Thin walls are features we see often in designs, and they can present a range of issues for injection-molded parts (more on those later). The easiest way to avoid potential problems is to amend your design to beef up the walls or include minor adjustments. Due to part functionality requirements, we know it may not always be possible to avoid thin walls altogether, so we’ll also cover some helpful design and material considerations if your part must include thin walls.
The Skinny on Thin-Walled Geometries
So, what’s the problem with thin walls? Success in injection molding is all about proper flow and thin walls make it difficult for plastic material to flow evenly throughout your part mold. Here are some common thin wall injection molding perils:
- Cracking
- Unformed areas from material flow issues
- Uneven cooling and warp
- Weak knit lines or fracture points
- Cosmetic texture inconsistencies
Uploading your CAD model early in the design phase lets us pinpoint any potential issues early on allowing you to modify it as needed while remaining on schedule. Our quoting software will automatically identify whether your part has thin walls and will flag any potential milling issues before we begin manufacturing the mold. If your design is flagged as including walls that are too thin, (typically, under 0.015-0.020 in. (0.381-0.508mm) depending on material) an applications engineer will be in touch to recommend adding additional draft to corners, thickness to thin walls or hard-to-reach areas, or other features to improve the design.
Material Matters
When mulling over which material to choose for your part, keep in mind that choosing the right materials is dependent on your part geometry and application needs.
Certain materials flow easily through thin areas, including thermoplastics like
- high-density polyethylene (HDPE)
- low-density polyethylene (LDPE)
- polypropylene (PP)
- Nylon (PA)
These are all great options for parts that include a living hinge; a thin area that needs the ability to bend. Another material in the thermoset family is liquid silicone rubber (LSR), which fills incredibly easily—so much so, it can present flash risk on parting lines. We can help reduce flash by adding additional features to the mold design.
On the other hand, materials like polycarbonates are sticky and have difficulty filling in geometries with thin walls. Part wall thickness should be a key consideration when determining which material to go with.
Check out our wall thickness recommendations for each of our materials, and keep in mind we’re here to help provide suggestions.

Avoid Hitting a Wall: Design Tips and Tricks
Here’s a rundown of helpful tricks to keep in mind when designing and choosing a material for molded parts with walls:
- In general, ensuring your design has uniform wall thickness between 0.060 and 0.120 in. (1.5-3.0mm) throughout will ensure that the parts cool evenly and will prevent warping.
- One exception: ribs should be about 50-60 percent of the thickness of the main base, as shown in the photo to the right. Ribs that are the same thickness throughout can leave extra material at the base of the rib.
- To make a more robust thin rib wall, consider adding gussets (cross support ribs) to strengthen the design without simply making the rib thicker.
- Adding flow paths including radii to thin geometry can help material flow into thin ribs or sections more easily.
- While parting lines (the seam where two halves of the mold join) should be expected on most molded parts, changing up the location of your parting line can make all the difference cosmetically. Your quote will identify your parting line location and we may make recommendations on modifying the geometry to a more unnoticeable location.
Uploading your CAD file early allows us to lend you feedback on your design and helps us guide you through the injection molding manufacturing process. If we foresee any issues with wall thickness or part geometry in general, we can advise on how to correct it quickly to ensure you receive your finished parts on time.

Adding gussets can help support thin-ribbed walls.
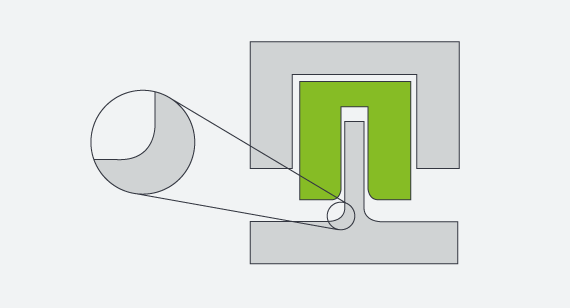
Adding radii to internal corners of your part geometry is critical in helping a part eject cleanly from the mold.
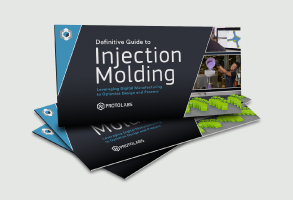
If you have any issues getting your guide, click here to download.

Need custom injection-molded parts? Get an online quote today.
Upload a Part