What is NPI Manufacturing? New Product Introduction Explained.
A recent Nike ad talks about how the global sneaker and apparel company creates new shoe products through “continuous refinement…Use, observe, design, build, test, fail, repeat.”
That description nicely portrays the build-test-iterate process of what many of our agile engineering and product design customers use to quickly develop new products to address market needs. They do it through the process of New Product Introduction (NPI), also sometimes called New Product Development (NPD).
We work with folks in a wide range of industries because the various stages of product development are really all about speed. How you can build things faster, make the right parts faster, gain customer feedback as you are developing your early ideas, and then turn around and make more iterations of the product—again, faster. Our digital manufacturing methods deliver that speed, which we explore in more detail in our trend report on developing a product strategy. Concurrent with that speed, our customers also want high quality control and standards along with quality inspection systems that are in place throughout the prototyping and production processes.
This blog post explores what NPI is, and the process involved in developing, refining, testing, validating, and launching a new product to market.
What is NPI in manufacturing?
New Product Introduction (NPI) or New Product Development (NPD) is a process for creating a plan to take a product from early concept to final, go-to-market form.
The process starts with early research and market data related to a particular product idea or need, then moves into proof-of-concept prototyping. Following that, design and engineering phases occur concurrently. Then comes validation or verification testing, production validation, quality testing, and finally a ramp up to mass production.
NPI and NPD are terms used in most, if not all, industries to describe or define this process in some form. The level of depth in certain industries will vary. For example, the medical, aerospace, and automotive industries will go deeper into the verification steps because of industry compliance requirements and the complexity of products being produced. Let’s look at these steps, one by one.

Research, Market Data, and a Business Plan: An NPI Prequel
Even before the NPI or NPD process gets underway, a company will first seek to understand and identify what problem customers want solved. The needs of customers—the end users—are more closely examined at this stage. Then, the company will conduct research and review market data that is related to whether a new product or idea is needed or viable.
Based on that research, a product manager, general manager, or potentially a founder of a startup company, will do an initial proposal that eventually takes the form of a business plan, which then gets approval to move forward.
Proving and Defining Key Concepts, Feasibility for NPI
The research and business plan will lead to this starting point, a proof-of-concept prototype. Here, the company is assessing whether the product idea is feasible. A CAD software model shows the product concept and its components. The actual, physical manufacturing and materials at this stage are strictly for prototyping: cardboard, foam, duct tape, and, in some cases, desktop 3D printing.
Design and Engineering Development
Design and engineering work concurrently during this stage using rapid prototyping—aided by the speed of digital manufacturing, of course—to develop two kinds of concepts. The design concept is the “looks like” prototype, focusing on its look and commercial appeal, looking also at cost, lead times, and manufacturability. The engineering concept is the “works like” prototype, focusing on product functionality and how it will work. Alpha testing is conducted now. At this stage, 3D printing (aka additive manufacturing), sheet metal fabrication, or CNC machining are used to create prototypes.

An engineer checks settings on his CNC mill prior to machining a part.
Engineering Validation Testing (EVT) for NPI
This is where injection molding comes into play, as the “looks like” and the “works like” prototypes are combined, using final end-use, production material. Important decisions are made at this stage, such as what material will be used for the product and which manufacturing process will be used, which is dependent on the quantity required. For example, if only 100 are needed, 3D printing might work just fine, but if thousands are needed, then molding is likely used. This stage is also where product developers use the design for manufacturability (DFM) process that helps validate the engineering aspects of the product and helps review cost tradeoffs. At this phase, developers can do iteration to validate and test different configurations, materials, and so on.
Design Validation Testing (DVT) for NPI
This stage is where all the design specifications are validated, looking again at the customers’ needs. This DVT step makes sure that the final product meets the requirements defined early in the process. At this point, iterations are completed, design is ready for production, and the configuration is locked up. In addition, a quality engineering aspect is included in this process, which involves the usual quality checkmarks: first article inspection, quality documentation, quality audits, and so on. And, though quality engineering is mentioned here in this section, it is, in fact, an element that is woven throughout this entire process.
Production Validation Testing (PVT) for NPI
An important step, PVT involves verifying mass production yields with one, near-final, production-worthy design. This is all about scaling. We are getting close to ramping up for final production, transferring from prototyping to production. In other words, this process involves working through the “boxes” that need to be checked off before going into production.
Ramping Up to Mass Production
Essentially, this is a final step. It’s a last look at things before launching to market with mass production of the product. As a digital, on-demand manufacturer, we can help with that ramp up, too. With us, you can procure parts on demand, without minimum order quantities (MOQs). This concept of manufacturing on demand helps you manage market volatility, so you’re not tied to massive production forecasts. When demand spikes, you can get parts quickly, avoiding the risk of lost sales opportunities because of stock outages or long lead times. Along these lines, on-demand sourcing also lowers overall inventory cost and warehousing expenses.
As noted, this NPI or NPD process is deployed in most industries for the designing and building and launching of new products. Further, the key to a successful NPI process is speed, which enables rapid prototyping as engineers and product designers move through the process.
For questions about how our digital manufacturing services at Protolabs can help with your NPI needs, or questions about any of our services at Protolabs, please contact an applications engineer at customerservice@protolabs.com or 877-479-3680.
Gurvinder Singh is Protolabs’ global product director for injection molding.

If you have any issues getting your guide, click here to download.
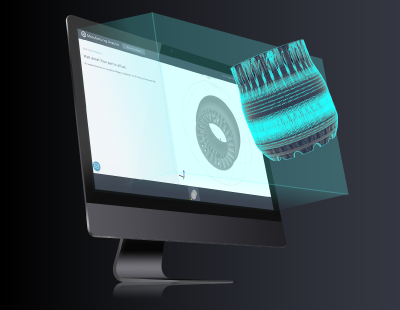
Need custom 3D-printed parts? Upload your CAD file for an instant online quote.
Get Printed Parts