexibility, though, moderate undercuts and "bump off" features are easy to accommodate, and designers will be happy to know that injection-molded LSR can be made into a virtual rainbow of colors.

Injection molding LSR for complex parts requires consideration of how to maximize flow and avoid thick areas that could sink or warp.
Moving from Silicone 3D Printing to Injection Molding
This is admittedly a 30,000-foot view of the best practices for each of these processes, which is why many online service bureaus provide manufacturability analyses to potential customers. What they might not tell medical part developers, however, is to avoid painting themselves into a 3D-printed corner. Silicone injection molding has few design constraints, but it does not compare to the freedom that comes with 3D printing.
Moving from 3D printing to another process, such as injection molding, means being cognizant that your designs must still follow the design for manufacturing rules for that other process. For example, designers might prototype a part using SAM or one of the other AM technologies mentioned earlier, only to find their parts are not moldable once they’re ready to enter the high-volume commercial market. The message is clear: always evaluate designs for manufacturability at all stages of the product lifecycle, and always discuss plans with your manufacturing partner early on. Doing so can avoid an expensive lesson later.
Manufacturing considerations aside, it’s an exciting time for any medical device designer who wants to take advantage of silicone’s many desirable qualities. Whether 3D-printed or injection-molded, this important elastomer repels water, has low thermal and electrical conductivity, is resistant to ultraviolet light, radiation, oxygen, and most chemicals, and—grade permitting—can be used safely for years and years within the human body. And thanks to the continuous forward march of advanced manufacturing, silicone can now be used to 3D-print a wide range of cost-effective medical parts boasting the fine finishes and accuracy normally associated with injection molding.

If you have any issues getting your guide, click here to download.

Need custom parts? Upload a 3D CAD file to get an online quote.
Get Printed Parts