How to 3D-Print Flexible Parts
Explore the 3D printing materials and processes available for making flexible parts.
An Introduction to Flexible 3D Printing
Is there nothing 3D printing can’t do? Besides the typical rigid and geometrically complex printed parts you’ve seen, there are also many materials suitable for printing flexible parts. Before diving in, it’s important to know the strengths and limitations of both the materials and the process you choose to manufacture your parts.

Key Mechanical Properties of Flexible Materials
There are certain key qualities that flexible materials must possess that are important considerations when choosing the one that works best for your application.
Creep Resistance
Over time, materials that are in contact with other parts can start to deform. This characteristic reflects the ability of a material to resist that deformation. It's an important measure for flexible materials in 3D printing, as parts may be subjected to continuous stress, especially when used in weight-bearing applications or constant pressure.
Ductility
This refers to a material's ability to deform under tensile stress. In 3D printing, ductility is a measure that indicates flexibility and the ability to bend or stretch without breaking.
Elasticity
This generally desirable trait is the ability of a material to return to its original shape after deformation. It's a key attribute for flexible 3D-printed parts that need to withstand repeated stress and deformation without permanent damage.
Fatigue Resistance
Parts must withstand repeated cycles of stress without failing. This is particularly true for flexible parts that are subject to frequent bending, twisting, or other forms of stress.
Flexural Strength
This measures a material's resistance to bending. It's crucial for flexible 3D-printed parts that need to maintain their shape under load without breaking or permanently deforming.
Tear Resistance
This self-explanatory attribute is a material's ability to resist tearing or ripping. It's one of the most important qualities when choosing a material for your flexible 3D-printed parts, especially if they might be subjected to impact or sharp forces.
Tensile Strength
Expand a rubber band far enough and you'll likely be rewarded with a snap and red mark on your hand. Tensile strength measures a material's resistance to breaking under tension. It's important for flexible materials, as they may need to withstand pulling forces without tearing or snapping.
Considering all the qualities listed above, here is a quick chart detailing the flexible 3D printing materials we offer, and which stack up best according to those properties.
Material Property | Materials |
---|---|
Creep Resistance | PA11 Black, TPU 70-A |
Ductility | PA11 Black, TPU 70-A, True Silicone |
Elasticity | PA11 Black, Digital Photopolymer, TPU 70-A, True Silicone |
Fatigue Resistance | PA11 Black, Digital Photopolymer, TPU 70-A |
Flexural Strength | Accura Xtreme White 200, PA11 Black, Digital Photopolymer |
Tear Resistance | PA11 Black, Digital Photopolymer, TPU-70A, True Silicone |
Tensile Strength | Accura Xtreme White 200, PA11 Black, Digital Photopolymer, TPU 70-A |
Flexible Materials for 3D Printing
We have three printing technologies suitable for flexible parts: PolyJet, stereolithography (SLA), and selective laser sintering (SLS).
The first of these, PolyJet, uses UV light to cure droplets of photopolymers sprayed out of jets, something like an inkjet printer. The precisely distributed material quickly fuses to the layer below it. It’s a fast process that also allows you to choose the durometer (hardness) of your material, with Shore A hardness values ranging from 30A through 95A. It’s ideal for overmolding parts and can hold tight tolerances.
SLA materials include ABS-Like White, PP-Like Translucent, and True Silicone. These are all thermoset resins that cure via a UV laser.
ABS-Like White is known for its strength, flexibility, and durability, plus you can use it to manufacture large parts. PP-Like Translucent is very flexible but also offers excellent resolution and fine detail. The added plus is that its translucency is perfect in applications in which you want to monitor fluid flow or need to see beneath the part. True Silicone is a recent material that offers all the benefits of injection molded silicone, and adds the ability to design complex, organic geometries. As with the digital photopolymer used in PolyJet, you can dial in the durometer of your True Silicone parts.
SLS materials that can yield flexible parts include PA11 Black, Polypropylene Natural, and TPU 70-A.
As with SLA, a laser is used to fuse, or sinter, layers together, but in this case, the material comes in powder form that fills a large vat. PA11 Black (PA850) maintains ductility and flexibility, but also yields strong, temperature-resistant parts. Polypropylene Natural is a low-weight and chemical-resistant material. TPU 70-A has a rubber-like quality, both aesthetically and physically. Parts made of TPU 70-A have high elongation at break, so they are built to bounce back, rather than split.
Material | Process | Properties |
---|---|---|
Accura Xtreme White 200 | SLA | Durability, Large Format, Moisture Resistance |
Digital Photopolymer | PolyJet | — |
PA11 Black | SLS | Dimensional Stability, Durability |
Polypropylene Natural | SLS | Chemical Resistance, Dimensional Stability |
Somos 9120 | SLS | Durability, Transparency |
TPU 70-A | SLS | Impact Resistance, Water Resistance |
True Silicone | SLA | Moisture Resistance, Temperature Resistance, Water Resistance |
Three of these materials are categorized as elastomers: Digital Photopolymer, TPU 70-A, and True Silicone. By their nature, they offer high elasticity, resilience, and a soft, rubbery feel. The other four materials areclassified as plastics. While they can bend and flex, they tend to be less stretchy.
Design Considerations for Flexible Parts
Now that you know basic differences between material properties, it’s time to explore best practices in your CAD models to ensure that your parts print properly.
Overhangs and Bridges
Avoid complex overhangs and bridges because they can be challenging to print with flexible materials. Simplify your design or use supports if necessary.
Post-Processing
Some flexible materials may benefit from post-processing techniques like annealing or heat treatment to improve their properties. SLS parts sometimes have surface roughness, which can be reduced using vapor smoothing—a process that chemically melts excess material. Vapor smoothing also creates more uniform color and seals surfaces, making them easier to clean. SLA parts benefit from light sanding and fine bead blast to remove nibs and smooth the part.
Print Orientation
The direction in which your part is printed plays a major role in the print speed, surface finish, and mechanical properties of flexible parts. Try to orient the part to minimize the need for supports. We can work with you on that aspect of the printing process.
Tolerances
With flexible parts, tolerances are a somewhat inexact specification as the part can change dimensions with even the slightest application of pressure. That said, overly tight tolerances could lead to difficulties in assembly or part functionality.
Wall Thickness
There’s a tradeoff when it comes to wall thickness. A thicker wall will get you a stronger part that holds dimensions better, but it could reduce flexibility. This is where iteration comes in handy to find just the right balance before committing to specific geometries.
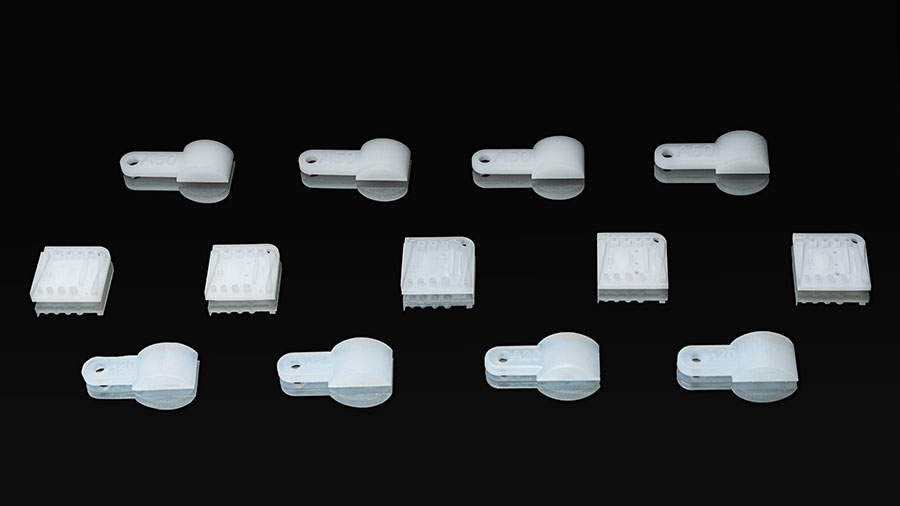
Final Thoughts
This article represents a starting point when evaluating flexible 3D printing materials. If you need more help, we have in-house experts who can guide you through your projects to ensure that you get your flexible printed parts quickly. Contact one of our applications engineers at 877-479-3680 or customerservice@protolabs.com.