
Tooling for Production Injection Molding
Reduce part costs and create supply chain flexibility with automated injection molding
Certifications ISO 9001:2015 | ISO 13485 | CTQ Inspections | ITAR
Talk with Our Production Team
Hello! We just need a few bits of information then a manufacturing expert will reach out to you directly to see we how can partner on a future production project.
Thank you! We've received your request and a member of our team will reach out shortly.
We have two injection molding service options—prototyping and on-demand manufacturing—and each offers its own benefits depending on your project needs. If part quantities are higher, an affordable piece-part price is important, and quick-turn production throughout your product life cycle is critical, our on-demand manufacturing option is ideal.
Production Grade Tooling for Injection Molding
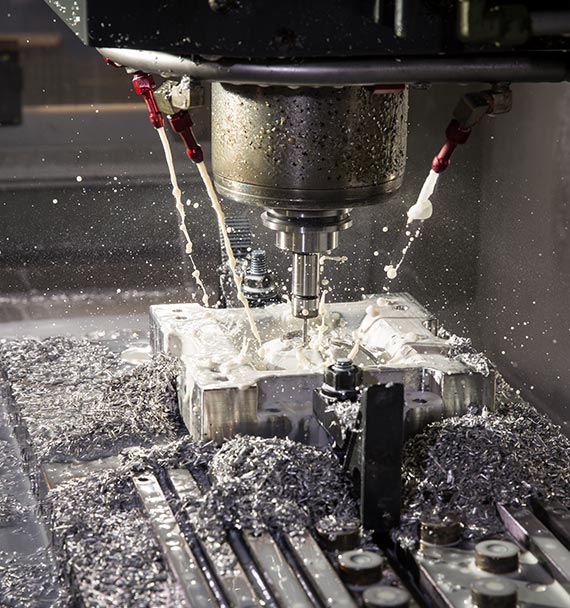
Mold Price | Higher than prototyping tool |
---|---|
Part Price | Lower than prototyping tool |
Mold Cavities | Single and multi-cavity |
Guaranteed Mold Life | Unlimited |
Mold Storage | Stored for 3 years of inactivity |
Quality Documentation | Molding process development report and basic inspection reports included; enhanced inspection reports available upon request |
Additional Features |
|
Injection Molding for End-Use Production
Protolabs on-demand manufacturing service helps you simplify your supply chain so you can get quality parts easier and faster. Using industry best practices like scientific molding, we accelerate manufacturing cycles to reduce your time to market. We meet your inventory needs with no minimum order quantities, and offer supply chain flexibility ranging from bridge tooling and just-in-time (JIT) production to line-down emergency coverage.

Low-volume Runs
- Validate part design, assembly processes, and market demand with pilot runs prior to mass production.
- Manage inventory overhead with production of parts only when demand dictates.
- Use as the primary production method for products with annual sales volumes of a few thousand units.
Bridge Tooling
- Implement cost-effective aluminum tooling before committing to a capital expense with steel tooling.
- Minimize the “cost of waiting” for a steel tool—and get to market quicker.

Optimizing Supply Chain
- Minimize down time and reduce the risk of stock-outs when large-scale production tools are being repaired.
- Mitigate the risk of domestic and global shipping delays by having a reliable, on-demand supplier of low-volume parts.
- Manage increases in demand volatility without going on back-order.
Reduce Production Costs
- Unlock new market opportunities with cost-effective production of low-volume, end-use parts
- Procure parts on demand, without any Minimum Order Quantity (MOQ) requirements
- Lower inventory costs and warehousing expenses with on-demand sourcing.