Mold Texture Standards and Finishes
Choose from standard and Mold-TechTM finishes for several texturing options to improve the surface finish of plastic molded parts
Although the surface finish on any plastic injection-molded part might be perfectly suitable for its intended application, you should be aware that there is a range of available texturing options, all can be applied to certain areas of a mold or even the entire mold.

These include:
- finishes produced by bead-blasting or polishing the mold surface
- wood or leather-like graining
- pebbled surfaces
- matte, gloss, or hazy finishes, and many others
Such textures can improve parts’ grippability, enhance egonomics, hide parting lines and other cosmetic defects, or simply make the finished parts more aesthetically pleasing.
Need some real-world examples? An automaker might choose to texture a car’s injection-molded dashboard or trim pieces with a faux wood appearance. Developers of handheld power tools apply texture to make their products easier to grip. And, along these lines, paint and stickers adhere more readily to some textured surfaces, while others help make parts more scuff- and abrasion-resistant.
Finish vs. Texture in Injection Molding
So what are these texturing options, and how can I include them in my part design? The first thing to know is that two distinct paths exist for mold texturing and finishing at Protolabs. The first includes the PM (ProtoMold) and SPI (Society of the Plastics Industry; now Plastics Industry Association) finishing standards outlined in the chart. Most are applied by hand via polishing, stoning, or bead-blasting of the mold surfaces after machining, although EDM might be used in certain circumstances, and these options are also covered in our design tip on injection molding surface finishes.
Finish Callout | Description |
PM-FO | Protolabs’ texture; non-cosmetic; finish to Protolabs’ discretion |
PM-F1 | Protolabs’ texture; low cosmetic; most tool marks are removed |
PM-F2 | Protolabs’ texture; non-cosmetic; EDM permissible |
SPI-C1 | 600 grit stone |
SPI-B1 | 600 grit paper |
SPI-A2 | Grade #2 diamond buff |
PM-T1 | Protolabs’ texture; light bead-blast |
PM-T2 | Protolabs’ texture; medium bead-blast |
Shown in the table above are our standard finishing options. SPI-A2 (Grade #2 diamond buff), for instance, produces a shiny, high-gloss finish on most materials. SPI-C1 is applied using a 600 grit stone and offers a dull matte finish. Sitting in between is SPI-B1, made with 600 grit abrasive paper. There are also the various PM-style finishing options, which produce everything from non-cosmetic surfaces that may show some tool marks to the lightly textured finishes generated with bead-blasting.

Steps to Success in Mold Texturing
So how is texturing accomplished? Two distinct processes are available, but which one to use depends on the type of finish, its surface depth, and the mold material. Regardless, both are applied after the mold cavities have been completely machined and their soon-to-be-textured surfaces smoothed to the requisite level. For light texturing, a corrosive chemical is applied in a controlled manner, etching the mold cavity until the desired depth and appearance are reached. If certain surfaces are not going to be textured, those areas are masked off with protective tape beforehand.
For more aggressive or geometric textures such as checkerboards and diamond patterns, a five-axis laser is typically used to ablate the mold material, essentially burning it away much as a CNC laser-cutter slices sheet metal into highly accurate pieces. Some textures may reach depths of 0.003 in. (0.0762mm) or more, which raises another important point: the need for larger draft angles when texturing is applied to the mold’s sidewalls. As a general rule, we recommend one degree of draft for every 0.0005 in. to 0.0006 in. (0.0127mm to 0.01524mm) of texture depth, or roughly 6 to 7 degrees for a typical wood grain or leather-like finish. As always, refer to the our DFM (design for manufacturability) analysis that accompanies your online quote.
Don’t Forget the Materials When Considering Mold Texturing
Part materials are another consideration. We do not recommend textured surfaces when molding soft polymers such as TPE and liquid silicone rubber (LSR), as these don’t pick up the finish very well. Nor does texturing add much cosmetic value with white or transparent materials like polycarbonate, except in those cases where the texture may serve to diffuse light or provide other optical properties. As with all things in manufacturing, exceptions abound, but in most cases, texturing provides the best cosmetic results in darker materials.
Finally, take special care when using fiber and flame-retardant polymers with textured molds. These materials tend to generate higher surface resistance during the molding process, creating drag and turbulence that may be reflected in the part appearance—glass fibers, for instance, can add a stringy or sparkly finish to a textured part, while flame retardants might lead to the whitish streaks known to plastic injection molders as splay. That said, these and other concerns are, in most cases, easily addressed with the right mold design, which is why we encourage you to reach out to one of our applications engineers who are always available to help at 877-479-3680 or customerservice@protolabs.com.
And while our standard finishing options do include bead-blasted surfaces, these are not true “textures” as described at the beginning of this design tip. These fall under the Mold-TechTM standards; as you will see, these are produced through chemical etching or laser-based modification of the mold cavity. Each is represented by an MT- followed by a five-digit code. For example, MT-11010 presents a sand-like appearance, MT-11120 resembles smooth concrete, while MT-11555 has a wood panel look, and so on.
Rules of the Texturing Road for Injection Molding
Literally hundreds of Mold-Tech specifications exist. Aside from the sand, concrete, and wood textures just discussed, there are also checkerboards, diamonds, straight or curved lines, and more. We are happy to supply a sample plaque showing the seven most popular finishes.
Mold-Tech textures can be applied to steel or aluminum molds. Before uploading a design to the our site, you should indicate which surfaces require texturing, along with the desired Mold-Tech number. Depending on the desired texture, the surface(s) may require smoothing to remove tool marks—usually to an SPI-C1, as listed in the accompanying chart—or even polishing to an SPI-A2 if the Mold-Tech texture is very light. However, if a PM-T1 or PM-T2 texture has already been applied to a mold surface, additional texturing is not possible without re-machining one or both mold halves.
This brings up an important point. As with so many things in life, texturing is not free. It most likely will add additional lead time to your order. For those of you still in the development stage, it's a good idea to hold off on mold texturing decisions until you're done iterating. Doing so will reduce project costs and get you to the finish line that much faster. Best of all, it can often be added to a completed mold when geometry and existing surface roughness permits.
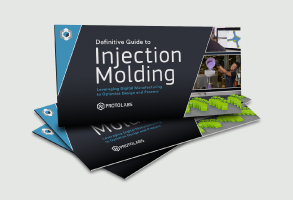
If you have any issues getting your guide, click here to download.

Need custom injection-molded parts? Get an online quote today.
Get Custom Parts