Given the many types of plastics available to the design and manufacturing communities, each with unique properties that can differ significantly from their neighbors, it should come as no surprise that finding the best material for an application can be challenging.
Fortunately, there’s no shortage of high-quality materials, and unless you’re operating in extreme environments, a few options often rise to the top for their versatility. Polypropylene (PP) and polyethylene (PE), which encompasses high-density polyethylene (HDPE), low-density polyethylene (LDPE), and linear low-density polyethylene (LLPDE), are similar materials boasting properties that make both a fan favorite across a variety of applications.
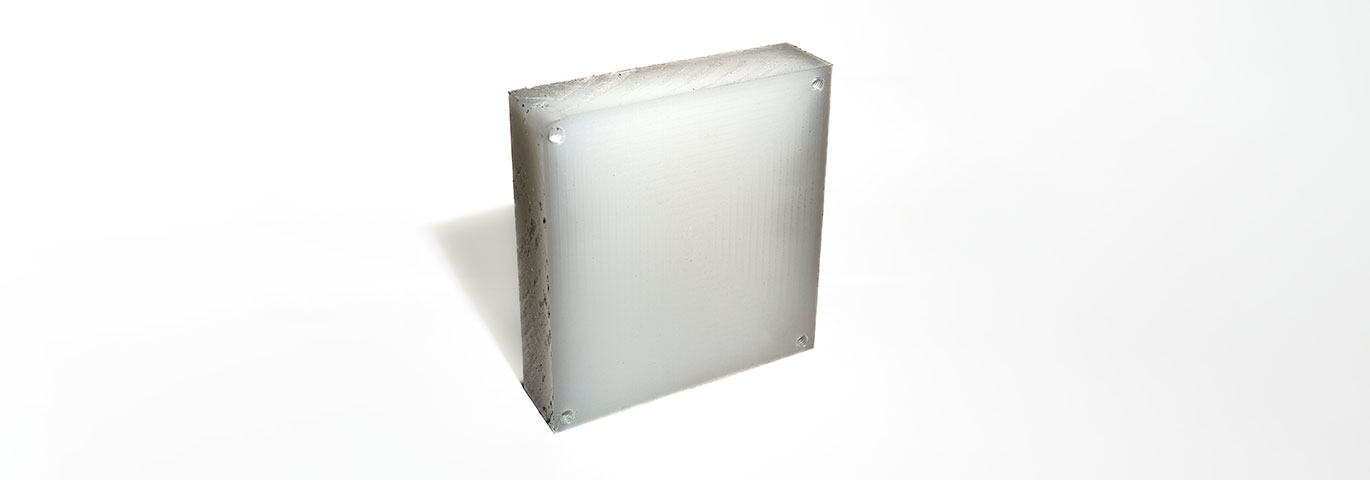
Polypropylene is a lightweight versatile material commonly used for diverse applications like packaging, automotive parts, and electrical components.
Introducing Polypropylene and Polyethylene
We’ll get into the details of each shortly, but in general terms, PP and PE are tough and relatively flexible, electrically insulative, resistant to most chemicals, lightweight, and abundantly cost-effective. Because of this, they see broad use in plumbing pipes and fittings, medical components, a wide range of consumer goods, and much more. For example, the microwavable bowl containing the beef stew you brought for lunch today is almost certainly made of polypropylene, while the bag you carried it in is most likely made of polyethylene.
Thanks in part to the Beatles and their classic song Polythene Pam, polyethylene has become one of the most widely recognized of all polymers. As just noted, it’s often the first choice for plastic bags and many other thin films but also enjoys widespread use in children’s toys, automotive components, electrical and electronic insulators, milk jugs, detergent bottles, and anywhere a lightweight, strong, and thermally-resistant polymer is needed.
While we offer variants of both materials, it’s important to recognize the primary difference between the three classes of PE. Thanks to its higher density and molecular weight, HDPE is more rigid and has a higher tensile strength than LDPE, which is fairly flexible and elastic. And LLDPE, thanks to the linear alignment of its molecular chains, is the most flexible of all and an excellent choice for the “living hinges” found on many containers.
High-density Polyethylene (HDPE) |
|
Low-density Polyethylene (LDPE) |
|
Linear low-density Polyethylene (LLDPE) |
|

Polyethylene comes in multiple densities and is considered sustainable because it can be melted and reused repeatedly.
Differentiating Polypropylene and Polyethylene
While LLDPE can make a great hinge, you know what is even more flexible? Polypropylene. In fact, most grades of PP are the winner of any contest where flexibility and fatigue resistance are the key determinants, which is why this versatile polymer is used to make rope, carpeting, car bumpers, roofing, and numerous other applications that often overlap with the PE family. PP is also more lightweight than PE, a bit stiffer and more chemically resistant (but not by much), a little less sturdy, and a bit less expensive (again, not by much).
Perhaps the most significant differences between PE and PP are their working ranges. Where LDPE has a melting point in the 105-115°C (220-240°F) range, HDPE melts at 130-137°C (266-279°F), and LLDPE sits between the two, PP withstands temperatures up to 160°C (320°F). This makes it more suitable for medical components that must be sterilized. Conversely, PE is more resistant to extreme cold (as low as -80ºC, or -112°F), while PP begins to fail at freezing temperatures.
Other differentiators include:
- LDPE is transparent, and some PE can be made optically clear, but PP is almost always translucent (like the milk jug mentioned a while ago).
- Polyethylene is a better electrical insulator but is prone to electrostatic charge, which is why some grades come with antistatic fill.
- PP is stiffer and more resistant to chemicals and organic solvents than PE.
- PE is more susceptible to UV radiation but can be protected with additives. It’s also more flammable.
- Both are approved by the FDA for use in food applications. Most are also considered medical-grade plastics.
- Polyethylene has better weldability, yet polypropylene is known to have better weld strength.
Manufacturing Polypropylene and Polyethylene
So what about this last part: manufacturability? With one exception, the similarities continue. As with most polymers, PP and PE are eminently machinable. Tool wear is practically nonexistent and cutting forces are low.
And as you might have discerned from the many mentions of jugs, containers, toys, automotive parts, and similar mass-produced consumer items, both plastics are also injection moldable. If you are looking for additional best practices to mold either plastic, visit our Design Tip library.
What we will mention is 3D printability. We offer several grades of PP and PP-like materials for its different 3D printing technologies, but we don't currently have anything directly comparable to PE. This may change when 3D printer manufacturers and/or material suppliers provide friendlier, more printable grades of polyethylene, but until then, PA12 nylon is a robust, cost-effective, and very capable substitute.
Where to Learn More
These are general guidelines, and as suggested at the outset, there can be significant variability between one grade of plastic and another. And in some instances, additives are available that will improve part performance. Check out our material library and read the manufacturer's data sheet for specifics, and when needed, reach out to one of our applications engineers at customerservice@protolabs.com or 877-479-3680.

If you have any issues getting your guide, click here to download.
