What is Short Run Injection Molding? Benefits and Use Cases

With a bit of luck and a robust design, product engineers eventually face a day of reckoning: demand for their polymer parts is on the rise and neither 3D printing nor machining will meet the expected production needs. When that happens, it’s time to invest in an injection mold.
If you’re taking the traditional manufacturing pathway, you’d better get started. Because once you’ve found a reputable tooling house and invested in toolmaking for production, you’ll likely need to wait months for its delivery. Yes, the individual piece price is attractive—at least at higher volumes—but getting there can be a real nail-biter. Fortunately, there is an alternative: Short-run injection molding.
What is Short-Run Injection Molding?
Short-run injection molding is a process that uses less expensive tooling for lower quantities. It bypasses the high-volume paradigm just described—large investment, long wait times, and above all, inflexibility—in favor of one that’s much more nimble.
Unlike so-called “hard” production tools, short-run plastic injection molds are made from aluminum, a metal known for its easy machinability and high thermal conductivity. No, they don't last as long as those made from hardened tool steel, but for jobs under 10,000 pieces, they represent a lower-cost alternative, one that also delivers finished parts in just a week or two rather than several months.
There are lots of ways to leverage this manufacturing technology, but simply put, short runs are an excellent choice for manufacturers looking to get high-quality plastic parts as quickly and cost-effectively as possible.
Key Benefits of Short-Run Injection Molding
But what are the benefits? For starters, aluminum injection molds are much less expensive than their hardened counterparts—how much less depends on the number of cavities, part geometry, and other molding considerations, like the presence of undercuts or inserts, but suffice it to say, you’ll be pleasantly surprised.
There's much more to the equation than cost, however. Shorter lead times and the ability to iterate quickly mean accelerated product development cycles, speeding time-to-market. This benefit is further bolstered by the fact that our short-run injection molding service has no minimum order quantities, so customers can order only what's needed for current demands. And since parts are molded from production-grade materials and boast high-quality surface finishes (comparable to those of some 3D printing), they are well-suited to demanding, end-use applications.
Cost Considerations for Short-Run Molded Parts
The minimum order quantity statement above comes with a small caveat, albeit an important one. As with any manufacturing process, machine setup and tooling for short-run injection molding takes a fixed amount of time, the costs of which must be amortized across that order quantity.
Before looking at some use cases, though, it’s important to further define the term “short run.” The general quantity tipping point from short-run to production molding is 10,000 parts. Through Protolabs quick-turn factory offering, customers have two tooling options: Prototyping molds are guaranteed for a minimum of 2,000 shots (most last much longer), while those that fall under our on-demand production offering enjoy a mold life guarantee—when your aluminum tool wears out, we’ll replace it free of charge. While both are technically short-run injection molding, the former provides a more economical option based on your quantity needs.
When combined with our other on-demand benefits—first article inspection, capability reports, scientific molding process development reports, and PPAP to name a few—many customers have opted to make a short-run aluminum mold their final mold.
Looking at quantities closer to the millions? Production tooling may be a better choice for you. The other side of the equation brings you to 3D printing where a part is often less expensive at very low quantities. That's why many manufacturers choose to print their prototypes until they've determined the final design, after which they will move to short-run injection molding.

A technician takes a close look at an aluminum mold. Aluminum molds cost much less than steel ones, making them a great choice for prototyping.
When to Use Short-Run Injection Molding
So which approach is best? The answer depends on your company’s unique requirements. For example, consider a medical device manufacturer that has successfully launched a new design but given ongoing market volatility, is uncertain whether to invest in a steel production tool. That’s a perfect scenario for a short-run injection tool since it supports a "pay as you go" approach to the product's introduction. And if the medical company decides to go all-in on a steel tool, the aluminum mold will serve as a "bridge" over the coming months until the production mold's delivery, testing, and ramp-up is complete.
That brings up another common application of short runs. Bridge tools are not just used to meet rising demand during the ramp-up phase of product introduction. They also can serve as a low-cost insurance policy on more mature programs.
One recent example comes from an appliance manufacturer that ran into quality problems several years after product launch. Faced with many weeks of downtime, the company required a bridge tool that would keep their assembly line operational until they completed repairs to the production tool. Since they now own a second mold, they can use it to meet unexpected demand spikes or as a backup in case the primary tool fails again.
Lastly, short-run injection molding provides another crucial benefit: it allows designers to optimize for moldability and product performance with far less risk than the alternative, which is to go directly from 3D-printed prototype to steel production tool. By testing your designs with an aluminum tool, you can greatly reduce development costs. For industries like medical device, the ability to cut down on development time while navigating FDA hurdles with short-run injection molding is crucial.
Injection Molding for Large Quantities
Worried short-run injection molding isn't a fit for you? Our digital network opens up molding capabilities for larger, and more complex parts in higher-volume production quantities.
- High-volume molding with price breaks available
- High-requirement projects for larger, deeper, more complex molded parts
- Quotes for 100,000+ parts
- All complexities sized up to 79 in. (2m)
- 12 surface finishes (A1-A3, B1-B3, C1-C3, D1-D3) plus Mold-Tech finishes available
- Custom color-matching possible
- Aluminum and steel tooling, including Tool Steel P20
Want to learn more about short-run injection molding? Upload a file for a free moldability analysis and then reach out to a Protolabs molding expert to discuss the results. You’ll be molding parts in no time.
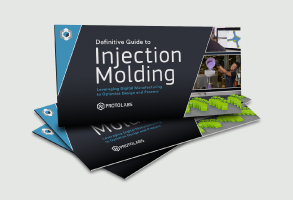
If you have any issues getting your guide, click here to download.