How Data-driven Manufacturing Unlocks Speed and Transparency during Injection Molding Process
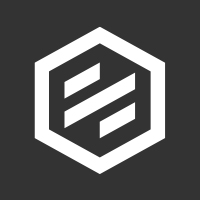
A global pandemic. Economic disarray. Material shortages. What’s next, a plague of locusts? Oh yeah, we had those in the Mid-Atlantic in summer 2021, too (well, cicadas, anyway). All of those—except the locusts—have had a major effect on supply chains and the way companies do business. Because of this, manufacturing speed and quality have become even more critical for engineers and product developers in need of molded parts. That’s when digital manufacturing can really help.

Injection Molding Quotes and Consultative Design Service
Let’s start just after you upload a 3D CAD model. In addition to automated feedback that highlights design modifications to improve manufacturability, sometimes, designs require the nuance that comes from deep knowledge of the equipment and materials that will be used to mold your part. Finding a supplier that offers those insights is important, and a real time-saver. We call it our Consultative Design Service (CDS). For example, if you’re not sure about the best draft angles for your part, our applications engineers can assist with helpful advice to ensure that your models are further designed for manufacturability. It’s a one-two punch—AI analysis complemented by human expertise. From there, quoting is typically a breeze…but you have another option to help get accurate, consistent parts.

Improving Part Outcomes with Critical-to-Quality Specs
Many of the parts we manufacture have at least one measurement that’s mission critical. Maybe the parts won’t work in an assembly unless a planned hole is within spec. Typical CAD models provide an opportunity to include specific dimensions, but what if you could tell your manufacturer early-on that dimension X is the one that makes or breaks a part? That’s where Critical-to-Quality (CTQ) comes in.
The CTQ specifications that you include in your quote and CAD model help to guide us during manufacturing, saving another critical dimension: TIME. We can often tell you if it’s possible for us to make your part before the mold is cut.
CTQ is also an important element of our digital manufacturing processes because we use these specs to evaluate initial runs of your parts. Let’s say that your parts require sample qualification or part validation. CTQ becomes even more crucial at that point because the data that flows from those initial shots can predict the future tolerances for those critical dimensions, revealing the suitability of end-use parts for a given assembly.
I bet you’re worried that all these verifications will slow down lead times, but here’s the thing. While those measurements do take a while to do when they are done by hand, digital manufacturing uses technology to speed processing. To get around the time factor, we have inline Coordinate-measuring Machines (CMMs) that automate the process—another huge timesaver.

Scientific Molding and Validation
With every part we manufacture, we collect tons of data and that enhances our ability to predict outcomes. Using automated data collection and evaluation to ensure manufacturing repeatability is the premise behind scientific molding. If we’re confronted with a complex geometry, or other challenging specifications, we can look back and see what processes have succeeded in the past and repeat those steps. It’s all in the database. In some shops, that task comes down to the collective memory of an individual or group, but with true scientific molding in a digital manufacturing environment, computers handle most of it, and provide instantaneous solutions.
Beyond helping design for manufacturability, having each step documented makes validation a snap, and consistency a given.
Injection Molding in the Future
As Industry 4.0 tells us, data-driven manufacturing IS the future, and the process of injection molding is no exception. Partnering with a digital manufacturer can quickly guide you through tough design questions and give you another competitive edge in an increasingly competitive business climate.