Manufacturing Partnership Helps Fuel College Formula Team Electric Vehicles
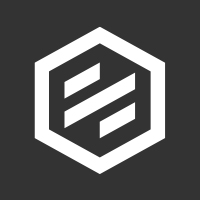
Supporting universities that are making breakthroughs in product innovation is a cause near and dear to us, and we love seeing what the next generation of product designers and engineers are up to!
This year, we teamed up with colleges across the country to sponsor and support university-run teams building an electric or combustion vehicle from scratch as part of nationwide Formula and Supermileage competitions, organized by SAE International. We worked with undergrad students in teams at Berkeley, Northwestern, University of Illinois Urbana – Champaign, and University of Michigan-Dearborn, lending manufacturing grants to fund 3D-printed and CNC-machined parts for their super cool and innovative EVs. Seriously, check these whips out!

But before these teams can race their cars in annual SAE competitions, they need to build their vehicles from the ground up, which is no easy feat. We sat down with Chris Leafstrand, chief mechanical engineer on Berkley’s Formula Electric team to get the scoop on the program, the process of building a fully functioning EV, and working with us on their part needs.
Accelerating Toward an Electric Future
To say that EVs are on pace to win the majority over combustion vehicles soon isn’t an exaggeration. In fact, the EV industry is expected to soar to $5 trillion by 2030, according to Wedbush Securities. Two-thirds of Ford’s commercial vehicle sales are expected to be all-electric or plug-in hybrids by 2030. Digital manufacturing is playing a key role in the booming EV industry, from prototyping in the R&D phase, all the way to assembly line production. With new electric vehicles comes new technologies and new products that didn’t exist with combustion vehicles including battery packs, charging stations, seals and gaskets, and RADAR systems, to name a few. Check out our trend report for the full download on all things EV and AV.
Teaming up with Formula Berkeley
The Formula Berkeley team is comprised of 90 undergraduate members, all dispersed among different vehicle-specific subsector teams including: mechanical, chassis, dynamic, power train, accumulator, programming, high and low voltage, and electrical engineering. “There’s a lot of coordination between the sub teams. They all have these key dynamic interfaces that are really important to make sure we’re on the same page,” said Leafstrand. The team’s workshop is about a 20-min. drive away from campus. The team meets weekly to work on their respective sectors and as often as four to five times per week when gearing up for a new season.
Building the electric vehicle is only the first piece of the puzzle, but the underlying aim is much larger. “Our main goal is rule compliance. One of the biggest hurdles to get through is being able to pass the rigorous technical inspection that every vehicle needs to go through to compete in the dynamic events,” explained Leafstrand. “There’s a weigh in, an accumulator tech inspection, and a tilt test, where they tilt your vehicle 60 degrees to see if it falls over.” Each team must pass every testing checkpoint before they’re given the green light to run in the dynamic racing events.
What else was top of mind when assembling their EV? Manufacturability. “We didn’t have a ton of machine shop access. On campus, we have a laser cutter and a water jet so it’s great for 2D operations, but we didn’t have a lot of 3D access and that’s one reason we love working with Protolabs,” said Leafstrand. “That’s going to be our manufacturing strategy moving forward: to focus on plate and 2D operations in house and to utilize Protolabs for all of those difficult to make parts because that’s what you guys are really good at.”

CNC ASAP
While most of the process went smoothly for team Berkeley, no matter how much planning is done ahead of time, there are bound to be some bumps in the road for a project of this scale. For Leafstrand’s team, time got the best of them, and they were in need of accumulator mounts ASAP for their EV.
“We were in crunch time in the weeks leading up to the competition. A lot of us were working at internships and whatnot. We would have a normal office hours and then drive back to Berkeley for the evening and work on the car until the wee hours of the morning. We had one person who had machine shop access that could run our accumulator mounts on the mill, but we weren’t able to machine steel easily and we didn’t have great material selection, so Protolabs came to the rescue and were able to get us the parts in a really quick turnaround.” The team received their parts five days after uploading their design file.
While the team passed the chassis and accumulator technical inspection, there were a few hiccups that ultimately prevented them from racing this past year.
What was the biggest challenge for the team during this year’s vehicle build? “Manufacturing. We didn’t estimate the overall time everything would take and a lot of times we didn’t design for manufacturability. That’s our big focus going into the next season,” said Leafstrand. Next season, the team hopes to have their vehicle ready by March to give them ample time to test it themselves and run it through a mock-competition.

Work Hard. Play Hard.
Leafstrand’s favorite part about the team is their fun and supportive team culture. Getting to work with other people in the design and manufacturing process is a lot of fun. Advice for those interested in joining in future years? “Run the team like a business. What you learn in our team extends beyond classes or projects where you don’t necessarily get the real-world engineering experience that’s similar to what you’ll be doing after college. There’s plenty of room to grow and shape this team over the next couple of years, so that’s what really excites me.”
Prototype & Production Parts
The parts we manufactured for the Formula university teams aren’t cookie cutter, one-size fits all. We manufactured a variety of different components for both prototyping (mainly 3D printing) and production parts used within the vehicles.
College |
Manufacturing Service(s) Used |
Parts Created |
Type of Vehicle |
Berkeley |
CNC Machining and |
Accumulator mounts |
Electric |
Northwestern |
3D Printing (Multi Jet Fusion) |
Battery cell holders |
Electric |
University of Illinois |
CNC Machining |
Real wheel adapter assembly |
Electric |
University of Michigan-Dearborn |
CNC Machining and 3D Printing |
Machined: front and rear suspension rockers Printed: parts for the intake, plenum, and restrictor in the powertrain system |
Combustion |