Fillets vs. Chamfers: How to Handle Edges and Corners in CNC Machining Design
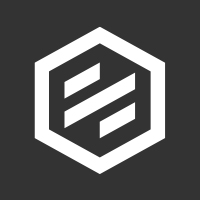
The crisp, sharp edges in 3D models don’t always translate well to the real world and real-world objects. Rounded corners and edges are easier on the eyes, according to experts. They also make parts and products easier to handle—and (arguably) safer.
A newly machined metal part can end up with edges that are sharper than desired for the end user unless the design smooths or breaks those sharp edges. To create an edge break, the design should incorporate sloped or beveled edges and corners known as chamfers—or rounded ones called fillets.
Fillets vs. Chamfers
Understanding the difference between fillets and chamfers can determine whether a part succeeds or fails. Making the right choice also can save machining time, meaning parts will be ready faster and more cost-effectively. Choosing incorrectly may result in a part that doesn’t last long enough. In addition to smoothing sharp edges, fillets and chamfers reduce stress on a finished part while adding aesthetic appeal.
Some people may use the terms fillet and chamfer interchangeably, but chamfers and fillets are different, and each has its own functional and design considerations. To get an idea of the difference, picture it this way: the beveled, 45-degree edge of a laptop computer is an example of a chamfer while the typically rounded edges of computer mouse or a desk or table are examples of fillets.
A rule of thumb for deciding which to choose is to favor fillets for anything handheld, so you can avoid sharp edges of frequently handled objects. Use chamfers for hidden parts, those that go inside an assembly or finished product.
What is a Fillet?
A fillet is a rounded edge or corner of a part. Fillets help to reduce stress and distribute it over a larger surface, improving load-bearing capacity and helping to prevent rapid deformation of a stressed part. A concave fillet is on the interior of a part while a convex fillet is on the exterior. Fillets also can create transitions between features when, for example, a vertical wall meets an angled surface within a part.

Designing fillets for every edge break on a part, however, would drive up the cost of that part. That’s because it would require using a specialty tool and a more time-intensive 3D milling process, with a ball endmill performing simultaneous x-, y- and z-axis movements, gradually removing material at increments of just 0.010 to 0.020 in. (0.254 to 0.508mm) at a time.
That’s in part why when a basic edge break is all a part needs, a chamfer may be the answer.
What is a Chamfer?
A chamfer refers to a flat, sloped edge or corner, also known as a bevel. A single tool can create chamfers of different sizes, so a design can include them without increasing the part’s manufacturing time and cost. Chamfers do provide stress resistance but over a lesser surface area so overall, their stress resistance is less than fillets.
To eliminate sharp, raw or semi-raw cut metal edges, a chamfer with a 0.010 in. (0.254mm) edge break at a 45-degree angle makes sense in many cases. For a part that will have other parts attached with screws, a 60-degree chamfer on the edge of the holes will serve as a lead-in for the screw and allow the head of the screw to sit flush with the part surface.
Aside from rare cases where a part requires a knife edge, we offer edge breaks on CNC-machined parts as a complementary service. But knowing more about fillets and chamfers can make for better, more intentional design choices that will deliver on performance, cost, or other considerations for a project.