3D Printing Trend Report 2024
A global survey on market growth, ecosystem maturation, and technological innovations in 3D printing
Key Findings
The annual growth rate of the 3D printing market exceeds expectations, indicating a confident market, and the continued maturation of the 3D printing industry.
$57.1B
We predict the 3D printing market will grow to reach $57.1 billion by the end of 2028
70%
Of surveyed businesses printed more parts in 2023 than in 2022
82%
Of respondents said 3D printing helped them save substantial costs
21%
Primary used 3D printing for end-use parts in 2023, up from 20% in 2022
47%
Of respondents say lead time was the main reason why they opted for 3D printing over other manufacturing methods–up from 44% in 2023
77%
Of respondents think 3D printing will have the most significant impact on the medical industry
Introduction
3D printing has evolved to occupy an established place in manufacturing today. As it has become a more widely applied industrial manufacturing process, the industry is coming of age. A large network of specialized companies providing support and solutions for a range of production processes has emerged. From design software through automated production solutions to enhanced post-processing methods, this budding ecosystem signals that production-level 3D printing is used by ever-growing numbers of businesses. The wider availability of specialized solutions in turn increases the uptake of production level 3D printing.
This trend also extends to different types of printers and materials—and businesses that are geared to highly specific applications, issues, and fields are often most likely to prevail in the wider industry.
The applications of 3D printing are growing not just in type, but in scale, too, with both micro printing and large-format applications continuing to evolve. There continues to be significant investment in additive manufacturing solutions and materials, particularly in the medical and aerospace sectors. Innovative, often highly specialized, materials are coming to the market, expanding the potential applications of the technology. Software and hardware are evolving at pace, too, with new developments partly fueled by AI.
Key Takeaway
This report is split into sections that:
- Investigate the state of the market in 2023.
- Explore the trends shaping the industry in 2024.
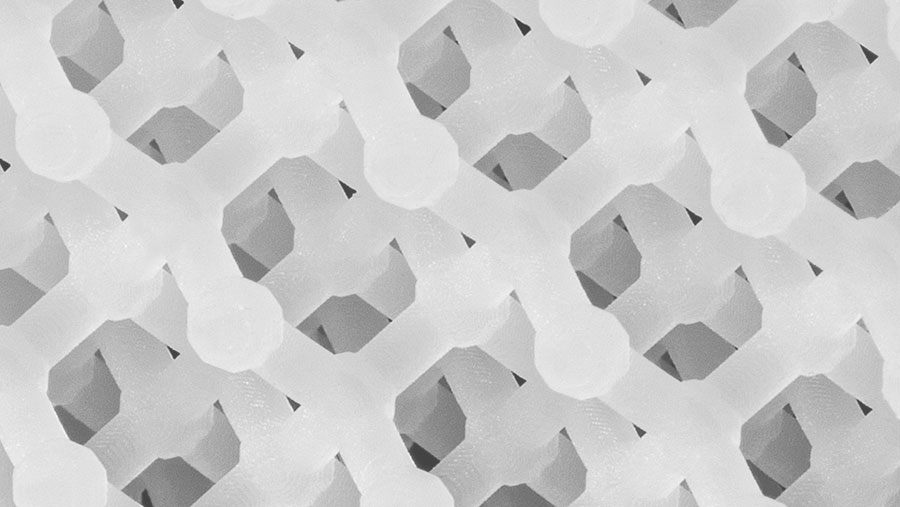
3D Printing Market Growth

This graph summarizes data reported by leading market analyst firms that evaluated the 3D printing market in 2023, including revenue from 3D printing systems, software, materials, and services, but excluding internal corporate investments in 3D printing technologies. It was collated based on publicly available information and it provides the best estimate of the current size and future potential of the global 3D printing market.
The 2023 market size was estimated at $22.14 billion on average, representing a 26.8% increase on 2022's $17.46 billion. This is far exceeding expectations. It is 10% higher than we predicted in last year's report, which forecast the 2023 market size of $19.9 billion at a compound annual growth rate (CAGR) of 17%.
If we apply last year's CAGR (26.8%) to 2024, the market size would grow to $28 billion. Taking market fluctuations into account, we're using a more conservative growth rate based on averages across the past five years. This arrives at a CAGR of 21% and a market size of $24.8 billion by the end of 2024 and $57.1 billion by the end of 2028.

This increased market growth rate is reflected in the responses to the 2024 edition of Protolabs Network's annual survey of more than 700 engineers, designers, manufacturers, and other members of our global engineering community. Of the survey respondents, 70% printed more parts in 2023 than in 2022. Only 21% printed the same amount of parts as they had printed in 2022, and just 9% printed fewer parts than in the previous year.
Production run volumes have remained stable in the past year. While in previous years, the number of respondents saying they printed more than 10 parts rose from 36% for 2020, to 49% for 2021, and to 76% in 2022, this figure stayed at 76% for 2023, marking a stabilization. However, there was one shift: the percentage of respondents saying they printed more than 1,000 parts rose from 4.7% to 6.2% compared to the previous year. This may signify a further increase of the usage for 3D printing technology for the production of end-use parts or aesthetic parts rather than prototyping. Indeed, there was a slight increase in respondents saying they primarily use 3D printing for end-use parts in 2023, up to 21% from 20% in 2022.

The speed and agility of 3D printing continues to be an attractive aspect of the technology. Almost half (47%) of respondents said lead time was the main reason why they opted for 3D printing over other manufacturing methods—up from 44% in the previous year. Easy access to tech (43%) and geometric complexity (41%) were other important features, as was the price, which was the deciding factor for 33%, up from 29% the previous year. And you can see why this remains such a winning argument: 82% said 3D printing had helped save substantial costs in their manufacturing pipeline.

3D printing remains a fast-changing, exciting sector with unexpected innovations emerging constantly. It has endless potential to transform existing industries and practices. New materials are being created, AI is set to disrupt this sector as much as all the others, and 3D printing technology is steadily being improved or even transformed, from the very small to the rather big applications. Of our survey respondents, 77% think the medical and healthcare sector, which incorporates manufacturing microscopic parts, is the industry where 3D printing has the most potential for having a significant impact—arguably a process that is already well underway. The construction industry, and particularly housing, is one of the more ostentatious applications of 3D printing. Of our survey respondents, 44% expect 3D printing to help housing construction reach new heights.

10 Things to Look out for in 2024 and Beyond
We expect the following developments and trends to have an impact on the 3D printing industry in the coming year.
1. A stronger focus on production
As the 3D printing ecosystem continues to mature, a network of specialized companies providing support and solutions for production processes is springing up around 3D printing businesses—offering everything from design software through automated cleaning and sorting solutions to enhance post-processing technologies. This in turn increases the uptake of production-level 3D printing.
2. New specialized plastics and composites
New materials with a wide range of properties, from elasticity to conductivity, biocompatibility, and reduced UV sensitivity, and especially tailored for 3D printing, are being developed and certified at pace.
3. Hybrid manufacturing
Processes combining additive manufacturing with CNC machining and other technologies are on the up and up, testing the limits of what can be achieved in manufacturing.
4. Multi-material printing
Enabling the combination of materials with different properties in one printed object, multi-material printing opens the door to a wider range of products being created within additive manufacturing and can remove the need for assembly.
5. The rise of metal printing
Used predominantly for aerospace, automotive, and medical applications, as well as for tooling, metal printing continues to be a hugely successful technology. The ever-increasing demand for it is evidenced by Protolabs' new 120,000-square-foot facility wholly dedicated to DMLS printing.
6. Vapor smoothing
Vapor smoothing is becoming prevalent across the industry, radically improving surface finishes in a wide range of applications and simplifying production-level printing processes.
7. Automation in manufacturing processes
Automation systems supported by computer vision, thermal sensors, and AI can effect significant labor savings and thus cost efficiency.
8. Advances in AI
Rapid advances in AI technology are impacting hardware (e.g., by leveraging computer vision and sensors), software (e.g., by enabling non-planar FDM printing), and are making 3D printing more accessible to a wider audience by providing design support.
9. Investment in micro 3D printing
At the microscale, 3D printing is the only technology that can achieve certain geometries and quantities; this potential continues to be leveraged, particularly by the medical and dental sector.
10. Large-format 3D printing
Heaving into view on the other end of the scale, there are exciting new developments in large-format printing—not just for metal printing, but also for plastics, helped along by new robotic systems.
Trends by industry
Key figures
Agriculture (87%) |
Design (9%) |
Transportation (33%) |
Medical (77% of respondents) |
Our survey of the global engineering community included more than 700 respondents, among them engineers, designers, and manufacturers. This gave us a very thorough overview of perspectives, numbers, and opinions coming from a variety of different industries, roles, and regions. In some subjects, there were notable discrepancies between respondents of different industries: for instance, 87% of respondents in the agriculture industry said they had printed more parts in 2023 than the year before, which is much higher than the cross-industry average of 70 percent.
The increased market growth rate that we observed in our market data analysis was reflected in the survey, where 70% of respondents stated that they had printed more parts in 2023 than in 2022. A total of 21% printed the same amount of parts as they had printed 2022, and just 9% printed fewer parts than in the previous year. The industries in which the percentage of respondents stating they printed more parts than in the previous year was the highest were agriculture (87%), electronics (83%), transportation (83%), construction (79%), and medical devices (75%).
Looking at the "applications of 3D printing" chart below, 67% of respondents said they used 3D printing for prototyping, while 21% use it for end use parts, but the breakdown of these applications differs greatly by industry. The industries with the highest adoption of 3D printing for end-use parts were transportation (33%), robotics (30%), and industrial automation (27%). In the design industry, 9% were using 3D printing for aesthetic parts, more than double the average.

The term 3D printing encompasses several additive manufacturing technologies that can differ in material selection, surface finish, durability, and manufacturing speed and cost. When we asked our respondents which they used more frequently, they said:
- FDM: 59%
- SLA: 20%
- SLS: 11%
- MJF: 7%
Breaking this up by industry, there are some notable differences to the above averages.
For instance, in agriculture, 87% used FDM most frequently, and in construction, it was 79%. On the flipside, only 42% of respondents in the medical industry used FDM most frequently, as it was more highly skewed towards SLA, with 40% of respondents using it most frequently—twice as many as the 20% average.
Biotechnology is another sector where a relatively high percentage (25%) of respondents used SLA most frequently, while automotive had the highest adoption of SLS—20% compared to the average of 11 percent.
Finally, when it comes to MJF, two industries used this much more frequently than the 7% average: industrial engineering (18%) and electronics (15%).

Trends by region
Key figures
Global average of 7%. |
Global average of 4%. |
Global average of 67% for prototyping and 21% for end-use parts. |
Global average of 70%. |
Our survey demonstrated a distinct difference between the regions in how respondents were using 3D printing. The percentages below show regional trends versus global averages.

The Big AI Promise
Do we believe the hype of an AI future for 3D printing?
The emergence of AI has been so fast-moving, so wide-ranging, and so disruptive in almost every industry, it's clear that it'll have an impact in the 3D printing space, too. The question is in which part of the process the technology will be most consequential. Of our survey respondents, 14% think AI will have the biggest impact by providing automated and accessible DFM at the slicer level; 23% think it will be the development of new materials and printing techniques; and 25% think AI will improve accessibility to non-planar FDM printing through improved slicer software. The largest group of respondents, at 33%, see AI having the biggest impact at the hardware level, through enabling automated print tuning by leveraging computer vision and sensors.
"Like every industry today, 3D printing is capitalizing on the excitement around next generation AI and automation tools," says François Minec, Global Head of 3D Polymers, HP Personalization and 3D Printing at HP. "Advancements in 3D hardware, firmware, and software are bringing data analytics and KPI monitoring to the forefront, enabling scalability for even more manufacturers."
Adam Hecht, co-founder and director of Additive Manufacturing at DIVE, a design agency specialized in industrial additive manufacturing, agrees that it's the hardware where AI is going to be most helpful. "Right now, we have a lot of smart printers that are very dumb. They will say something is wrong without specifying what it is. That's very frustrating for a lot of consumers and companies. But as the systems get smarter, they can actually help users to self-diagnose, or dial in new materials, for example—I think that's where we're going to see a lot more adoption."
"In terms of quality control, most of what I've seen has been in-process monitoring," says Eric Utley, 3DP applications engineering manager at Protolabs. "There's definitely research going on in that area, and I can certainly see it being offered commercially in the next couple of years."

Alex Huckstepp, advanced-manufacturing expert and co-founder of a still-stealth manufacturing software startup, agrees. "Process control—anomaly detection and closed-loop feedback opportunities—would be a frontier where AI and machine learning could have an impact."
When it comes to generative design, Hecht thinks AI's impact may be more limited. "Generative design works fairly well in terms of topology optimization. But I wouldn't say it's too universally helpful, other than for very specific parts of the industry such as aerospace, automotive, or medical, that are creating very high-performance, lightweight parts. It works out really well in those."
AI can also be help for consolidating the many elements of designing for 3D printing, from optimizing to adding lattices and surface textures such as basket weaves. "There's so much you can do to a part because you have so much freedom in 3D printing," says Hecht. AI-assisted programs can help with combining these elements in one step to make the design process easier.
"We're starting to see interesting tools on the design side—designing within manufacturing process constraints in a much more automated, optimized way," says Huckstepp. "Then there's Multiphysics process simulation—there's some really interesting AI tools emerging there."
"AI-generated CAD is accelerating quickly," adds Utley. "And NASA has been promoting their software, which is much more manufacturing focused, and a lot of that is really, really interesting." The software generates optimized designs in line with the parameters specified by engineers. "It's tuned towards specific manufacturing processes and is actually doing topology optimization," Utley says.
But you don't have to be working at NASA level for AI to be useful for you—in fact, the skill and constant practice required, for example, to be efficient with making 3D CADs means AI assistance can significantly accelerate and simplify these processes, not to mention present an appealing proposition to engineers who are less familiar in the design space. "I think an important factor stopping people from ordering 3D printing is not knowing how to design," says Robin Brockötter, supply chain manager at Protolabs Network, "and I can imagine that AI will make this a lot easier."

From Prototyping to Production
Printing production-run volumes of parts is becoming an increasingly viable solution.
While the use of 3D printing for rapid prototyping has been developing since the late 80s and is now extremely common, the industry has also steadily continued its move towards production applications, including low-volume production, mass customization, and serial production. "We're seeing more and more large-quantity orders and repeat orders," says Protolabs Network's Robin Brockötter. "There's definitely a trend towards full-scale production." This is influenced by many and diverse factors, including a preference for more local production amid global supply-chain disruptions (9% of our survey respondents said low susceptibility to supply chain issues is the main reason why they opted for 3D printing over other manufacturing methods) and sustainability concerns.
In 2023, 21% of our survey respondents used 3D printing for end-use parts—up from 20% in 2022—and 4% used it for aesthetic parts. When it comes to replacing injection-molding manufacturing with 3D printing processes, it's all about order volumes: for low-volume production, 3D printing is often the more cost-effective solution, while at higher volumes, injection molding becomes more economical. However, the point where that happens—the 'sweet spot' of maximum viable 3D printing order volume—is shifting. "3D printing can now start producing more and more parts before injection molding becomes cheaper," says Brockötter. Results from our 2024 survey support this. In our 2023 survey, doubts around 3D printing as a choice for "production volume and scale" led 47% of respondents to opt for different manufacturing technologies, but this year that number has dropped to 45%, showing increased confidence in scaling with 3D printing. And throughout the years, our surveys also show a steady growth in production-run volumes: respondents saying they printed more than 10 parts rose from 36% in 2020, to 49% in 2021 and to 76% in 2022. While this figure has stayed the same for 2023, marking stabilization, the percentage of respondents saying they printed more than 1,000 parts rose from 4.7% in 2022 to 6.2% in 2023.

Beyond the actual printing process, there are many other aspects that influence the scalability of using 3D printing technologies for production, from software, design, and materials to post-processing and finalizing tasks such as cleaning, secondary finishing, spot removal, stress relief, and inspections. As the 3D printing ecosystem continues to mature, a support system of companies providing many of these services is springing up around 3D printing businesses, simplifying production processes. This in turn will encourage the uptake of these processes. In addition, increasing familiarity with DFAM—the additive design space—will mean engineers and designers will become more proficient at navigating design limitations and opportunities and leveraging new materials.
And many obstacles are becoming less of an issue due to new developments and technologies. One example is post-processing, which can currently present a bottleneck. 27% of respondents to the 2024 survey named "post-processing and finishing requirements" as a reason for choosing other manufacturing methods over 3D printing, and 40% listed "quality and consistency of the final product". However, as vapor smoothing is becoming prevalent across the industry and surface finishes are being radically improved, post-processing is becoming less of a hurdle for production-level 3D printing. "Vapor smoothing machines have come a long way in recent years," says Grant Fisher, supply chain manager at Protolabs, "specifically for vapor smoothing Nylon 12"—the most common material for MJF and SLS parts. "We continue to see a lot of growth in MJF and SLS, and vapor smoothing is a great option for aesthetic and end-use parts."
Another example is automation of the manufacturing process. For instance, computer-vision-supported systems to help sort finished 3D printed parts can represent significant labor savings and cost efficiency, further pushing the numbers in favor of 3D printing.
Standardization is one key issue that remains, particularly in sectors such as aerospace, automotive and the medical industry. "We do a lot of work with aerospace, particularly in metal printing," says Protolabs' Eric Utley, "and the big hurdle that everyone's dealing with is standardization. Building out that validation and standardization—I personally think it will take a few ears to unstick that." But the will is there and the cogs are moving. "It is a big talking point in the wider industry," says Utley.
The medical and aerospace sectors are the ones where 3D printing to for production will continue to play the biggest role, says Alex Huckstepp. "These are the industries that are willing to spend a lot on high-performance, high-quality, complex custom designs and components. And that was always thought of as where 3D printing in production could make sense. The real production growth is still coming from those two industries. The space-race boom that we're seeing has definitely been a tailwind for 3D printing."
There's another point that's often overlooked when discussing production-level 3D printing, sometimes to the detriment of embracing its incredible potential: it shouldn't necessarily be approached as a replacement for existing technologies at all. "I think a lot of people have in their mind that 3D printing is an injection molding competitor—yea, it's not," says DIVE's Adam Hecht. "It's an entirely new way of making things. They just don't compete. There's some overlap, yes, but ultimately, their career separate. 3D printing is an entirely new tool. It's enabling us to solve problems, and ultimately, to make products that previously couldn't exist. All the low-volume, specialized applications and products where you previously had to tell people, sorry, we can't make that—we can make them now. It's just entirely different."
And one thing that's going to enable and accelerate this are the specialized materials that are increasingly emerging on the 3D printing market.
Key Takeaway
As the 3D printing ecosystem continues to mature, a support system of companies providing many of these services is springing up around 3D printing businesses, simplifying production processes.
The Emergence of Specialized Materials
Elasticity, conductivity, heat resistance... new materials with a range of properties are being tailored for 3D printing
There is an increased focus on the development of specialized materials at production level. "We're always looking at materials that need to actually work out in a field, in a factory, in a lab," says DIVE's Adam Hecht. While a few years ago, printing standard polypropylene was the order of the day, he says that "now, companies are designing blends actually tailored for 3D printing. They're creating a lot of materials that are geared for very specific applications within 3D printing, whether that's conventional thermoplastics that have been re-engineered for 3D printing, or resins that aren't just for prototyping, but for very specialized, high-temperature, high-elasticity types of applications. That's been really exciting for us to see."
Hecht names Carbon Fiber PP Filament by the 3D materials innovator Xtellar as an example. "Polypropylene has been notoriously challenging to print via FDM," he says, "but new formulas address these challenges, while maintaining important qualities of polypropylene like chemical resistance, low density, and impact strength." Another example for a highly specialized material is CPX by Filament Innovations, which makes machines and advanced materials specifically for custom prosthetics.
Traditionally, research and development in the 3D printing industry has leaned heavily on metal. "There's a lot more money in industries utilizing metal, such as aerospace and medical," says Hecht, "so they've been able to make a lot more progress on the side of research and investing." Protolabs' Eric Utley agrees: "There's always a lot of research going on in metals," he says. But now, there is also a real push for production-capable plastics, as well as more specialized materials such as ceramics and silicone. "Some markets, like automotive, consumer, healthcare, and industrial, are doing an amazing job showing the world what can be done when we approach manufacturing with a 3D mindset," says HP's François Minec. "Materials innovation will only lead to further disruption in these markets and beyond."

Materials with properties such as elasticity, conductivity, heat resistance, or improved stiffness, materials with dissipative properties, extra lightweight materials, biocompatible materials, and materials with reduced UV sensitivity are emerging and entering the market.
As they are becoming more accessible, they are set to transform 3D printing practices. "An important emerging property is heat resistance for high-temperature applications," says Protolabs' Grant Fisher. "We are starting to see ceramic 3D printing in the market—is has some technical challenges but is capable of making some unique parts with great thermal properties." Another example is TPU—thermoplastic polyurethane—a relatively new material for powder-based printing technologies such as MJF and SLS that's been described as a bridge between rubbers and plastics. With its flexibility and durability, it can be used for custom gaskets and seals, and the fact that it's a skin-safe material means it's also suitable for wearables and medical applications.
In addition, HP has announced a new nylon-based material for its widely adopted MJF printers that it says offer superior surface aesthetics and cost-efficiency in parts production. According to Minec, it has "reduced variable costs per part and a significantly lower total cost of ownership," as well as the "sustainability benefit of the highest reusability ratio" of all PA 12 materials in the market.
The push for new, production-capable materials is something that's happening industry wide. "There's a number of companies throwing their hat in the ring," Utley says. "There's a lot of market competition going on."
When used in production, plastic parts need a fire rating such as a UL rating in the US or the CE rating in the EU, so consequently, flame-resistance is one property that is in high demand. "Again, it demonstrates that maturation of the market," says Utley. "There's now enough production plastic printers out there for companies to start offering flame-rated plastic materials that can be used in production."
Some sectors, particularly the medical industry, aerospace, and automotive, are highly reliant on certifications. "Working closely with standardization bodies and certification agencies to ensure new materials meet necessary criteria and regulations [is] key, in addition to compiling data and procedures that show the new material is consistent, reliable, and repeatable throughout the manufacturing process," says Minec.
And while this is rarely a speedy affair, things are moving along, says Fisher. For example, "more and more materials get approved for use in aircraft interiors." And new certifications tend to have a big impact on the industry as a whole. "As materials get approved for defense contract work and government work, it really opens up that area. So whenever a material gets approved for a specific kind of government application, it's a big deal." Indeed, in our survey, 64% of respondents stated that materials and/or compliance certificates were either "very important" or "sometimes important" to their 3D printing projects.
In the same survey, only 10% named "material properties" as the main factor why they opted for 3D printing over other manufacturing methods—a figure that is likely to increase considering the exciting developments in this particular field.
Starting Small, Going Big
From microscopic parts to bridges and houses, 3D prints come in all sizes
One factor that effectively illustrates the evolution and maturation of 3D printing is the incredibly wide range of scales on which it is happening. From parts that are so small they are barely visible to the renewed push for large-format 3D printing, the sector truly covers all shapes and sizes. "There are 3D printers that are the size of an entire room," says Protolabs' Grant Fisher. "There are 3D printers that are printing bridges and houses."
The technology naturally lends itself to microprinting. "There's geometries and quantities that only 3D printing can do at that scale," says Eric Utley at Protolabs. One of the main industries where this is being utilized is the medical sector, particularly in dental care. "There's a lot of companies investing millions in dental printing very small, precise, FDA-certified" adds DIVE's Adam Hecht. And advancements in this investment-rich sector then tend to make their way across the industry. "So much innovation is found there that it's now translating to other small parts that utilize similar foundational technologies, such as vision systems," says Hecht. "We've seen a lot more companies in recent years specializing in the micro world, just because some of the technologies can get such small, fine details. You just can't machine parts that small. You can't mold parts that small. So I would say that that's certainly happening."
At the other end of the scale, Hecht expects a significant push for large-format 3D printing, for applications such as tooling or furniture, helped along by new, larger systems such as robotic pellet systems. These systems offer greater design freedom, complexity, and production flexibility. They can also eliminate, or at least reduce, the substantial amounts of waste associated with machining large parts, and drastically cut down the labor needed to manually fabricate large structures from many smaller parts. "It's a really interesting next step for various industries, and it opens a new door to possibilities for larger pieces—and we're seeing a lot more companies are jumping on that wave as well."
In addition to furniture, boats are another example where 3D printing can significantly save on manual labor costs and material waste. Large-format printing is also being utilized for art and marketing purposes, and, of course, there's the aforementioned houses. "Printing housing in concrete seems to be growing quite a bit," says Utley.
Hecht also thinks that in certain circumstances, large-format polymer printing can replace sheet-metal parts. "Where speed, agility, and complexity present a challenge for conventional sheet-metal manufacturers, large-format printing is a clear winner. It reduces minimum order quantities and enables the design to evolve without additional costs. Small sheet-metal parts are hard to compete with, but for large ones, the constraints begin to add up and printing becomes a contender."
Of course, there are limits. For simple shapes made from metal, conventional manufacturing processes often remain the most efficient. Alex Huckstepp mentions the time when there was an ambition to 3D print an entire rocket, "before they realized that 3D printing a big cylindrical tank is not a cost-effective way to make that big shape. You can just roll a piece of sheet metal and do it how everyone else does." In short, you don't always need rocket science to build a rocket.

The Shape of Things to Come
Based on an analysis of data reported by leading market analyst firms that evaluated the 3D printing market in 2023, we estimate the 2023 market size to be $22.14 billion on average. This represents an annual growth rate of 26.8%, far exceeding previous projections. This increased market growth rate is reflected in the responses to the 2024 edition of our annual survey of our global engineering community, in which 70% of respondents indicated that they printed more parts in 2023 than in the previous year.
The industry has steadily continued its move towards production applications, including low-volume production, mass customization, and serial production. A network of companies providing production support and specialized solutions for a wide range of fields and applications has emerged, signifying a maturation of the wider 3D printing ecosystem.
Automation systems supported by computer vision, thermal sensors, and AI can effect signification labor savings, and thus cost efficiency, further encouraging the uptake of production-level 3D printing.
AI is expected to have a wider impact on hardware, for instance in quality control with in-process monitoring and anomaly detection. Smart printers will get smarter, improving user experience. Design for additive manufacturing will also benefits from AI innovations—think topology optimization, Multiphysics process simulation and AI-generated CAD.
New materials that are especially tailored for 3D printing are being developed and certified at pace. These specialized materials have a wide range of properties, such as high elasticity, conductivity, heat resistance, biocompatibility, and reduced UV sensitivity.
Investment in micro 3D printing continues to be significant. The technology's ability to achieve highly complex geometries at a microscopic scale is leveraged by a range of industries, particularly by the medical and dental sector. On the other end of the scale, new developments in large-format printing promise to have an impact on sectors such as construction.
Other trends and developments we expect to have an impact on the 3D printing industry in the coming year include the continued rise of metal printing (DMLS), used predominantly for aerospace, automotive, and medical applications as well as for tooling; hybrid manufacturing processes combining additive manufacturing with CNC machining and other technologies; and multi-material printing, enabling the combination of materials with different properties in one printed object.
Protolabs Network's Robin Brockötter points out that with growing knowledge and education, opportunities and new ideas will continue to transform the sector. "We're still at a time where people aren't familiar with the full capabilities and use-cases of 3D printing. But as future generations of designers and engineers are being trained to learn about the capabilities of 3D printing and are entering the workforce, these innovations will become more and more common." At the rate that these developments are taking hold, the entire manufacturing industry will continue to shift, and at pace. Presented with a shorter path to innovation, there's potential for engineers to bring all kinds of ideas into our lives in the time it takes for a print to cure.
How We Created This Report
To produce this report, we collected market trend data from various sources. These included figures from several leading market analyst firms that evaluated the 3D printing market in 2023, a survey of over 700 engineers, designers, manufacturers, and other who have engaged with Protolabs Network, along with interviews of industry experts. We'd like to thank Robin Brockötter, Grant Fisher, and Eric Utley from Protolabs for their participation in creating this report and Adam Hecht, Alex Huckstepp, and François Minec for sharing their insights and ideas.