
Sheet Metal Assemblies
Get custom fabricated assemblies delivered in as fast as five days. Upload your assembly file to get an online quote
Certifications ISO 9001:2015 | ITAR Registered
Free Design Review for Fabricated Assemblies
Our design review consists of a 30-minute virtual meeting with one of our sheet metal applications engineers. It’s a perfect opportunity to discuss any questions you may have about your project. Common discussion questions include:
- Navigating assembly construction options
- Tolerance stack-up
- Costing trade-offs
Our online sheet metal assembly service lets you create functional, end-use products delivered to you in days. With each project, you get design for manufacturability (DFM) feedback and expert-level support. You can choose from a broad range of finishing options to achieve your aesthetic requirements.
Fabricated assemblies are frequently used for:
- Functional prototyping
- Product testing and qualification
- Low volume, end-use production
- Pilot runs
File Format and Configuration
Preferred file formats for assemblies are upper-level assembly STEP files. For SOLIDWORKS users, a solid assembly file (.sldasm) with separate component files (.sldpart) is preferred.
If your project is a weldment or has welding requirements, please provide a 2D drawing with your CAD submission.
For situations where Protolabs will not assemble your project components, a solid (or top-level) assembly file is not required.
Materials
Choose from readily available materials which can be easily constructed into a final assembly. Industry standard material thicknesses are used for all material types. Common materials found in fabricated assemblies are:
- Aluminum 5052-H32
- Low carbon steel CR 1008
- Stainless steel 304/304L
- Stainless steel 316/316L
Each of these materials provides excellent formability and weldability characteristics, as well as superior corrosion resistance in harsh environments.
Additional materials are available, such as pre-plated steels (galvanized or galvannealed). However, the pre-treated coating makes these materials candidates for rivet-based assembly construction.
Our material comparison tool offers more information on sheet metal types and thickness ranges.
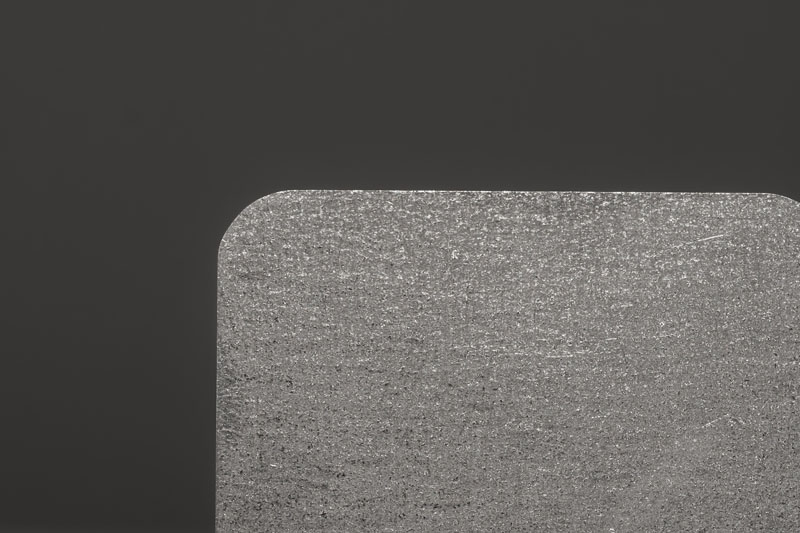
Cold-rolled galvannealed steel is a great choice for strength and corrosion resistance.
Assembly Construction Guidelines
Customizing your assembly design can take many forms. Consider the following for your next sheet metal project.
Maximum assembly size (when fully constructed): 47 in. x 39 in. x 36 in. (1194mm x 991mm x 914mm)
Available assembly methods:
- Welding (seam, tack, stitch weld techniques)
- Riveting (pop and solid rivets)
- Hardware insertion

Using a punch tool or laser to cut designed holes is a great idea, but make sure you know the plusses and minuses of each option.
Formed features:
- Linear bending (via press brake) with tooling options between .010 in. and 1 in. (0.254mm and 25.4mm).
- Large radius bending for additional functional or aesthetic requirements using bump forming or roll-forming techniques.
- Punch-formed features such as louvers, ribs, dimples.
Tolerances:
- Typical sheet metal tolerances apply to assemblies. Review our design guidelines for more details.
- Specific tolerance questions, including stack-up and fitment, can be addressed by scheduling a free 30-minute design review.
Machined Features:
Post-processing CNC machining can offer additional features typically found on more complex geometries. These design elements are hard to achieve with laser cutting, punching, or press brake forming alone. Possible features include:
- Pockets
- Holes, cutouts, or features at risk of deformation during forming
- Flange length reduction
Inspection reporting options:
- Material and/or finishing certifications are available*
- Inspection documentation, including First Article Inspection*
- All parts and assemblies are inspected for dimensional and visual accuracy based on Protolabs work standards prior to shipping.
*Must be requested before your order is placed. Choose from options shown on your online quote.
Hardware Insertion Guidelines
An extensive stocked library of fasteners is available from brands such as PEM and Southco.
File Formatting:
- Recommended: Include any hardware in your 3D CAD model as separate solid bodies from the main sheet metal body. Use industry standard hardware part numbers when possible (e.g. CLS-M6-1)
- Alternative: Upload your CAD file without hardware and include a 2D drawing noting hardware types and locations.

We offer a huge variety of PEM hardware. Avoid issues with placement while still in the design phase with these guidelines.
Examples of Available Hardware Types to Customize Your Project:
- Self-clinching nuts
- Self-clinching standoffs
- Flush-head studs
- Miniature self-clinching nuts
- Self-clinching flush nuts
- Flush-head pins
- Self-clinching blind fasteners
- Thin sheet non-flush studs
- Self-clinching lock nuts
- Self-clinching micro pins
- Panel fasteners
Lead Time: Adding hardware to your part design does not add lead time.
Design Guidelines:
- For inserts to grip the sheet metal correctly, the material of the hardware insert must have a hardness equal to or greater than the material into which it is inserted. Further details on hardware and material compatibility can be found in our Design for Manufacturability Toolkit.
- Our design tip on effective hardware integration covers hardware use cases and part placement considerations.
Welding Guidelines
Welding is available to join or fuse your metal components into their assembled form. Our most common welding capabilities include gas metal arc welding (MIG) and gas tungsten arc welding (TIG).
Welding Design Guidelines:
- To avoid material warping or “oil canning,” the minimum material thickness for welded assemblies is 0.042 in. (1.07mm).
- Maximum material thickness for welded assemblies is 0.250 in. (6.35mm).
- Always specify welding location requirements on your 2D drawing.
- If possible, avoid specifying a welding method, unless required for functionality.
- Material types must be consistent across parts when welding multiple geometries.
Riveting is an option to consider if you are looking for additional flexibility when joining your metal components. Riveting is a technique in which components are joined using a type of hardware called a rivet. For more information, review our blog post on the different advantages of welding or riveting your next project.
Lead Time: Welding adds 1 business day.

Welding creates a strong bond between two pieces of sheet metal.
Finishing Options for Assemblies
In addition to feature or geometry customization, our finishing services for components and assemblies allow for customization of your aesthetic requirements. Our finishing options include:
- Plating
- Powder coating
- Wet paint
- Masking
- Part marking
- Metal surface finishing
Lead Time: Most finishing options add 1-2 days per finish. See our finishing options page for more details.

Some say parts aren't finished until they're finished. Explore your options to take your parts to the next level.