Understanding Powder Bed Fusion Technology
Powder bed fusion (PBF) is an additive manufacturing process that fuses atomized powder to build parts
Powder bed fusion (PBF) is an additive manufacturing, or 3d printing, technology that uses a heat source—typically a laser—to sinter or fuse atomized powder particles together. Like other additive processes this is done one layer at a time until the part is completed.

Powder bed fusion technologies are:
- direct metal laser sintering
- selective laser melting
- electron beam melting
- selective laser sintering
- multi jet fusion
Powder bed fusion is a relatively high-cost additive manufacturing technology when not outsourced. It is mostly used in industrial and commercial applications. Both metal and polymer-based processes can be used for end-use production parts in addition to rapid prototyping applications.
How Does Powder Bed Fusion Work?
Similar to other additive manufacturing processes, a 3D CAD file is created and loaded into the machine. From there, the process usually starts by heating the bed of powder to a consistent temperature. The machine then begins drawing the first layer of the part or support features and, in doing so, fuses together the powder particles. This is continued, layer-by-layer, until the part is completed.
Metal powder bed fusion processes like DMLS and EBM require support structures in order to secure the part to the build platform. Otherwise, the parts would curl upwards as internal stresses build up during the fusing process. After the build of a metal PBF part there are variety of methods to remove support structure material.
On the other hand, polymer-based PBF processes are unique in that parts do not require support structures. Selective laser sintering works in similar way to metal PBF processes. Powder is loaded into the machine and a laser is used to sinter or fuse the particles together. Multi Jet Fusion (MJF) works slightly differently in that fusing agents are first applied to the powder material and then a heat element sweeps over the bed, which then fuses the material together. This is a slightly more efficient process which makes MJF a good option for larger volumes of nylon parts.
Below are videos that walk through how three types of powder bed fusion work to build parts.
Materials Available for Powder Bed Fusion
Powder bed fusion supports a range of commonly used materials.
Metals | Polymers |
|
|

Post-Processing for Powder Bed Fusion Parts
Most PBF parts will require post-processing to achieve the desired surface finish quality. Any excess powder must also be removed from the part. Tip: be sure to design parts with powder outlet channels. Since PBF parts are durable and suitable for functional testing and end-use, tapped holes and threads are an option.
Metal PBF parts must receive heat treatment due to how the process results in internal stresses. After a heat treatment, support structures are removed from the parts and additional post-processing can proceed. Depending on customer requirements, there are a number of post-processing capabilities to improve surface quality such as CNC machining and polishing.
Plastic PBF parts are removed from the bed of unfused powder and excess material is removed with a bead blast—this also results in a consistent surface finish. As part of our standard finishing, MJF parts receive a black dye treatment—this further improves finish quality. SLS parts are left as-is once the bead blast is completed, but SLS parts are good candidates for additional dying if color is desired.

If you have any issues getting your guide, click here to download.
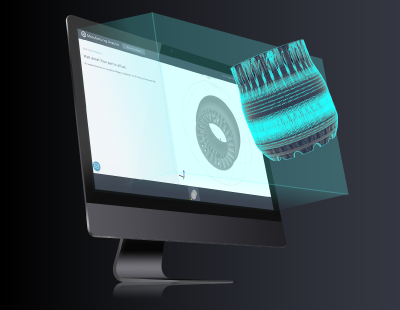
Get an online 3D printing quote today.
Upload a Part