
Metal 3D Printing for Production Parts
Improve strength, dimensional accuracy, and cosmetic appearance of end-use metal components
Looking for an additive manufacturing solution for production projects? With our metal 3D printing technology, you’re able to choose from several secondary processes like post-process machining, tapping, reaming, and heat treatments that produce end-use production parts. To ensure high-quality parts, we also offer powder analysis, material traceability, process validation, and inspection reporting, and our direct metal laser sintering (DMLS) 3D printing process is ISO 9001 and AS9100D-certified. It’s industrial 3D printing designed around your project needs—whether prototyping or production.
Why Protolabs for Production-grade Metal 3D Printing?
1. Expertise
Consultative quoting and design feedback from our experienced engineering team and reliability from a manufacturer that has 3D printed millions of unique geometries over the last two decades.
2. Project Management
Dedicated project management support for all of your production needs from part design to finishing processes.
3. Scale
More than 100 industrial-grade metal and polymer 3D printers across five additive manufacturing technologies supporting production projects in various engineering-grade materials.
4. Quality
Rigorous process controls and engineering staff focused on achieving parts with tight tolerances, dimensional accuracy, and robust mechanical properties.

Large Format Metal 3D Printing
We’re expanding our 3D printing capabilities for metal parts with a new GE Additive X Line printer. It produces Inconel 718 and Aluminum parts as large as 31.5 in. x 15.7 in. x 19.7 in. Have a project that might be a good fit? Contact us and we can discuss your requirements.
Production Capabilities for Metal 3D Printing
Post-Process Machining

Achieve tight tolerances while having the design freedom of additive manufacturing.
- 3- and 5-axis milling
- Turning
- Wire EDM
- Tapping and reaming
Powder Analysis & Material Traceability
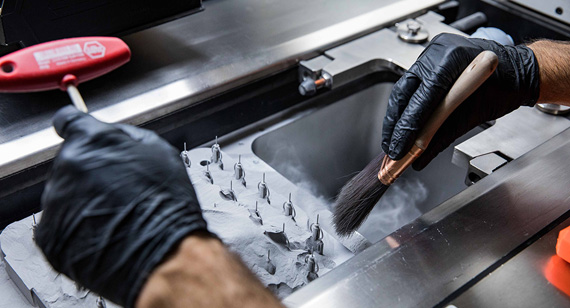
Receive an analysis of source powder and traceability back to material supplier to meet your production requirements.
- Chemistry
- Particle size and distribution analysis
- Mechanical coupon testing
Mechanical Testing

Certified testing to confirm mechanical requirements on production parts.
- Tensile
- Rockwell Hardness
- Fatigue
- Vibration
Heat Treatments
Specialized heat treatment processes improve the mechanical properties of parts by relieving internal stresses that develop during the sintering process.
- Stress relief
- Hot isostatic pressing (HIP)
- Solution annealing
- Aging
Quality Inspections & Reports
Validate part geometry and evaluate material structure for quality reporting.
- Dimensional inspections with ballooned report
- First article inspection (FAI) per AS9102
- CMM, optical, and CT scanning
- X-ray
- Surface roughness
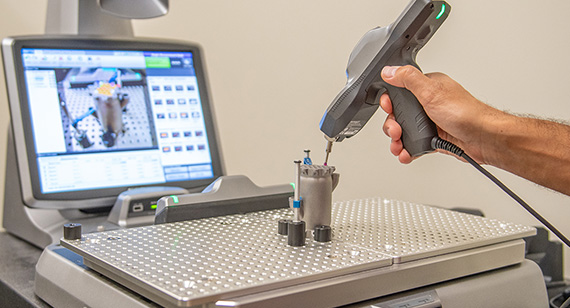
CERTIFICATIONS

Designing Metal Production Parts for Additive Manufacturing
When creating 3D-printed metal components for end-use production, additional post-processing steps and enhanced quality reporting are often needed. In this webinar, you’ll learn about our advanced additive manufacturing capabilities to support your production projects.
Materials and Equipment for Metal 3D Printing
Materials
- Aluminum / ALSi10Mg
- Cobalt Chrome
- Inconel 718
- Stainless Steel 17-4 PH
- Stainless Steel 316L
- Titanium / Ti 6AL-4V
Equipment
We use GE Additive Concept Laser Mlab, Mlab 200R, M2, and X Line 2000R machines for DMLS production that offer large build sizes, produce accurate parts, and provide quick turnaround times. The Mlab and Mlab 200R are ideal for manufacturing metal components with elaborate structures, and they are ideal when high surface quality and fine component structures are needed on parts. The M2 is a large platform machine that is able to produce larger metal parts than the Mlab, and the X Line 2000R can produce parts with build volumes as large as 800mm by 400mm by 500mm. All of our 3D printing equipment can handle both reactive and non-reactive metal powder.
