Hacksmith Brings Marvel’s Hulkbuster to Life with a Helping Hand from Protolabs
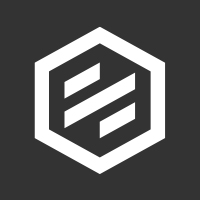
Much to the delight of their 12.4 million YouTube subscribers, the innovative minds at Hacksmith are at it again, bringing fictional items featured in film, video games, and comics to life through iterative design and inventive engineering. We sat down with co-founder and COO, Ian Hillier, to chat about Hacksmith’s humble beginnings, its latest Hulkbuster project (which we were psyched to assist with for 3D-printed components), and what’s next for the creative crew.
Building Hacksmith from the Ground Up
James Hobson, co-founder and the original "Hacksmith,” started building things and recording video footage of the process back in 2006 to share with friends. James and Ian went to high school together and joined the school’s robotics club, winning a 2007 Canadian national robotics championship. One of their first notable projects was converting an old Honda Del Sol to electric using forklift components.
After college, the duo’s calling to continue engineering manifested in an entrepreneurial endeavor. James’ dedication to uploading weekly YouTube videos was paying off and the channel grew to 60,000 subscribers. “James quit his full-time job to focus on his YouTube channel, uploading videos of cool engineering projects and making zero money doing it. Naturally, I joined him,” Hillier said.
With six months of savings and a core motivation to inspire the next generation of engineers, Ian joined forces with James and continued to grow their channel. “The Captain America shield video that we made went viral, which is one of the main reasons we’re here today. After that, sponsors came in right at the six-month mark. Since then, we’ve been continuously growing the team, expanding our abilities, adding partners and it’s exploded from there.”
Hacksmith x Protolabs = HULK SMASH!
We’re no stranger to Hacksmith’s tech-driven creations. We created parts for two previous projects: the Infinity Blade from Marvel’s “Avengers: Endgame” movie and a 3D printed metal grappling hook from The Mandalorian series. This time around, Hacksmith approached us to 3D print four nylon pieces for a new and improved Hulkbuster Punching Fist.
“For this project, both the aesthetics and the overall strength are very important,” Hillier said. “Normally, I’d use a fused deposition modeling (FDM) printer that I have, but there are certain limitations with those. I wanted to go with SLS [selective laser sintering], which I don’t have the ability to do in-house, so Protolabs was the obvious choice.”

The Hulkbuster Punching Fist is a new and improved Ironman version of one the team created a couple of years ago. According to Hillier, the first version was too heavy and didn’t punch fast enough due to its six pneumatic cylinders, which prevented adequate air from circulating fast enough. The goal for Hulkbuster 2.0? To match the impressive 300 punches per minute as showcased in the movie. “We figured, let’s put some better engineering in this and we can make it even faster,” said Hillier. Hulkbuster 2.0 averages about 350 punches per minute, packing a faster and even bigger punch.
Breaking Down the Technical Design
In the design phase, team Hacksmith started thinking through the general Hulkbuster architecture and how to fit all necessary components into something to hold onto with one hand. “I wanted to use a motor but fitting a mechanism in that tight of a space wasn’t working. I went back to pneumatics and considered what valves do I need to make this as fast as possible,” Hillier explained. There are carbon dioxide (CO2) cylinders in the arm piece that powers it. After quite a bit of prototyping and experimentation, it was back to SolidWorks to fine-tune the aesthetics.

Function > Beauty
Creating pieces that match the scale of those in movies while robust enough for real-world application is no easy feat. “We focus more on functionality over aesthetics. There are other creators out there that make props that look exactly like they do in the movie, but they won’t work. For us, functionality is the most important thing,” said Hillier.
How does the team pick and choose which projects to bring to life? “We have a million ideas for projects but following through is the hard part. We get to do the fun part of engineering: the prototype phase. Other companies have to worry about logistics, supply chain and large quantities, but we just need to make a cool prototype.”
The Hacksmith crew has seen impressive growth over the last few years, both on their team and in their evolving capabilities. “We just recently celebrated our six-year business anniversary, which is surreal,” Hillier said. The team now has 22 employees, including a retail team that sells Hacksmith merch. With a slew of projects in the works and a potential facility relocation, fans can expect more exciting engineering marvels in the future.