Additive manufacturing (AM) for metals has seen rapid growth over the past decade, especially in the direct metal laser sintering (DMLS) sector where just about every industry has found a place in which additive manufacturing makes sense. Prototypes, production parts, mold components, and one-off custom parts that are only possible with AM are built daily on these machines.
Every day we see headlines showcasing certification of new materials, finer print details accomplished, and larger build sizes, but we rarely see much about the other post-processing side of metal AM. There aren’t a lot of people talking about de-powdering, heat treating, stress relieving, finish machining, polishing, and sometimes the most overlooked of all—cutting parts from the build plate.

Removing Printed Parts from Build Plates
Let’s face it: Cutting off a build plate is one of the most boring and overlooked parts of the metal 3D printing process, but it’s critically important that it be done quickly and efficiently the first time so it doesn’t add unneeded costs. This seemingly simple process has become increasingly challenging in recent years. Printers are faster than ever, but they are printing parts in materials that are harder and harder to cut from the build platforms. Sometimes, build platform sizes are too large for readily available cutoff methods. We identified this pending problem and began searching for a better solution for the issue, which came in the form of EDM Performance Accessories’ HB series molybdenum wire EDMs. EDM stands for electrical discharge machining, and goes by other names, such as spark machining, spark eroding, die sinking, wire burning, or wire erosion. EDM erodes materials using repetitive sparks between the platform and the molybdenum wire in contact with a dielectric fluid.
EDM Solves for Scale
With our fleet of GE Additive Concept Laser M2s, and the recent purchase of two Concept Laser X Line 2000R printers, we needed to manage capacity and have the ability work with parts as large as 31.5 in. by 15.75 in. by 19.69 in. (800mm by 400mm by 500mm). The HB800 EDM handles all three dimensions without issue, yet still works with smaller builds. Another consideration was accuracy. Traditional bandsaws are fine for our large-format aluminum parts but are not ideal for cutting harder ones, printed in Inconel. Using molybdenum EDM technology, the HB series EDM was able to complete test cutoffs of both steel and Inconel materials at only 0.005 in. (0.127mm) off the build plate surface and cutting only a 0.008 in. (0.203mm) kerf or gap through the part.

A dielectric fluid is used to keep the electrical current flowing through the cutting wire while not dissipating it in the liquid.
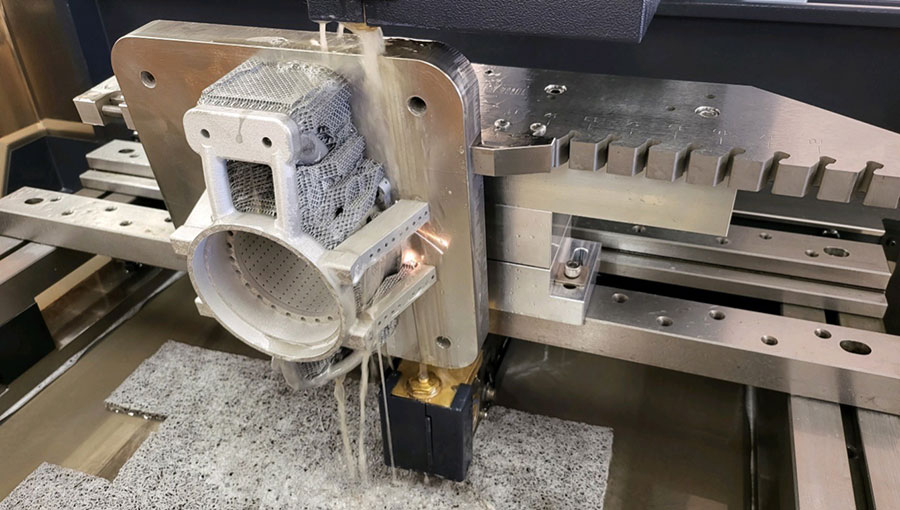
Sparks reveal the location of the molybdenum wire as it cuts through the support structure.
Brass vs. Molybdenum Wire: Reducing Speed and Cost
After size and capacity, we had to consider speed and cost. Our goal is to provide customers with quick-turn prototypes and end-use parts at price points most small or large companies can use. To assess cutting speed, we compared a traditional challenging part on both our existing brass wire EDM machine and our HB series EDM. The brass EDM averaged a 7-8 hour cut off time on this steel valve body. This part had many small support pieces that could break loose during cutting, causing wire breaks and delays. It also has large variations in cut thickness. These are less than ideal conditions for efficient EDM cutting. Fast wire molybdenum EDM, however, works using a much different method than brass EDM. The wire runs at nearly 40 feet (12.2m) per second on the HB machine creating a “flushing” effect through the part to speed material removal. The wire has double the tensile strength and nearly 3x the melting point of brass EDM wire, too. These two features allowed for a completely error-proof cutoff and no loss in speed or delays from breaks. In the end, the molybdenum EDM shaved off six hours of processing time.

This entire cut of a stainless steel DMLS part from the build platform was achieved in only 44 minutes.
Still, there is no sense in investing in a new technology if it won’t directly help customers. Not only does the molybdenum EDM cost less to purchase, but because it runs faster and has few moving parts or expensive chillers, it reduces costs that are factored into quotes. The combination of decreased cycle times and reduced machine operating cost lowered process costs by 80-90% overall for the two years we’ve worked with these machines. Ultimately, these savings carry over to the customer.
Metal parts are never easy to separate from their build plates, but these EDM machines have proven to be great time savers, especially when paired with our large-format GE Additive X Line printers.
Thanks to Clay Olson at EDM Performance Accessories for providing detailed information to support this blog post.

If you have any issues getting your guide, click here to download.
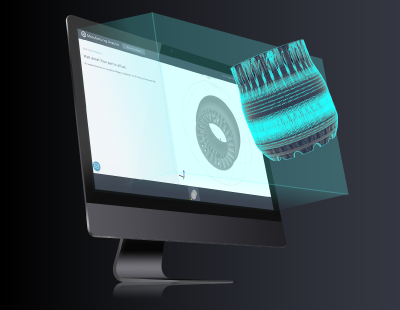
Need custom 3D-printed parts? Upload your CAD file for an instant online quote.
Get Printed Parts