The medical field is one of constant innovation. New and evolving 3D printing technologies are enabling efficiencies in surgical procedures, advancing medical devices like implants and prosthetics, and translating patient-specific medical scans into 3D-printed models. Our customers often leverage our services including metal 3D printing, stereolithography (SLA), selective laser sintering (SLS), Carbon DLS, PolyJet, and Multi Jet Fusion (MJF) for diverse healthcare applications.
In 2023 alone, analysts predict a 17% increase in market size for 3D printing with the medical sector a lead driver of momentum. Additive manufacturing has grown exponentially over the last several years for diagnostic and treatment solutions in healthcare. Here are a few trends we’ve noticed on 3D printing’s ever-evolving role in the medical industry.

A microfluidic device used in the medical industry.
Implants, Prosthetics, and Devices
The introduction of biocompatible materials in 3D printing is paramount for prototyping and production of medical components like implants, prosthetics, and medical devices that will be coming in direct contact with someone inside or outside of the body. 3D printing is also fitting for medical due to its ability to accommodate small, precise, and complex geometries, which is a must.
Protolabs has manufactured various components used in prosthetics like custom-machined joints for an exoskeleton, fixtures to adjoin pieces together, and parts used in paralympian ‘Monster’ Mike Schultz’ Moto Knee and Versa Foot2 system. We’re pleased to have a strong and ongoing partnership with Schultz and love cheering him on in various Paralymptic Games.
Customers turn to us to rapidly prototype and produce medical devices like surgical instruments, wearables, robotic arms, and microfluidics.
Patient-Specific Anatomical Printed Models
Speaking of patient-specific printed models, healthcare providers (not in dentistry) turn to 3D printing to create anatomically correct models for any area of the body for a variety of reasons. One important one being striving for overall improved doctor-patient communication. Physicians often explain an upcoming procedure or surgery by showing the patient how the process works with a step-by-step demonstration using a 3D model.
Another use for patient-specific anatomical models is for surgeons to conduct pre-surgical simulation practice to help lower the risk of complications and enable efficiency ahead of procedures. These models are also commonly used for training and educational purposes to enhance trainee pre-procedural understanding.

MicroFine, an exclusive material developed at Protolabs, offers extremely tight tolerances, making it a great fit for intricate and tiny medical applications.
Small, but Mighty, MicroFine
At Protolabs, our exclusive MicroFine™ resin is often used in medical applications due to its ability to produce extremely fine features and part geometries—as small as 0.0025 in. (0.0635mm). UVision360 leveraged Protolabs’ additive manufacturing service opting for MicroFine™ to rapidly prototype ultrafine parts for their patented LUMINELLE DTx Hysteroscopy System used to diagnose and treat problems within the uterus.
“A lot of these procedures are done in hospitals with old technology that is bulky, big, and uncomfortable,” Erich Dreyer, chief technology officer for UVision360, said.
Quick-turn manufacturing at Protolabs helped UVision360 quickly iterate on the device’s design, allowing it to launch to market while dramatically cutting cost.
Erich Dreyer
Printing for Dental Products
Dentists and orthotics labs turn to 3D printing for custom, patient-specific crowns, dentures, implants, clear aligners, and more. A study by SmarTech market research predicts that the dental 3D printing market opportunity could reach $9.5 billion by 2027.
Dental providers often use additive manufacturing for patient-specific products including printed models to accurately understand a patient’s anatomy and formulate a custom treatment plan.
Materials for Medical
Below is a list of the 3D printing materials we offer that are commonly used for medical devices, models, or instrumentation:
ABS-Like (White, Translucent/Clear, Gray, and Black)
These durable, yet flexible material options offer the tightest tolerances available for any of the 3D printing technologies.
MicroFine™
An exclusive Protolabs’ material used to build complex 3D-printed parts with micro-sized features as small as 0.0025 in. Optimal part sizes are 1 in. x 1 in. x 1 in. or less.
Silicone
This material offers excellent detail, high temperature and wear resistance, and has passed biocompatibility testing, making it an ideal option for medical devices like seals, gaskets, and customized devices.
Stainless Steel (316L or 17-4 PH)
Corrosion-resistant metals like stainless steel also offer high heat tolerance, corrosion resistance, and a high tensile strength.
Titanium
This workhouse alloy offers high strength, making it a great fit for medical components and instruments.
3D printing will no doubt continue to play an integral role in manufacturing components in healthcare. If you’re ready to move forward with your next project, just upload a part or reach out to one of our applications engineers at customerservice@protolabs.com or 877-479-3680.

If you have any issues getting your guide, click here to download.

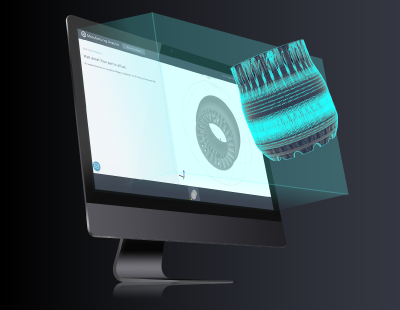
Need custom 3D-printed parts? Upload your CAD file for an instant online quote.
Get Printed Parts