Titanium vs Aluminum: Workhorse Metals for Machining and 3D Printing
When you think of a dream team of material characteristics for parts, light weight and strength come to mind. Naturally, so do aluminum and titanium. Both materials tick off other important boxes, such as excellent resistance to corrosion and tolerance for heat. Using 3D printing or CNC machining, these two metals have proven to be incredibly versatile for parts across a range of industries.
Aluminum and titanium are both light, but for different reasons. Aluminum’s low specific gravity (2.7 g/cm3) means that it’s considerably lighter than counterparts such as steel, which is about three times as heavy. Although titanium is about two-thirds heavier than aluminum, its inherent strength means that you need less of it. In fact, you need a fraction of the amount of titanium to get the same physical strength you would get with aluminum. Titanium is used in aircraft jet engines, for example, and in spacecraft, too. Its strength and light weight reduce fuel costs.
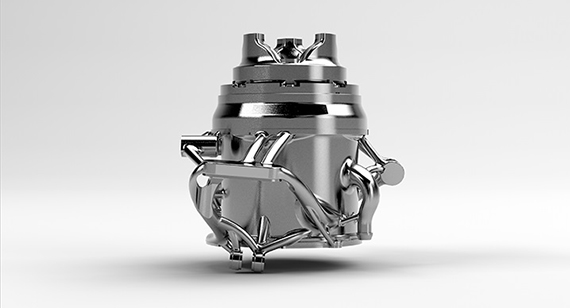
The aluminum alloy used in the DMLS process adds silicon and magnesium, building parts with material properties exceeding their die-cast counterparts.
Material Properties of Aluminum and Titanium
This chart provides a technical overview of the types of aluminum and titanium we offer for DMLS and machining.
Material | Process | Tensile Strength | Elongation | Hardness |
---|---|---|---|---|
Titanium (Ti 6Al-4V) |
DMLS | 172 ksi (1186 MPa) |
10% | 40 HRB |
Aluminum (AlSi10Mg) |
DMLS | 35 ksi (241 MPa) |
10% | 45 HRB |
Aluminum 6061-T651 |
CNC | 40 ksi (276 MPa) |
17% | 95 HBW 10/500 |
Aluminum 7075-T651 |
CNC | 83 ksi (572 MPa) |
11% | 85 HBW 10/500 |
Titanium (Grade 5 Ti 6Al-4V) |
CNC | 138 ksi (951 MPa) |
14% | 35 HRC |
The big difference between your two choices for machining aluminum has to do with the amount of copper in the alloy. In a head-to-head comparison, if you need something with impressive strength that can tolerate a high friction environment, 7075 makes the most sense. 6061 does better in welding applications, it’s easier to machine, and costs less. The bottom line when machining aluminum: If low weight, high tolerance to heat, and high strength are key, 7075 is the way to go.

Aluminum vs. Titanium
Because both materials offer high strength and low weight, it’s important to look at other differentiators when deciding which alloy to use for your parts.
- Strength/Weight: In critical situations where every gram counts but you need strong parts, titanium is the way to go. Titanium medical components, complex satellite components, fixtures, and brackets all succeed precisely for this reason.
- Cost: Aluminum is the most cost-effective metal for machining or 3D printing. While titanium adds cost, it still can drive value. Lighter weight parts translate into fuel savings in transportation applications, and titanium parts simply last longer.
- Thermal Properties: Applications that require high thermal conductivity, such as a heat sink, will benefit from aluminum. For high-temperature applications, titanium’s high melting point benefits applications where heat resistance is a priority, such as aerospace engine components.
- Corrosion Resistance: Both aluminum and titanium offer excellent corrosion resistance.
Titanium’s corrosion resistance and lack of reactivity makes it the most biocompatible metal, so it’s great in medical applications, such as surgical instrumentation. Ti 6-4 also holds up well to salty environments and is often used in marine applications.
Aluminum Applications
Aluminum is everywhere—it’s the most common metal on the planet. The thin layer of aluminum oxide that forms on it when exposed to air makes it essentially corrosion-free and its light weight helps keep your parts from acting like a boat anchor. While aluminum generally doesn’t react to acids, it does tend to corrode in alkaline (basic) environments.
In general, aluminum finds its way into aircraft and building materials, such as non-load-bearing framing. More specifically, 6061 is the choice for bicycle frames, SCUBA tanks, fishing reels, small boats, and vehicle frames. 7075’s stronger properties make it ideal for molds for plastics and tooling, and aircraft frames. And if you’re looking for a good electrical conductor, aluminum can do that. It has a great ability to transfer heat, which makes it excellent for heat sinks.
The aluminum alloy used in our direct metal laser sintering (DMLS) process, AlSi10Mg, adds silicon and magnesium. It’s often used for casting and is most similar to a 3000 series alloy, given the addition of magnesium as the principal alloying element. The properties of 3D-printed aluminum exceed its die-cast counterpart except for lower elongation at break.
Titanium Applications
Titanium is also one of the most common metals on Earth, but its melting point is so high it’s difficult to process it into a usable product. That’s a big reason why it is more expensive than other metals. Titanium parts have additional cost implications because they are difficult to machine. Titanium is known for its strength and has a high strength-to-weight ratio. It also offers excellent corrosion resistance and equally poor electrical conductor.
One of titanium’s pluses is low thermal expansion. With a melting point of about 3,000 degrees F (1,660 degrees C), when exposed to heat, it maintains its form better. Moreover, rather than absorb heat, titanium likes to reflect it, so you’ll find it in low-E windows, bouncing back warming infrared rays from the sun.
In terms of appearance, titanium’s color varies depending on how much it has been altered. It can range from dull gray in raw form to shiny silver when smooth. The titanium used in our DMLS process is Ti 6Al4V, more commonly referred to as Ti 6-4. It has mechanical properties similar to Ti grade 23 annealed and has exceptional tensile strength.
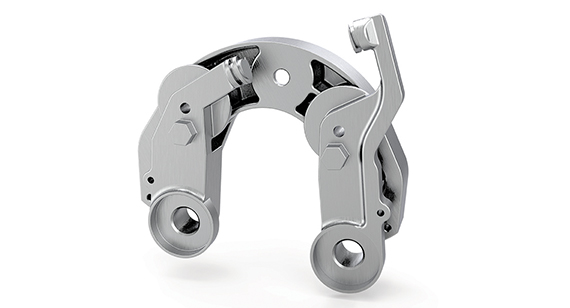
Aluminum machining is popular in the auto industry where lightweighting is key to improve fuel economy and minimize impact on performance, such as this tensioner for Litens Automotive.
Why Machine Aluminum and Titanium?
CNC milling and turning are time-tested ways to manufacture aluminum and titanium parts. The processes are fast—often producing parts in less than a day—and they adhere to tolerances of +/- 0.005 in. (0.13mm). If you need a prototype part quickly, aluminum stands out for its low cost and high quality. However, machining is somewhat limited in terms of geometries, so extremely complex designs require a different solution such as DMLS, no matter what material you choose.
One factor you might not think about when choosing material is machining waste. While milling away excess material is fine for inexpensive aluminum, it’s not ideal for pricey titanium. Because of this, engineers often choose to manufacture prototypes using aluminum, then switch to titanium for production parts.
Why 3D Print Aluminum and Titanium?
DMLS is an additive manufacturing process. Using a fusing laser to weld powdered metal together, it forms parts, layer by layer. The primary advantage to DMLS is that you can create parts with incredibly complex geometries, such as honeycombs and mesh-like structures. Machining just can’t match DMLS’s design flexibility, regardless of which metal.
One advantage of 3D printing titanium that you might not have thought of has to do with titanium’s cost. Using powder means you end up with virtually no waste metal. Moreover, while manufacturing costs are somewhat higher using DMLS, the parts deliver value through the combination of strength and weight reduction. And added bonus? DMLS lets you combine separate parts of assemblies into a single, strong part. This saves assembly time and reduces your Bill of Materials (BOM).
For additional help, feel free to contact a Protolabs applications engineer at 877-479-3680 or customerservice@protolabs.com. To get your next design project started today, simply upload a 3D CAD model for an interactive quote within hours.