
Liquid Silicone Rubber Injection Molding
Get custom silicone rubber parts within days.
Certifications ISO 9001:2015 | ITAR Registered | CTQ
Jump to Section
→ Capabilities
→ Materials
→ Surface Finishes
→ Quality Inspections
→ About Silicone Rubber Molding
Our liquid silicone rubber (LSR) molding process produces custom prototypes and end-use production parts in 15 days or less. We use aluminum molds that offer cost-efficient tooling and accelerated manufacturing cycles, and stock various grades and durometers of LSR materials.
Common applications for silicone rubber molding:
- low-volume production
- bridge tooling
- pilot runs
- functional prototyping
Liquid Silicone Rubber Molding Capabilities
Our basic guidelines for silicone rubber molding include important design considerations to help improve part moldability, enhance cosmetic appearance, and reduce overall production time. View our design guidelines page for more details.
US | Metric | |
SIZE | 12 in. x 8 in. 4 in. | 304.88mm x 203.2mm x 101.6mm |
VOLUME | 13.3 cu. in. | 217,948 cu. mm |
DEPTH |
No greater than 2 in. from any parting line; deeper parts are limited to a smaller outline |
No greater than 50.88mm from any parting line; deeper parts are limited to a smaller outline |
PROJECTED MOLD AREA | 48 sq. in. | 30968 sq. mm |
Tolerances: Protolabs can maintain a machining tolerance of +/- 0.003 in. (0.08mm) with a linear tolerance of +/- 0.025 in./in. (0.025mm/mm).
Surface Finish Options
FINISH | DESCRIPTION |
---|---|
PM-F0 | non-cosmetic, finish to Protolabs' discretion |
PM-F1 | low-cosmetic, most toolmarks removed |
PM-F2 | non-cosmetic, EDM permissible |
SPI-C1 | 600 grit stone, 10-12 Ra |
PM-T1 | SPI-C1 + light bead blast |
PM-T2 | SPI-C1 + medium bead blast |
SPI-B1 | 600 grit paper, 2-3 Ra |
SPI-A2 | grade #2 diamond buff, 1-2 Ra |

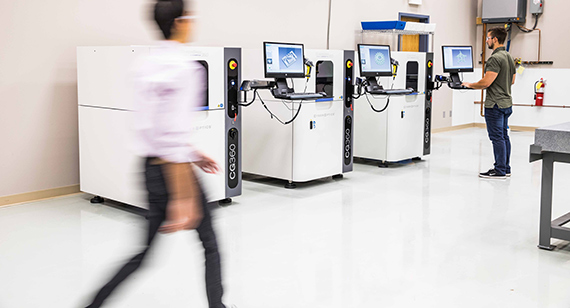
Quality Inspections and Finishing Options
Depending on your application's requirements, you can choose from the following when requesting a quote for your silicone rubber parts.
Quality Inspections available for on-demand manufacturing orders
- Designing for Manufacturability (DFM) Feedback
- Scientific Molding Process Development Report
- In-process CMM inspection and machine monitoring
- First article inspection (FAI) and process capability report with GD&T

Learn More About Liquid Silicone Rubber Molding
Our guide to liquid silicone rubber (LSR) discusses the injection-molding process of the elastic material and offers guidelines to improve molded LSR parts. While there are some shared similarities to thermoplastic injection molding, LSR is a thermoset material with a unique set of design characteristics.
How Does Liquid Silicone Rubber Molding Work?
Due to the flexible nature of LSR, parts are manually removed from the mold, and thus, ejector pins are not built into the mold design. Like a standard aluminum tool, an LSR molding tool is fabricated using CNC machining to create a high-temperature tool built to withstand the LSR molding process. After milling, the tool is polished by hand to customer specifications, which allows six standard surface finish options.
The finished tool is loaded into an advanced LSR-specific injection molding press that is precision geared for accurate control of shot size to produce the most consistent LSR parts. Since LSR is a thermosetting polymer, its molded state is permanent—once it is set, it can’t be melted again like a thermoplastic. When the run is complete, parts (or the initial sample run) are boxed and shipped shortly thereafter.
Liquid Silicone Rubber Resources

Get an online quote and injection molding design analysis today.